PRE2022 3 Group3
Group members
Name | Student id | Major |
---|---|---|
Luta Iulia Andreea | 1671685 | BCS |
Sonia Roberta Maxim | 1675656 | BCS |
Marie Spreen | 1909983 | |
Fenna Schipper | 1625624 | BPT |
Hakim Agni | 1430149 | BCS |
Lazgin Mamo | 1502506 | |
Dhruv Manohar | 1568868 | BCS |
Introduction
Problem statement
Plastics have had a big impact on the medical industry. Their main advantage is the ease of sterilization compared to traditional materials used in healthcare such as ceramics, glass and metal. The latter materials needed time-consuming sterilization processes, steaming or autoclaving, whereas for plastics, there is a new technology used: gamma sterilization. With the use of plastics, procedures are easier and safer and the costs have been reduced a lot[1]. But this revolutionary change of plastics in health care also results in a lot of plastic waste. In 2020, globally over 32 billion pounds of healthcare plastics were produced, and this is expected to grow to 48 billion pounds by 2025. Most of this plastic is being disposed of in landfills or by incineration even though much of this material is uncontaminated and recyclable[2]. During the Corona crisis, the waste became even more because the large amount of single-use plastics that were needed as personal protective equipment. "There has been a dramatic demand for personal protective equipment (PPE). PPE which includes masks, safety goggles, face shields, hair covers etc. are all made of plastics like polyethylene terephthalate (PET)" [3]. All these plastics have a great impact on the environment, especially because most of these plastics are assumed to be infectious and cannot be discarded with the common municipal waste. Moreover, lack of sufficient landfills available have persuaded mankind to think of sustainable recyclable options. Most of the medical plastics have the potential to be recycled back into the petrochemical industry as a feedstock for the production of new plastics or refined fuels[1]. Recycling these plastics is a solution to solve the crisis of plastic pollution, but recycling medical plastic has difficulties involved in sorting and cleaning.
To use plastics for biomedical application, it is important that plastics are selected with appropriate material, chemical or thermal properties, sterilization potential and durability because not all plastics can be recycled. If the plastics are not recycled in the correct way they can cause serious health issues and long-term pollution[3]. Even though recycling medical plastic can make a serious difference, still very little is known and done. There is an association, HPRC (Healthcare Plastics Recycling Council), that tries to solve this problem. However, still not a lot has improved.
In the US, the economy lost more than US$7.2 billion from landfilled plastic waste in 2021 according to Department of Energy (DOE) estimates. "We posit that a substantial amount of landfilled plastic waste could be recovered through advanced sorting, existing, and emerging recycling processes", asserts Anelia Milbrandt, a senior research analyst at the DOE’s National Renewable Energy Laboratory.[4]
Objectives
To help the recycling process of medical plastic, we will try to come up with a robot which makes helps with dividing the different plastics based on their properties so it will be easier to recycle them. In order to do this literary research will be done and a concept will be made.
Why?
Medical staff already have a heavy workload and many responsibilities to deal with during their time at hospitals and clinics. Except from the shortage of medical staff due to the growing population in European countries, the available medical staff already spend much time on other tasks than taking care of patients. For instance, a study published in SAGE journals reports that doctors for instance spend 8.7 hours per week (16.6 % of working hours) on administration less than physicians who spend 20.3 % of working hours on administrative tasks[5]. Training medical staff to separate medical waste based on their chemical properties could be a cheaper and easier solution , however it would also put more workload on them and affect the service quality they provide for their patients.
In addition , Stericycle’s Healthcare Workplace Safety Trend Report found that more than 90% of healthcare professionals surveyed believe effective medical waste management is key to providing the best patient care possible. On the other hand, those surveyed also reported that improper medical waste management contributes to fatigue and burnout (68%) and can negatively impact patient health and safety (72%). Nurses can save time and energy when they can dispose of medical waste through a streamlined process."[6]
State of the art
In this section we will investigate potential attempts that have already been implemented in order to tackle different aspects of this problem and existent technologies that can help towards creating a final design.
Machines developed that can separate 12 different types of plastic[7]
Researchers from the Department of Biological and Chemical Engineering at Aarhus University have created a new camera technology that can differentiate among 12 types of plastic From these types, PVC, PP, PS, PE, PC, PET, PA12, ABS are frequently used in the healthcare system. For example, Polycarbonate (PC) is usually found in syringes, tubes and stents. The camera technology separates the different types of plastic based on their pure chemical composition. It uses a hyperspectral camera and machine learning algorithms to analyze the type of plastic directly on the conveyor belt.
In comparison, the current technology that usually uses near-infrared technology or density tests, can separate a much smaller variety of plastics and it is not as efficient.
Plastic classification via in-line hyperspectral camera analysis and unsupervised machine learning[8]
Hyperspectral imaging with wavelengths from 955 to 1700 nm on thirteen different plastics analyzed by PCA has shown that the spectral range is sufficient to differentiate plastics. Unsupervised machine learning has proven to cluster the plastic types and the resulting loading matrix correctly classified unknown plastic samples.
Healthcare Plastics Recycling Council (HPRC)[9]
The council showcases multiple case studies run in hospitals regarding plastic recycling. Even though multiple hospitals are planning and developing a recycling program, none of them had promising enough results to make a breakthrough.
- Chicago Regional Recycling Project: HPRC and Plastics Industry Association (PLASTISCS) are currently running a recycling program in the Chicago area. Participating hospitals are Advocate Illinois Masonic Medical Center, and NorthShore University Health System’s Evanston, Skokie, Glenbrook, and Highland Park Hospitals. The project includes various companies providing logistics and recycling support, sustainability management software service, financial support and specialized bags for collection and transportation of the plastic materials.
- Kaiser Permanente and Cleveland Clinic: the approach focuses on external waste recycling companies that will deal with sorting the mixed plastic waste. The programs are not yet running.
- Mayo Clinic: Mayo Clinic’s Healthcare Plastics Recycling Program began in 2013 and from 2016-2017 it saw a 78% increase in recycling the PP, PS and other types of plastic and a 9% increase in recycling PET AND HDPE plastics. The project involves the addition of a baler, a grinder and willing external plastic buyers.
TRASHBOT[10]
Physical implementation of a autonomous sorting waste technology. Developed by cleanrobotics, the technology uses AI and computer vision to detect the recyclables and then applies machine learning algorithms to sort them and divert them into specific bins.
ECOSTERYL[11]
Ecosteryl is a machine produced by the company AMB based in Belgium that offers a solution for medical waste treatment and recycling. The waste is shredded and decontaminated in a secured machine. The machine does not need any water or steam.
ECODAS[12]
ECODAS is a company based in France that also deals with medical waste. This includes medical waste from hospitals, clinics, other healthcare institutions, seaports and airports. The ECODAS machine is an automated system that sterilizes regulated medical waste and thereby reducing around 80% of the waste volume. The recycling and sterilization include shredding and steaming of waste.
Users
Primary Users: Medical Staff
In the USA, the current workflow of medical staff regarding plastic waste management varies depending on the facility and region. However, there are generally accepted guidelines and best practices that medical staff follow to manage plastic waste.
Firstly, medical staff are trained to segregate waste at the point of generation, which means that they sort the waste into different categories such as infectious, hazardous, pharmaceutical, or general waste. This helps to ensure that each type of waste is managed appropriately and safely. Once segregated, the plastic waste is typically collected in specialized containers that are labeled and color-coded to indicate the type of waste they contain. For example, infectious waste may be collected in red containers, while hazardous waste may be collected in yellow containers. Medical staff are also encouraged to minimize the amount of plastic waste they generate by using reusable or sustainable alternatives whenever possible. This includes using cloth gowns and towels instead of disposable ones, using reusable containers for sharps disposal, and minimizing the use of single-use plastics in the medical setting. Overall, the workflow of medical staff regarding plastic waste management in the USA involves careful segregation, labeling, and disposal of plastic waste, as well as a focus on minimizing the amount of waste generated.
There are many problems that faces the nurses which makes medical waste management inefficient. In a study published in the "Journal of nursing management" , nurses were interviewed and the following problems are expressed: Firstly, medical and nursing students that temporarily work in a hospital lack the knowledge about recycling management process. Secondly, emergency cases which require immediate intervention leads to mistakes in throwing the waste in the correct disposal unit. Thirdly, lack of personnel leads to a heavy workload which again causes inevitable human mistakes. The biggest obstacle facing recycling was a lack of information about recyclable and contamination of materials.[13]
For this group of users , it is essential that the segregation of medical plastic waste is done appropriately and automatically. Segregation robots can help medical staff quickly and efficiently sort medical waste, saving time and increasing productivity. Furthermore , Medical waste must be properly segregated and disposed of according to local and national regulations. Segregation robots can help ensure that medical staff comply with these regulations, reducing the risk of fines and other penalties.
Secondary Users: Hospital Management
Now in hospitals, waste is generally separated into color-coded bins or bags. This system however is far from flawless. Because the color selected for each waste type varies between different regions. This lack of standardizations results in errors in the waste separation and makes the system inefficient.
In hospitals the separation of infectious and non-infectious waste is an important process because faults during this process can result in higher costs and danger for the people working with the waste. Studies conclude that 70 to 80 percent of the infectious waste stream leaving hospitals include non-infectious wastes that have been mixed into the infectious waste stream due to poor separation practices. When non-infectious waste ends up being mixed with the infectious waste the costs will be significantly higher because it all has to be processed as infectious waste which is a more expensive process[14]. The poor separation system can also become dangerous when a person comes in contact with infectious waste.
To prevent a mix up of the non-infectious and infectious waste it will be best to separate the two directly when it is deposited into the bins. This however comes with another problem, a lack of clear sorting protocols which makes it hard for the staff to correctly separate the waste.
When sorting plastics there are some additional points to take into consideration in the separation process. There should be a separation between the plastics that can be recycled and the ones that cannot to recycle as much of the plastic as possible. This should be done very carefully because when the waste is not handled correctly it can lead to serious environmental problem. The plastics which can be recycled should again be sorted into their ease of recyclability. When the plastics are infectious, they first have to be sterilized before they can be send with the other waste[3].
So overall for the good waste separation system in hospitals it is best if the waste is separated at the source and for the plastics it is important that is correctly separated based on the recyclability of the plastic to recycle as much of the plastic as possible.
Tertiary Users: Waste Handlers
In the process of plastic-recycling, waste handlers are working on reprocessing plastic scraps and waste into useful products. This often requires greater processing than the recycling of other materials, due to the unique properties of plastics and the various steps that need to be considered. Due to the high molecular weight of large polymer chains, dissolving plastics cannot easily be achieved through heating. Therefore the mixing of different plastics tends to produce phase-separated material, which is structurally weak and only useful in a very limited range of applications. In addition the widespread use of dyes, fillers and other additives leads to many more impurities that have to be accounted for. Oftentimes the polymers are damaged in the process of removing these impurities. Whenever it is possible to produce a single-material and clean stream of plastic, the plastic recyclables are usually shredded and worked into pellets, which are then used to produce new products. Oftentimes products which are themselves made from recycled plastic are no longer recyclable, due to the structural toll the recycling process takes on the material.[15]
The difficulty of the plastic-recycling process is reflected in the amount of plastics recycled. According to a survey in the U.S. in 2021 an estimated 40.1 to 51 million tons of plastic waste were generated, of which only between five and six percent of total plastic were recycled. The majority of U.S. plastic waste is land filled.[16]
The demand for recycled plastics and therefore the market volatility for waste handlers is affected by the price of virgin commodity plastics. Specifically the mixed material healthcare plastic waste streams in addition to the low mass per unit area of plastics relative to other materials, leads to a high logistic cost associated with the recycling process. The European Recycling Industries Confederation (EuRIC) wrote a position paper on the capital investment required to use heavy chemical recycling plants that process mixed waste streams (i.e. through processes such as pyrolysis). It concluded that this would be economically viable at a crude oil price of $65-75/barrel. Over the last five years, oil prices have not been above this range. On the other hand the vast amount of recyclable plastics that are currently ending up in landfill in addition to the momentum behind advanced recycling technologies could work to minimize the cost of the recycling process and ensure market volatility.
While the recycling of plastics has to of course be economically viable, it should also be environmentally viable. The Dutch firm CE Delft analyzed the greenhouse gas reduction and concluded that purification and depolymerization technologies were comparable to mechanical recycling whereas thermal conversion technologies (e.g. pyrolysis), while generating greater greenhouse gas emissions than mechanical recycling, still fell below what would be expected from incineration.[17]
Especially medical waste bears the additional risk of being infectious. Using various sterilization processes we could get rid of that risk, but add to the logistic and economical barriers for waste handlers.[3]
There are essentially four common plastic recycling routes (as can be seen in the figure to the right):
- Primary recycling is the process of reusing single type plastics which are clean or uncontaminated or converting plastic scraps into products with similar characteristics of the original material. Oftentimes waste plastics can be mixed with virgin material to ensure the required product quality. This is considered a closed loop process, as can be seen in the figure.
- Secondary recycling is the recovery of plastic wastes by mechanical means. It involves washing the plastic to remove contaminants and grinding the material. Repeatedly processing plastic in this way leads to slowly building contamination and thermal degradation over time.
- Tertiary recycling is the (often chemical) process of converting the material into smaller molecules (liquids or gasses) to generate chemicals and fuels. It involves chemical processes such as purification, wherein polymers are chemically separated from unwanted additives, decomposition/depolymerization, which breaks the molecular bonds of plastics into monomers and intermediates by biological, chemical, or thermal means, and thermal conversion, which brings plastics back to their most basic petrochemical building blocks by breaking their molecular bonds. The most popular methods of thermal conversion is pyrolysis, where medium temperatures are applied in the absence of oxygen or air to convert plastic waste into liquid and gaseous products and a char byproduct. This process is very useful since it allows for the recycling of material blends.
- Quaternary recycling is the process of recovering energy from waste plastic by incineration. This method is applied whenever wastes are highly contaminated and cannot be recycled by normal means. The process results in waste residues and ultimately pollution as well as harmful gasses that are released during combustion. It reduces the volume of waste to 1% and effectively decomposes toxic or contagious waste.[3]
Design concept
To help with the process of recycling plastics in hospitals, we will design a bin robot. The purpose of this robot is to separate the most common types of plastics in hospitals by itself, so that the medical staff do not have to have extra training and knowledge to separate the plastics correctly.
MoSCoW List
In order to define our design requirements, we created a list which prioritizes these using the MoSCoW method.
Must Haves | Should Haves | Could Haves | Won't Haves |
Opening that people throw the trash into | Sensor for fullness detection | (interactive) Display for more detailed fullness indication | Mechanism to recycle plastics |
Sensor Mechanism that can sense characteristics of plastics | Simple fullness indication | System for relaying fullness information to relevant staff | Connection to underground storage |
Algorithm or Software that can use sensor data to categorize plastics | Way of identifying emptied plastic types for easy storage (e.g: color coded bags) | Odor remover to remove unpleasant odors | Mechanism for detecting contagious waste |
Different compartments to store the respective types of plastic | Compartment for general waste | Wheels to move through the hospital | Mechanism for sterilizing contagious waste |
Mechanism that puts incoming trash into appropriate compartment | Easy access to controller and mechanical parts for maintenance | Mechanism that compresses the trash | |
Must follow the hospital regulations [18] | Updatable over the air | ||
Proper isolation of compartments, trash may not mix under any circumstances | Mechanism that makes bin inaccessible when full | ||
Once trash is inside it stays inside unless a professional empties the bins | |||
Accessible at all times, unless it is full, or someone is unloading the trash | |||
Accessible, lockable additional opening that full bins can be emptied through | |||
Appropriate dimensions, fits through doors and inside corridors[19] | |||
Be easy to use:
|
|||
Be safe to use:
|
Use Cases
As we continue to design our medical plastics waste sorting bot, it is important to consider all of the different functionalities it will need to have in order to effectively sort the waste. One key aspect of this is the ability for the design to appropriately perform in all potential circumstances. To achieve this, we have identified several specific use cases and the corresponding functionalities of our bin. These use cases represent one step in the process of creating our final project, as we work towards a fully functioning system for medical plastics waste recycling.
The figure above depicts the process through which each piece of waste can be disposed of appropriately.
The following use cases describe this and additional processes that the bin needs to handle:
- Disposing waste: The bin allows the access of the piece into the inside of it. The waste is scanned by the sensor mechanism, which uses its algorithm to identify the type of plastic it contains. The piece of waste is then placed in the respective compartment for the specific type of plastic, which is clearly labeled on the outside of the bin.
- Classifying waste: Upon receiving waste, it is scanned and classified in the correct category. The sensor mechanism identifies the type of plastic, and the algorithm categorizes it accordingly.
- Sorting waste: Upon classifying the waste correctly, the bin uses the sorting mechanism to sort the waste into its respective compartment. The sorting mechanism ensures that each type of plastic is stored in its designated compartment, preventing contamination and making it easier for recycling companies to process the materials.
- Signaling fullness: When the bin gets full, a sensor will activate. The bin closes temporarily until an employee empties it. A signal is sent to the management team to let them know the bin is full. This feature ensures that the bin is emptied before it overflows, preventing litter and potential health hazards.
- Disposing non-plastic: The bin allows the access of the piece into the inside of it. The waste is scanned, and it is noticed that the piece does not contain plastic. The piece of waste is then placed in the compartment for unknown substances, which is separate from the compartments for plastic.
- Compressing the waste: The bin can use a combination of weight and IR sensors to determine if the waste is compressible or not, and if it is, it can compress the waste to fit more plastics in it. This feature maximizes the bin's capacity and reduces the frequency of emptying.
- Emptying the bin: Upon arriving at the bin the employee will empty each full compartment individually, taking the plastic waste to the appropriate recycling unit for further processing. After emptying, the bin will resume normal operation.
- Sterilizing the waste: This feature is not included in the design.
After establishing the MoSCoW list of requirements and considering several use cases for our medical plastics-waste sorting bot, we focused on developing a detailed design that would meet each of these requirements. To aid in this process, we created a 3D model of the exterior of the trash bot, which allowed us to visualize the physical layout and design of the bot before moving forward with considering its specific components.
The figures to the right show our design, which features an opening, through which users can dispose of waste easily. The blue screen next to the opening functions as a display for important information regarding the status of the bot, such as when a compartment is full and requires emptying. The bot's seven separate compartments are clearly visible in the image, each with its accessible, lockable opening. The compartments can be emptied individually, allowing for efficient disposal and recycling of plastic waste.
Furthermore, our 3D model depicts a cable extending from the trash bot into the wall, indicating that the bot will be powered via a standard electrical outlet. This will allow for consistent and reliable operation of the trash bot, ensuring that it is always accessible to hospital staff and functioning properly to sort medical plastic waste.
We chose to specifically design our automated waste sorting system in the form of a bin, as this approach would allow hospital staff to easily and safely dispose of waste without requiring extensive training or knowledge of plastic sorting. Additionally, the automation process ensures that waste is sorted accurately and efficiently, minimizing the environmental impact of medical waste.
In the following section, we will delve into the specific functionalities and components of our medical plastics waste sorting bot design in greater detail.
Argumentation for our Design Choices
Separating between Non-infectious vs infectious Waste
For the bin, the choice was made to only focus on non-infectious plastics for the bin. This will result in the product only sorting the non-infectious plastics. It is important to make a decision on whether to collect non-infectious or infectious plastics. When the two are mixed, all the plastics need to be treated like infectious waste. The treatment of infectious waste is a lot more expensive than the treatment of non-infectious waste, so a mixture of the two will only result in more, unnecessary costs. There are some reasons why the choice was made to sort the non-infectious plastics with this bin instead of the infectious plastics. First, about 85% of medical waste is general, non-infectious waste[20]. This means that when the bin focuses on the non-infectious waste it will have a lot more impact than when it focuses on the infectious waste because there will be a lot more waste to sort. Furthermore, non-infectious plastics can immediately be recycled in the Recycling stream of general waste. When the plastics are infectious, the plastics first have to be sterilized. This will not be possible with just this bin, which results in an even harder process because an extra machine should be added.
Separating Between Different Types of Plastics
According to a report by the Healthcare Plastics Recycling Council (HPRC), most healthcare plastic products, that qualify for recycling, fall within five primary applications:
- Sterilization Wraps
- Irrigation Bottles
- Basins, Pitchers, Trays
- Flexible Primary Packaging
- Rigid Primary Packaging
These products can be further categorized into seven different plastic types:
- polypropylene (PP)
- high density polyethylene (HDPE)
- polystyrene (PS)
- multi-materials (HDPE, polyester, polyethylene (PE), polyamides, PP, ionomer)
- polyethylene terephthalate glycol (PETG)
- polycarbonate (PC)
- low density polyethylene (LDPE)[17]
According to our user research the best way of sorting our plastics in a way that maximizes the chances of it being recycled is by creating single material waste streams. If done reliably and with little to no contamination with other materials, this provides waste handlers with high quality material that requires minimal processing before recycling. However there exists a trade-off with regard to the detail of separation between the quality of the waste stream on the one hand and the logistic cost of storage and transportation on the other. If we separate the plastics into all seven categories of healthcare plastics, we create additional costs for both the hospitals and the waste handlers in having to store and transport these plastic types separately. We might consider grouping plastic types together, based on their role in traditional mechanical recycling processing.
The recycling industry commonly differentiates between seven resin types, of which five overlap with our medical plastics categorization: PET, HDPE, LDPE, PP and PS. These plastics are easily recyclable in the current recycling system. [21]
While separating the plastic waste into these resin types is possible, either through manual labor or automation, it can be very inefficient. Especially when mixed with the municipal waste stream, as it is currently often done, a lot of contaminants and lots of inefficiencies are introduced.[22]
By separating the waste at the source and providing uncontaminated, single material streams of these plastics we provide waste handlers with a clean, direct source of high quality, recyclable plastics. While some of these plastics are compatible with traditional mechanical recycling possessing, others (especially multi materials) are only recyclable through more advanced technologies (chemical recycling). These chemical ways of recycling are a lot less established in the U.S. and demand a high upfront investment, but could be highly profitable, considering the vast amounts of plastics that currently go unrecycled.[23]
In addition to our five mechanically recyclable categories we therefore also introduce a sixth multi material category. This category outputs a multi material plastic waste stream that could be processed by a chemical plastic recycler.
At last we also need a seventh category for non-plastic waste. While our bin should serve as a plastics-only solution, human error will most likely introduce non-plastic materials into our system.
This leaves us with seven categories along which we separate the waste:
- PET
- HDPE
- LDPE
- PP
- PS
- Multi Materials
- Other
The Sensors
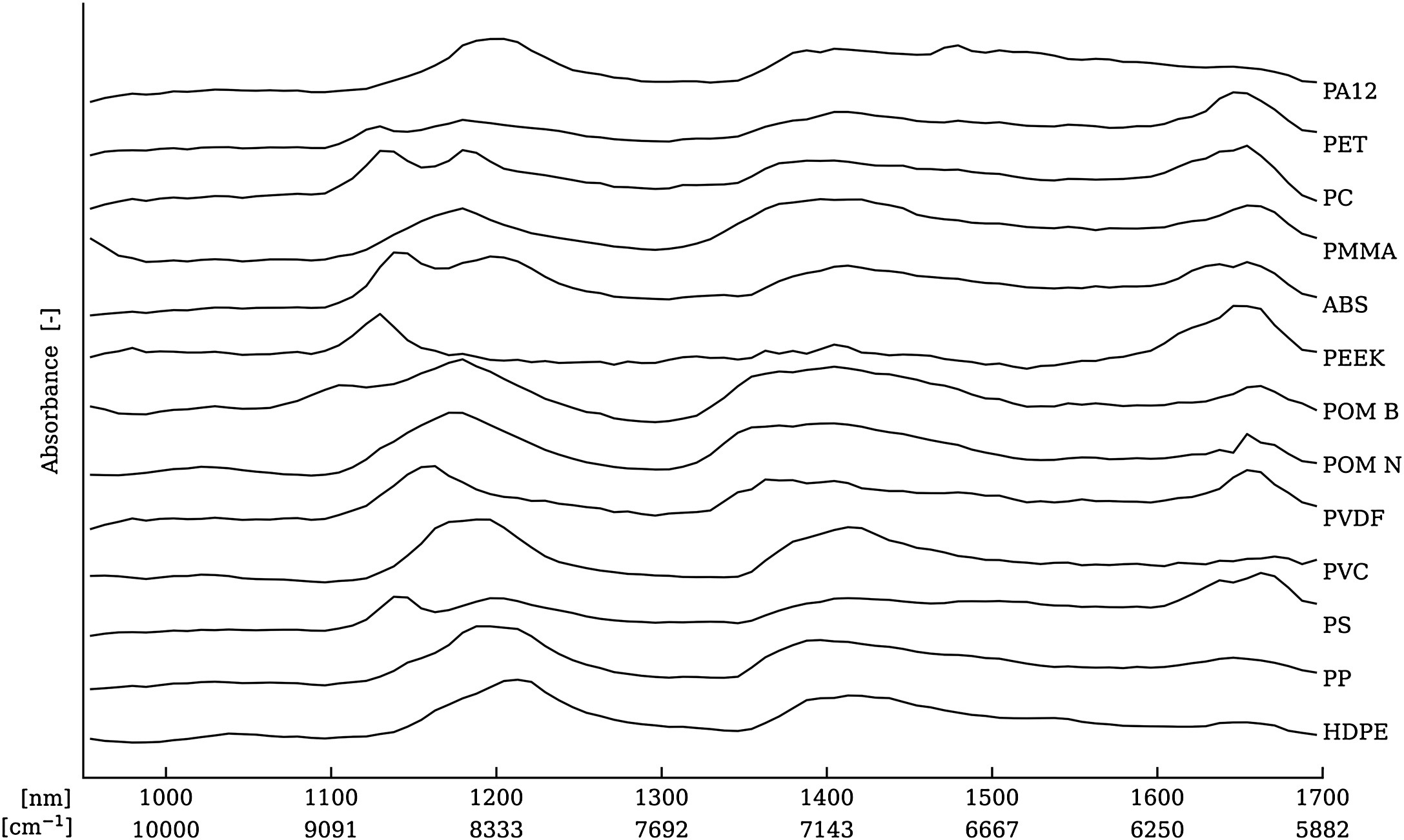
To sort the different types of plastics correctly, we have chosen to make the plastic classification via in-line hyperspectral camera analysis and unsupervised machine learning. This technology has been developed by Aarhus University together with the Danish Technological Institute and a team of Danish companies; Dansk Affaldsminimering, Makeen Energy and Dansk Retursystem. It is a brand new , innovative technology that differentiates between the types of plastic based on the chemical composition of the waste, thus increasing the accuracy of the sorting process. In order to do this, the system applies unsupervised machine learning on short wave infrared hyperspectral data to build a model for classification of plastics.
Even though the hyperspectral system is a very new and quite expensive technology, we chose it due to its perks over the usual plastic sorting technologies. The most used plastic sorting technique nowadays is Near Infrared Spectroscopy, completed by human sorting. The technology uses near-infrared region of the electromagnetic spectrum to measure the absorbance and scattering of light of specific resins [24]. These resins are solid or liquid synthetic organic polymers that are used as the basis of plastics. To translate, NIR spectroscopy is used to identify the absorption bands of different types of plastic, thus providing the information needed to separate them [24]. When looking at the advantages of Near Infrared Spectroscopy, one can find that it is a very fast technique which is also non-destructive, meaning that the plastic can be recycled after being analyzed. However, the disadvantages of this technology are quite significant as well. Most importantly, it does not provide accurate results when the plastic sample is too small, transparent or filled with carbon black. This is why, many times, NIR sorting is completed by human workers.
This is the main reason why we chose the hyperspectral camera system over the NIR. Both systems come at quite a high cost, however, the hyperspectral camera represents a highly promising alternative, designed to overcome the obstacles of the NIR, thus completely automating and improving the sorting process.
Having all of this in mind, a good way to work with materials, identify them or define their properties is to study how light interacts with them. The hyperspectral camera recognizes materials based on their spectral signatures (how much light is absorbed/ reflected/ transmitted). A spectrum represents the amount of light in different wavelengths. The hyperspectral sensors collect information as a set of 'images'. Each image represents a narrow wavelength range of the electromagnetic spectrum, also known as a spectral band.
The data collected by the hyperspectral sensors is processed using principal component analysis (PCA) and K-means clustering for differentiating the types of plastic.
When it comes to the setup of the hyperspectral system, two rows of four halogen spots (12 V, 20 W) illuminating it at a 45° angle are used. The line-scan hyperspectral camera should be equipped with a spectrograph (QiSpec, QT5022K-I320-SWIR, Qtechnology, DK).
Besides increased accuracy, we have also chosen this model for the future perspective of replacing any kind of manual sorting with an automated one. The system currently is capable of differentiating among 12 types of plastics, however we want to adapt it to our 7 categories of plastics. The bin will also have another bin, besides the 7 plastic ones, for any waste not fitting into the 7 plastic types.
The bin has also a digital signaling system for the case in which at least one of the bins is full. When the bin is full, the bin will close and a warning signal will be sent to the waste management of the hospital. We want to achieve this by using a distance sensor. After doing some research , we have found two types of distance sensors specifically designed for waste bins[25]:
- The Benewake TF Series Distance Sensors
- The Benewake CE30 Series 3D LiDAR Sensors
The two categories of sensors are specially created for a specific type of bin, as shown in the two figures on the side. Having in mind that our product must have the most efficient space design for the 8 bins, we chose to use the Benewake TF Series Distance Sensors, as the bins will be tall and narrow.
The Compression Mechanism
One of the features that could be added to the design is a trash compressing mechanism. The best solution to achieve this would be by using a vertical compactor. These compactors have a small footprint and are perfect to use in small, crowded spaces, like hospitals. When the compactor chamber is full, its ram is activated by a switch causing the ram to move down on the waste and compress it.
The process of a vertical compactor creates a bale or block that can be used for recycling. After the containers are full, they can be kept on site to decrease the frequency of pickups and therefore, also transportation and disposal costs.[26]
Amount of waste in the bin
Per patient per day between 25 pounds and 34 pounds of waste of produced[27]. Of this waste, about 20% to 25% are plastics[28]. When we take an average of both these number this will mean approximately 6,64 pounds of plastic waste per patient per day. In the bin we designed only collects general, non-infectious waste. Of the 6,64 pounds of plastic waste about 85% of it is general waste, so approximately 5,64 pounds of general plastic waste per patient per day which our bin can collect[20]. When calculating this in kilograms this will be approximately 2,5 kilograms. To estimate how much fits into the bin the number of liters per kilogram was calculated. This calculation is based on the assumption that 1 kilogram of plastic was equals approximately 26,32 liters[29]. The measurements of one compartment in our bin are 30x60x90 cm which means that 162 liter fits into one compartment. Our bin will have 7 compartment which means that 1134 liter of plastic waste will fit in total in our bin. Assuming that indeed one patient produces 2,5 kilograms of plastic waste per day and that 1 kilogram equals 26,32 liters, approximately the plastic waste of 17,2 patients can be collected by one bin per day. This is however assuming that the different types of plastics are equally divided so that all the compartments are full at the same time. This will most likely not be the case so the expectation is that the bin has to be unloaded earlier. On the other side, there will be a compressor in the bin which causes a significate decrease of the volume of the plastic waste which will mean that more waste can be collected by the bin. So keeping these factors in mind, the estimation is that the bin will be able to collect at least the plastic waste of 17,2 patients per day, and probably even more.
Technical Design Decisions
Motors and Actuators
The main movement is the vertical positioning of the rectangular box containing the trash, when it is first inserted in the dustbin. For now, lets call this the the 'trash box'. The trash box needs to move vertically (on the y axis); it needs to be really accurate and fast. It also needs to be able to support heavy weight if someone throws some heavy trash in their. Hence, for optimal precision, the best type of motors to use will be Stepper Motors, more accurately a close loop bipolar stepper motor.[30]
Stepper motors are easily available and are used very commonly for CNC applications and 3-d printers, which means there are plenty tutorials on how to control them precisely. A NEMA 23 Stepper Motor seems ideal for the use cases describe above. It is more advisable than a NEMA 17 as it can hold more weight, and can go faster than a NEMA 17 Motor. According to StepperOnline[31], a NEMA 17 can go up-to 3000 RPM, and it has a maximum thrust up-to 27kg when supplied 3A of current. [32]. All of these specification cover the use cases for vertical movement perfectly. To achieve fast movement, it is not advisable to use a nut screw for movement like many 3d printers do, rather it is better to use a belt driven movement system. This[33] is a good tutorial which explains Belt Driven vs Screw Driven CNC movement systems.
The trash box does need to open and close. The motors in there need to be durable, and should have enough holding torque such that if a heavier than expected object is thrown into the trash box, then the doors of the trash box do not open. High Powered small servos such as this one[34] would be ideal for this task. The optimal trash box door would need 2 servos similar to this one, as these servos have high torque and metal gears which ensure that they wont break under high load. Each servo can be placed on one side of the door, serving as a hinge. If 2 servos fail to do the job in the prototype, it will be advisable to make use of 4 servos, where you have 2 for each door.
A should have listed on the Moscow list, is a vertical ram system for trash compression. For this, powerful electric linear actuators are needed. Electric Linear Actuators are a type of actuator that converts energy and signals into a linear motion, in other words a backward or forward motion. This linear motion is then used to tilt, lift, push or pull an object where force is required. This can be done through electrical AC and DC motors, or hydraulics and pneumatics[35].
Many actuators are available, but unfortunately they are really expensive, it might be advisable to make one ourselves. As this is a should have and not a must have, for a prototype, this is one part that can be skipped!
Material Choices
The outside of the actual dustbin should be made using 3003 Aluminum Sheets. The reason this is optimal is because it is easily available, cheap, paintable, and it has superior corrosion resistance and is easy to work with. All the sharp edges can be contoured such that it does not harm anyone, and thus it would fulfill the 'must have' condition of being safe. Furthermore, 3003 Aluminum is strong and durable enough for the current use cases. Its tensile yield strength averages around 27000 Psi and ultimate strength averages around 29000 Psi[36]. Tensile Yield strength basically means the maximum amount of strength that can be applied before the aluminum deforms permanently. However, this is not needed for a prototype, for making a prototype for demonstration purposes, only a skeletal model of the dustbin is required. The most important factor is to make sure it is stable, the movement mechanism can still happen, and that the correct dimensions can be achieved. Thus, it is advisable to use 40mm x 40mm T-Slot Aluminum Profiles to make a prototype. These profiles can be milled to the exact dimensions required for the machine by many different manufacturers in the Netherlands, as these profiles are very commonly used for CNC machines. They are durable, and strong enough for a prototype. The fact that they are used by many hobby CNC makers, makes these profiles very easy to use and build stuff with, and there are a lot of guides on the internet on how to go about working with T-Slot aluminum profiles. These profiles should be used to make an outer skeletal frame of the dustbin, and all the other parts of the dustbin can be secured to these profiles. Since they are used for CNC machines, manufacturers are obliged to mill these profiles with precision.
Dimensions
The length of the machine will be quite long, approximately 320 cm long. We have 7 compartments, and possibly one trash compressor, which would require us to have atleast 30*8 = 240 Cm of length. If we want to leave a gap of 10 centimeters in between all of the bins, and the edges of the machine, then thats 80 more cm. While one can argue that the dustbin is too long, it needs to be placed correctly in the hallway, and all 7 compartments are necessary for the use cases.
For the height of the machine we have a 10 cm raise from the bottom, 5 cm for the wheels, a 90 cm tall bin, a sorting box which is 30 cm tall, and the roof of the machine, which will be around 10 cm long, making the whole machine approximately 1.3 m tall. The width of dustbin needs be around 0.8m wide.
Micro-Controllers
Training a Neural Network with all the different items takes a lot of time, but luckily the training doesn't need to be done in the dustbin itself, classification does though! Luckily, classification is done way faster, but the speed does depend on the processor of the micro-controller. Hence, it's more advisable to use an STM32 based micro-controller over an Arduino. An STM 32 has a 32-bit processor while a regular Arduino UNO has an 8-bit processor. STM32 pays more attention to engineering practice. In fact, there are many simple instruments in the factory, such as temperature controllers, ordinary motor controllers, low-end PLCs, and some civilian toys, game controllers, wired keyboards and mice, and other peripherals and so on are very practical[37]. While it is harder to program using the STMCube IDE (standard STM 32 IDe), it is also something which has a lot of documentation online and many tutorials are available. A good beginner STM 32-bit board is the Nucleo-F446Re, its pin configuration it similar to that of an Arduino Uno, and it can also be programmed using the Arduino IDE, making the board easier to use and understand for the purposes of making a working prototype[38].
Other Components
The board unfortunately does not come inbuilt with a Wifi module, so a separate ESP8266 Wifi Module is necessary for OTA-updates and for ensuring internet connection with the dustbin. Another component necessary would be motor drivers for the NEMA 23 Stepper Motor; the TB6600 is a popular and easy to use choice, and is compatible with the recommended motor[39].
One of the could haves listed in the in the Moscow list above is an interactive display for the user. A display which indicates how full the dustbin is, would be really helpful for a prototype. There are many displays available on the market, and they also have touch screen, although for ease of use and connectivity for the prototype, it will be better to use an O-Droid unit! Odroid is a company which makes peripherals for a variety of a embedded systems applications! The Odroid VU-5A is a 5-inch display unit, with android built in [40]. Furthermore, this display can be connected to the STM-32 board, and it can give commands as it has serial output. The fact that this has android built in, will be really convenient as it is fairly easy to set up a basic android application with serial communication amongst the STM32 board and the O-droid unit; a fancy GUI displaying the properties of the dustbin is not really necessary for the prototype.
Cost Analysis
For a prototype, we made a detailed cost analysis with the bare-minimum requirements who's purpose is to just test out sorting and movement. Keep in mind that the costs of items are found online, and can differ from website to website, and are rough approximations of what the cost in right now. The most expensive part is the hyper-spectral camera. It is a relatively new technology compared to everything else and is also the hardest to source. For the dustbin to manufactured and available publicly, this is the biggest cost challenge out of all the items.
Discussion
For the bin we tried to have the research on the design and the technical parts of the bin as completed as possible but due to lack of time we did not manage to look into every part of the bin and the process around the bin. So there are still a couple of things we think should be researched more.
Firstly within this project we considered the inclusion of a compression mechanism. This can be a very useful addition to the bin because plastic waste mostly takes much more volume than needed. With the implementation of a compressor as much waste as possible will fit into the bin which results in a longer period between unloading the bin. This will be cost efficient as well as time efficient because the bins have to be unloaded less so less staff is needed to unload the bins and less time needs to be spent on constantly unloading the bins. A rough design of the compressor is already included within our final design, but more research would be needed to realize the implementation.
Secondly one of the main issues we encountered during the development of our product was the challenge of sterilizing contaminated waste. While our product could function effectively in a medical context, it was clear that implementing a sterilization mechanism that would function efficiently and reliably would be difficult. As a result, we decided not to tackle this issue and instead focus on the sorting aspect of waste management. In addition the medical sector presents a highly regulated environment, where specifically plastic products such as packaging or certain tools will often be regulated through centralized bodies such as the Food and Drug Administration (FDA)[41]. A considerable and potentially more effective way of increasing non-infected plastic-waste recycling in american hospitals might therefore lead through regulated and standardized labeling on packaging that helps easily identify and discriminate between different types of plastics. This means that while our product could function well in a medical context and brings with it considerable benefits, the medical sector might not be the most optimal context for our type of product. Since plastic waste is produced in many different contexts and the sorting algorithm and design parameters could easily be altered to fit a different context, our design could be useful in other fields like manufacturing, public places, schools or more.
Furthermore, we think it would be very helpful if a signal can be send to the waste management system so that they can keep track of which bin is how full and when it needs to be unloaded. This will help the waste management system to work more efficiently because they don’t have to spend time to check the bins if they have to be unloaded, instead they exactly know which bin they have to unload. This also ensures that no problem arises with bins not opening up because they are full. To make this implementation as useful as possible more research needs to be done.
Lack of knowledge about the Danish sorting algorithm is also a big issue to tackle. We were not able to figure out how accurate the the classification process was as we were not able to get access to the Neural Network ourselves, and there is not enough information for us to determine the speed of recognition, or to validate the training process of the Neural Network, as it is really new
Another problem we were not able to find a solution for is how to deal with waste thrown into the bin which are multiple objects or objects which are not only made of plastic but also different kinds of materials. For the bin a hyperspectral camera is used. When multiple objects are thrown in at ones, it is likely that the camera will analyze only one of the objects. When this happens and the other object is of a different kind of plastic, the machine will throw both of the objects in the compartment where the object that it detects should be sorted. When the other object which is not detected is of another type of plastic, it will mix up the sorting process. Different types of plastic will be mixed up in that compartment which will cause problems in the recycling process, which may even be harmful. Therefore, it is really important that there comes a solution to this problem. Somewhat the same problem occurs when an object with multiple materials is thrown into the bin. Here the camera will most likely again analyze one of the materials. Which of the materials it detects will decide in which compartment of the bin the object will be thrown. However, when there are two kinds of materials and the object comes into a compartment which only collects a specific type of plastic, it will mix up this sorting process as well. One of the solutions we though of for these problems is a rotation camera, so it detects different angles of the object and in this way also detects if there are multiple materials. This can be a good solution for when there is one object with multiple materials. The machine should however know what to do in this situation, in which compartment it should throw the object. For the problem with multiple objects the rotating camera can also be part of the solution. However, there should still be thought of the best way to make sure that the different objects are both being thrown into the right compartment after being analyzed.
Lastly, we recognized the importance of conducting user research to ensure that our product meets the needs of its users. While we sent an email to 50 American hospitals requesting feedback on our product, we did not receive any useful responses in time to include in our project report. Moving forward, we believe that conducting more research and user analyses will be crucial to ensuring the success of our product.
Conclusion
During the research for the design concept of our product, we gained a lot of different kinds of perspectives on our project. Overall, we believe that a lot can be done to improve the level of recycling plastics in hospitals. Our product can be a good solution. However, we also came to the insight that it will be a hard task to design a bin which is complete to the level that it is efficient enough to make a real change. In hospitals there are a lot of extra factors which have to be taken into consideration when designing a product. Therefore, it would be better to first use the bin in different industries with less complex conditions. This will most likely mean that the bin should be adjusted to the plastic waste in that industry, but we believe this can be easily done by adjusting some elements of the bin. When the product proofs to be effective in a less complicated environment, the bin can be implemented into environments with more complex factors and waste management systems. In either environment, a lot of research still needs to be done to make sure the bin works well and is efficient. For now, it is hard to draw a conclusion on how effective the bin will be because this will depend on a lot of different factors, but because almost none of the plastics in hospitals are being recycled now, the smallest things can already make a difference.
Appendix
Logbook
Week | Name | Total | Breakdown of hours |
---|---|---|---|
1 | Luta Iulia Andreea | Team formation + sending emails | |
Sonia Roberta Maxim | 3 | Team formation + sending emails (1h), research ideas for first meeting (2h) | |
Marie Spreen | 1 | Team formation + research for ideas | |
Fenna Schipper | 1 | Team formation + research ideas for first meeting (1h) | |
Hakim Agni | 1 | Team formation + reading course info | |
Lazgin Mamo | 1 | Team formation | |
Dhruv Manohar | 1 | Team formation | |
2 | Luta Iulia Andreea | 6 | online meeting (1h), first meeting + tutorial (2h), literature study (3h) |
Sonia Roberta Maxim | 6 | first meeting + tutorial (2h), literature study (3h), online meeting (1h) | |
Marie Spreen | 6 | research + meeting + online meeting | |
Fenna Schipper | 6 | literature study (3h) and 2 meetings (3h) | |
Hakim Agni | 4 | Research (3h) + online meeting (1h) | |
Lazgin Mamo | 6 | Literature study (3hours) and meetings (3 hours) | |
Dhruv Manohar | 0 | Was sick and had not found a team yet | |
3 | Luta Iulia Andreea | 8.5 | Research + State of the art, tutorial + 2 meetings (3.5h), |
Sonia Roberta Maxim | 8.5 | Research + State of the art (5h), tutorial + 2 * meetings (3.5h), | |
Marie Spreen | 10 | survey research + Meetings + general research + contact hospitals | |
Fenna Schipper | 8.5 | research + problem statement + meetings + start MoSCow | |
Hakim Agni | 6 | Research (3.5h) + online meeting (1.5h) | |
Lazgin Mamo | 6 | meetings(3 hour) + research paper for importance of recycling bin (2 hours)+ writing the objective on wiki (1 hour) | |
Dhruv Manohar | 11 | Meetings (3 Hours) + catching up with current work (2 hours) + research into sorting mechanisms (3 hours) + research into other sorting bins (2 hours ) + tutorial (1 hour) | |
4 | Luta Iulia Andreea | 9 | meetings, tutorial, beginning research on design |
Sonia Roberta Maxim | 11 | structuring wiki page, research on users, meetings | |
Marie Spreen | 12 | contact hospitals + meetings + research on tertiary users | |
Fenna Schipper | 11 | research + writing secondary users + meeting | |
Hakim Agni | 8 | meeting (1 hour) + research current workflow (4 hours) + research medical waste (3 hours) | |
Lazgin Mamo | 8 | meetings (3 hour)+ research primary users need and writing the wiki (5 hours) | |
Dhruv Manohar | 12 | meetings + design team meetings + design research + research into motors and | |
5 | Luta Iulia Andreea | 12 | 3 meetings, tutorial, designing moscow requirements and usecases, reasearch |
Sonia Roberta Maxim | 12 | Tutorial + 3 * meetings, Research + Helping with moscow list and use cases, updated wiki | |
Marie Spreen | 10 | meeting + design-research + meeting + argument write up | |
Fenna Schipper | 10 | meetings + research + writing argumentation design choices (infectious vs non-infectious) | |
Hakim Agni | 7 | research (2 hours) + finding hospitals (5 hours) | |
Lazgin Mamo | 10 | meetings + helping with Moscow list + researching technical needs for the robot | |
Dhruv Manohar | 11 | meetings + design research + research into CNC movement systems + research into stepper motors | |
6 | Luta Iulia Andreea | 12 | 2 meetings, tutorial, research on must haves design, writing findings in wiki + argumentation |
Sonia Roberta Maxim | 12 | meetings, tutorial, research on should haves and could haves, writing argumentation on wiki | |
Marie Spreen | 16 | 2 meetings, tutorial, edit moscow, flowchart, blender model bin, generate blender animation | |
Fenna Schipper | 11 | meetings + research design + sketching design of the bin | |
Hakim Agni | 10 | finding and contacting hospitals + cleaning up the wiki | |
Lazgin Mamo | 3 | due to sickness only joined meetings | |
Dhruv Manohar | 13 | meetings + research into micro-controllers + research into o-droid unit + research into materials | |
7 | Luta Iulia Andreea | 12 | 2 meetings, research on how the hyperspectral system works, writing findings in wiki |
Sonia Roberta Maxim | 12 | meetings, economic analysis+ amount of waste, writing on wiki | |
Marie Spreen | 12 | meetings + blender animation + prep presentation | |
Fenna Schipper | 15 | meetings + research + writing amount of waste in bin | |
Hakim Agni | 12 | meetings + cleaning up the wiki + research | |
Lazgin Mamo | 12 | meetings + making the slides. | |
Dhruv Manohar | 16 | meetings + research into aluminum profiles and prototype techniques + making slides + script for presentation + presentation prep | |
8 | Luta Iulia Andreea | 9 | presentation, finishing hyperspectral technology part and meetings |
Sonia Roberta Maxim | 9 | presentation, cleaning up references and wiki editing, meetings | |
Marie Spreen | 9 | presentation + meetings + wiki editing | |
Fenna Schipper | 11 | meetings + writing discussion + conclusion + last checks wiki | |
Hakim Agni | |||
Lazgin Mamo | 8 | peer review meeting and attending the presentations session and organizing wiki (problem statement and users) | |
Dhruv Manohar | 14 | meetings + putting everything on the wiki + research into cost analysis |
- ↑ Jump up to: 1.0 1.1 Plastics, R. (2018, April 30). Why Are Plastics Essential in the Medical Industry - Raya Plastics. Rayda Plastics. https://www.rayda.co.uk/blog/plastics-in-medicine/
- ↑ Plastics, R. (2018b, April 30). Why Are Plastics Essential in the Medical Industry - Raya Plastics. Rayda Plastics. https://www.rayda.co.uk/blog/plastics-in-medicine/
- ↑ Jump up to: 3.0 3.1 3.2 3.3 3.4 Joseph, B., James, J., Kalarikkal, N., & Thomas, S. (2021e). Recycling of medical plastics. Advanced Industrial and Engineering Polymer Research, 4(3), 199–208. https://doi.org/10.1016/j.aiepr.2021.06.003
- ↑ CNS MEDIA. (2022, May 5). How much? US losing billions every year to landfilled plastic waste, finds Department of Energy. .packaginginsights.com/. https://www.packaginginsights.com/news/how-much-us-losing-billions-every-year-to-landfilled-plastic-waste-finds-department-of-energy.html
- ↑ Woolhandler, S., & Himmelstein, D. U. (2014). Administrative Work Consumes One-Sixth of U.S. Physicians’ Working Hours and Lowers their Career Satisfaction. International Journal of Health Services, 44(4), 635–642. https://doi.org/10.2190/hs.44.4.a
- ↑ S. (2022, May 4). Efficient Waste Management Can Help Improve Nurse Well-Being. Stericycle. https://www.stericycle.com/en-us/resource-center/blog/making-nurses-days-easier-with-more-efficient-waste-management
- ↑ Rushton, K. (2022, February 28). Machines developed that can separate 12 different types of plastic. Innovation News Network. https://www.innovationnewsnetwork.com/machines-developed-separate-12-different-types-plastic/16788/
- ↑ Jump up to: 8.0 8.1 Henriksen, M. L., Karlsen, C. B., Klarskov, P., & Hinge, M. (2021). Plastic classification via in-line hyperspectral camera analysis and unsupervised machine learning. Vibrational Spectroscopy, 118, 103329. https://doi.org/10.1016/j.vibspec.2021.103329
- ↑ Hospital Recycling Case Studies | HPRC. (2022, May 5). Healthcare Plastics Recycling Council. https://www.hprc.org/hospital-recycling-case-studies/
- ↑ TrashBot: The smart recycling bin that sorts at the point of disposal. (2023, February 28). CleanRobotics. https://cleanrobotics.com/trashbot/
- ↑ ECOSTERYL : Traitement et recyclage des déchets médicaux. (2021, May 26). Ecosteryl. https://www.ecosteryl.com/
- ↑ ECODAS. (2022, September 6). ECODAS T100 - DASRI, treatment of infectious , hospital and medical waste. DASRI, Treatment of Infectious , Hospital and Medical Waste. https://www.ecodas.com/en/ecodas-t100-en/
- ↑ Sürme, Y., & Maraş, G. (2022). Recycling, responsible consumption and nursing: A qualitative study of surgical nurses’ recycling and medical waste management. Journal of Nursing Management, 30(8), 4514–4522. https://doi.org/10.1111/jonm.13891
- ↑ Windfeld, E. S., & Brooks, M. S. (2015). Medical waste management – A review. Journal of Environmental Management, 163, 98–108. https://doi.org/10.1016/j.jenvman.2015.08.013
- ↑ https://www.pulpandpaper-technology.com/articles/plasticwaste
- ↑ Statista. (2023, February 6). Plastic waste managed in the U.S. 2018-2021, by method and scenario. https://www.statista.com/statistics/1339439/plastic-waste-management-by-method-us/
- ↑ Jump up to: 17.0 17.1 https://www.hprc.org/wp-content/uploads/2022/05/Advanced-Recycling-White-Paper-Phase-1.pdf
- ↑ http://www.hospitalbins.com/pdf/health_technical.pdf
- ↑ https://healthfacilityguidelines.com/ViewPDF/ViewIndexPDF/iHFG_part_c_space_standards_dimensions
- ↑ Jump up to: 20.0 20.1 World Health Organization: WHO. (2018, February 8). Health-care waste. https://www.who.int/news-room/fact-sheets/detail/health-care-waste
- ↑ RTS - Recycle Track Systems. (2022, October 28). The Complete Plastics Recycling Process - Recycle Track Systems. Recycle Track Systems. https://www.rts.com/blog/the-complete-plastics-recycling-process-rts/
- ↑ C. Rizan, F. Mortimer, R. Stancliffe, M.F. Bhutta; Plastics in healthcare: time for a re-evaluation; J. R. Soc. Med., 113 (2020), pp. 49-53
- ↑ https://cen.acs.org/environment/recycling/Plastic-problem-chemical-recycling-solution/97/i39
- ↑ Jump up to: 24.0 24.1 https://www.solidscanner.com/en/basics-and-limitations-of-nirs-nirs-and-how-it-is-used-in-plastic-recycling/
- ↑ http://en.benewake.com/news/detail/5da03c994d839408076b615b.html
- ↑ Trash Compactors: Types, Uses, Features and Benefits. (n.d.). https://www.iqsdirectory.com/articles/baler/compactors.html
- ↑ Waste - Sustainability Roadmap. (n.d.). http://www.sustainabilityroadmap.org/topics/waste.shtml#.ZDG5SHZBxPY
- ↑ Jain, N., & LaBeaud, D. (2022). How Should US Health Care Lead Global Change in Plastic Waste Disposal? AMA Journal of Ethics, 24(10), E986-993. https://doi.org/10.1001/amajethics.2022.986
- ↑ Convert waste volume to weight – Your description. (n.d.). BRANZ. https://www.branz.co.nz/sustainable-building/reducing-building-waste/assessing-waste/volume-weight/
- ↑ https://ieeexplore.ieee.org/abstract/document/4510518
- ↑ https://www.omc-stepperonline.com/support/what-is-the-maximum-speed-highest-frequency-of-the-stepper-motor
- ↑ https://novantaims.com/hybrid-stepper-motor/lm23-nema-23-3-0a-1-8-external-linear-stepper-motor/
- ↑ https://www.youtube.com/watch?v=NTW2Be1pOGw
- ↑ https://www.conrad.nl/nl/p/motor-micro-servo-high-powered-high-torque-metal-gear-mg92b-adafruit-2307-1516601.html
- ↑ https://nl.rs-online.com/web/c/mechanical-power-transmission/electric-actuators/electric-linear-actuators/
- ↑ https://www.thomasnet.com/articles/metals-metal-products/3003-aluminum/
- ↑ https://www.orientdisplay.com/stm32-vs-arduino/
- ↑ https://www.st.com/en/evaluation-tools/nucleo-f446re.html
- ↑ https://www.tinytronics.nl/shop/en/mechanics-and-actuators/motor-controllers-and-drivers/stepper-motor-controllers-and-drivers/hy-div268n-5a-tb6600-stepper-motor-controller-5a-8-42v
- ↑ https://www.sossolutions.nl/odroid-vu5a-5inch-hdmi-display-inclusief-multi-touch-en-audio
- ↑ Center for Devices and Radiological Health & Center for Devices and Radiological Health. (2018, March 22). Code of Federal Regulations (CFR). U.S. Food And Drug Administration. https://www.fda.gov/medical-devices/overview-device-regulation/code-federal-regulations-cfr
5. https://www.sciencedirect.com/science/article/pii/B9780444638571000012