PRE2024 3 Group5
General Notes
TRIDENT (Tactical Robotic Inspection & Detection for Enhanced Nautical-hull Testing)
Tasks for this week:
- Luuk - Localization on the hull
- Anh - Ultra sonic sensor & inform Luuk and Luca about sensors stuff
- Simon - State of the Art of the current robots
- Anton - Continue writing about the MFL & inform Luuk and Luca about sensors stuff
- Luca - Physics for the simulation
Points from last meeting:
- What type of ship of ships we are inspecting?
- Ships with metal hulls
- Ships with a hull flat enough that the robot can drive on them
- What is the effective scanning area?
- Needs to be researched
- What would be the position of the sensors on the robot?
- On the underside and probably at the middle
- How would the movement be integrated with the sensors?
- What is the effective area of the sensors?
- How fast can you travel for robust detection with the sensors?
- How does the movement connects to localization?
- What would be the top speed?
- How are we connecting the sensor read-out to the localization of the robot?
Integration:
In the presentation: Show the robot going over the hull and "find a crack" and then display the flux lines and images of the crack.
Movement & Sensor integration: Anton and Anh will inform Luca and Luuk about how fast the robot can travel for robust crack detection. (Look at eddifys site)
Localization & Sensor integration: Anton and Anh will look into how much data can be captured by the robot at once and tell Luuk so he can know how to localize the data on the model of the ship.
Group Members
Name | Student ID | Department | |
---|---|---|---|
Anton Veshnyakov | 1866508 | Electrical Engineering | a.veshnyakov@student.tue.nl |
Luuk Kool | 1883542 | Electrical Engineering | l.j.c.kool@student.tue.nl |
Anh That Tuan Ton | 1816209 | Electrical Engineering | a.ton.that.tuan.anh@student.tue.nl |
Luca Rutz | 1781294 | Electrical Engineering | l.d.rutz@student.tue.nl |
Simon van Valkengoed | 1881361 | Electrical Engineering | s.h.v.valkengoed@student.tue.nl |
Problem Statement
The hull of an ocean-going vessel is subjected to immense forces and the unforgiving conditions of the ocean. As a result, these vessels must undergo hull inspections twice within every five-year period in a dry dock. These regulations originate from the SOLAS convention and are overseen by the Maritime Safety Committee of the IMO[1]. For bulk carriers and oil tankers, an example is Resolution MSC.461(101), which mandates that their hulls be inspected twice every five years in a dry dock, with certain exceptions[2].
A key challenge for shipyards conducting these inspections is the inability to accurately predict how long a vessel will remain in dry dock. This uncertainty stems from what the inspection would uncover, as the extent of necessary repairs remains unknown until the inspection procces is completed. Consequently, it is diffucult for shipyards to efficiently plan and allocate their dry dock facilities.
To mitigate this issue, it would be advantageous for shipyards to conduct preliminary inspections that identify serious structural concerns in advance. This proactive approach would allow shipyards to anticipate potential repair needs, improve scheduling, and optimize dry dock usage.
Deliverable and goals (Maybe some small tweaks)
The deliverable of this project will be a simulation of a robot that inspects the hulls of ships. This simulation will include the sensing part of a robot (measure its location and dynamics, measure the hull integrity and process it), but will not include actuators such as wheels or thrusters. The simulation should work for every (smooth) model of a ship hull.
The main goals are:
- Measure location with suitable precision and map this position on the manifold of the hull.
- Research non destructive testing for observing a hull underwater.
- Implement movement of the robot in a simulation software.
- Find the relevant user requirements and uses.
Planning
Week | Tasks |
---|---|
1 | Initial group set-up and task planing. |
2 | Literature research. |
Reach out to a specialist in the field. | |
3 | Research subgoals |
4 | Implement subgoals |
5 | Implement subgoals |
Draw conclusions and possible future improvements. | |
6 | Create the final presentation. |
7 | Finalize the wiki page. |
User Interviews
Damen Group
To better understand what the industry, and thus the users of this product, would want, it was decided to reach out to the Damen Group here in the Netherlands because of their vast knowledge in building, inspecting, and using dry docks.
After reaching out to them we came into contect with Klaas Kuper how is a Area Sales Manger of the Netherlands, Poland and the baltic states. Mr Kuper kindly answerd our questions via the email and invited us for a teams meating which we gladly accepted.
In the team meeting, we discussed the potential use cases for an underwater hull inspection robot. Specifically, we explored the advantages of a survey robot that can assess the structural integrity of a ship's hull with greater accuracy than the current robots, which rely on cameras.
The original concept for the underwater robot was to replace dry dock inspections of the hull. However, Mr. Kuper pointed out that the time saved during dry dock stays would be minimal since the ship would still need to enter dry dock for other inspections and to access areas the robot cannot reach.
He suggested that the robot could be more useful in assessing the ship's hull before it enters dry dock. This would allow the shipyard and the shipowner to better estimate the duration of the dry dock stay and identify necessary repairs in advance. The main advantage of this approach is that the shipyard could better schedule dry dock availability and prepare for upcoming repairs, while shipowners would gain a clearer understanding of the inspection costs and potential repair expenses.
Question | Answers |
---|---|
How often are ship hull inspections needed, and what types of inspections are required? | On average A seagoing vessel is docked 2 times every 5 years. Sometimes one of the dockings can be a so called in water survey.
Type of class survey’s: Periodical surveys:
https://english.ilent.nl/topics/seagoing-vessels https://rs-class.org/en/services/classification-surveys/#:~:text=Classification%20surveys%20of%20various%20purpose,retainment%20and%20confirmation%20of%20the |
How expensive are hull inspections, and what factors influence the cost? | Depends on the scope and the age of the vessel. At a new vessel the scope is limited. If the vessel gets older more items need inspection. |
What are the most expensive or least reliable parts/methods to inspect? | Hull thickness measurement.
https://www.mme-group.com/nl/scheepvaart/ https://www.mme-group.com/nl/maritieme-surveys/ultrasone-diktemetingen-utm/ |
What are the most challenging areas of the hull to inspect and why? | Flat bottom. Due to groundings. Ballast tanks (inside the hull) due to corrosion |
What are the most commonly used methods for ship inspections today? | Drydocking or divers. |
How often are divers used for inspections, and what are the risks involved? | Only for intermediate or bottom survey. Risk that damages are missed / mis interpretated |
What are the most common defects found during hull inspections, and how are they
detected? |
Dents, cracks, punctures, cavitation etc. visually or by 3D measurement. |
Users requirements summery
After talking to various companies in the field of ship construction and maintenance, the following requirements were formulated for the different users.
The shipyards:
- Cost effective system.
- Corrosion detection.
- bio foliage observation.
- superficial and inner metallurgical fracture observation.
The ship owner:
- Time-effective to the point that it does not disrupt the normal shipping process. (that it can be done while a ship is loading/unloading or while it is waiting to dock)
- That the test are Non destructive.
State of the art (WIP!!!)
(state of the art concepts and robots go here)
The current state of the art for underwater inspections of the hull of ocean going vessels are Remotely Operated Vehicles (ROVs) and Autonomous Underwater Vehicles (AUVs), which together are called Unmanned Underwater Vehicles (UUVs). The current state of the art for UUVs is the lithurary review of "A systematic literature review of unmanned underwater vehicle-based structural health monitoring technologies" by Joel Friesen Waldner and Ayan Sadhu[3]
Sources:
Magnetic Flux Leakage (MFL) detection
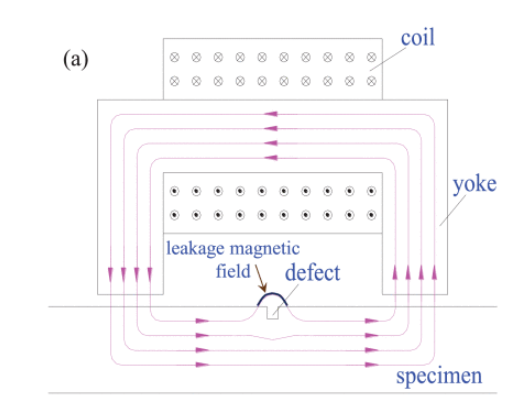
Today, the main energy sources that most people rely on, such as gas and oil, are being transported using pipes running in all kinds of environments. It is crucial to maintain the structural integrity of the pipes as a leak can potentially cause a catastrophe. However, it is impossible to inspect hundreds of thousands of kilometers of pipes visually, both due to the sheer size of them and also due to the fact that some of them run under ground or under water. To tackle this problem, engineers came up with a robot that can enter a pipe and scan it from the inside, looking for potential abnormalities. One of the main tools to accomplish this task is using the Magnetic Flux Leakage technique. Since most pipes are built out of steel, which is ferromagnetic, meaning it conducts magnetic fields within itself, it is possible to recognize a defect in the pipe by measuring the magnetic field that passes through a certain point in a pipe[5]. In a similar manner, this technology can be used on the hulls of ships since they are also made of ferromagnetic materials, usually steel and steel alloys. Since the idea of using MFL for ships is quite novel, little research has been done on implementing the system on a robot or similar machine to carry out the inspection. As a result, we base our research on models and experiments that have been conducted on land based objects, such as pipes and train rails. The assumption here is that using the equations that govern those models and experiments, it is possible to adjust the technique to be used under water.
What is Magnetic Flux Leakage?
In order to understand what magnetic flux leakage is and how it can be useful for detecting cracks and metal defects, we first need to understand the concept of magnetic flux in general. Magnetic flux is the measure of the total magnetic field passing through a given area. Mathematically, magnetic flux is defined as: Φ = B · A · cos(θ), where B is the magnetic field strength [Tesla], A is the area [m2], and cos(θ) is the angle between the area and the magnetic field. Magnetic flux is measured in units of Weber and can be created by magnets that are put in-line with the ferromagnetic material, or by using current carrying wires that induce a magnetic field as can be seen in Figure 1. While most of the magnetic flux is following the shape of the ferromagnetic material, some of it will jump through the gaps that are present in the loop, which is called leakage or fringing. As can be seen in Figure 1, a surface defect, such as a crack, will cause some of the flux to "leak" or take a different path than the straight line it should usually follow. Small amounts of leakage also happen in the gaps between the flux producing yoke and the specimen itself but those can be neglected as they are not usually picked up by the sensors. The sensor used to detect the magnetic field leakage is called a Hall Effect Sensor.
Hall Effect Sensor
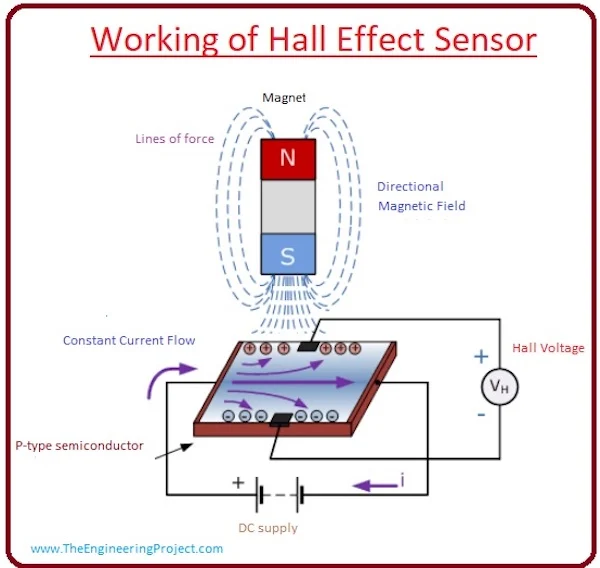
To pick up the magnetic leakage from a defect on a surface, a Hall Effect sensor is utilized. The hall effect is the interaction between a current carrying conductor and a perpendicularly moving magnetic field, when the later exerts a force on the moving charge, making it concentrate on one side of the conductor. As a result of that concentration, a voltage can be created and measured on the transverse side of the conductor. By utilized a Hall effect sensor, it is possible to detect not only the presence of a magnetic field, but also its strength, as it would be proportional to the strength of he induced voltage. The Hall Effect voltage is described by the following equation: VH = IB / qnd, where I is the current through the conductor, B is the magnetic field strength, q is the charge of an electron, n is the charge carrier density, and d is the thickness of the conductor in the direction of the magnetic field.
MFL application in the industries
Magnetic flux leakage (MFL) detection is one of the most popular methods of inspection of structures made out of ferromagnetic materials. It is a nondestructive testing technique which uses magnetic sensitive sensors to detect the magnetic leakage field of defects on both the internal and external surfaces of given structures. [7] The inspection of those structure is often important due to the safety and health risk that small fatigue cracks can cause, especially when talking about oil and gas pipes, or the tanks of a oil carrier ship. IN addition to fatigue cracks, MFL can be used to detect such things as corrosion, erosion and metal loss, although there are more reliable and easier methods to go about detecting those defects. For the pipeline reliant industries, MFL is useful as it can be mounted on a special robot that goes inside the pipe and by suing the MFL can detect defects both on the inside and outside of the pipe without requiring a direct human access to the entirety of the pipe. In the train industry, MFL can be used to detect early-stage fatigue cracks on the wheels, which is crucial for the safety of the train and its passengers, as broken wheels can lead to derailments and catastrophic consequences.[4]
Influence of crack orientation on MFL
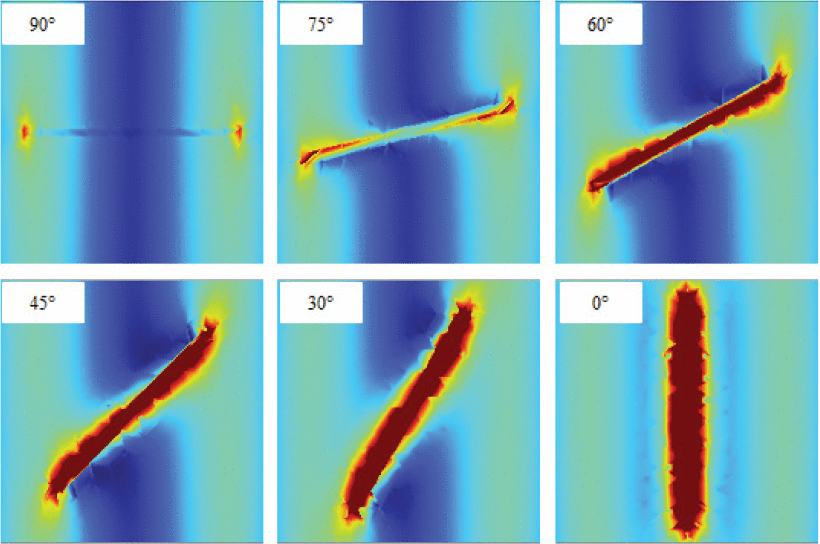
Due to the 3D nature of our world, cracks can be created and then propagate in different direction in the material. When using one MFL sensor it is sometimes hard or impossible to get a strong enough leakage so that it can be detected by the sensor. Additionally, even when using a linear arrangement of of sensors it is still not enough if the crack is perpendicular to the sensor array. [8] As stated in the research paper [8], it is advised to use a circular sensor array in order to achieve the best crack detection and orientation. Figure 3 demonstrates the different digitalized read-outs from the MFL sensor with relation to the angle of the crack to the sensors. The difference of the crack detection as a result of its orientation is explained by the following equation: B' = B · cos(β), where B' is the resulting magnetic flux density across the crack, B is the original flux density, and β is the crack's relative angle with respect to the magnetization direction. Additionally, it has been shown that deeper or wider cracks result in stronger leakage fields, as well as changing the amplitude and spatial distribution of the signal, which makes FML highly suitable for detecting cracks [9].

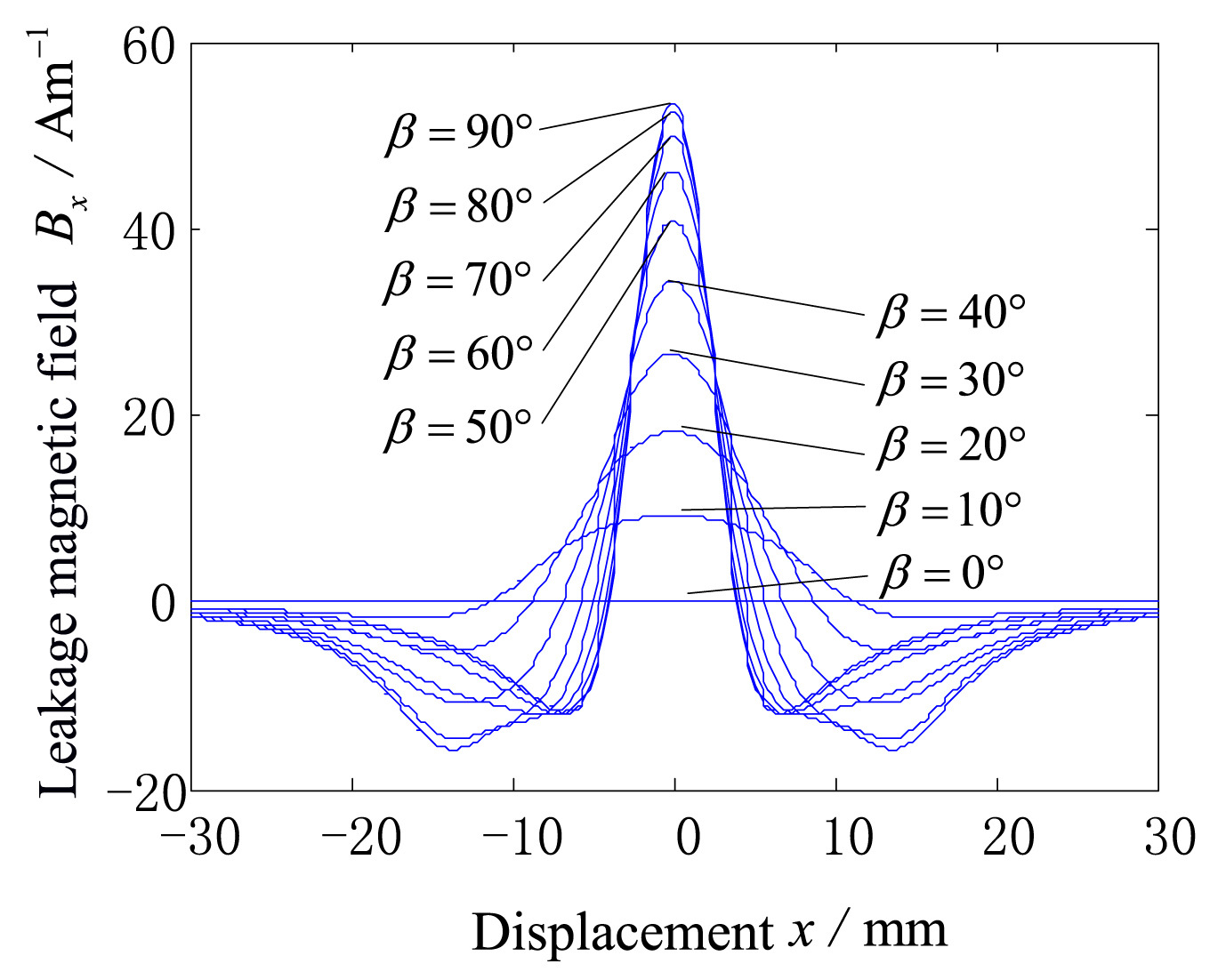
Expanding the equation for the magnetic flux across the crack, the strength of the flux can be expressed as demonstrated in Figure 4. The flux strength relies further on other parameters of the crack, such as its width, length, and depth, where β is the most important variable [10]. Figure 5 Shows how the orientation of the crack in relation to a linear detector influences the strength of the detected flux leakage.
Sensor placement and Scanning techniques
When utilizing MFL for crack detection, there are a variety of different ways to position the sensors. The simplest way is to arrange the sensors in a linear array which allows for a large area coverage while requiring minimal space utilization, making the entire scanner fairly compact. Researchers have built such a sensor array and demonstrated that it can detect cracks in mild steel plates with ease [12]. Furthermore, the detection can indicate the depth and orientation of the crack as signals reach sensors at different times. Another way to arrange the sensors is in a circular pattern. As shown in Figure 3, a circular array of sensors will allow not only for crack detection but also for easier orientation detection. But "looking" at a crack from multiple angles, the circular array can at once indicate the crack orientation without the need to swab the whole area, unlike the linearly arranged sensors [8]. Another less common, and as of yet experimental, way to use MFL is called Pulsed MFL, or PMFL. By pulsing the external magnetic field by means of an electromagnet, PMFL offers better defect localization and sizing by using features in the time-frequency domain. A research paper on the topic showed that it is the best solution overall for both on-surface and sub-surface crack detection, which makes it suitable for applications where access is limited to only one side of the inspected surface [13].
Remanent Magnetic Flux Leakage
Another way to use magnetic flux leakage is to rely on a property of ferromagnetic materials called remanent magnetization. Remanent magnetization occurs when ferromagnetic materials are exposed to strong magnetic fields. When the external magnetic field is removed, instead of going back to being neutrally magnetically charged, ferromagnets will retain some of the magnetic filed and will become "magnetized" themselves [14]. When a crack is present in a ferromagnetic material, it may be hard to detect it with regular MFL detection techniques due to the already high magnetic field present in the observed section and the inherent flux leakage that happens in all materials. However, when the external magnetic field is removed but the material remains magnetized, the flux leakage across the crack will be more pronounced in relation to the weakened background magnetization. This allows sensors to pick up any cracks and defects easier, even if their size is fairly small [14].
Current applications
While being available for some time already and having some substantial research done on it, not many companies have developed MFL sensors that re available of the shelf. The most prominent company to integrate MFL sensors into its products is Eddyfi. According to the company's website, Eddyfi provides the highest performance Non-Destructive Testing (NDT) inspection technologies in the world, helping OEMs, asset owners and service companies enhance productivity, save lives, and protect the environment [15].
Eddyfi uses MFL technologies primarily for pipeline inspection and has a line of products that perform the same role but at differing size points.
For example, the Pipescan HD is a portable sensor array that can be used for pipe inspections. According to Eddyfi, Pipescan HD is the highest resolution MFL scanner on the market. With a high Probability of Detection (PoD), the Pipescan HD is an effective and reliable pipe inspection solution for corrosion and pitting detection [16]. The scanner module requires almost no surface preparation and no couplant, which is a substance that helps transmit energy. Scanning speed of the Pipescan HD can be up to 1m/s, and it has an adjustable reporting threshold to define the depth at which the scanner works.
Max theoretical speed of movement
In a paper published by a research team from Nanjing University of Aeronautics and Astronautics, China, the speed limits of detection using MFL were explored [17]. In their test setup, the researchers used a spinning wheel, which had pre-made cracks for simulation purposes, as their test subject. Near the wheel, 2 magnetizing yokes were attached with their polarities being opposite to each other. Three perpendicular Hall Effect sensors were attached to the yoke that is placed against the direction of the spinning wheel. That way, the wheels surface is first magnetized by the yoke without the sensors and then the polarity of the magnetization is reversed by the yoke with the sensors, which increases the flux leakage and makes it easier for the hall sensors to pick it up. In testing, the team spun the wheel in speeds ranging from 5 m/s (18 km/h) up to 55 m/s (198 km/h) and recorded the results. The results indicate that the flux leakage detection is getting better, although non-linearly, as the speed was increased [17], meaning there is a good feasibility for high speed MFL detection to be applied in crack detection industries.
Design choices for ship hull inspection
In conclusion to the research made for the (WIP!)
Non-destructive inspection using ultrasound system
One of the most representative non-destructive testing methods for the inspection of ship hull is the Ultrasonic Testing. In general, this method utilizes the propagation of ultrasonic waves to get information of cracks or deformation in a solid body. Within this method, various techniques were developed[18]:
- Ultrasonic Thickness Measurement (UTM): UTM is a non-destructive technique that measures the local thickness of a structure by analyzing the difference in arrival times between direct and reflected waves. This method requires ultrasonic sensors to be in direct contact with the hull surface, which must be cleaned of coatings, corrosion, and biofouling. The final measurement locations are chosen based on a comprehensive survey to ensure they represent the average hull condition.
- Pulse-Echo Ultrasonic Testing (PEUT): PEUT is used to analyze internal defects within a structure. It employs a system where one sensor generates and receives ultrasonic waves. By examining the maximal amplitude and velocity of echoes reflected by defects, the size, location, and nature of the defects can be determined. This technique is commonly used for inspecting hull welds, constituent materials, and measuring thickness.
- Phased Array Ultrasonic Testing (PAUT): PAUT is advantageous for complex structures as it uses an array of ultrasonic elements to focus and scan the area of interest without moving the probe. By controlling each element in the array, the energy of the wavefront can be bent, deflected, and focused to produce cross-sectional images of defects, making it easier to analyze intricate structures.
- Guided Wave Ultrasonic Testing (GWUT): GWUT is designed for long plate-like structures and uses guided ultrasound waves, such as Lamb waves, to detect and locate defects at remote locations. These waves can propagate over significant distances with minimal attenuation and energy loss, making them suitable for inspecting thin-wall structures. However, GWUT may not be applicable to curved structures or those with varying geometries.
- Time-of-Flight Diffraction (TOFD) Ultrasonic Testing: TOFD determines the position and size of defects by measuring the time of flight of ultrasonic pulses rather than the amplitude of the reflected signal. This method uses a pair of ultrasonic probes, with the transmitter emitting a pulse and the receiver picking it up. If a crack is present, the waves are diffracted from the crack tip, allowing the size of the crack to be calculated.
- Air-Coupled Ultrasonic Testing (ACUT): ACUT uses air as the coupling medium instead of traditional liquid couplants like water or gel. This non-contact method eliminates the drawbacks of contact ultrasonic testing, making it more efficient for health monitoring and non-destructive testing. ACUT is particularly suitable for inspecting large-scale hulls made of metal or composite materials.
Working principle of UTM
In this project, it is decided that the MFL is used for localization of cracks and deformations on the vessel due to its advantages mentioned above. However, it is quite difficult to measure the depth of deformation, or the thickness loss due to corrosion with just MFL. Such challenge is resolved by using a simpler yet robust method: the UTM technique. There exists three main principle of UTM: resonance method, Lamb Law method and pulse reflection method. In the first method, by emitting ultrasonic waves of varying frequencies onto a workpiece, resonance occurs when the thickness equals a multiple of half the wavelength[19]. This method achieves high accuracy (≤0.1mm) with smooth surface finishes, which is not always the case for ship hull due to biofouling. For the second one, Lamb waves occur when ultrasonic frequency relates to both incident angle and workpiece thickness. These waves propagate in thin plates with wavelengths that are comparable to the plate thickness. The key to thickness measurement is that their propagation characteristics (velocity, dispersion) depend directly on the frequency-thickness product[20]. While they excel at measuring thin materials, when Lamb wave modes propagate in a fluid medium, they may suffer leakage by mode conversion into the fluid at a radiation angle dictated by Snell's law[21]. Lastly, the pulse echo method sends ultrasound through homogeneous materials, with propagation time proportional to thickness. This method works on rougher surfaces, making it versatile for various material conditions.
UTM using resonance method
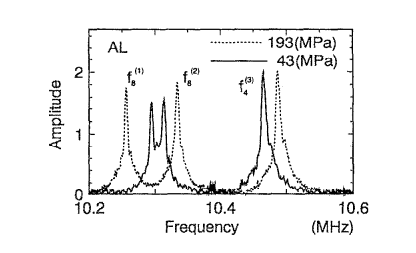
Ultrasonic thickness measurement using the resonance method involves transmitting high-frequency sound waves into the material, making these waves travel through the material and reflect back from the opposite surface. By varying the transmitted waves' frequency, the natural frequency of the material can be found by resonance. This effect can be seen by measuring the reflected waves; when resonance occurs, a significant increase in amplitude is obtained. As the resonance frequency is measured, the thickness of the material is calculated based on the known speed of sound in the material and the resonance frequency[23]. From the natural frequency, the thickness in m can be determined by D = nV / 2fn, where n is an integer indicating the order of resonant modes, V is the velocity of the wave travelling in the material in m/s, and fn is the found natural frequency in Hz of the material [22]. Most importantly, the velocity of the wave depends on which type of wave is being transmitted. When thickness loss due to corrosion occurs, the natural frequency of the material at that location is decreased while the resonant amplitude increases[24]. Although, this method requires a certain amount of time standing still to find the natural frequency, which accumulates to a longer measuring time for the robot.
UTM using Lamb Law method
In actual field measurements, where flat surfaces are not always the case, marginal errors were expected from the implementation of the aforementioned method. For instance, some operators reported large fraction of erroneous result in repeatability and reliability test[25], while a paper found that the 95% thickness confidence interval in some measurements was as wide as ±1.1 mm[26]. This can be WIP!

UTM using pulse reflection method
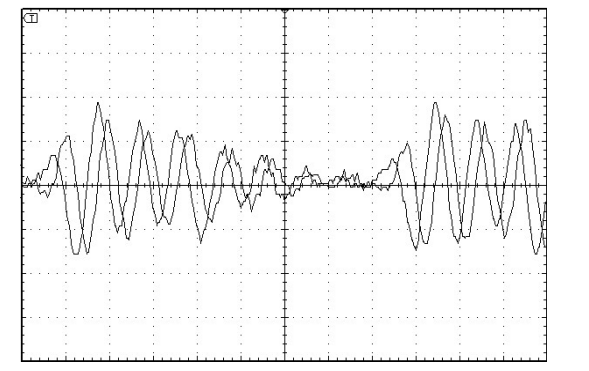
Fundamentally, the thickness in m D of the workpiece can be determined by D = ½ v(T0 - 2si / vc), where v is the velocity of the ultrasonic wave in the steel plate in m/s, T0 is the time delta between the transmission of the wave and its first echo, si is the length of the probe and and vc is the velocity of the wave in the probe. Depending on the medium (i.e., underwater, in air), vc will hold different values. One drawback of this method comes from the complexity of signal processing caused by the attenuation of some composite sound [27]. Also in [27], one method to solve such problem has been studied. For this method, the system employs four key approaches to improve accuracy: Extracting peak echo signal values to minimize amplitude fluctuations from noise; Using differential circuits with zero-crossing comparators to effectively isolate peak echo signals; Measuring time between echo signals via dual peak detection, eliminating the need to measure ultrasonic propagation in the probe. In other words, when the initial pulse reaches the bottom surface of the vessel, part of it is reflected back to the transducer while the rest continues to oscillate within the material and then getting reflected back little by little. The time difference between the first and and second echo determines the round trip time of the signal within the material, which leads to its thickness. From this discussion, the thickness equation can be calculated by D' = ½ v(T1 - T0), where T1 and T0 are the time between the first echo and the second echo respectively. The pulse reflection method extracts secondary echo signals for analysis, requiring minimal surface quality. This allows measurement of materials with rough, concave, or painted surfaces while maintaining good echo signal quality. Another problem that is proprietary to this design is its dependency to the surface's normal vector. If the deformation leads to the inner surface being at an extreme angle compared to the outer surface, it would result in a delay in round trip time, affecting the accuracy of the measurement.
Design choices for ship hull inspection
Since the robot is a single unit with all peripherals attached to it, all sensors needs to be compact while providing robust and accurate measurements. As explained above, surfaces that suffer from corrosion or deformation heavily affect the reliability of the resonance method. It also increase the total operating duration of the robot due to the search for the natural frequency of the material. As for the Lamb Law method, it was found that this method is not advantageous for underwater operation. WIP!
Localization
One of the sensors that are normally used to find an orientation and position in robotics is the inertial measurement unit. This sensor measures the linear acceleration and angular velocity of the robot. These can be integrated to find the linear position, linear velocity and angular orientation. With this the position of the robot can be estimated at every timestep. Over time this measurement becomes inaccurate due to the imperfect digital integration methods as well as imperfections in the sensor itself. Another method to find the location of the robots is by using a model and track the position by remembering the amount of rotation applied to the wheels. This method will also be imprecise in the long run due to things like slippage in the wheels and imperfections in the model. These methods can be combined in what is called a Kalman filter. The
Logbook
Name | Total Time (Hours) | Work Description |
---|---|---|
Anton Veshnyakov | 7 | Attended lecture (3h), Organized and structured the wiki page (1h), Group meeting (1h), Organizing the planning chart (1h), Research of problem statement and objectives (1h) |
Luuk Kool | 7 | Attend lecture (3h), search for papers (1h) / meeting (1h)/ research sensors(2h) |
Anh That Tuan Ton | 5 | Searched for relevant articles (1h), research paper (4h) |
Luca | 2 | meeting (1h), research on needed components (1h) |
Simon | 5 | meeting, reading about non-destructive inspection techniques for ship inspection. |
Name | Total Time (Hours) | Work Description |
---|---|---|
Anton Veshnyakov | 10 | Meeting with group and company research (4h), Research of relevant literature (4h), Second group meeting (2h), |
Luuk Kool | 8 | Meeting with group (4h), meet again (1h), read papers (3h) |
Anh That Tuan Ton | 7 | Meeting with group (4h), research for additional company (1h), second group meeting (2h) |
Luca | Meeting with group (4h), messaging companies (1h) | |
Simon | 9 | meeting with group (4h), communicating with the company Damen (1h) research for the cost of the actual inspections of the ships (4h) |
Name | Total Time (Hours) | Work Description |
---|---|---|
Anton Veshnyakov | 18 | Meeting with group (4h), Robot simulation software research (4h), Meeting with simulation researcher (2h), Second meeting with the group (2h), Research and summery of MFL (6h) |
Luuk Kool | 11 | Meeting with group (4h), second meeting with group (2h), installing and getting to know gazebo (4h), find 3d model for hull (1h) |
Anh That Tuan Ton | 12 | Meeting with group (4h), second meeting with group (2h), research on ultrasonic testing methods (4h), study other state of the art papers (2h) |
Luca | Meeting with group(4h), getting familiar with gazebo (3h), creating a 3d model for the robot(1h) | |
Simon |
Name | Total Time (Hours) | Work Description |
---|---|---|
Anton Veshnyakov | 9 | Meeting with group (3h), research and writing about MFL (6h) |
Luuk Kool | 12 | meet with group (4h), second meeting (2h), work on gazebo(6h) |
Anh That Tuan Ton | ||
Luca | Meeting with group (3h), working on movelment in gazebo(4h), do a force analysis of the robot(1h) | |
Simon |
Name | Total Time (Hours) | Work Description |
---|---|---|
Anton Veshnyakov | 13 | Meeting with group (4h), writing the wiki (3h), wiki writing (6h) |
Luuk Kool | 4 | Meeting with group (4h), working on gazebo (6h) |
Anh That Tuan Ton | ||
Luca | Meeting with group (4h), Working on the gazebo sim (8h) | |
Simon |
Name | Total Time (Hours) | Work Description |
---|---|---|
Anton Veshnyakov | ||
Luuk Kool | ||
Anh That Tuan Ton | ||
Luca | ||
Simon |
Name | Total Time (Hours) | Work Description |
---|---|---|
Anton Veshnyakov | ||
Luuk Kool | ||
Anh That Tuan Ton | ||
Luca | ||
Simon |
Articles summary
https://tuenl-my.sharepoint.com/:w:/r/personal/a_ton_that_tuan_anh_student_tue_nl/Documents/Documents/Year%203/Quartile%203/0LAUK0/Article%20summary.docx?d=w072622aab5a34691aa5c9248b16dc866&csf=1&web=1&e=gP4b5P
Simulation software
Simulink 3D animation can be used. This system can interact in Unreal Engine.
Documentation:
https://nl.mathworks.com/products/3d-animation.html https://nl.mathworks.com/help/driving/unreal-engine-scenario-simulation.html https://nl.mathworks.com/videos/series/using-unreal-engine-with-simulink.html https://nl.mathworks.com/help/vdynblks/ug/customize-scenes-using-simulink-and-unreal-editor.html
Gazebo can also be used for simulations. It is open source. https://gazebosim.org/home
Bibliography
- ↑ International Maritime Organization. (n.d.). Maritime Safety Committee (MSC). IMO. Retrieved March 15, 2025, from https://www.imo.org/en/MediaCentre/MeetingSummaries/Pages/MSC-Default.aspx
- ↑ 2.0 2.1 THE MARITIME SAFETY COMMITTEE. (2019). RESOLUTION MSC.461(101) (adopted on 13 June 2019) AMENDMENTS TO THE INTERNATIONAL CODE FOR THE ENHANCED PROGRAMME OF INSPECTIONS DURING SURVEYS OF BULK CARRIERS AND OIL TANKERS, 2011 (2011 ESP CODE). https://wwwcdn.imo.org/localresources/en/KnowledgeCentre/IndexofIMOResolutions/MSCResolutions/MSC.461(101).pdf
- ↑ Waldner, J. F., & Sadhu, A. (2024). A systematic literature review of unmanned underwater vehicle-based structural health monitoring technologies. Journal of Infrastructure Intelligence and Resilience, 3(4), 100112. https://doi.org/10.1016/j.iintel.2024.100112
- ↑ 4.0 4.1 E. Li, Y. Chen, Z. Yuan and J. Wang, "Train Wheel Magnetic Flux Leakage Testing Method Based on Local Magnetization Enhancement," in IEEE Transactions on Instrumentation and Measurement, vol. 72, pp. 1-9, 2023, Art no. 6002409, doi: 10.1109/TIM.2023.3251393.
- ↑ Y. Long et al., "A Novel Crack Quantification Method for Ultra-High-Definition Magnetic Flux Leakage Detection in Pipeline Inspection," in IEEE Sensors Journal, vol. 22, no. 16, pp. 16402-16413, 15 Aug.15, 2022, doi: 10.1109/JSEN.2022.3190684.
- ↑ "Roundup: Automotive Hall Effect Sensors Find New Life," All About Circuits, accessed March 19, 2025. [Online]. Available: https://www.allaboutcircuits.com/news/roundup-automotive-hall-effect-sensors-find-new-life/
- ↑ Shi Y, Zhang C, Li R, Cai M, Jia G. Theory and Application of Magnetic Flux Leakage Pipeline Detection. Sensors (Basel). 2015 Dec 10;15(12):31036-55. doi: 10.3390/s151229845. PMID: 26690435; PMCID: PMC4721765.
- ↑ 8.0 8.1 8.2 8.3 W. Gong, M. F. Akbar, G. N. Jawad and F. Zhang, "Surface Crack Size Estimation Based on Quantification and Decoupling of Magnetic Flux Leakage (MFL) Signals of Circular Array Sensors," in IEEE Sensors Journal, vol. 24, no. 10, pp. 16752-16762, 15 May15, 2024, doi: 10.1109/JSEN.2024.3379401.
- ↑ Feng B, Wu J, Tu H, Tang J, Kang Y. A Review of Magnetic Flux Leakage Nondestructive Testing. Materials (Basel). 2022 Oct 20;15(20):7362. doi: 10.3390/ma15207362. PMID: 36295427; PMCID: PMC9610001.
- ↑ 10.0 10.1 Dehui Wu, Zhitian Liu, Xiaohong Wang, Lingxin Su, Composite magnetic flux leakage detection method for pipelines using alternating magnetic field excitation, NDT & E International, Volume 91, 2017, Pages 148-155, ISSN 0963-8695, https://doi.org/10.1016/j.ndteint.2017.07.002.
- ↑ Dehui Wu, Zhitian Liu, Xiaohong Wang, Lingxin Su, Composite magnetic flux leakage detection method for pipelines using alternating magnetic field excitation, NDT & E International, Volume 91, 2017, Pages 148-155, ISSN 0963-8695, https://doi.org/10.1016/j.ndteint.2017.07.002.
- ↑ Mohd Aufa Hadi Putera Zaini, Mohd Mawardi Saari, Nurul A'in Nadzri, Zulkifly Aziz, Detection of crack on a mild steel plate by using a magnetic probe incorporating an array of fluxgate sensors, Materials Today: Proceedings, Volume 109, 2024, Pages 74-80, ISSN 2214-7853, https://doi.org/10.1016/j.matpr.2023.06.428.
- ↑ Ali Sophian, Gui Yun Tian, Sofiane Zairi, Pulsed magnetic flux leakage techniques for crack detection and characterisation, Sensors and Actuators A: Physical, Volume 125, Issue 2, 2006, Pages 186-191, ISSN 0924-4247, https://doi.org/10.1016/j.sna.2005.07.013.
- ↑ 14.0 14.1 Haotian Wei, Shaohua Dong, Lushuai Xu, Fan Chen, Hang Zhang, Xingtao Li, Internal inspection method for crack defects in ferromagnetic pipelines under remanent magnetization, Measurement, Volume 242, Part A, 2025, 115907, ISSN 0263-2241, https://doi.org/10.1016/j.measurement.2024.115907.
- ↑ Eddyfi Technologies, “About Us.” [Online]. Available: https://www.eddyfi.com/en/aboutus. [Accessed: Mar. 23, 2025].
- ↑ Eddyfi Technologies, “Pipescan HD.” [Online]. Available: https://www.eddyfi.com/en/product/pipescan-hd. [Accessed: Mar. 23, 2025].
- ↑ 17.0 17.1 Ping Wang, Yunlai Gao, GuiYun Tian, Haitao Wang, Velocity effect analysis of dynamic magnetization in high speed magnetic flux leakage inspection, NDT & E International, Volume 64, 2014, Pages 7-12, ISSN 0963-8695, https://doi.org/10.1016/j.ndteint.2014.02.001.
- ↑ Bosen Lin, Xinghui Dong, Ship hull inspection: A survey, Ocean Engineering, Volume 289, Part 1, 2023, 116281, ISSN 0029-8018, https://doi.org/10.1016/j.oceaneng.2023.116281.
- ↑ Shi Yiwei. Ultrasonic detection[M]. Beijing: Mechanical Industry Press, 2005:94-96.
- ↑ K. R. Leonard, E. V. Malyarenko, and M. K. Hinders, “Ultrasonic lamb wave tomography,” Inverse Problems, vol. 18, no. 6, p. 1795, nov 2002. [Online]. Available: https://dx.doi.org/10.1088/0266-5611/18/6/322
- ↑ Y. Roh and B. T. Khuri-Yakub, "Finite element analysis of underwater capacitor micromachined ultrasonic transducers," in IEEE Transactions on Ultrasonics, Ferroelectrics, and Frequency Control, vol. 49, no. 3, pp. 293-298, March 2002, doi: 10.1109/58.990939.
- ↑ 22.0 22.1 M. Hirao, H. Ogi, H. Fukuoka; Resonance EMAT system for acoustoelastic stress measurement in sheet metals. Rev. Sci. Instrum. 1 November 1993; 64 (11): 3198–3205. https://doi.org/10.1063/1.1144328
- ↑ Fan, Wei, and Pizhong Qiao. "Vibration-based damage identification methods: a review and comparative study." Structural health monitoring 10.1 (2011): 83-111.
- ↑ S. A. Kudus, Y. Suzuki, M. Matsumura, and K. Sugiura, “Vibration- response due to thickness loss on steel plate excited by resonance frequency,” IOP Conference Series: Earth and Environmental Science, vol. 140, no. 1, p. 012123, apr 2018. [Online]. Available: https://dx.doi.org/10.1088/1755-1315/140/1/012123
- ↑ van Roodselaar, Albert, et al. "Statistical modeling of some NDE measurement uncertainties." Inspector Summit Conference Proceedings. 2009.
- ↑ Wilson, P. T., D. P. Krouse, and C. J. Moss. "Statistical Analysis of UT Wall thickness data from corroded plant." Nondestructive Testing Australia 41.3 (2004).
- ↑ 27.0 27.1 27.2 J. Pan, F. Chen, Z. Song and Y. Feng, "Ultrasonic Pulse Reflection Method of Thickness Measurement System based on FPGA," 2020 5th International Conference on Mechanical, Control and Computer Engineering (ICMCCE), Harbin, China, 2020, pp. 2224-2228, doi: 10.1109/ICMCCE51767.2020.00482.
- ↑ J. Pan, F. Chen, Z. Song and Y. Feng, "Ultrasonic Pulse Reflection Method of Thickness Measurement System based on FPGA," 2020 5th International Conference on Mechanical, Control and Computer Engineering (ICMCCE), Harbin, China, 2020, pp. 2224-2228, doi: 10.1109/ICMCCE51767.2020.00482.
- ↑ Ferreira, C.Z., Yuri, G., Conte, C., Avila, J.P., Pereira, R.C., Morais, T., & Ribeiro, C. (2013). UNDERWATER ROBOTIC VEHICLE FOR SHIP HULL INSPECTION: CONTROL SYSTEM ARCHITECTURE.
- ↑ Cardaillac, Alexandre & Skjetne, Roger & Ludvigsen, Martin. (2024). ROV-Based Autonomous Maneuvering for Ship Hull Inspection with Coverage Monitoring. Journal of Intelligent & Robotic Systems. 110. 10.1007/s10846-024-02095-2.
- ↑ Negahdaripour, Shahriar & Firoozfam, Pezhman. (2006). An ROV Stereovision System for Ship-Hull Inspection. Oceanic Engineering, IEEE Journal of. 31. 551 - 564. 10.1109/JOE.2005.851391.
- ↑ A. F. Ali and M. R. Arshad, "Ship Hull Inspection using Remotely Operated Vehicle," 2022 IEEE 9th International Conference on Underwater System Technology: Theory and Applications (USYS), Kuala Lumpur, Malaysia, 2022, pp. 1-4, doi: 10.1109/USYS56283.2022.10072609. keywords: {Underwater cables;Visualization;Remotely guided vehicles;Prototypes;Inspection;Sensors;Safety;Remotely Operated Vehicle;Ship Hull Inspection;Unmanned Underwater Vehicle},
- ↑ Li, J., He, Y., Tao, W. (2025). Design and Implementation of a Modular Underwater Brush-Clearing Robot and Its Observation Module. In: Pham, D.T., Lei, Y., Lou, Y. (eds) Mechanical Design and Simulation: Exploring Innovations for the Future. MDS 2024. Lecture Notes in Mechanical Engineering. Springer, Singapore. https://doi.org/10.1007/978-981-97-7887-4_35