PRE2024 3 Group5: Difference between revisions
Tag: 2017 source edit |
(added source) Tag: 2017 source edit |
||
Line 456: | Line 456: | ||
<ref>A. F. Ali and M. R. Arshad, "Ship Hull Inspection using Remotely Operated Vehicle," 2022 IEEE 9th International Conference on Underwater System Technology: Theory and Applications (USYS), Kuala Lumpur, Malaysia, 2022, pp. 1-4, doi: 10.1109/USYS56283.2022.10072609. keywords: {Underwater cables;Visualization;Remotely guided vehicles;Prototypes;Inspection;Sensors;Safety;Remotely Operated Vehicle;Ship Hull Inspection;Unmanned Underwater Vehicle},</ref> | <ref>A. F. Ali and M. R. Arshad, "Ship Hull Inspection using Remotely Operated Vehicle," 2022 IEEE 9th International Conference on Underwater System Technology: Theory and Applications (USYS), Kuala Lumpur, Malaysia, 2022, pp. 1-4, doi: 10.1109/USYS56283.2022.10072609. keywords: {Underwater cables;Visualization;Remotely guided vehicles;Prototypes;Inspection;Sensors;Safety;Remotely Operated Vehicle;Ship Hull Inspection;Unmanned Underwater Vehicle},</ref> | ||
<ref>Li, J., He, Y., Tao, W. (2025). Design and Implementation of a Modular Underwater Brush-Clearing Robot and Its Observation Module. In: Pham, D.T., Lei, Y., Lou, Y. (eds) Mechanical Design and Simulation: Exploring Innovations for the Future. MDS 2024. Lecture Notes in Mechanical Engineering. Springer, Singapore. https://doi.org/10.1007/978-981-97-7887-4_35</ref> | <ref>Li, J., He, Y., Tao, W. (2025). Design and Implementation of a Modular Underwater Brush-Clearing Robot and Its Observation Module. In: Pham, D.T., Lei, Y., Lou, Y. (eds) Mechanical Design and Simulation: Exploring Innovations for the Future. MDS 2024. Lecture Notes in Mechanical Engineering. Springer, Singapore. https://doi.org/10.1007/978-981-97-7887-4_35</ref> | ||
<ref>THE MARITIME SAFETY COMMITTEE. (2019). RESOLUTION MSC.461(101) (adopted on 13 June 2019) AMENDMENTS TO THE INTERNATIONAL CODE FOR THE ENHANCED PROGRAMME OF INSPECTIONS DURING SURVEYS OF BULK CARRIERS AND OIL TANKERS, 2011 (2011 ESP CODE). https://wwwcdn.imo.org/localresources/en/KnowledgeCentre/IndexofIMOResolutions/MSCResolutions/MSC.461(101).pdf</ref> |
Revision as of 16:32, 15 March 2025
General Notes
TRIDENT (Tactical Robotic Inspection & Detection for Enhanced Nautical-hull Testing)
Tasks for this week:
- Luuk - Localization on the hull
- Anh - Ultra sonic sensor
- Simon - Use case
- Anton - Continue writing about the MFL
- Luca - Physics for the simulation
Group Members
Name | Student ID | Department | |
---|---|---|---|
Anton Veshnyakov | 1866508 | Electrical Engineering | a.veshnyakov@student.tue.nl |
Luuk Kool | 1883542 | Electrical Engineering | l.j.c.kool@student.tue.nl |
Anh That Tuan Ton | 1816209 | Electrical Engineering | a.ton.that.tuan.anh@student.tue.nl |
Luca Rutz | 1781294 | Electrical Engineering | l.d.rutz@student.tue.nl |
Simon van Valkengoed | 1881361 | Electrical Engineering | s.h.v.valkengoed@student.tue.nl |
Problem Statement (NEEDS AN UPDATE!!!)
The hull of a ship is constently exposed to the eviroment and the immens stresses that the water can generate onto it. For this and many other reasons, ships need to go into a dry dock to be inspeceted in every nook and cranny to make sure that the are still sea worthy.
Inspecting the hull of a ship is a critical step in insuring its safety and operability, be it a small fishing boat or a giant ocean crossing cargo ship. Traditionally, those inspections were done using divers[1]. As technology progressed, the role of hull inspections shifted from humans to ROVs (Remotely Operated Vehicles) and other autonomous robotic systems. However, currently the available solutions operate primarily while the ship is in the shallow waters of a port or while it is already docked[2]. This means, that if a ship incurred some damage, it will be discovered relatively late in its journey, which in turn will delay the repairs and keep the ship docked for longer than necessary. Our system aims to make the discovery of possible faults in advance, while the ship is still at sea, allowing for faster turn around time and potentially reduced ecological impact.
Non Destructive Testing on Ships & Boats – Marine NDT | Eddyfi - can be integrated into the problem statement as it is nicely worded.
Deliverable and goals (NEEDS AN UPDATE!!!)
The deliverable of this project will be a simulation of a robot that inspects the hulls of ships. This simulation will include the sensing part of a robot (measure its location and dynamics, measure the hull integrity and process it), but will not include actuators such as wheels or thrusters. The simulation should work for every (smooth) model of a ship hull.
The main goals are:
- Measure location with suitable precision and map this position on the manifold of the hull.
- Sense for defects in the hull.
- Implement the robot in a simulation software.
- Find the relevant user requirements and uses.
Planning
Week | Tasks |
---|---|
1 | Initial group set-up and task planing. |
2 | Literature research. |
Reach out to a specialist in the field. | |
3 | Research subgoals |
4 | Implement subgoals |
5 | Implement subgoals |
Draw conclusions and possible future improvements. | |
6 | Create the final presentation. |
7 | Finalize the wiki page. |
User Interviews
(Interview with Damen goes here)
Users requirements summery (NEEDS AN UPDATE)
After talking to various companies in the field of ship construction and maintenance, the following requirements were formulated for more efficient ship inspection:
- A small and cost effective system.
- Corrosion detection.
- Dent detection.
- Fracture detection.
- Ability to perform its mission underwater.
- Ability to perform its mission in a timely manner.
State of the art
(state of the art concepts and robots go here)
Sources:
Magnetic Flux Leakage (MFL) detection
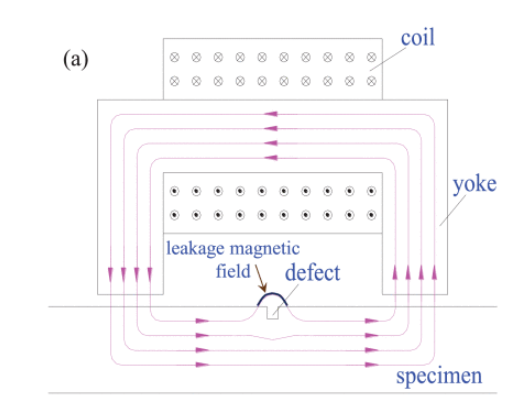
Today, the main energy sources that most people rely on, such as gas and oil, are being transported using pipes running in all kinds of environments. It is crucial to maintain the structural integrity of the pipes as a leak can potentially cause a catastrophe. However, it is impossible to inspect hundreds of thousands of kilometers of pipes visually, both due to the sheer size of them and also due to the fact that some of them run under ground or under water. To tackle this problem, engineers came up with a robot that can enter a pipe and scan it from the inside, looking for potential abnormalities. One of the main tools to accomplish this task is using the Magnetic Flux Leakage technique. Since most pipes are built out of steel, which is ferromagnetic, meaning it conducts magnetic fields within itself, it is possible to recognize a defect in the pipe by measuring the magnetic field that passes through a certain point in a pipe[4]. In a similar manner, this technology can be used on the hulls of ships since they are also made of ferromagnetic materials, usually steel and steel alloys. Since the idea of using MFL for ships is quite novel, little research has been done on implementing the system on a robot or similar machine to carry out the inspection. As a result, we base our research on models and experiments that have been conducted on land based objects, such as pipes and train rails. The assumption here is that using the equations that govern those models and experiments, it is possible to adjust the technique to be used under water.
What is Magnetic Flux Leakage?
In order to understand what magnetic flux leakage is and how it can be useful for detecting cracks and metal defects, we first need to understand the concept of magnetic flux in general. Magnetic flux is the measure of the total magnetic field passing through a given area. Mathematically, magnetic flux is defined as : Φ = B · A · cos(θ), where B is the magnetic field strength [Tesla], A is the area [m2], and cos(θ) is the angle between the area and the magnetic field. Magnetic flux is measured in units of Weber and can be created by magnets that are put in-line with the ferromagnetic material, or by using current carrying wires that induce a magnetic field as can be seen in Fig. 1. While most of the magnetic flux is following the shape of the ferromagnetic material, some of it will jump through the gaps that are present in the loop, which is called leakage or fringing. As can be seen in Fig. 1, a surface defect, such as a crack, will cause some of the flux to "leak" or take a different path than the straight line it should usually follow. Small amounts of leakage also happen in the gaps between the flux producing yoke and the specimen itself but those can be neglected as we assume that the yoke would be in full contact with the ship body.
MFL application in the industries
Magnetic flux leakage (MFL) detection is one of the most popular methods of inspection of structures made out of ferromagnetic materials. It is a nondestructive testing technique which uses magnetic sensitive sensors to detect the magnetic leakage field of defects on both the internal and external surfaces of given structures. [5] The inspection of those structure is often important due to the safety and health risk that small fatigue cracks can cause, especially when talking about oil and gas pipes, or the tanks of a oil carrier ship. IN addition to fatigue cracks, MFL can be used to detect such things as corrosion, erosion and metal loss, although there are more reliable and easier methods to go about detecting those defects. For the pipeline reliant industries, MFL is useful as it can be mounted on a special robot that goes inside the pipe and by suing the MFL can detect defects both on the inside and outside of the pipe without requiring a direct human access to the entirety of the pipe. In the train industry, MFL can be used to detect early-stage fatigue cracks on the wheels, which is crucial for the safety of the train and its passengers, as broken wheels can lead to derailments and catastrophic consequences.[3]
Influence of crack orientation on MFL
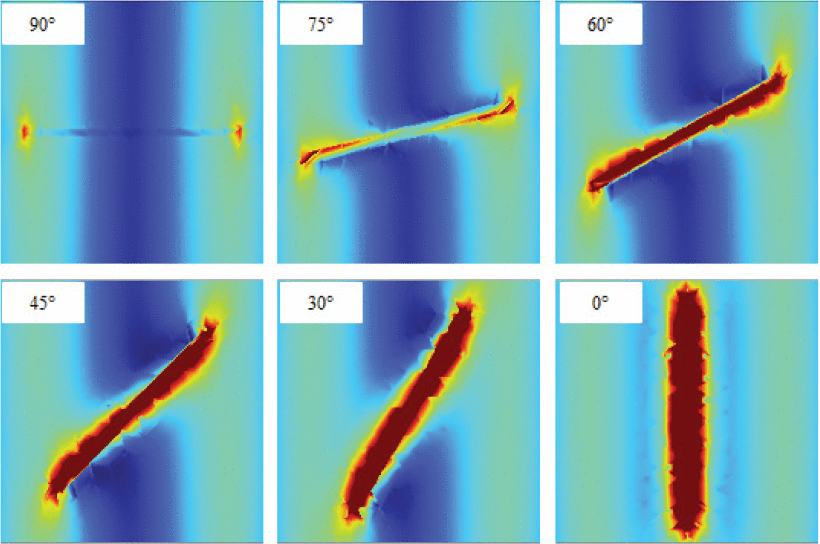
Due to the 3D nature of our world, cracks can be created and then propagate in different direction in the material. When using one MFL sensor it is sometimes hard or impossible to get a strong enough leakage so that it can be detected by the sensor. Additionally, even when using a linear arrangement of of sensors it is still not enough if the crack is perpendicular to the sensor array. [6] As stated in the research paper [6], it is advised to use a circular sensor array in order to achieve the best crack detection and orientation. Figure 2 demonstrates the different digitalized read-outs from the MFL sensor with relation to the angle of the crack to the sensors. The difference of the crack detection as a result of its orientation is explained by the following equation: B' = B · cos(β), where B' is the resulting magnetic flux density across the crack, B is the original flux density, and β is the crack's relative angle with respect to the magnetization direction. Additionally, it has been shown that deeper or wider cracks result in stronger leakage fields, as well as changing the amplitude and spatial distribution of the signal, which makes FML highly suitable for detecting cracks. [7]
Composite magnetic flux leakage detection method for pipelines using alternating magnetic field excitation - ScienceDirect - has some info on how the orientation of the crack affects the readout and some math to support it.
Internal inspection method for crack defects in ferromagnetic pipelines under remanent magnetization - ScienceDirect - has info about using MFL and RMFL (remnant magnetic flux leakage) so can be used as supporting evidence or as a completely different way to detect cracks.
Detection of crack on a mild steel plate by using a magnetic probe incorporating an array of fluxgate sensors - ScienceDirect - simple explanation of how to use MFL to detect cracks and defects in metals (has some math equations)
Theory and Application of Magnetic Flux Leakage Pipeline Detection - PMC - the name speaks for itself. Has a nice picture/diagram to visualize the leakage field in every axis.
A Review of Magnetic Flux Leakage Nondestructive Testing - PMC - has a good paragraph of sensing methods
Current applications
Sharck HR for SCC and surface-breaking cracks assessment | Eddyfi
Swift M MFL Pipeline Corrosion Mapping | Eddyfi
Enhanced localized MFL detection
Can also use the train source
Simulation of Enhanced FML
Pulsed magnetic flux leakage techniques for crack detection and characterisation - ScienceDirect
Guided Ultrasonic Wave inspection
One of the most representative non-destructive testing methods for the inspection of ship hull is the Ultrasonic Testing. In general, this method utilizes the propagation of ultrasonic waves to detect cracks or deformation in a solid body. Within this method, various techniques were developed[2]:
- Ultrasonic Thickness Measurement (UTM): UTM is a non-destructive technique that measures the local thickness of a structure by analyzing the difference in arrival times between direct and reflected waves. This method requires ultrasonic sensors to be in direct contact with the hull surface, which must be cleaned of coatings, corrosion, and biofouling. The final measurement locations are chosen based on a comprehensive survey to ensure they represent the average hull condition.
- Pulse-Echo Ultrasonic Testing (PEUT): PEUT is used to analyze internal defects within a structure. It employs a system where one sensor generates and receives ultrasonic waves. By examining the maximal amplitude and velocity of echoes reflected by defects, the size, location, and nature of the defects can be determined. This technique is commonly used for inspecting hull welds, constituent materials, and measuring thickness.
- Phased Array Ultrasonic Testing (PAUT): PAUT is advantageous for complex structures as it uses an array of ultrasonic elements to focus and scan the area of interest without moving the probe. By controlling each element in the array, the energy of the wavefront can be bent, deflected, and focused to produce cross-sectional images of defects, making it easier to analyze intricate structures.
- Guided Wave Ultrasonic Testing (GWUT): GWUT is designed for long plate-like structures and uses guided ultrasound waves, such as Lamb waves, to detect and locate defects at remote locations. These waves can propagate over significant distances with minimal attenuation and energy loss, making them suitable for inspecting thin-wall structures. However, GWUT may not be applicable to curved structures or those with varying geometries.
- Time-of-Flight Diffraction (TOFD) Ultrasonic Testing: TOFD determines the position and size of defects by measuring the time of flight of ultrasonic pulses rather than the amplitude of the reflected signal. This method uses a pair of ultrasonic probes, with the transmitter emitting a pulse and the receiver picking it up. If a crack is present, the waves are diffracted from the crack tip, allowing the size of the crack to be calculated.
- Air-Coupled Ultrasonic Testing (ACUT): ACUT uses air as the coupling medium instead of traditional liquid couplants like water or gel. This non-contact method eliminates the drawbacks of contact ultrasonic testing, making it more efficient for health monitoring and non-destructive testing. ACUT is particularly suitable for inspecting large-scale hulls made of metal or composite materials.
In this project, the ultrasonic transducers are implemented to measure the thickness loss of the ship hull due to corrosion, that is, the UTM method. Fundamentally, it consists of an ultrasonic transducer that emits a pulse and receive an echo. The time delta between the pulse and echo determines the thickness of the measured material.
Logbook
Logbook
Name | Total Time (Hours) | Work Description |
---|---|---|
Anton Veshnyakov | 7 | Attended lecture (3h), Organized and structured the wiki page (1h), Group meeting (1h), Organizing the planning chart (1h), Research of problem statement and objectives (1h) |
Luuk Kool | 7 | Attend lecture (3h), search for papers (1h) / meeting (1h)/ research sensors(2h) |
Anh That Tuan Ton | 5 | Searched for relevant articles (1h), research paper (4h) |
Luca | 2 | meeting (1h), research on needed components (1h) |
Simon | 5 | meeting, reading about non-destructive inspection techniques for ship inspection. |
Name | Total Time (Hours) | Work Description |
---|---|---|
Anton Veshnyakov | 10 | Meeting with group and company research (4h), Research of relevant literature (4h), Second group meeting (2h), |
Luuk Kool | 8 | Meeting with group (4h), meet again (1h), read papers (3h) |
Anh That Tuan Ton | 7 | Meeting with group (4h), research for additional company (1h), second group meeting (2h) |
Luca | Meeting with group (4h), messaging companies (1h) | |
Simon | 9 | meeting with group (4h), communicating with the company Damen (1h) research for the cost of the actual inspections of the ships (4h) |
Name | Total Time (Hours) | Work Description |
---|---|---|
Anton Veshnyakov | 18 | Meeting with group (4h), Robot simulation software research (4h), Meeting with simulation researcher (2h), Second meeting with the group (2h), Research and summery of MFL (6h) |
Luuk Kool | 4 | Meeting with group (4h) |
Anh That Tuan Ton | 12 | Meeting with group (4h), second meeting with group (2h), research on ultrasonic testing methods (4h), study other state of the art papers (2h) |
Luca | Meeting with group(4h), getting familiar with gazebo (3h), creating a 3d model for the robot(1h) | |
Simon |
Name | Total Time (Hours) | Work Description |
---|---|---|
Anton Veshnyakov | 3 | Meeting with group (3h), |
Luuk Kool | ||
Anh That Tuan Ton | ||
Luca | ||
Simon |
Name | Total Time (Hours) | Work Description |
---|---|---|
Anton Veshnyakov | ||
Luuk Kool | ||
Anh That Tuan Ton | ||
Luca | ||
Simon |
Name | Total Time (Hours) | Work Description |
---|---|---|
Anton Veshnyakov | ||
Luuk Kool | ||
Anh That Tuan Ton | ||
Luca | ||
Simon |
Name | Total Time (Hours) | Work Description |
---|---|---|
Anton Veshnyakov | ||
Luuk Kool | ||
Anh That Tuan Ton | ||
Luca | ||
Simon |
Sensors
Hull
Camera for visual inspection
ultrasonic for thickness measurements
Rail robot
Determine position along rail:
Estimate position with encoder on the wheel, this will drift due to slip. Position can be reset with periodic magnets in the rail and hall effect sensors.
Inspecting robot
Determine position along line
Determine speed
Determine angle
Determine depth
Might be possible to track these with an imu on the robot, subtracting with an imu on the rail robot to compensate for the movement of the ship. Can work in conjunction with an encoder on the wheels or a mapping to the ship topology for more accurate results (kalman filter)
chains?
Articles summary
https://tuenl-my.sharepoint.com/:w:/r/personal/a_ton_that_tuan_anh_student_tue_nl/Documents/Documents/Year%203/Quartile%203/0LAUK0/Article%20summary.docx?d=w072622aab5a34691aa5c9248b16dc866&csf=1&web=1&e=gP4b5P
Simulation software
Simulink 3D animation can be used. This system can interact in Unreal Engine.
Documentation:
https://nl.mathworks.com/products/3d-animation.html https://nl.mathworks.com/help/driving/unreal-engine-scenario-simulation.html https://nl.mathworks.com/videos/series/using-unreal-engine-with-simulink.html https://nl.mathworks.com/help/vdynblks/ug/customize-scenes-using-simulink-and-unreal-editor.html
Gazebo can also be used for simulations. It is open source. https://gazebosim.org/home
Bibliography
- ↑ Song, C., Cui, W. Review of Underwater Ship Hull Cleaning Technologies. J. Marine. Sci. Appl. 19, 415–429 (2020). https://doi.org/10.1007/s11804-020-00157-z
- ↑ Jump up to: 2.0 2.1 Bosen Lin, Xinghui Dong, Ship hull inspection: A survey, Ocean Engineering, Volume 289, Part 1, 2023, 116281, ISSN 0029-8018, https://doi.org/10.1016/j.oceaneng.2023.116281.
- ↑ Jump up to: 3.0 3.1 E. Li, Y. Chen, Z. Yuan and J. Wang, "Train Wheel Magnetic Flux Leakage Testing Method Based on Local Magnetization Enhancement," in IEEE Transactions on Instrumentation and Measurement, vol. 72, pp. 1-9, 2023, Art no. 6002409, doi: 10.1109/TIM.2023.3251393.
- ↑ Y. Long et al., "A Novel Crack Quantification Method for Ultra-High-Definition Magnetic Flux Leakage Detection in Pipeline Inspection," in IEEE Sensors Journal, vol. 22, no. 16, pp. 16402-16413, 15 Aug.15, 2022, doi: 10.1109/JSEN.2022.3190684.
- ↑ Shi Y, Zhang C, Li R, Cai M, Jia G. Theory and Application of Magnetic Flux Leakage Pipeline Detection. Sensors (Basel). 2015 Dec 10;15(12):31036-55. doi: 10.3390/s151229845. PMID: 26690435; PMCID: PMC4721765.
- ↑ Jump up to: 6.0 6.1 6.2 W. Gong, M. F. Akbar, G. N. Jawad and F. Zhang, "Surface Crack Size Estimation Based on Quantification and Decoupling of Magnetic Flux Leakage (MFL) Signals of Circular Array Sensors," in IEEE Sensors Journal, vol. 24, no. 10, pp. 16752-16762, 15 May15, 2024, doi: 10.1109/JSEN.2024.3379401.
- ↑ Feng B, Wu J, Tu H, Tang J, Kang Y. A Review of Magnetic Flux Leakage Nondestructive Testing. Materials (Basel). 2022 Oct 20;15(20):7362. doi: 10.3390/ma15207362. PMID: 36295427; PMCID: PMC9610001.
- ↑ Ferreira, C.Z., Yuri, G., Conte, C., Avila, J.P., Pereira, R.C., Morais, T., & Ribeiro, C. (2013). UNDERWATER ROBOTIC VEHICLE FOR SHIP HULL INSPECTION: CONTROL SYSTEM ARCHITECTURE.
- ↑ Cardaillac, Alexandre & Skjetne, Roger & Ludvigsen, Martin. (2024). ROV-Based Autonomous Maneuvering for Ship Hull Inspection with Coverage Monitoring. Journal of Intelligent & Robotic Systems. 110. 10.1007/s10846-024-02095-2.
- ↑ Negahdaripour, Shahriar & Firoozfam, Pezhman. (2006). An ROV Stereovision System for Ship-Hull Inspection. Oceanic Engineering, IEEE Journal of. 31. 551 - 564. 10.1109/JOE.2005.851391.
- ↑ A. F. Ali and M. R. Arshad, "Ship Hull Inspection using Remotely Operated Vehicle," 2022 IEEE 9th International Conference on Underwater System Technology: Theory and Applications (USYS), Kuala Lumpur, Malaysia, 2022, pp. 1-4, doi: 10.1109/USYS56283.2022.10072609. keywords: {Underwater cables;Visualization;Remotely guided vehicles;Prototypes;Inspection;Sensors;Safety;Remotely Operated Vehicle;Ship Hull Inspection;Unmanned Underwater Vehicle},
- ↑ Li, J., He, Y., Tao, W. (2025). Design and Implementation of a Modular Underwater Brush-Clearing Robot and Its Observation Module. In: Pham, D.T., Lei, Y., Lou, Y. (eds) Mechanical Design and Simulation: Exploring Innovations for the Future. MDS 2024. Lecture Notes in Mechanical Engineering. Springer, Singapore. https://doi.org/10.1007/978-981-97-7887-4_35
- ↑ THE MARITIME SAFETY COMMITTEE. (2019). RESOLUTION MSC.461(101) (adopted on 13 June 2019) AMENDMENTS TO THE INTERNATIONAL CODE FOR THE ENHANCED PROGRAMME OF INSPECTIONS DURING SURVEYS OF BULK CARRIERS AND OIL TANKERS, 2011 (2011 ESP CODE). https://wwwcdn.imo.org/localresources/en/KnowledgeCentre/IndexofIMOResolutions/MSCResolutions/MSC.461(101).pdf