Water Transport Infrastructure: Difference between revisions
Line 167: | Line 167: | ||
The southern parts of Niger are naturally dominated savannahs | The southern parts of Niger are naturally dominated savannahs | ||
Environmental issues in Niger include destructive farming practices as a result of population pressure. Illegal hunting, bush fires in some areas and human encroachment upon the flood plains of the Niger River for paddy cultivation are environmental issues. Dams constructed on the Niger River in the neighboring countries of Mali and Guinea and also within Niger itself are also cited as a reason for a reduction of water flow in the Niger River—which has a direct effect upon the environment. A lack of adequate staff to guard wildlife in the parks and reserves is another factor cited for loss of wildlife. | Environmental issues in Niger include destructive farming practices as a result of population pressure. Illegal hunting, bush fires in some areas and human encroachment upon the flood plains of the Niger River for paddy cultivation are environmental issues. Dams constructed on the Niger River in the neighboring countries of Mali and Guinea and also within Niger itself are also cited as a reason for a reduction of water flow in the Niger River—which has a direct effect upon the environment. A lack of adequate staff to guard wildlife in the parks and reserves is another factor cited for loss of wildlife. | ||
[[File:Road Niger.png|600px|right|wrap]] | |||
Surrounded by the vast Sahara desert, Niger is one of the least developed countries in the world. With intense droughts, poor soil conditions and the gradual spread of the desert, life is hard. The rainy season lasts from June to October during which 99% of the annual rainfall occurs with peaks in August, however it is still possible to have up to 10 days of drought during this month, making the distribution of rainfall extremely irregular. This is even more apparent in the north, where the the rainfall is unpredictable. Overall rainfall is below 100 mm and the potential evaporation is 2 to 3 meters per annum. During the rainy season, widespread hollows are transformed into temporary water pools and can act as a water source. The coolest months are November to February with a low mark of 19°C in December and the hot season from March to May has a mean maximum of 40°C. | Surrounded by the vast Sahara desert, Niger is one of the least developed countries in the world. With intense droughts, poor soil conditions and the gradual spread of the desert, life is hard. The rainy season lasts from June to October during which 99% of the annual rainfall occurs with peaks in August, however it is still possible to have up to 10 days of drought during this month, making the distribution of rainfall extremely irregular. This is even more apparent in the north, where the the rainfall is unpredictable. Overall rainfall is below 100 mm and the potential evaporation is 2 to 3 meters per annum. During the rainy season, widespread hollows are transformed into temporary water pools and can act as a water source. The coolest months are November to February with a low mark of 19°C in December and the hot season from March to May has a mean maximum of 40°C. | ||
The Government faces many barriers to providing public services like clean water and toilets. The economy can barely fund infrastructure. And the extreme climate makes installation and maintenance a major challenge. However, the Republic of Niger has one of the best and macadamized road networks in sub Saharan Africa. This macadam is a type of road construction consisting of layers of small angular stones compacted in shallow lifts and it has a straight surface, which is an all weather road. | The Government faces many barriers to providing public services like clean water and toilets. The economy can barely fund infrastructure. And the extreme climate makes installation and maintenance a major challenge. However, the Republic of Niger has one of the best and macadamized road networks in sub Saharan Africa. This macadam is a type of road construction consisting of layers of small angular stones compacted in shallow lifts and it has a straight surface, which is an all weather road. | ||
Primary roads are paved, secondary roads consist of lateral and gravel, tertiary roads generally consist of dirt. While the primary and secondary roads are more or less passable during the wet season, trails will practically become impassable. The terrain is predominantly sand dunes and desert plains in the south with hills in the north. | |||
[[File:Ground Level Niger.png|600px|left|wrap]] | |||
Soil in the northern Saharan region infertile. The Sahel, a region which forms a transitional zone between the Sahara and the region south, has thin white soils covered with salty deposits from intense evaporation that forms an infertile crust. The southern region however is cultivated, as the area has soils associated with uplands or extensive dunes or basins. | Soil in the northern Saharan region infertile. The Sahel, a region which forms a transitional zone between the Sahara and the region south, has thin white soils covered with salty deposits from intense evaporation that forms an infertile crust. The southern region however is cultivated, as the area has soils associated with uplands or extensive dunes or basins. |
Revision as of 08:19, 4 June 2018
Group Members
Name | Student Id |
---|---|
Han Wei Chia | 1002684 |
Hans Chia | 0979848 |
Joost Roordink | 1005406 |
Dennis Rizviç | 1020540 |
Minjin Song | 1194206 |
Thomas Gian | 0995114 |
Subject
According to research, one in six people have no access to drinkable water. Even if they have a water source, it takes them hours of travelling long distances to reach it. This causes a harsh environment for humans to survive in. Current methods of transporting water require expensive infrastructure investments, which is often not affordable for areas where water access is limited (they often tend to be fairly poor). We want to see if robots replacing these is a viable option.
Objectives
Our objective investigate the viability of using a robot to replace the manual labor that millions of people need to do to have access to water, compared to other possible solutions to this problem.
Users
The main users are charities that help communities or even the communities themselves that have no convenient access to water in areas with a semi-arid or desert climate. We assume these areas can generate the amount of solar power needed to power the water transport robot for most of the day.
Approach
At first we will gather information on the currently existing possible solutions. Then we build a use case through answering questions such as: “What advantages does the robot have over the already existing solutions?”, “How will the logistics of ((bringing to village)) and maintaining the robots work?”. Based on the use case, we can state the technical requirements the robot should have in order to work. Based on the approximate costs of the requirements, we can compare it with other known solutions in terms of pricing. Finally, we will compare all solutions in all perspectives to conclude whether a robot is truly a viable alternative.
Milestones
- Summaries research papers
- USE Aspects
- Locating water research
- Water Transport research
- Water cleansing research
- Existing infrastructure research
- Realize water transport robot
- Incorporate water transport robot in infrastructure.
Deliverables
- Logbook
- Planning
- Final document (including code)
- Presentation
- Research paper of the infrastructure , With Advantages, disadvantages and cost comparisons.
Planning
Literature study
Why does this problem need to be solved?
According to Graham et al[1], over 13 million women and 3 million children that are responsible for water collection in their household need to walk for more than 30 minutes. Note that these numbers are from only 24 countries in sub saharan africa, and the scale of the real problem is even larger than these numbers suggest. The paper also mentions various negative effects this has on these people. One of them is decreased hygiene. In the case of one particular disease(trachoma) has its prevalence almost doubled if water access is further away. Diarrhea also sees significant decreases if water collection time is reduced. Collection of water is also a physically demanding job. The negative effects of this are studied by Geere et al. in [2]. They report that manual carrying of water results in a serious increase in spinal, neck and head pain. Children doing manual labour to fetch water has also been linked with decreased school performance[3]. This is mostly linked to fatigue and lower attendance rates of children that need to carry water compared to those that don’t. Another major concern is the opportunity cost of the time women spend on getting water. Research done by Cairncross and Cuff[4] that compared two villages with different access to water found that time saved by reducing travel times to water sources would be used on either other household tasks or used to spent more time with children. This is also backed by research done by Koolwal and Van de Walle[5], which finds that reduced travel times to water access improve children’s education rather than paid-market labour participation.
Water Access
Water Wells
Water wells have been used for ages in order to have access to groundwater as a source of water consumption. They are inexpensive and require little technology as it’s mainly manual labor in which every person can participate in. However, the costs and difficulty depend on the location of where the well is to be built. In areas where the groundwater level is deep in the ground and also what type of ground it is that provides stability of the surrounding earth will prove to be important factors.
cost of wells
The main advantage of wells is that there very cost effective ones there running, but the initial cost and the time required to make them can add up a lot.
The cost of a well being drilled can vary, depending largely on the depth of the well, the diameter of the hole and the materials needed for the job. Other factors can also affect the cost of the well, such as the quality of the pump, and all the other technology you want to attach to it, man hours needed for the job, transportation of materials and equipment.
Accurate information on drilling prices or costs in sub‐Saharan Africa is not easy to access. Systematic analysis is a challenge because there is poor, fragmented and non‐standardized record keeping of water supply projects and programmes in sub‐Saharan Africa as well as lack of transparency. Table 1 provides examples of estimated and actual borehole costs and prices, ranging from $2,000 to $500,000 ($120 to $1,271 per meter)[6].
Disadvantages
Digging a well can be risky as you will usually be digging deep in the earth, which might collapse depending on the type of ground you work on. This requires technical overhead to avoid construction failures. And once you have a well, they aren’t well known for their hygienic reputation. Wells are easily contaminated and increase the chance of spreading various waterborne diseases such as cholera. Although there are ways of preventing the well of becoming contaminated, like sealing the well head, cleaning it with chlorine solutions and periodically checking it, these wells all require knowledgeable maintenance from the local community that makes use of these wells. They will have to be educated to protect the drinking water. But the cleanup of the well’s water is quite expensive and difficult as well, since they will require chemical, physical and biological treatments. The local community won’t have the knowledge on which treatments to apply and this will require an expert to perform throughout cleansing on every well. Knowing all the difficulties and costs that come along with using a well, It might not always be the best option.
Pipelines
Pipelines are mostly used for transporting different kinds of fluids, including petroleum, water, and natural gas. In this research, we will look deeper into how water transport, especially transport of drinking water, works and how much it costs.[7]
Advantages
The advantages of using pipelines for water transportation are low maintenance costs, stable fluid transportation through difficult terrains, and low energy cost. Pipelines normally lasts for about 50 years and have low probability of leaks during the lifespan [8] Pipelines are hidden underground, so there are no physical limitations once the pipelines are built. Compared to other transport methods, such as over ground vehicles, water pipelines are much more cost efficient since water is transported by a pump that requires little energy to operate.
Disadvantages
The main disadvantages of using pipeline for water transport is that it is difficult to find the source of leakage when it is known that the pipelines are broken. Although the probability of broken pipelines are low, the broken pipelines may take a long time to repair since it is buried underground. Also, the pipelines are inflexible in capacity once they are constructed since they have fixed pipe sizes that need to be compatible with other pipeline networks. The construction of pipelines are also limited to certain areas as they are buried underground and the constructors have to consider the environmental consequences of creating underground pipelines.
Cost analysis
According to the Trans Africa Pipeline that constructed the water pipelines across sub-Saharan region of Africa, the project that involves about 6,000 km of pipelines with pipe monitors, desalination plant, water tanks, and water pumps cost about 9.9 billion US dollars to construct and estimated cost about 380 million US dollars per year to maintain those pipelines.[9]
There are two types of water that can be used to create drinking water: Surface water and groundwater. Surface water is open to the environment and therefore exposed to human and animal activity, which causes surface water to be contaminated. To create drinkable water from contaminated water, it needs to be treated, but treatment of contaminated water comes with extra costs. Also, surface water often has more salinity than drinkable water, which causes the water to be unsafe for consumption. To reduce the salt in surface water to drinkable levels, the water needs to be desalinated. The process of desalination costs $1/m3 for seawater and $0.60/m3 for brackish water.[10] Groundwater is often a lot less salt, which causes the desalination costs to be a lot lower. In some cases desalination is not even needed, which means that the costs of desalination will be non-existent. For further treatment, groundwater needs nothing more than filtration of sand and other small particles, so in terms of cost groundwater is the far superior option compared to surface water.
Transport of water by pipelines costs around $0.05-0.06/m3 for every 100 kilometer of horizontal movement and has about the same price for a vertical lift of 100 meters.[10]
This means that transport of water by pipeline to areas that require more vertical lift are more expensive, than areas where only horizontal movement is needed.
Robot
Will a robot be accepted by the population in rural areas, that may not have any previous experience with robots?
The robot is intended to be used in areas where water access is a serious issue. These areas are often poor and have less access to technology in general. Therefore it might be an issue that the primary user group of these robots do not have any previous experience in encountering robots. One study that dealt with this issue is[11]. In this study a remotely controlled robot was used to carry water in a rural village in India in order to observe the users reactions to this robot. The study reports that the robot was positively received by the population. It also noted that there seems to a strong cultural influence in what the robot was perceived to be, f.e. being seen as female despite it having a male voice. This means that the robot will need some degree of modularity in its appearance and interaction with users to adapt to any local customs that might affect its performance. It should be noted however that this study was carried out in India, so it can be disputed whether the results are applicable to rural areas in africa.
The advantages of having a robot as a solution
In the list below, we’ll consider three other possible methods of assuring water for a community of people and compare them with the robot. The three methods are: building a well, building a pipeline network and transporting water to the community through vehicles such as planes, boats or trucks/ cars.
- The robot is instantly deployable. Pipelines, wells etc need to be build and often takes a long amount of time, while a robot can be build beforehand and be deployed instantly to places where it’s needed. This is an advantage over pipelines and wells since they have a much longer construction time. The main contester on this point would be to have a vehicle transport water towards the community. While transportation with vehicles would be faster, it also requires more manpower and more money (traveling cost) the longer this form of transportation persists. A robot on the other hand has no other costs or need for manpower next to maintenance and build cost, which can be done beforehand and might thus be a better option regarding money and manpower.
- The robot is reusable. If a better means of transportation of water is deployed, the robot can be reused at a different location where it is needed. Being instantly deployable and reusable means that the robot can be moved and deployed quickly at another location. This is a great attribute in case the robot is used as a temporary form of providing water. When the robot is no longer needed in a certain area, it can simply be moved to another location which only requires traveling time and the traveling cost.
- Sustainability. A robot which is able to power itself by sunlight is mostly or fully (depending on how it’s made) self-sustainable excluding maintenance. This is also a characteristic of wells or pipelines, but overall it is a huge advantage over transporting water by conventional means towards a place. Maintenance is the largest problem regarding the sustainability of the robot. Depending on how well the robot is build, the frequency of the maintenance would be increased or decreased. While maintenance is a problem with the robot, all structures, including the well and the pipeline, require some form of maintenance from time to time. Since the robot has not yet been fully built and tested, it is hard to give an estimate of the frequency of maintaining the robot and the time it takes to perform the maintenance and thus we can’t say if it would be more or less frequent or time-consuming than pipelines or wells.
- Automatic. Since the robot is automatic, just like a well or a pipeline, it helps people gather water and thus saving them time. A well and a pipeline can also fulfil this criterion if it is located relatively close to the community. Having the robot being fully automatic, the habitants of the area, will have more time which could possibly be spent on improving education or improving their settlement such as building better houses, creating a road, building a well or creating a pipeline network. It might be possible to let a person of that community do the maintenance depending on the complexity of the robot. If this would be possible, the sustainability of the robot would further improve.
- Deployability: the places it can be deployed. The robot has a couple of conditions to be deployed in a certain area. The first one would be strong long-lasting sunlight and the second would be that it’s able to traverse the area. While this is not an advantage, but more restrictions to the robot, it is possible that it would be the only viable option.
- A pipeline without a pump requires there to be a decent foundation for the network and the starting position needs to be higher than the destination. If that’s not the cause, the pipeline would need a pomp which would consume energy based on the different in height.
- For the construction of a well, there needs to be a large underground water source. Underground water is often salty to some degree and might thus not be drinkable water. The last problem with a well is the depth that the underground water source is located at. If the depth is too great, construction a well would be too difficult and thus not viable.
- Transportation of water through boats, planes, trucks is close to always an option, the main problem with this form of transportation is that it’s time consuming, requires manpower and requires a lot of energy and thus money in the long-term. This method is more of a short-term method until they find something better and is most likely not viable in the long-term since the cost would increase each time you have to transport water.
In case all of the above methods are not viable, the robot might be the best idea to be deployed, if it satisfies the above-mentioned requirements.
From the list of advantages, we can conclude that the robot does have a few cases in which it outperforms the other methods. While the robot is not viable in every situation, it fulfils some niche cases in which the other methods are not optimal.
Technical Requirements
Cost comparison to wells and pipelines
Trans African Pipeline, a project aimed to install 6,000km of pipeline and desalination plant in Northern Africa estimated to cost around $9.9 billion. In the case of our scenario, installing 3km of water pipeline would cost $4.95 million, if the same method of calculation was used. If separate calculation were used, taking $4 million dollars for the pipeline itself, $1.5 million for one water tank and pump over 3 km of distance, $83,000 for solar panel to power the pump, and $40 million for monitoring system, will cost around $45 million in total. In this calculation, desalination plants and nuclear plants were taken out off the cost calculation since our scenario does not fit with using sea water for providing water. Maintenance of 3 km of pipeline will cost around $9,300 to $18,600 per year. For a 3 km setup of pipeline, $45 million dollars plus $18,600 per year does not seem to be cost efficient to support a population of 250 people.
According to Water Wells for Africa, the average cost for building a well in Africa costs around $8,000, mostly in Malawi and Mozambique. [12] According to the WaterPage.com, the cost of building a well with modern technology, using hydraulics for digging a well, will cost around $8,000 on average, without the cost of purchasing the hydraulics equipment. [13] The lower cost, using Eureka Drill System or other small hydraulics, will cost around $1,500. The lowest cost of the three options, which is digging a borehole that are human operated without any mechanical equipment, will cost few hundred dollars to dig. However, these methods are only available if there is a water source available nearby underground. If the water source is located deeper, the costs will increase drastically as it will either require more manpower or more costs to use the hydraulic equipment.
Scenario
Country: Republic of the Niger Population estimate: 21 million Area: 1,267,000 km2 Prosperity ranking: 139th out of 149 Landscape:
Groundwater located very deep in the ground. From around 50 to 250 meters below ground level
The north of Niger is covered by large deserts and semi deserts. The southern parts of Niger are naturally dominated savannahs Environmental issues in Niger include destructive farming practices as a result of population pressure. Illegal hunting, bush fires in some areas and human encroachment upon the flood plains of the Niger River for paddy cultivation are environmental issues. Dams constructed on the Niger River in the neighboring countries of Mali and Guinea and also within Niger itself are also cited as a reason for a reduction of water flow in the Niger River—which has a direct effect upon the environment. A lack of adequate staff to guard wildlife in the parks and reserves is another factor cited for loss of wildlife.
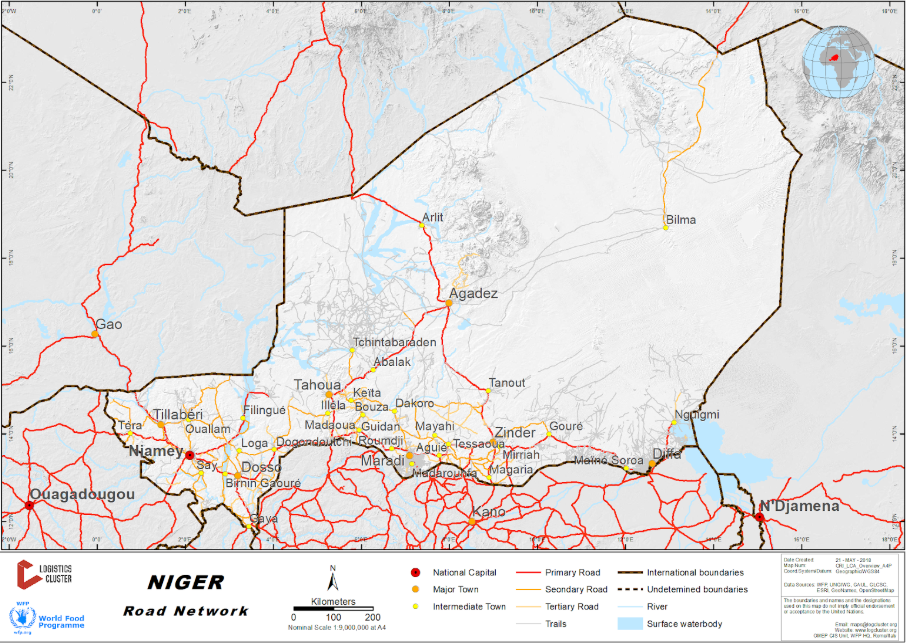
Surrounded by the vast Sahara desert, Niger is one of the least developed countries in the world. With intense droughts, poor soil conditions and the gradual spread of the desert, life is hard. The rainy season lasts from June to October during which 99% of the annual rainfall occurs with peaks in August, however it is still possible to have up to 10 days of drought during this month, making the distribution of rainfall extremely irregular. This is even more apparent in the north, where the the rainfall is unpredictable. Overall rainfall is below 100 mm and the potential evaporation is 2 to 3 meters per annum. During the rainy season, widespread hollows are transformed into temporary water pools and can act as a water source. The coolest months are November to February with a low mark of 19°C in December and the hot season from March to May has a mean maximum of 40°C. The Government faces many barriers to providing public services like clean water and toilets. The economy can barely fund infrastructure. And the extreme climate makes installation and maintenance a major challenge. However, the Republic of Niger has one of the best and macadamized road networks in sub Saharan Africa. This macadam is a type of road construction consisting of layers of small angular stones compacted in shallow lifts and it has a straight surface, which is an all weather road.
Primary roads are paved, secondary roads consist of lateral and gravel, tertiary roads generally consist of dirt. While the primary and secondary roads are more or less passable during the wet season, trails will practically become impassable. The terrain is predominantly sand dunes and desert plains in the south with hills in the north.
Soil in the northern Saharan region infertile. The Sahel, a region which forms a transitional zone between the Sahara and the region south, has thin white soils covered with salty deposits from intense evaporation that forms an infertile crust. The southern region however is cultivated, as the area has soils associated with uplands or extensive dunes or basins.
In rural areas, women perform arduous physical labor such as gathering firewood hand-processing food, fetching water from the well, and building and tending cooking fires. In rural areas, many families discourage girls from pursuing an education beyond primary school. At the one university, the University of Niamey, males predominate. Among some groups, particularly in the north, many families opposed all secular schools until recently, fearing them as sources of government control and cultural change.
Our Scenario plays in this Northern part of Niger. it can be from 19 to 48 degrees Celsius. There will be a water well 3 km distance from the community to the water source. The Community size consist of 250 people(Niger population is very thin in the north of the graph and thus small communities are more common)
Robot Design
Requirements
Design choices
Energy Source(to be completed)
The main goal here is to have a rough watt/m^2 number to be able to make an estimate of how much space is needed to satisfy the energy needs of the robot. The solar panels have mostly been picked from the list given at [14] to have some guarantee that they are within the price range we can afford for this robot. Note that we will not yet pick one specific panel here, since we would require knowledge of exactly how much space we have, what the dimensions of said space are, and how much power is actually needed in order to pick the cheapest panel that satisfies our needs.
From [15]we can see that we can expect an efficiency of something in the range of 16-18%.
In Niger, we have an average daily irradiance of about 6 to 7 kwh/m^2[16]
Using E=A*r*H*PR[17], where E is energy, A is the solar panel area, r is the efficiency, H is the solar irradiance and PR is a factor accounting for various electrical losses(usually taken at 0.75), we can calculate that the daily energy per square meter is, depending on the exact solar panel and irradiance used, between E=A*0.16*6*0.75=A*0.72kwh and E=A*0.18*7*0.75=A*0.945kwh. This gives the following lower and upper bounds on the performance of a solar panel: 0.72*3600000/(24*3600)=30w/m^2 0.945*3600000/(24*3600)=39w/m^2
We can also use the kwh/kwp map given in[16]. The panels listed in [15] and [18] give a nominal power within a range of 250 to 300 wp. In northern Niger we get a daily kwh/kwp production in the range of 5 and 5.5. This then gives a worst case of 5*0.25=1.25 kwh/day and a best case of 5.5*0.3=1.65 kwh/day.
However, these wp figures are for the entire panel, which is usually larger than 1m^2. For wp/m^2 we need to look at table 1. Note that each panel has several variants and we have rounded the area to make the numbers easier to read, so exact numbers may differ a bit.
With these numbers, we’re looking at a rough 160-180 wp/m^2 range for the panels. These number then give 5*0.16=0.8 kwh/day and 5.5*0.18=0.99 kwh/day as lower and upper bounds. Note that these numbers are roughly the same as those found earlier, so the conversion to w/m^2 will give the same results.
Panel | ALLMAX framed 60 cell[18] | 330|335P-FG[15] | 295|300MS-FG[15] | 275|280P-FG[15] | SUNIVA OPTIMUS |
---|---|---|---|---|---|
wp/m^2 | 180 | 165 | 150 | 180 | 165 |
Additionaly, we have also calculated how much energy we expect to need for various different speeds. This was done in an external latex file since it involved quite a bit of mathematics/physics. (NOTE TO TUTORS: not entirely finished yet since this turned to be quite complex, and the writing style also needs some work) https://v2.overleaf.com/read/nhdhyhfjkjrd
Locomotion
With the given scenario, there are 5 possible methods of locomotion in the desert. Although not all of them are suitable for this scenario, they give good comparison of which of the aspects will work best in the desert.
The tires are the most common types of locomotion for a vehicle in any road conditions. Different types of tires are available for different terrain conditions, whether it is on hardgrounds like asphalt or soft grounds like sand or dirt. Since it is the most common type of locomotion on vehicles, it is very easy to find replacements, even with specialized tires. In comparison to other methods of locomotion, tires are cheaper and simpler to maintain since it only requires tire replacements a tire punctures. However, conventional tires may not work well with soft grounds, which requires more expensive specialized tires.
The second option to solve the locomotion is the tank tracks, which is used mostly for heavy all terrain vehicles. Tank tracks are easily maneuvered in any road conditions, whether it is hard or soft grounds. However, the cost to operate tank tracks in the vehicle is very expensive in terms of energy and money. Tank tracks require higher power input since tank tracks are usually heavy. Tank tracks replacement when damaged or broken down is not simple, so the maintenance costs are high in money and time.
The newly discovered method of locomotion in the desert is a screw propelled locomotion. The way this works is that two or four screws are attached to the vehicle to maneuver through soft grounds. When four screws are attached for locomotion, the maneuverability of the vehicle significantly increases compared to that of the vehicle with two screws. Just like some vehicles with tank tracks, this vehicle is also amphibious. However, further research is needed to implement this locomotion since some of the vehicles that used this type of locomotion are from the 20th century. This locomotion may not work well if it is going through normal road infrastructure. Maintenance can also be expensive as screws need to be design in accordance to the given ground conditions.
A combination of ski and small tracks were also discussed for the locomotion of the robot. This is already adapted in snowmobiles, which maneuvers through snows very effectively. If parts in snowmobiles for locomotion are redeveloped in such a way that it adapts to soft grounds with higher temperature, this locomotion seems to be the most plausible method. However, this requires further research on soft grounds other than snow as this method requires reconfiguration of snowmobiles. Furthermore, it takes both positives and negatives of the tank tracks to a smaller degree.
The last method of common locomotion on the ground is railways. Railways are one of the fastest ways of moving in the ground with its fixed yet direct railways that cause little accidents. If enough infrastructures are developed, it is possible for longer and more efficient travels to be performed by the robots. However, its biggest issue is that it requires expensive and time consuming infrastructure installation even on short distance travels. Railways on soft grounds may not perform well as the railways need to be installed on hard grounds. Furthermore, the routing of this locomotion is very limited once it is installed on the ground. The maintenance cost may be cheaper as it is more durable than some of the locomotion methods mentioned above, but once it requires maintenance, it will take lots of time and money.
Motor
Water Tank
pick-up and drop-off mechanic
In our scenario we have a water well. Our robot needs to be able to draw out water from this well. The easiest way to acquire this is by pumping the water out of the well into the robot. For pumping out the water we have two possibilities of how to obtain this. The first would be to station the water pump on top of the robot together with a tube to suck out the water and have the robot carry this around. The second option would be to place an automatic water pump on top of the water well. The problems with the first option are that the robot would constantly need to carry the pump which adds up to the weight and this the amount of energy consumed and that every single robot would need his own pump to function. In case there are multiple robots assigned to the same water well, it would mean that every robot would need his own pump which might make the cost unnecessary higher. Because of these reason it might be beneficial to have a pump separate from the robot which is stationed at the water well. The down side of this method would be that it would increase the time that a robot would be functional after deployment. The time from deployment till functionality would thus only depend on the time it takes to install the automatic pump onto the water well.
Pick-up
By placing the water pump at the well we can modify the design of the pump in such a way that it is able to pump water into the robot. If we look at the current design of wells, whether the water is stored into a container or comes straight out of the well. They all have an something in common in the design. The water outlet attached to it always drops the water straight downwards. There is 1 major designs choices to get the water into the robot. The first option is to modify the robot in such a way to be able to get water from the water outlet. By doing this their will be less trouble during the implementation of the robots itself as they can get water from any water outlet, but this is an very difficult task as there are more design for an water outlet. Creating a mechanism for the robot to be able to get water from any water outlet will be highly complicated. The second option is to modify the water outlet in such a way that it can fill the robot. By doing this their will of course be more trouble during the implementation, as we would need to make adjustments to the water outlet. This of course comes with a tradeoff that there is no need to invest a lot of time and money into solving the problem unlike the first option.
In our scenario we chose to work out the second option since there is no clear estimate of how fast this would be solved. The time and research cost could be more wisely spend on other components of the robot. For example the highly complicated issue NASA had in which they spend millions of dollars into finding the solution on how to write with a pen in space. The solution they came up with was very pricy and not that reliable, while the russians just used a pencil.
Drop-off mechanic
For the drop-off mechanic, a simple faucet at the bottom of the water container of the robot should be sufficient. Since people have been living in the village described in our scenario, they should have some means to hold water, since they need to have something that they used to transport water in. Because of this, a faucet to let the water flow out of the water container into their means to hold the water should be sufficient. Ideally the robot would be emptied immediately and start gathering water again, but in case all the water storage is full or everyone is unable to use the faucet (for example sleeping), the robot will wait till the water container is empty before it goes to gather more water. To avoid this, it might be beneficial for the villagers to construct a water tank, during their newly gained free time, in which the robot will drop-off the water. Although it might not be viable for villagers to construct a safe water tank without sufficient knowledge of how to create one and how to maintain the tank to avoid pollution of the water.
Transport system
The robot will use a GPS for tracking it's position while it moves towards its destination. The location of the destination is input as GPS coordinates. There are two possible ways for a robot to create a path. The first one is that a path is already present, this path will most likely be created by the villagers and the robot will try to follow it. The second is that there is no path present, in this case the robot will turn until the front faces towards the destination which afterwards the robot will try to move directly towards. To make sure the robot does not deviate from its path, every x traveled meters the GPS is used to check whether the location from the robot is still on its path. The robot will keep moving on its path until it either reaches the destination or something is hindering the robot from continuing.There are multiple things that can hinder the robot from continuing it’s path, each creating a different response from the robot to solve it. Here’s a list of things that the robot might encounter and how it should react.
Rocks, debris or plants on the path.
When encountering these things, the first thing the robot will have to do is to decide the gravity of its situation based on the height and width, the robot will chose if it will more around it or go over it. In case the rocks, debris and plants are small enough such that they won’t hinder the robot from going easily over it,the robot will decide to go over it. If that is not the case, the robot will have to move around it and thus changing it’s path. Using it’s sensors it will move around it and after the obstacle is no longer present, it will use it’s GPS to form a new straight path towards the destination.
Cliffs
A cliff can be a problem which the robot will have to avoid. The main problem with a cliff however is the detection of it using a sensor. At the bottom of the cliff, the cliff will be detected as a large wall and will thus be treated the same as a rock which the robot will not be able to travel over it. Detecting an cliff at the top will be more difficult since the ground will simply stop. For this reason the robot will have a ultrasonic sensor dedicated to detecting the ground in front of the robot to avoid such situations. When the robot has detected a cliff which hinders him from continuing on it’s path, it will again move around it and once it has accomplished this, create a new path and continue on it.
Damage by external factors, such as wild animals
It is possible that the robot will be attacked by animals while on-route. This can be known by using the gyroscope values, attacks will cause some form of shaking to the robot which are visible as spiking values in the gyroscope measurements. To fend off animals, the robot will be equipped with a speaker that will play a loud sound when threatened. It will also be possible to play the sound of a lion or tiger to scare off most animals, but this sound might attracted lioness or tigress which can worsen the situation.It will also save the GPS location of where the attack happened for avoidance in the future.
Once the robot reaches the destination coordinates according to its GPS, depending on the size of the water source it might not see where to retrieve water from. Small sources as wells might be missed as the GPS usually has a radius of approximately 5 meters, in cases like these we would require a more precise location for the robot to reach the well. Possible solutions are including a camera in the robot to detect the well on its own or a signal transmitter could be placed on the well. Using a camera will require more processing power to run a detection algorithm, while using a signal transmitter will need the overhead of having one installed at the destination well.
To get back to the village, the robot will basically have the source coordinates input, assuming that it started moving from the village, and it will move towards it as described above how it moves to a destination.
Durability(to be completed)
As the water transportation robot is expected to function in sub-Saharan Africa, it is certainly required for the robot to have a certain degree of sand erosion resistance. For this purpose materials and coatings can be deliberately selected to improve sand erosion resistance. According to K. Haugen et al [19] solid tungsten carbide materials and the ceramics Si3N4 and B4C are the most sand erosion resistant materials. Also, a Degun tungsten carbide layer as a coating significantly improves the anti-sand erosion characteristic of the coated material. Depending on how durable these materials are in factors other than sand erosion resistance they could be used to cover the top layer of the robot with a Degun tungsten carbide layer as coating.
Material options for basic frame structure:
Aluminium: Has been known as a light and strong material. A lower weight of the robot results in less power consumption for the movement which makes it quite a desirable option.
General properties of aluminium and its alloys are: [20]
- Low density compared to steel: 2.7 g/cm^3 compared to 7.83g/cm3
- Low density coupled with high strength in some of its alloys makes it a great material to create strong, but lightweight vehicles and by extension robots as well.
- Aluminium resists progressive oxidization, which causes steel to rust. When aluminium is exposed to oxygen it forms a thin, colorless and transparent inert aluminium oxide film that blocks further oxidation. So, the discoloration and flaking that is common with iron or steel does not occur with aluminium.
- Resists all sorts of corrosion when properly alloyed and treated.
- Great electrical thermal and electrical conductivity, but can be alloyed to have great electrical resistivity.
- Aluminium is non-ferromagnetic, non pyrophoric and non-toxic. Non-toxic is important, since the robot has to transport water.
- Can easily be fabricated into any form. There is no limit to the different shapes in which aluminium can be shaped.
Aluminium should be a good choice for the base frame or at least to supplement it. Aluminium alloys have more advantages, but have a higher production cost attached to it.
Aluminium alloys
Alloy 3003:
A widely used general purpose alloy with its major alloying element being manganese. Is used in moderate-strength applications requiring good workability.
5xxx series:
Aluminium alloy thats contains the major alloy element magnesium. The major benefit of these alloys is its corrosion resistance, which is better than all other types of alloys. The drawbacks of this aluminium alloy is its safe operating temperature, if the alloy contains over 3.5% magnesium, which shouldn’t rise above about 65 degrees Centigrade to avoid stress-corrosion cracking. Alloy 5456 is often used a storage tank or pressure vessel for this purpose. This alloy also has high weld efficiency and joint strength.
6xxx series:
Aluminium alloys that contains major alloy elements silicon and magnesium and are heat-treatable. Are not as strong as 2xxx or 7xxx alloys, but have good formability, weldability, machinability and corrosion resistance with medium strength.
Alloy 6061:
The general purpose 6xxx series alloy, which is used in a broad range of structural applications and welded assemblies. Such as truck components, railroad cars, automotive parts, machine parts, aircrafts etc. Has 42 ksi tensile strength and 36 ksi yield strength.
Alloy 6151:
Has 44 ksi tensile strength and 37 ksi yield strength Is used in the automotive industry due to being able to make intricate forgings for automobiles with this alloy.
Alloy 6205:
Has as benefit a high impact resistance. If the speed of the robot reaches a certain point, this alloy could be used to counteract crashes in case they happen.
Alloy 7150:
Aluminium alloy that contains zinc as major alloying element. Has 84 ksi tensile strength and 78 ksi yield strength. It is used in aircrafts and other structures, requiring high strength. This strength comes with the disadvantage of reduced resistance to stress corrosion cracking.
High strength steel: Is the base choice of material for automobile bodies due to its strength, ductility and low cost. Knowledge of the material, processing properties and efficient design of steel are all well-explored. However, the material itself is heavy resulting in more fuel consumption. Also, the strength of this material is likely not to be well-utilised in the robot, since crashes are unlikely to happen and the crashes that will happen will be at low speed. Magnesium: Very lightweight material, which sees some usage in automobile industries already due to its malleability cutting down costs of production. One of the downsides is that there is not much magnesium production which limits supply. Also it doesn’t enjoy the creep resistance that aluminium does have.
As the robot is expected to function for a long time without maintenance it becomes quite clear that it needs the remain functional even if some components fail. To achieve this, the number of vital components needs to be reduced, also these components need to be well-protected and fail proof. For this purpose, designing components to be less reliant on another seems to be a valid strategy. A few examples of this concept would be: Separating power sources for different components, more important parts would have their battery placed in more protected areas. Multiple of the same component, if a critical component were to fail, then a backup component would be able to continue, ensuring that the robot keeps doing its job. Also, if multiple of the same component are in use at the same time, it should be designed in such a way that if one of them fails, the other components would be able able to make up the difference. Also, creating fail safes for many different situations is also needed to improve the durability of the robot.
Magnesium Alloy: [21]
The density of magnesium is around 1.8g/cm^3, making the lightest material of the available materials for the frame. Magnesium alloy with silicon has high creep resistance but may decrease corrosion resistance if iron is found. Magnesium itself has a poor corrosion resistance and is weak to stress concentration. Magnesium is resistant to progressive oxidation with oxide layer formed while the metal is heated. However, when the temperature reaches about 450 degrees celsius, the layer is destroyed and magnesium begins to melt. Magnesium has lower electrical conductivity, but has higher damping performance than aluminium. Magnesium is non toxic and diamagnetic. The main advantage of magnesium is the high weight per strength ration due to its low density compared to other available frame materials. Magnesium also has high fatigue limit and is very easy to recycle.
Alloys:
- AZ91D
- AZ91D is the most commonly used magnesium alloy that has 33.4 ksi tensile strength and 23.2 ksi yield strength. AZ91D is widely used in many of current automotive parts such as transmission case, steering box and subframe. Its main advantages are room temperature strength, high die-castability, and corrosion resistance.
- AM60, AM50, AM20
- AM60 is used for wheels in Porsche, while AM50 and AM20 are used for seat frames in Mercedes Benz. Their advantages are high ductility and good impact strength. These alloys have tensile strength of 35 ksi, 33 ksi, and 30 ksi and yield strength of 18 ksi, 18 ksi, and 13 ksi, respectively.
- AZ31 [22]
- AZ31 was experimented by Morteza Kiani and 3 others from KeAi as one of the components to replace steel parts in original body frame of a car to optimize the weight of a car to minimum. The experiment resulted in 54.5 kg of weight reduction with similar crashworthiness to that of the original frame. AZ31 has tensile strength of 37.7 ksi and yield strength of 29 ksi.
References
- ↑ Graham JP, Hirai M, Kim S-S (2016) An Analysis of Water Collection Labor among Women and Children in 24 Sub-Saharan African Countries. PLoS ONE 11(6): e0155981. https://doi.org/10.1371/journal.pone.0155981
- ↑ Geere, J. A. L., Hunter, P. R., & Jagals, P. (2010). Domestic water carrying and its implications for health: a review and mixed methods pilot study in Limpopo Province, South Africa. Environmental Health, 9(1), 52.
- ↑ Hemson, D. (2007). ‘The toughest of chores’: policy and practice in children collecting water in South Africa. Policy Futures in Education, 5(3), 315-326.
- ↑ Cairncross, S., & Cuff, J. L. (1987). Water use and health in Mueda, Mozambique. Transactions of the Royal Society of Tropical Medicine and Hygiene, 81(1), 51-54.
- ↑ Koolwal, G., & Van de Walle, D. (2013). Access to water, women’s work, and child outcomes. Economic Development and Cultural Change, 61(2), 369-405.
- ↑ Danert, K.; Carter, R.C.; Adekile, D.; MacDonald, A. Cost-effective boreholes in sub-Saharan Africa. In Proceedings of the 33rd WEDC International Conference, Accra, Ghana, 7–11 April 2008.
- ↑ PIPELINE 101. (n.d.). Retrieved from http://www.pipeline101.org/Why-Do-We-Need-Pipelines
- ↑ What is the Life Expectancy of Your Pipes | Essentra Pipe Pro... (2017, March 01). Retrieved from https://essentrapipeprotection.com/what-is-the-life-expectancy-of-your-pipes/
- ↑ Tennyson, R. (n.d.). TRANS AFRICA PIPELINE: Sustainable Water for Sub Sahara Africa. Retrieved http://transafricapipeline.org/PDFs/SustainableWaterAcademyPaper.pdf
- ↑ 10.0 10.1 Zhou, Y., & Tol, R. S. J. (2005), Evaluating the costs of desalination and water transport. Water Resources Research, 41(3). doi:10.1029/2004WR003749.
- ↑ Deshmukh, A. , Krishna, S., Akshay, N., Vilvanathan, V., J. V., S. and Bhavani, R. R. (2018) HRI – "In the wild” In Rural India: A Feasibility Study. In: 13th Annual ACM/IEEE International Conference on Human Robot Interaction (HRI 2018), Chicago, IL, USA, 5-8 March 2018,
- ↑ “Water Wells For Africa.” Water Wells For Africa RSS, waterwellsforafrica.org/whats-the-cost/
- ↑ “Cranfield University Water Management.” Water Page Resources: The Importance of Water Conservation, www.thewaterpage.com/cranfiel.htm.
- ↑ “Most Affordable Solar Panels.” Lets Go Solar, www.letsgosolar.com/solar-panels/rankings/affordable/
- ↑ 15.0 15.1 15.2 15.3 15.4 Solar Inc. “Dymond Panels.” Solar Power for Home: Residential Solutions|Canadian Solar, www.canadiansolar.com/solar-panels/dymond.html.
- ↑ 16.0 16.1 “Solar Resource Maps of Niger.” Solargis, solargis.com/maps-and-gis-data/download/niger
- ↑ “How to Calculate the Annual Solar Energy Output of a Photovoltaic System?” How to Calculate the Output Energy or Power of a Solar Photovoltaic System, Excel PV Calculator to Estimate Solar Electricity Output., photovoltaic-software.com/PV-solar-energy-calculation.php
- ↑ 18.0 18.1 “US/ALLMAX-PD05.05.” Trina Solar, 22 May 2017, www.trinasolar.com/us/product/allmax/allmax-pd0505
- ↑ Haugen, K., Kvernvold, O., Ronold, A., & Sandberg, R. (1995). Sand erosion of wear-resistant materials: Erosion in choke valves. Wear, 186-187, 179-188. doi:10.1016/0043-1648(95)07158-x
- ↑ Davis, J. R. (2011). Aluminium and Aluminium Alloys. In Alloying: Understanding the basics. (pp. 351-416). Materials Park, OH: ASM International.
- ↑ Moosbrugger, Charles. “Introduction to Magnesium Alloys.” Engineering Properties of Magnesium Alloys, ASM International, 2017, pp. 1–10.
- ↑ Kiani, Morteza, et al. “Design of Lightweight Magnesium Car Body Structure under Crash and Vibration Constraints.” Journal of Magnesium and Alloys, vol. 2, no. 2, 2014, pp. 99–108., doi:10.1016/j.jma.2014.05.005.