Integration Project Systems and Control 2013 Group 2: Difference between revisions
Jump to navigation
Jump to search
Line 78: | Line 78: | ||
==== Week 2 ==== | ==== Week 2 ==== | ||
* ... | * Rens and Jeroen conducted an FRF measurement on the left pizza robot. They did a closed loop measurement on each axis by applying a sin-wave + white noise to the plant. The sine wave is added to overcome the massive friction. The controller used in the closed loop measurement is tuned very low. During the FRF measurement the following data is collected: the input signal (u), the white noise signal (w), and the output voltages (v). With this data we calculated the process sensitivity and the sensitivity and to obtain the plant we divided them (similar as we did during the Motion Control course). We are uncertain if the left and right pizza robots have a similar plant so perhaps we should repeat the FRF measurement on the right robot because that one has the pizza racks on it. |
Revision as of 11:23, 25 February 2013
Group Members
Name: | Student id: | Email: |
Rens Samplonius | 0785119 | r.j.samplonius@student.tue.nl |
Frank Evers | 0789890 | f.evers@student.tue.nl |
Juan Guo | 0825223 | j.guo@student.tue.nl |
Jeroen Lamers | 0771264 | j.w.lamers@student.tue.nl |
Planning
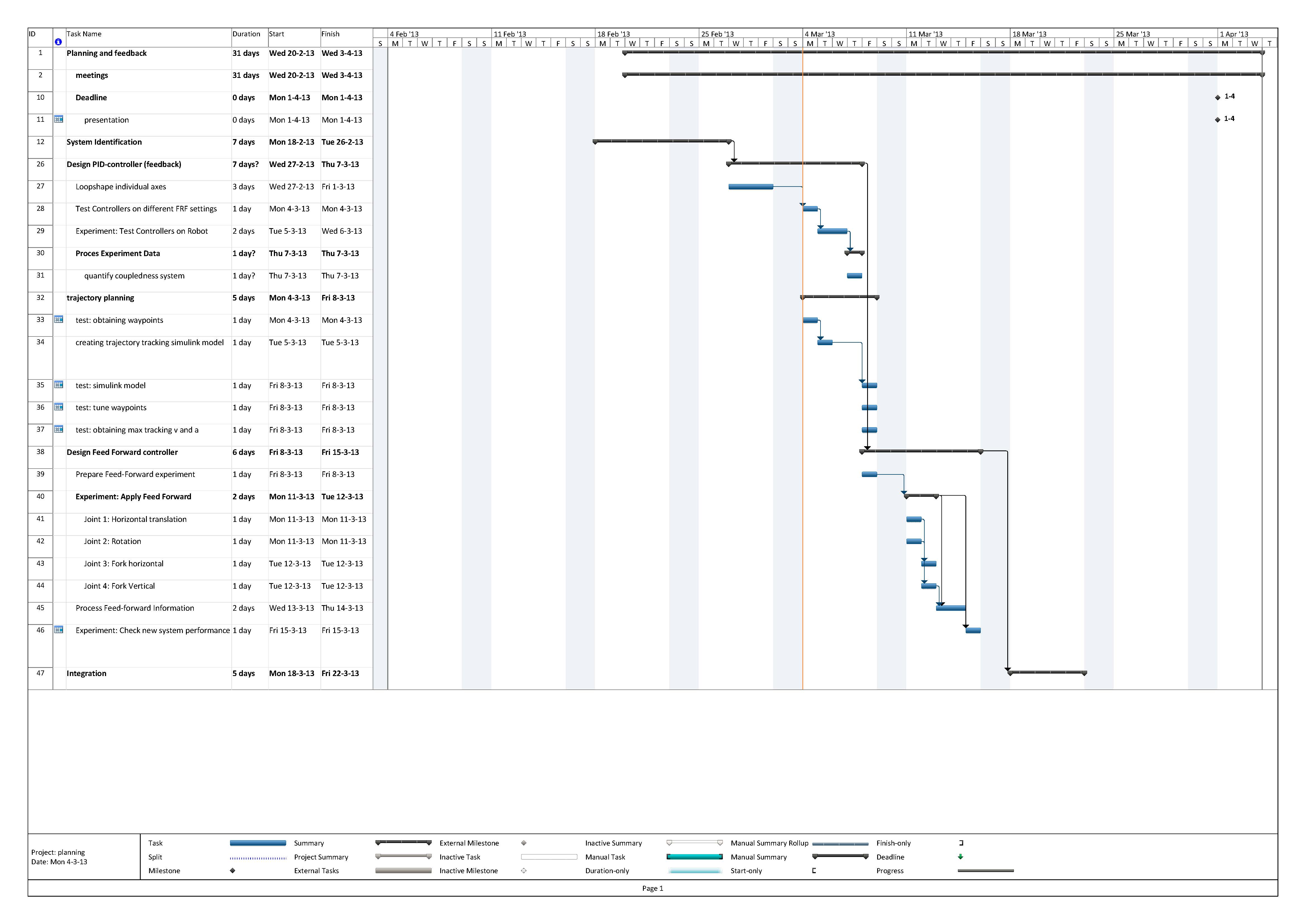
Week: | Activities: |
---|---|
Feb 18 - Feb 24 | |
Obtain robot specifications such as motor saturation (Frank - 4 hours). | |
Design FRF measurement white noise injection and conduct the measurement (Rens / Jeroen - 6 hours). | |
Make a selection of useful literature for the other group members (Jazz - 5 hours). | |
Feb 25 - Mar 3 | |
Design of kinematic model (not sure yet if needed) (Frank - 8 hours) | |
Analyze FRF data (Rens / Jazz - 8 hours) | |
Determine optimal algorithm: PID, LQG, H1, MPC or ILC (Jeroen - 4 hours) | |
Mar 4 - Mar 10 | |
Design controllers based on chosen algorithm for four axises separately (loop shaping) feedback and feedforward (All - 8 hours) | |
Mar 11 - Mar 17 | |
Test/tune designed controllers on the machine (Jazz / Rens - 5 hours) | |
Design optimal trajectory (Jeroen / Frank - 8 hours) | |
Mar 18 - Mar 24 | |
Test optimal trajectory on the machine (Frank / Jeroen - 3 hours) | |
Make presentation + solving unexpected problems (Rens / Jazz - 3 hours) | |
Apr 1 - Apr 7 |
Progress
Week 1
- List of what you have done and learned
- ...
Week 2
- Rens and Jeroen conducted an FRF measurement on the left pizza robot. They did a closed loop measurement on each axis by applying a sin-wave + white noise to the plant. The sine wave is added to overcome the massive friction. The controller used in the closed loop measurement is tuned very low. During the FRF measurement the following data is collected: the input signal (u), the white noise signal (w), and the output voltages (v). With this data we calculated the process sensitivity and the sensitivity and to obtain the plant we divided them (similar as we did during the Motion Control course). We are uncertain if the left and right pizza robots have a similar plant so perhaps we should repeat the FRF measurement on the right robot because that one has the pizza racks on it.