PRE2019 3 Group13: Difference between revisions
(675 intermediate revisions by 5 users not shown) | |||
Line 1: | Line 1: | ||
<div style="width:calc(100vw - 175px);background-color:#FDFEFE;padding-bottom:35px;position:absolute;top:0;left:0;"> | |||
<div style="font-family: 'q_serif', Ariel, Helvetica, sans-serif; font-size: 14px; line-height: 1.5; max-width: 1125px; word-wrap: break-word; color: #333; font-weight: 400; box-shadow: 0px 25px 35px -5px rgba(0,0,0,0.75); margin-left: auto; margin-right: auto; padding: 70px; background-color: white; padding-top: 25px;"> | |||
<center><big><big><big><b>Parkinson Spoon for Hand Tremors</b></big></big></big></center><br> | |||
== Group members == | == Group members == | ||
{| | {| class="wikitable" style="border-style: solid; border-width: 1px;" cellpadding="3" | ||
|- | |- | ||
! scope="col" width="width:20em;" |Student name | ! scope="col" width="width:20em;" |Student name | ||
Line 34: | Line 40: | ||
|} | |} | ||
== | == Peer review == | ||
[[Peer review ]] | |||
== | == Presentation == | ||
You can download the presentation here: https://we.tl/t-bdd7DOqQko . | |||
== Problem Statement == | |||
Simple tasks like eating are not as easy for everyone. For instance: people with a tremor, or who are suffering from Parkinson’s disease, have trouble with something as simple as bringing a spoon to their mouth. Their meals take a lot longer and they often have to be assisted while eating. There are several products available on the market, like self-stabilizing spoons and forks, but the disadvantage of these products is that they are quite expensive and big. With these existing solutions people are able to eat independently again, but they always have to take their own cutlery with them. | |||
== Objectives == | |||
'''Independent use -''' | |||
The user should be able to utilize this product independently to assist them while eating. This means that the device should be easy to turn on and be natural to use. This way, the user can do daily life tasks without needing help from caregivers, and thus making them more independent. | |||
'''Cost efficient -''' | |||
As people with Parkinson's disease often already have enough costs to care for their disability, it is important that the device is affordable (less than €100,-). This way, it can be available for way more users in need. Another point to keep in mind is safety. If this device is too expensive the user will be at risk of being robbed, which has to be considered as people with Parkinson's disease can be more vulnerable and an easy target to rob. | |||
'''Comfortable in use -''' | |||
The device should be comfortable in use for the target group. It should have a shape that is comfortable to hold for the duration of a three-course meal. Using the device should not cause any pain or harm and users should have no negative feelings when using it. These criteria will be verified through user tests. The user should be fully comfortable using the device within two weeks of getting used to it. | |||
'''Recognize nature of movement -''' | |||
The device should recognize unwanted vibrations that are, for instance, caused by a tremor or Parkinson’s disease. The unwanted vibrations should be distinguished from deliberate movement of the cutlery within one period of movement. The error in recognizing the nature of the movement should be less than 10%. | |||
'''Act on unwanted movement -''' | |||
When an unwanted movement is recognized, this should be compensated by keeping the piece of cutlery stable. The stabilizing should not take more than two periods of unwanted vibrations. The piece of cutlery should only be allowed to move in the direction of the deliberate movements. | |||
The device should be compatible with at least 90% of the cutlery that is used in restaurants. Therefore the part of the device that is connected to the cutlery must be adjustable in size and it should be able to attach and use the device within one minute. The device should be able to work for at least three hours without intermediate charging. | '''Modular -''' | ||
The device should be compatible with at least 90% of the cutlery that is used in restaurants. Therefore the part of the device that is connected to the cutlery must be adjustable in size and it should be able to attach and use the device within one minute. This means that the user can feel more comfortable when using the device, as the device can be attached to the cutlery other people are using for example. The device should be able to work for at least three hours without intermediate charging. This is for the comfort of the user, as they might want to use the spoon during the whole day without having to charge it. | |||
== Approach, Milestones Deliverables and Planning == | == Approach, Milestones, Deliverables and Planning == | ||
=== Approach === | === Approach === | ||
The aim of this project is to help people with nerve diseases | The aim of this project is to help people with nerve diseases that cause tremors to become more independent. We are going to do this by making a device that can be attached to any cutlery, which makes it possible to eat independently for the target group. We want to achieve this goal by doing extensive research and eventually delivering a simplified prototype including information about this prototype on the wiki page. The approach to reach these goals contains multiple steps. | ||
1. Research | 1. Research | ||
Firstly, we will be going through research papers and other sources which describe the state of art of such cutlery and its respective components. This allows our | Firstly, we will be going through research papers and other sources which describe the state of the art of such cutlery and its respective components. This allows our team to get a grasp of the current technology of such a system and introduce us to the new developments in this field. This helps to create a foundation for the project, which we can develop into. The state of art also gives valuable insight into possible solutions to solve our problem statement. The research has to be done with the use of literature, survey(s), personal interview(s), recent reports from research institutes and the media and analysing patents that are strongly connected to our project. | ||
2. USE aspects | 2. USE aspects | ||
Furthermore, we will continue to analyze the problem from a USE – user, society, enterprise – perspective. An important source of this analysis is the state of art research, where the | Furthermore, we will continue to analyze the problem from a USE – user, society, enterprise – perspective. An important source of this analysis is the state of the art research, where the impact of these cutlery systems in different stakeholders is discussed. The USE aspects will be of utmost importance for our project as every engineer should strive to develop new technologies for helping not only the users but also the society as a whole and to consider the possible consequences of the system they develop. This analysis will lead to a list of requirements for our design. We also set up a survey to find out any unknown requirements. This makes that the requirements are based on the USE analysis and the survey. | ||
3. Product shaping | 3. Product shaping | ||
When we finish these two steps, we will develop a prototype in which the product will be conceptualized and programmed. In this process, the RPC's are used to design the software, hardware and the appearance of the prototype. | |||
4. Documentation | 4. Documentation | ||
To finish, the wiki has to be updated and should contain the whole process of designing our prototype, as well as all of the research that is done to get there. To accomplish this, someone will be assigned to check and edit the page every week. Besides the wiki, a presentation has to be made in anticipation of the last few weeks. | |||
Listed below is a summary of the main steps in our approach of the project. | |||
*Doing research on our chosen project using SotA literature analysis | *Doing research on our chosen project using SotA literature analysis | ||
* | *Analysing the USE aspects and set up the survey to determine the requirements of our device | ||
*Choose the Hardware and Software for the prototype | *Choose the Hardware and Software for the prototype | ||
*Work on the prototype | *Work on the prototype | ||
Line 94: | Line 110: | ||
* Week 1: The subject is chosen and also the Plan for the project has been made. | * Week 1: The subject is chosen and also the Plan for the project has been made. | ||
* Week 2: It is clear who the users are, the research is finished and also the requirements are | * Week 2: It is clear who the users are, the research (SotA) is finished and also the requirements are determined. | ||
* Week 3: Research into design prototype and costs + | * Week 3: Research into design prototype and costs + set up survey. | ||
* Week 4: Research into software prototype and a list of parts and estimation of costs is made | * Week 4: Research into software prototype and a list of parts and estimation of costs is made. | ||
* Week 5: Building prototype + information from | * Week 5: Building prototype + information from survey to improve the prototype. | ||
* Week 6: The prototype has been made. | * Week 6: The prototype has been made. | ||
* Week 7: The | * Week 7: The demo will be finished and ready to be presented. | ||
* Week 8: The wiki page is finished and updated with the results that were found from testing the prototype. Also, future developments are looked into and added to the wiki page. | * Week 8: The wiki page is finished and updated with the results that were found from testing the prototype. Also, future developments are looked into and added to the wiki page. | ||
Line 107: | Line 123: | ||
*This wiki page, which contains all of our research and findings | *This wiki page, which contains all of our research and findings | ||
*A presentation, which is a summary of what was done and what our most important results are | *A presentation, which is a summary of what was done and what our most important results are | ||
*A prototype | *A prototype, due to the situation caused by COVID-19 this consists of two parts: the electronics and the 3D printed case which could not be put together. | ||
*A | *A demo, due to the situation caused by COVID-19 this is included in the presentation | ||
===Planning=== | ===Planning=== | ||
Line 126: | Line 142: | ||
| style="text-align: center; font-style:italic; background-color:#deedfd;" | Research | | style="text-align: center; font-style:italic; background-color:#deedfd;" | Research | ||
| style="text-align: center; font-style:italic; background-color:#deedfd;" | RPC's and USE Analysis + start prototype research | | style="text-align: center; font-style:italic; background-color:#deedfd;" | RPC's and USE Analysis + start prototype research | ||
| style="text-align: center; font-style:italic; background-color:#deedfd;" | Hardware Design + | | style="text-align: center; font-style:italic; background-color:#deedfd;" | Hardware Design + Survey | ||
| style="text-align: center; font-style:italic; background-color:#deedfd;" | Software Design + | | style="text-align: center; font-style:italic; background-color:#deedfd;" | Software Design + Survey | ||
| style="text-align: center; font-style:italic; background-color:#deedfd;" | Prototype | | style="text-align: center; font-style:italic; background-color:#deedfd;" | Prototype | ||
| style="text-align: center; font-style:italic; background-color:#deedfd;" | Proof Reading | | style="text-align: center; font-style:italic; background-color:#deedfd;" | Proof Reading | ||
| style="text-align: center; font-style:italic; background-color:#deedfd;" | | | style="text-align: center; font-style:italic; background-color:#deedfd;" | Demo | ||
| style="text-align: center; font-style:italic; background-color:#deedfd;" | Conclusions | | style="text-align: center; font-style:italic; background-color:#deedfd;" | Conclusions + Future Developments | ||
|- | |- | ||
| rowspan="3" style="text-align: center;" | Heather Hanegraaf | | rowspan="3" style="text-align: center;" | Heather Hanegraaf | ||
Line 138: | Line 154: | ||
| Wiki Page check | | Wiki Page check | ||
| USE Analysis | | USE Analysis | ||
| | | USE Analysis | ||
| | | Presentation script | ||
| | | Start making presentation | ||
| Wiki Page check | | Wiki Page check | ||
|- | |- | ||
| | | Brainstorm subject ideas | ||
| Requirements justification | | Requirements justification | ||
| Survey | | Survey | ||
| Survey | | Survey | ||
| | | Send Survey | ||
| | | Survey ideas | ||
| | | Finish presentation | ||
| | | Finish presentation + audio | ||
|- | |- | ||
| Make the planning | | Make the planning | ||
Line 157: | Line 173: | ||
| | | | ||
| | | | ||
| | | Efficiency of performance method | ||
| | | Clean the wiki page | ||
| | | Clean the wiki page | ||
|- | |- | ||
| rowspan="3" style="text-align: center;" | Yara Daamen | | rowspan="3" style="text-align: center;" | Yara Daamen | ||
Line 166: | Line 182: | ||
| Survey | | Survey | ||
| Wiki Page check | | Wiki Page check | ||
| | | Foam grapper system | ||
| | | Foam grapper system | ||
| | | Finish Presentation | ||
| Wiki Page check | | Wiki Page check | ||
|- | |- | ||
Line 174: | Line 190: | ||
| | | | ||
| | | | ||
| Adjust objectives | |||
| | | | ||
| | | | ||
| | | Finish chapter "holding spoon" | ||
| | | Finish presentation + audio | ||
|- | |- | ||
| | | | ||
| | | | ||
| | | | ||
| | | Survey | ||
| | | | ||
| | | | ||
Line 189: | Line 205: | ||
| | | | ||
|- | |- | ||
| rowspan=" | | rowspan="3" style="text-align: center;" | Mayke Scheffer | ||
| Write problem statement and objectives | | Write problem statement and objectives | ||
| Research Prototype | | Research Prototype | ||
| Explain start prototype | | Explain start prototype | ||
| | | Improve Prototype | ||
| Wiki Page check | | Wiki Page check | ||
| | | Make final prototype | ||
| | | Finish prototype | ||
| Wiki Page check | | Wiki Page check | ||
|- | |- | ||
Line 203: | Line 219: | ||
| Improve Prototype | | Improve Prototype | ||
| | | | ||
| Order Components | |||
| Prototype Justification | |||
| | | | ||
| | | Finish prototype | ||
|- | |- | ||
| | | | ||
Line 221: | Line 228: | ||
| | | | ||
| | | | ||
| Meeting Prototype Building | |||
| | | | ||
| | | Edit BoM | ||
| | | Start testing prototype | ||
|- | |- | ||
| rowspan="3" style="text-align: center;" | Wouter Haneveer | | rowspan="3" style="text-align: center;" | Wouter Haneveer | ||
| Research 5 papers | | Research 5 papers | ||
| | | | ||
| 3D printing | | 3D printing | ||
| | | 3D printing report on wiki page | ||
| | | make 3D printing | ||
| Wiki Page check | | Wiki Page check | ||
| | | Finish 3D printing | ||
| Wiki Page check | | Wiki Page check | ||
|- | |- | ||
Line 239: | Line 246: | ||
| Summary State of the art sources 7-25 | | Summary State of the art sources 7-25 | ||
| | | | ||
| 3D printing improve | |||
| | | | ||
| Final 3D model printing | |||
| | | | ||
| | | Edit BoM | ||
|- | |- | ||
| | | | ||
Line 251: | Line 258: | ||
| | | | ||
| | | | ||
| | | Edit Wiki page | ||
| | | Clean wiki page | ||
|- | |- | ||
| rowspan=" | | rowspan="2" style="text-align: center;" | Gijs van Bakel | ||
| Write User part | | Write User part | ||
| Research Prototype | | Research Prototype | ||
| Mechanical solutions research | | Mechanical solutions research | ||
| | | Literature Study check | ||
| | | Meeting Prototype Building | ||
| | | Prototype Justification | ||
| Wiki Page check | | Wiki Page check | ||
| Wiki Page check | | Wiki Page check | ||
Line 267: | Line 274: | ||
| Summary state of the art sources 1-6 | | Summary state of the art sources 1-6 | ||
| | | | ||
| Arduino code on wiki page | |||
| | | | ||
| | | | ||
| | | Write future improvements | ||
| | | Finish future improvements | ||
|- | |- | ||
| style="background-color:#3f96f1; color:#efefef;" | | | style="background-color:#3f96f1; color:#efefef;" | | ||
Line 297: | Line 295: | ||
| Group meeting | | Group meeting | ||
| Group meeting | | Group meeting | ||
| | | Group meeting | ||
| | | Skype Meeting online | ||
| | | Skype Meeting 1 | ||
| | | Skype Meeting 1 | ||
|- | |- | ||
| Online meeting ( | | Online meeting (WhatsApp) about subject | ||
| | | | ||
| | | | ||
Line 310: | Line 306: | ||
| | | | ||
| | | | ||
| Skype Meeting 2 | |||
| Skype Meeting 2 | |||
|- | |- | ||
| | | | ||
Line 318: | Line 316: | ||
| | | | ||
| | | | ||
| | | Skype meeting 3 | ||
|} | |} | ||
== | == State of the Art== | ||
Several papers have been collected on the topic of self-stabilizing technologies, which are shown at the 'Literature study week 1' section near the end of the report, together with a short summary in one or two sentences. They are sorted into distinctive categories for clarity. The following section summarizes the most important findings of the collected literature for our project, together with additional research on other topics that have been done at a later time such as the section on mechanical stabilization. | |||
=== Similar products === | |||
Active cancellation hardware is currently used in noise-canceling headphones and a similar method can be used for self-stabilizing spoons<ref>Thilmany, J. (2013). Stable spoon. Mechanical Engineering; New York, 135(5) </ref>. This method uses two DC motors connected with mechanical yokes that couple vertical and horizontal motion of the spoon. The sensor/controller system uses a tri-axial accelerometer embedded in the spoon base to sense the direction of tremor in the x and y directions and directs the spoon to move in the opposite direction. A bandpass filter is used to filter out noise, and acceleration data as a function of time is resolved into the frequency domain using Fourier transformation<ref name = "Pathak">Pathak, A., Redmond, J. A., Allen, M., & Chou, K. L. (2013). A noninvasive handheld assistive device to accommodate essential tremor: A pilot study. Movement Disorders, 29(6), 838–842. https://doi.org/10.1002/mds.25796 </ref>. | |||
Vibration isolation and a dynamic vibration absorber can be used to reduce the hand tremor with a semi-active device, which can not only reduce hand tremors but can also generate its needed electrical energy<ref> Abbasi, M., & Afsharfard, A. (2018). Modeling and experimental study of a hand tremor suppression system. Mechanism and Machine Theory, 126, 189–200. https://doi.org/10.1016/j.mechmachtheory.2018.04.009 </ref>. In this system, two clamped guided piezoelectric beams are used to hold the spoon and a clamped piezoelectric beam is used as a dynamic vibration absorber. | |||
A PID controller can be used to actively control the system. This type of controller continuously calculates an error value e(t) as the difference between the desired setpoint (SP) and a measured process variable (PV) and applies a correction based on proportional, integral, and derivative terms (denoted P, I and D respectively), hence the name. In the study “Design of a noninvasive and smart hand tremor attenuation system with active control: a simulation study” two motors are used that can rotate in perpendicular directions, which allow the mechanism tip to move horizontally and vertically<ref> Abbasi, M., Afsharfard, A., Arasteh, R., & Safaie, J. (2018). Design of a noninvasive and smart hand tremor attenuation system with active control: a simulation study. Medical & Biological Engineering & Computing, 56(7), 1315–1324 https://doi.org/10.1007/s11517-017-1769-9 </ref>. | |||
Another method uses Inertial Measurement Unit (IMU) sensors and actuators for stabilizing a cup while under severe hand vibration. It is like the Active force method in the sense that a microcontroller processes the feedback from the IMU, upon which it rotates the two motors in the opposite direction of hand movement in order to achieve proper stabilization. PI and PID controllers are also used for this self-stabilizing cup<ref> Vishnu, V., Prabaharan, P., Sujadevi, V.G., Meher, M.D.IMU sensor-based self-stabilizing cup for elderly and Parkinsonism (2017) 2017 International Conference on Advances in Computing, Communications and Informatics, ICACCI 2017, 2017-January, pp. 2264-2269. </ref>. | |||
Note on the frequency of tremors: Based on previous studies, it is concluded that the frequency of the hand tremor is different from the frequency of the voluntary movement. Accordingly, the frequency of the hand tremor in Parkinson’s disease is in the range of 3–6 Hz and it is between 5 and 12 Hz in essential tremor disease. Therefore, a low-pass filter, with a cut-off frequency of 3 Hz, can be used to distinguish the voluntary motion from tremor movement<ref> Bhidayasiri R (2005) Differential diagnosis of common tremor syndromes. Postgrad Med J 81(962):756–762. https://doi.org/10.1136/ </ref>. | |||
=== Solutions to reduce tremors === | |||
Next to self-stabilizing wearables we also did research on ways to reduce tremors, the most important findings to reduce tremors are listed below. | |||
One could think about adding weight to the patient's wrist or use a heavier spoon, since then an equal amount of force would mean less movement since the mass is bigger<ref> McGruder, J., Cors, D., Tiernan, A. M., & Tomlin, G. (2003). Weighted Wrist Cuffs for Tremor Reduction During Eating in Adults With Static Brain Lesions. American Journal of Occupational Therapy, 57(5), 507–516. https://doi.org/10.5014/ajot.57.5.507 </ref>. Although some research<ref> McGruder, J., Cors, D., Tiernan, A. M., & Tomlin, G. (2003). Weighted Wrist Cuffs for Tremor Reduction During Eating in Adults With Static Brain Lesions. American Journal of Occupational Therapy, 57(5), 507–516. https://doi.org/10.5014/ajot.57.5.507 </ref> does support this, there are also studies<ref> Meshack, R. P., & Norman, K. E. (2002). A randomized controlled trial of the effects of weights on amplitude and frequency of postural hand tremors in people with Parkinson’s disease. Clinical Rehabilitation, 16(5), 481–492. https://doi.org/10.1191/0269215502cr521oa </ref> that state that no significant changes can be seen by adding weight. | |||
Another solution that could be applied to the spoon is to make the handle smaller. As research<ref> Ma, H.-I., Hwang, W.-J., Chen-Sea, M.-J., & Sheu, C.-F. (2008). Handle size as a task constraint in spoon-use movement in patients with Parkinson’s disease. Clinical Rehabilitation, 22(6), 520–528. https://doi.org/10.1177/0269215507086181 </ref> shows that a smaller handle makes people with Parkinson's disease move faster and smoother, possibly since they have more control over the spoon due to the shorter distance to it. | |||
An exoskeleton can also be used to suppress tremors<ref> Meshack, R. P., & Norman, K. E. (2002). A randomized controlled trial of the effects of weights on amplitude and frequency of postural hand tremors in people with Parkinson’s disease. Clinical Rehabilitation, 16(5), 481–492. https://doi.org/10.1191/0269215502cr521oa </ref>. Here, an exoskeleton uses an electromyogram (EMG) signal, which is a biosignal which affects the activation of muscles, to measure whether the movement is voluntary or not. If the movement is voluntary the exoskeleton moves with the body, else it will not move and suppress the movement. However, exoskeletons can be used in other parts of the arm as well, like seen in research<ref>Hosseini, S.M., Al-Jumaily, A., Kalhori, H.Tremor suppression in wrist joint using active force control method(2017) 9th Australasian Congress on Applied Mechanics, ACAM 2017, 2017-November.</ref> much more complicated exoskeletons can be made. This one uses Active Force Control (AFC) based on piezoelectric actuators to reduce tremors in the wrist. | |||
Tremors could also be reduced by measuring the distance to an object and keeping this distance the same with the help of motors<ref> Song, C., Gehlbach, P. L., & Kang, J. U. (2012). Active tremor cancellation by a “Smart” handheld vitreoretinal microsurgical tool using swept-source optical coherence tomography. Optics Express, 20(21), 23414. https://doi.org/10.1364/oe.20.023414 </ref>. However, for our project this is not relevant since we want our tool to be usable in a dynamic environment and to pick up food, we need to go towards the food and this way would work against what we want to accomplish. | |||
With the use of accelerometers, actuators and position sensors, tremors could be seen and reduced by countering the force of the tremor with an equally big force in the opposite direction, according to research<ref> Hamdy, A. (1999). Active damping of vibrations in elevator cars. Journal of Structural Control, 6(1), 53–100. https://doi.org/10.1002/stc.4300060105 </ref>. However, this system is designed for cars and is therefore too big and expensive to use for a spoon. If a way smaller and cheaper version could be made, it might be a good way to reduce tremors in a spoon but the problem is that it might be difficult to see whether a movement is from a tremor or a voluntary movement from the user itself. | |||
By rotating an unbalanced mass, one could counter and thus reduce a tremor<ref> Chuanasa, J., & Songschon, S. (2014). Essential tremor suppression by a novel self-balancing device. Prosthetics and Orthotics International, 39(3), 219–225. https://doi.org/10.1177/0309364614525185 </ref> . However, added on a spoon this would make the spoon too heavy since we should add multiple masses to be able to create a counterforce in every direction, thus making it not usable for cutlery. | |||
Using a coin type vibration motor and a microcontroller, it is possible to create random vibration patterns to distract the user from the bio-mechanical feedback loop with the hand and reduces the hand tremor and improving the ability to grip or hold an object<ref> Vidya, V., Poornachandran, P., Sujadevi, V.G., Dharmana, M.M.Suppressing Parkinson's diseases induced involuntary movements using wearables(2018) Proceedings of 2017 IEEE International Conference on Technological Advancements in Power and Energy: Exploring Energy Solutions for an Intelligent Power Grid, TAP Energy 2017, pp. 1-4. https://doi.org/10.1109/TAPENERGY.2017.8397267 </ref>. | |||
1. | Lastly, we found that muscle co-contraction could be used to stabilize joints<ref> Gallego, J.A., Rocon, E., Belda-Lois, J.M., Pons, J.L. A neuroprosthesis for tremor management through the control of muscle co-contraction (2013) Journal of NeuroEngineering and Rehabilitation, 10 (1), art. no. 36. DOI: 10.1186/1743-0003-10-36 </ref>. When a tremor is measured, the muscles are electronically contracted to stabilize the joint, this reduces the tremors since your muscles are contracted and thus unable to create a tremor. | ||
=== Measuring tremors === | |||
We also did research on ways to measure tremors, here are our findings of how to measure tremors. | |||
One could measure tremors by using advanced mathematical methods of time series analysis as seen in this research<ref>Lauk, M., Timmer, J., Lücking, C. H., Honerkamp, J., & Deuschl, G. (1999). A software for recording and analysis of human tremor. Computer Methods and Programs in Biomedicine, 60(1), 65–77. https://doi.org/10.1016/s0169-2607(99)00012-7</ref>. Here an easy to use Microsoft windows application is built to investigate forms of tremors using advanced mathematical methods of time series analysis. | |||
We also found a device using four accelerometers and is capable to measure tremors, movement and accidental falls<ref>Gugliandolo G, Capra PP, Bramanti A, Di Lorenzo G, Campobello G, Donato N, Marino S (2019). A Movement-Tremors Recorder for Patients of Neurodegenerative Diseases. IEEE Transactions on Instrumentation and Measurement, 68(5), 1451-1457. | |||
https://doi.org/10.1109/TIM.2019.2900141</ref>. This device also has the possibility to connect via Bluetooth, Wi-Fi and GSM to a remote supervisor. | |||
Another way to measure tremors is by combining accelerometers with gyroscopic transducers. A device is made using three-axis accelerometer and three axis gyroscopic transducers embedded in one device called shimmer<ref>Reem Musab, Azizan As’arry, Khairil Anas Md Rezali, Nawal Aswan Abdul Jalil, Raja Mohd Kamil Raja Ahmad, Mohd Zarhamdy Md Zain (2019). Tremor Quantification and its Measurements Using Shimmer. Journal of Physics: Conference Series, 1262. https://dx.doi.org/10.1088/1742-6596/1262/1/012024</ref>. This device can measure the acceleration, velocity and displacement of a tremor. | |||
=== Stabilization in other fields === | |||
So far all the sources that are found are directly related to our product, either with the active force method, a PID controller or some other electronic device. However we know that other methods of stabilizing, for instance mechanically, are also used in other fields. Since no sources have been found that directly use mechanical stabilization for stabilizing cutlery, some literature on self-stabilizing cameras has been found to see if we can draw any parallels. Mainly because we also wanted to see whether this could be applied to our problem statement. So to reach this goal, more literature research into stabilization in general has been done, with the results of this presented below. | |||
Some literature<ref> Rodriguez-Padilla, I., Castelle, B., Marieu, V., Morichon, D. A simple and efficient image stabilization method for coastal monitoring video systems (2020) Remote Sensing, 12 (1), art. no. 70. https://doi.org/10.3390/RS12010070 </ref> mentions how image stabilization is actually not done actively, but “edited in”. A template matching method is used that consists of selecting small high-contrast regions of an image and these are matched with a reference image to compute their displacement, which is then corrected<ref> Rodriguez-Padilla, I., Castelle, B., Marieu, V., Morichon, D. A simple and efficient image stabilization method for coastal monitoring video systems (2020) Remote Sensing, 12 (1), art. no. 70. https://doi.org/10.3390/RS12010070 </ref>. | |||
Another source of literature mentions a similar approach to the ones that have been found for stabilizing cutlery, using a PID controller with an inertial measurement unit (IMU)<ref> Auysakul, J., Xu, H., Pooneeth, V. Video stabilization with a dual system based on an IMU sensor for the mobile robot (2019) Advances in Intelligent Systems and Computing, 856, pp. 618-626. https://doi.org/10.1007/978-3-030-00214-5_78 </ref>. The same method is used for cameras on UAVs (unmanned aerial vehicles)<ref> Franco, F.P.L., Loubach, D.S., Fioravanti, A.R. An embedded system design for a two-axis camera platform control used in unmanned aerial vehicles (2017) Proceedings - 2017 LARS 14th Latin American Robotics Symposium and 2017 5th SBR Brazilian Symposium on Robotics, LARS-SBR 2017 - Part of the Robotics Conference 2017, 2017-December, pp. 1-6. https://doi.org/10.1109/SBR-LARS-R.2017.8215289 </ref>. | |||
MEMS (micro-electromechanical system)-based gyroscopes and accelerometers are also used in order to stabilize cameras. These units are however specifically made for this purpose and would be too big to use in the area of self-stabilizing cutlery<ref> Sofla, M.S., Parsa, M., Golshanian, H. Stabilizing a camera mount using MEMS gyroscope and accelerometer (2016) Transactions of the Institute of Measurement and Control, 38 (11), pp. 1345-1352. https://doi.org/10.1177/0142331215587339 </ref>. | |||
== USE Analysis == | |||
It is good to first know who the users of the product are. Society and enterprise must also be taken into account before we start making the prototype. That is why a USE analysis is being carried out. The requirements will then be formed from this USE analysis after which we will us to develop the prototype. | |||
===User=== | |||
First, we take a look at the user aspect of our product. At the start of this project it was only clear that there would be a product for people with a tremor or a disorder in the nerves. First of all, research was done into which disorders where tremors occur, since people with those disorders are potential users of our product. It was interesting to conduct further research into the disorders MS, Parkinson's and essential tremors. Now, a short analysis will follow about these diseases and then a choice will be made for which patients our device will be developed. | |||
'''MS''' | |||
More than 2.3 million people are affected by MS worldwide. Most people living with MS are diagnosed between the ages of 20 and 50, with more than twice as many women as men being diagnosed with the disease. MS is an abbreviation for multiple sclerosis. It is an unpredictable, often disabling disease of the central nervous system, caused by the immune system which attacks the protective sheath (myelin) that covers nerve fibers and causes communication problems between your brain and the rest of your body. Eventually, the disease can cause permanent damage or deterioration of the nerves<ref>Mayo Clinic Staff. (2019, 19 April). Multiple sclerosis - Symptoms and causes. Retrieved from https://www.mayoclinic.org/diseases-conditions/multiple-sclerosis/symptoms-causes/syc-20350269</ref>. Symptoms range from numbness and tingling to blindness and paralysis. The disease varies greatly from person to person, and from time to time, for the same person. For instance, one person might experience abnormal fatigue, another might have severe vision problems, and another could develop attention and memory issues. Besides these symptoms, tremor, lack of coordination or unsteady gait can also be experienced. Even severe symptoms could disappear completely and the person could regain lost functions. However, in the worst cases, people can have partial or complete paralysis<ref> National MS Society. (z.d.). MS the Disease. Retrieved from https://www.nationalmssociety.org/About-the-Society/Press-Room/MS-the-Disease </ref>. | |||
'''Parkinson's disease''' | |||
Parkinson's disease is the second most common progressive brain disease with 7 million patients worldwide. Parkinson's disease is a brain disorder that leads to shaking, stiffness, and difficulty with walking, balance, and coordination. Parkinson's symptoms usually begin gradually and get worse over time. As the disease progresses, people may have difficulty walking and talking. They may also have mental and behavioral changes, sleep problems, depression, memory difficulties, and fatigue. One clear risk factor for Parkinson's is age, most people with Parkinson’s develop the disease at about age 60. Parkinson's disease signs and symptoms can be different for everyone. Early signs may be mild and go unnoticed. Symptoms often begin on one side of your body and usually remain worse on that side, even after symptoms begin to affect both sides. Parkinson's disease has four main symptoms: | |||
tremor (trembling) in hands, arms, legs, jaw, or head, stiffness of the limbs and trunk, slowness of movement and impaired balance and coordination, sometimes leading to falls<ref> National Institute of Aging. (2017, 16 May). Parkinson’s Disease. Retrieved from https://www.nia.nih.gov/health/parkinsons-disease </ref>. Another symptom is chewing and swallowing difficulties can occur, especially during the later stages of the disease. These can be due to changes in function either in the autonomic nervous system or the muscles in the throat, known as the pharyngeal muscles<ref>The MNT Editorial Team. (2018, 26 October). Parkinson’s disease complications. Retrieved from https://www.medicalnewstoday.com/articles/323399#chewing-and-swallowing</ref>. | |||
'''Essential tremors''' | |||
Essential tremor is a nervous system (neurological) disorder that causes involuntary and rhythmic shaking. It can affect almost any part of your body, but the trembling occurs most often in hands — especially when doing simple tasks, such as drinking from a glass or tying shoelaces. Essential tremor is usually not a dangerous condition, but it typically gets worse over time and can be severe for some people. Other conditions don't cause essential tremor, although essential tremor is sometimes confused with Parkinson's disease. Essential tremor can occur at any age but is most common in people aged 40 and older. The tremor signs and symptoms begin gradually, usually more prominently on one side of the body, worsen with movement, usually occur in the hands first, affecting one hand or both hands, it can include a "yes-yes" or "no-no" motion of the head and it may be aggravated by emotional stress, fatigue, caffeine or temperature extremes<ref>Mayo Clinic Staff. (2019, 23 January). Essential tremor - Symptoms and causes. Retrieved from https://www.mayoclinic.org/diseases-conditions/essential-tremor/symptoms-causes/syc-20350534 </ref>. | |||
'''Target group''' | |||
Our targeted users are people suffering from hand and arm tremors which are caused by the Parkinson’s disease but also people suffering from essential tremors. We have chosen both conditions as users, as this increases the number of people who are potential users. Furthermore, essential tremors and the tremors in Parkinson's disease are very similar, therefore the spoon can be used by both patients. | |||
To really focus on perfecting a product fitted to our targeted users, it is necessary to choose a specific topic. Therefore, we mainly focus on Parkinson's patients, as this is a much better known problem that needs to be addressed. These users, people with Parkinson’s disease, are in almost all cases elderly around or above 60. These people are often in need of a lot of care and can’t perform a variety of independent tasks on their own. Especially eating is a very frequent activity that has to be assisted minimally 3 times a day. For patients who are still mentally healthy it can be a very degrading feeling to have to be fed. A device that could help these patients could greatly improve their independence and feeling of self-worth. Although we focus on Parkinson, the spoon can thus still be used by both parties. | |||
===Society=== | |||
For the society, this device can make a small, but needed, change to the healthcare. As the population of elderly grows bigger and bigger so will the amount of patients with Parkinson’s disease. This will have a big impact on the society as they are in high need of caring. By using this device, the working load for the caretakers could be decreased, allowing them to have more time for other activities. Furthermore, it can greatly improve patients' independence and feeling of self-worth. This is also a benefit to society, as people may feel happier overall. | |||
===Enterprise=== | |||
The Enterprise stakeholder is about companies that have the same kind of idea to tackle this problem. It is clear that there is already a market for these products. We will now discuss some of those similar products. | |||
'''Flexible TPE and Lepel Torso Grip''' | |||
Our solution is aimed at robots and works through the use of electricity, but there are also companies that have come up with a much simpler solution. For example, a flexible silicone edge around the edge of the spoon. In this way, the food stays on the spoon better. This can indeed be a good solution for the problem, but the success rate of an electric spoon is higher than with this solution. | |||
Another simple solution is to make a better grip on the spoon. This way the spoon is easier to hold for people with Parkinson's disease. The handle of the spoon itself then becomes larger, which research shows that this has no positive effect on the use of the spoon. This research was conducted by Clinical Rehabilitation and their findings were as follows: "The movement of the participants with Parkinson's disease was faster (shorter movement time) and smoother (fewer movement units) when they used spoons with a small or medium-sized handle than when using a spoon With a large-sized handle. In contrast, the healthy controls showed no significant differences in movement kinematics between handle sizes. Moreover, the participants with Parkinson's disease had a significantly smaller hand aperture and used more fingers to hold the spoons than the controls did"<ref> Ma, H.-I., Hwang, W.-J., Chen-Sea, M.-J., & Sheu, C.-F. (2008). Handle size as a task constraint in spoon-use movement in patients with Parkinson’s disease. Clinical Rehabilitation, 22(6), 520–528. https://doi.org/10.1177/0269215507086181 </ref>. This shows that the handle should not be too large, but it should be big enough since patients with Parkinson's hold the spoon with more fingers. So, in our design we want a combination of good grip, big enough size for holding the spoon, but not too big because this would have a negative effect on the time to move and the smoothness to do so. | |||
'''Foodrobot''' | |||
A robotic arm is another solution to the problem. ZorgvanNu explains how it works: "Obi has two control buttons: one to choose which bowl to scoop from, and one to control the scooping movement. An arm with a spoon on it scoops up the food and brings it to the mouth. If you are going to use Obi, first set the correct position of the arm in relation to your mouth. You can always set it (or have it adjusted) in a different way, so that you do not always have to sit in the same way"<ref> Zorg van nu. (2020, 11 February). Hulp bij eten met een eetrobot. Retrieved from https://www.zorgvannu.nl/oplossingen/hulp-bij-eten-met-een-eetrobot</ref>. This can be an effective solution if the tremors become so bad that the patient can no longer hold the spoon. However, we have opted for a different solution, which is to be more mobile and not to have to carry a large device if the patient goes out for diner, for example. Another disadvantage of this solution is that the contact between human and robot must be very consciously taken into account. Because if the patient suffocates, the robot simply continues, which would not be user-friendly. It is a good solution, if people come in the next stage of Parkinson's and they have no other option left. However, our solution is for people who can still use a spoon themselves. | |||
'''Liftware, Gyenno and "Smart"-spoon''' | |||
There are also products that are very similar to what we want to produce. This is namely a spoon that measures the tremors and then tries to counteract it by making the opposite movement. Liftware, Gyenno and "Smart" spoon are examples of this. Although there are already working products on the market, we are convinced that we can improve the product. | |||
Those products are namely still expensive and the spoon is attached to the device. Our goal is to produce a simple and cheap working device that can be attached to any spoon to create a natural eating experience. | |||
[[File:Enterprisegood1.jpg|thumb|center|900px|''Figure 1: Other solutions for the same problem, Stakeholder Enterprise'']] | |||
== Survey == | |||
A survey has been set up to find out how the prototype can be better shaped and which requirements have to be met. This survey was sent to several Parkinson associations. The first association we chose to message was called Parkinson Vereniging. We chose to send it here, as it is the largest institution of Parkinson's disease in the Netherlands. It was decided to conduct a survey in the Netherlands, as those associations are best accessible and the quickest response to our survey. The e-mail address we sent it to is: info@parkinson-vereniging.nl<ref>Parkinson Vereniging. (z.d.). Contact - Parkinson Vereniging. Retrieved from https://www.parkinson-vereniging.nl/vereniging/over-ons/contact</ref>. The survey is addressed to the caregivers of patients with Parkinson's. Here's what the survey looks like. [https://docs.google.com/forms/d/e/1FAIpQLSfME0exoPSjNz4ReOvD5ulC4dInkMmjatNTKIomBhKOiNx2iQ/viewform?usp=sf_link Link Survey]. They responded by telling us the Parkinson Vereniging wasn't really meant for that. They did however link two other options to continue our research. The first link they sent was of parkinsonzorgzoeker.nl<ref>parkinsonzorgzoeker. (z.d.). Contact - parkinsonzorgzoeker. Retrieved from https://(www.parkinsonzorgzoeker.nl</ref>. However, this site is mostly meant for approaching individuals, whereas we needed to contact as many people as possible. We thus decided that this site was not useful for us. The next link they sent was also from Parkinson Vereniging, but this time meant especially for research requests<ref>Parkinson Vereniging. (z.d.). Contact - Parkinson Vereniging. Retrieved from https://www.parkinson-vereniging.nl/onderzoek/oproepen-onderzoek/oproepen</ref>. We also sent them a mail. However, they reacted saying that they were for research centred around the people who have Parkinson's disease, not the caretakers. We then chose to go for different associations. We found Brabantzorg<ref>Brabantzorg. (z.d.). Contact - Brabantzorg. Retrieved from https://www.brabantzorg.eu/contact/Paginas/default.aspx</ref>, but they told us they were too busy because of corona. This is also the case for an association called Careyn<ref>Careyn. (z.d.). Contact - Careyn. Retrieved from https://www.careyn.nl/contact-met-careyn/</ref>. They also informed us that they were too busy with corona. The last association we messaged was 24uurszorgsevice<ref>Brabantzorg. (z.d.). Contact - Brabantzorg. Retrieved from https://www.24uurszorgservice.nl/contact/</ref>. They haven't responded yet. | |||
In view of circumstances (the COVID-19 virus) we still send the survey to the caregivers, but bearing in mind that there was probably no response to this, because the caregivers have their hands full. Hoping that there would be a reaction, it was the intention that a thematic analysis<ref>VPPK. (2017 maart). Thematic Analysis. Retrieved from https://www.vppk.be/wp-content/uploads/2017/03/THEMATIC_ANALYSIS.pdf</ref> was carried out on the results. This allowed us to make our product even better for the users, but given that we unfortunately did not have any responses to the survey, the requirements that follow in the next section are only based on the USE analysis and thus on literature study. | |||
== Requirements == | == Requirements == | ||
The requirements follow from the user analysis. This is because the users are going to use the product and therefore the device must meet their requirements. | The requirements follow from the user analysis. This is because the users are going to use the product and therefore the device must meet their requirements. | ||
{| class="wikitable" | border="1" style="border-collapse:collapse" | {| class="wikitable" | border="1" style="border-collapse:collapse" | ||
! style="font-weight:bold"; | Requirement ID | ! style="font-weight:bold"; | Requirement ID | ||
! style="font-weight:bold"; | Technical requirement description | ! style="font-weight:bold"; | Technical requirement description | ||
|- | |||
|- | |||
|- | |- | ||
| R1 | | R1 | ||
| The | | The device must cancel out at least 60% -70% of a sudden movement caused by a tremor | ||
|- | |- | ||
| R2 | | R2 | ||
| The | | The device must be able to withstand heat flux | ||
|- | |- | ||
| R3 | | R3 | ||
| The | | The device must be able to withstand water or other liquid | ||
|- | |- | ||
| R4 | | R4 | ||
| Energy consumption should be as low as possible | | Energy consumption should be as low as possible | ||
|- | |- | ||
| R5 | | R5 | ||
| It must be a device that can be mounted on a spoon. So a separate device. | | It must be a device that can be mounted on a spoon. So a separate device. | ||
| | |- | ||
| | |||
! style="font-weight:bold"; | Functional requirement description | |||
|- | |- | ||
| R6 | | R6 | ||
| | | The device must ensure that a person with a disability in the nervous system can eat independently | ||
|- | |- | ||
| R7 | | R7 | ||
| The size of the cutlery must not be larger than a normal spoon | |||
|The | |||
|- | |- | ||
| R8 | | R8 | ||
| The weight of the spoon must not be more than that of a normal spoon | |||
|The | |||
|- | |- | ||
| R9 | | R9 | ||
| The cost of the device must not be higher than 100 euros | |||
| The device must be | |||
|- | |- | ||
| R10 | | R10 | ||
| The device should have constructive elegance | |||
| The device | |||
|- | |- | ||
| R11 | | R11 | ||
| | | The device must work for 3 hours without the need for replenishing batteries. | ||
|- | |- | ||
| R12 | | R12 | ||
| | |The device must be natural and simple to use | ||
|- | |- | ||
| R13 | | R13 | ||
| | |The device must be durable and able to withstand sustained use | ||
| | |- | ||
| R14 | |||
| The device must be able to fit on any spoon and hold it securely | |||
|- | |- | ||
| R15 | |||
| The device must be compact and streamlined | |||
|} | |} | ||
Line 422: | Line 508: | ||
'''Technical Requirement Justification''' | '''Technical Requirement Justification''' | ||
It must be measurable whether the device works or not, which is why it has been stated in the requirements that the spoon must be able to | It must be measurable whether the device works or not, which is why it has been stated in the requirements that the spoon must be able to resolve 60% to 70% of all tremor movements. In this way, it is testable whether the spoon is indeed functioning properly. The percentages come from literature studies, from similar products. This study demonstrated a 71% to 76% reduction in tremor with the ACT device on<ref name="Pathak" />. Moreover, the classical Parkinson's tremor that occurs at rest is often asymmetrical and has a distal maximum and a typical frequency of 4–6 Hz<ref> Zach, H., Dirkx, M., Bloem, B. R., & Helmich, R. C. (2015). The Clinical Evaluation of Parkinson's Tremor. Journal of Parkinson's disease, 5(3), 471–474. retrieved from: https://www.ncbi.nlm.nih.gov/pmc/articles/PMC4923747/ https://doi.org/10.3233/JPD-150650 </ref>. So to meet the requirement of 60 to 70%, 2.6 - 3.9 Hz would have to be cancelled. | ||
The product must also be able to withstand heat flux and liquid. This is because it is used when eating | The product must also be able to withstand heat flux and liquid. This is because it is used when eating hot meals. For example, think of soup, which is both liquid and hot. | ||
Another standard but important requirement is the lowest possible | Another standard but important requirement is that the product should consume the lowest energy possible, which is self-explanatory. | ||
The last technical requirement is very important. As you can read in the USE Analysis section, there are similar products that also help people with tremors to eat independently. However, their product is a spoon, fork or knife that eliminates tremors. We want to make a product that can be attached separately to a spoon, fork or knife. In this way you only have to take the small device with you and not all the adjusted cutlery. | The last technical requirement is very important. As you can read in the USE Analysis section, there are similar products that also help people with tremors to eat independently. However, their product is a spoon, fork or knife that eliminates tremors. We want to make a product that is modular, so it can be attached separately to a spoon, fork or knife. In this way, you only have to take the small device with you and not all the adjusted cutlery. | ||
Line 431: | Line 517: | ||
'''Functional Requirement Justification''' | '''Functional Requirement Justification''' | ||
The most important requirement is | Of course, The most important requirement is that the spoon must help the user to eat independently. Furthermore, there are also requirements for the weight and size of the device. This is because people with Parkinson's disease already have trouble eating, and therefore the size and weight must be kept as small and as light as possible, so as not to add any more obstacles. The price of the spoon is also important since comparable but very expensive products are already on the market. We want to develop a product that is affordable for everyone, so a requirement has been set for the price of the product. Furthermore, the device must have a constructive elegance, this requirement speaks for itself. It must look presentable, or nobody would want to use it. Another functional requirement is that the service life of the spoon should last approximately 3 hours. This is because the device must at least accompany a meal since people do not want to replace the batteries in the middle of the meal. | ||
The device should be natural to use because a lot of elderly (especially those who are not mentally healthy anymore) struggle to use new technologies. If the device is not natural and simple to use, the eating experience might only be more stressful than before. The device should be durable because it will be used multiple times per day and will be cleaned and moved all the time. Furthermore, people with tremors can accidentally drop this device on the ground and bump it around, so it should be sturdy enough to withstand all of these incidents. As already stated before, the device must be separately attached to cutlery, but it is important that it is able to grab onto (almost) all cutlery and keep it secure. This makes our product stand out as it can be applied to the already provided cutlery. The last requirement, that the device must be compact and streamlines is also important. If there are loose parts or parts sticking out, they can get stuck to the environment which stops the user from eating. Especially due to the tremors the device will move around a lot and we do not want it to get stuck to anything. | |||
== Systems for holding spoon == | |||
From the USE analysis, the requirement emerged that our product must be a device that can be attached to the spoon (or other cutlery) and that it should be a separate device. This is because it then becomes much more portable. In this way, you only have to take the small device with you and not all the adjusted cutlery. However, this requires a system that ensures that the device can be attached to any spoon (or other cutlery), regardless of its size. Research has been done into which type of system would work best for this. In this section, you can read the results of the research. | |||
There are several ways to hold the spoon in place within the tool. It should be able to tightly hold on to almost any type of spoon and should thus be able to get a grip on different kinds of handles. Some of these systems offer a part of the solution or more. | |||
'''Gripper''' | |||
One of these systems is a gripper for small parts. These grippers are made to accommodate to different kinds of weights and shapes of small objects<ref> | |||
Camillo, J. (z.d.). Grippers for Small Parts. Geraadpleegd op 23 Maart 2020, van https://www.assemblymag.com/articles/94073-grippers-for-small-parts?iframe=1 | |||
</ref>. However, these grippers are mostly designed for small and delicate parts notes Costas Charalambous :“Grippers and vacuum cups always need a light tough to properly grab small parts because they’re delicate,”. Nonetheless, these grippers could be applied to our product even if they're originally made for more delicate parts. You can see such a gripper in Figure 2. | |||
'''Vacuum Gripper with Fingers''' | |||
Another one of these systems is a vacuum gripper which you can see in Figure 3. These grippers are very useful for gripping any kind of workpieces regardless of size, material and surface. It is also very lightweight and would be ideal for our device. However, this product seems to be very expensive. As we want to develop a cheap solution we will not be able to use this system, as one of our requirements mentions that the costs should be as low as possible. | |||
'''Vacuum Gripper wrapped around''' | |||
The third system is similar to the vacuum system, but replaces the "fingers" with a material that wrappes around the object and holds it. It is demonstrated in Figure 4. This material can meld to any shape upon contact with the object<ref>Wevolver | Knowledge shared by technology developers and scientists. (z.d.). Retrieved from https://www.wevolver.com/wevolver.staff/universal.robotic.gripper/</ref>. This system reduces the amount of parts that have to be controlled and can thus be more reliable and cheap. | |||
<div style="display: inline; width:1200px; float: right;"> | |||
<div style="display: inline; width:400px; float: left;"> | |||
[[File:gripper.jpg|200px|thumb|''Figure 2: Gripper system for small parts'']] | |||
</div> | |||
<div style="display: inline; width:400px; float: right;">[[File:material.png|300px|thumb|left|''Figure 4: Material that wrapped around the object'']] | |||
</div> | |||
<div style="display: inline; width:300px; float: right;">[[File:vacuum.png|200px|thumb|left|''Figure 3: Vacuum gripper system'']] | |||
</div> | |||
</div> | |||
<br><br><br><br><br><br><br><br><br><br><br><br><br><br> | |||
This research was important to realise what systems exist right now. However, we also found out that these systems are not applicable for our product. These systems are indeed very accurate and useful, but as we stated before, we want a affordable product. This means that we cannot use these systems. The attachment system we ended up using is very simple and described in the 3D printing section. | |||
== 3D printing == | |||
To make the case for all the electronics, we decided to use 3D printing to our advantage. However, before we can print something, we first need to draw the case. For this we decided to use Solidwork. With this program we are able to accurately draw a case since Solidwork makes it very easy to draw shapes with precise lengths. Solidwork also allows for easy fixes since if you change the length of one part Solidwork changes the other parts to fit this change. | |||
'''Holding the spoon''' | |||
[[file:screwKey.jpg|thumb|100px|''Figure 5: Screw key to make turning easier'']] | |||
The first step in designing the case is finding a way to hold most spoons without damaging it. Since we want our design to work for many different spoons, and every spoon has a different handle design, we needed to find a cheap way in which we could attach all spoons to our design. We decided to make a tube to put the spoon into, and then secure the spoon with a screw. To prevent damage to the spoon a piece of rubber can be added to the screw, however even without the rubber we did not damage the spoon by jamming it. To make it easier to turn the screw we could also add an attachment to the screw which you can easily turn, which would look like the one in Figure 5. Another problem was that it could be difficult to get the spoon in the center of the holder. To make this easy we made a V shape in the back of the holder which moves the back of the spoon to the center of the holder, shown in Figure 7. | |||
<div style="display: inline; width:1200px; float: right;"> | |||
<div style="display: inline; width:550px; float: left;"> | |||
[[File:holder.png|300px|thumb|''Figure 6: 3D drawing of holder '']] | |||
</div> | |||
<div style="display: inline; width:600px; float: right;">[[File:vInside.png|250px|thumb|left|''Figure 7: v shape inside holder to center the spoon'']] | |||
</div> | |||
</div> | |||
{{break}} | |||
{{break}} | |||
<br> | |||
'''Place servo's''' | |||
[[File:connection.png|300px|thumb|''Figure 8: connection piece'']] | |||
The second step in our design was to find a place for the servos. We could not just attach both servos to the handle and the holder, since then the holder would have two attachment points with the handle and would not be able to turn. We thus needed to either first correct the pitch or the roll axis relative to the handle. If we tried to correct the pitch axis before the roll axis, we would need to attach the pitch servo to the handle, then attach the roll servo to the pitch servo, and lastly attach the holder to the roll servo. This would however not be possible since rotating the handle around the roll axis would change the axis the pitch servo would correct in. Thus we first needed to correct the roll axis and then correct the pitch axis. We had to attach a handle to the roll servo, attach the roll servo to the pitch servo and finally connect the pitch servo to the holder. The roll servo needs to be behind the spoon in order to turn around the spoons roll axis, the pitch servo needs to be to the side of the spoon. Thus to be able to attach the roll servo to the pitch servo we need to make a connection piece. This connection piece needs to move from the side of the holder to the back of the holder while giving the holder enough space to turn along the pitch axis. The pitch servo needs to be attached to the connection on the body itself, while the roll servo needs to be connected to the connection with the feet of the servo. | |||
'''The handle''' | |||
Finally, we need to design a handle to hold the device with. This handle needs to be attached to the body of the roll servo, and have enough room inside it for the rest of the electronics. Because all the electronics need to be in the handle we also needed a way to open and close the handle. We decided to make the handle in two pieces, which we can attach together with screws. This also allows us to easily open the handle to replace batteries or remove broken electronics. Since one of the servos is outside the handle we needed a way for the cable to get inside the handle. In order to do this, we made a little cut in the side of one of the parts of the handle. With all the electronics that need to fit in the handle, the handle is bigger than we would have liked. This could be solved by using electronics particularly developed for this product, such that the shapes of the electronics allow for a more compact design. | |||
<div style="display: inline; width:1200px; float: right;"> | |||
<div style="display: inline; width:400px; float: left;"> | |||
[[File:handleSide1.png|240px|thumb|''Figure 9: part 1 of the handle with servo hole'']] | |||
</div> | |||
<div style="display: inline; width:300px; float: right;">[[File:assemble.png|280px|thumb|left|''Figure 11: Placement of the parts without electronics'']] | |||
</div> | |||
<div style="display: inline; width:400px; float: right;">[[File:handleSide2.png|300px|thumb|left|''Figure 10: part 2 of the handle with cable hole'']] | |||
</div> | |||
</div> | |||
<br><br><br><br><br><br><br><br><br><br><br><br><br><br> | |||
'''The results''' | |||
Below the printed results can be seen. The idea was to use the 3D printed case in the prototype, but because of the COVID-19 outbreak, we were unable to put the electronics together with the 3D printed component. This means that all these pictures are without most of the electronics. Since the servos used in the pictures are borrowed, we were unable to connect them to the parts thus in Figure 12 a notebook was put under the spoon in order to get the spoon on the correct height such that it looked like the product is fully attached. | |||
<div style="display: inline; width:1200px; float: right;"> | |||
<div style="display: inline; width:400px; float: left;"> | |||
[[File:3DPrintFull.jpeg|345px| thumb |''Figure 12: Prototype without electronics'']] | |||
</div> | |||
<div style="display: inline; width:300px; float: right;">[[File:handleRoom.jpeg|300px | thumb | left | ''Figure 14: Inside of the handle'']] | |||
</div> | |||
<div style="display: inline; width:400px; float: right;">[[File:servoConnection.jpeg|300px | thumb | left | ''Figure 13: Connection piece with servo's'']] | |||
</div> | |||
</div> | |||
== Prototype == | |||
===Circuit=== | |||
To get an idea of how such a spoon would work, we started with a very simple prototype in week 3. This prototype works with the active force method. The prototype will first be focused on spoons, since not all cutlery (spoons, forks and knives) have to be stabilized in the same way. Two servos will be used to compensate movements on the pitch and roll axis of rotation ([https://en.wikipedia.org/wiki/Six_degrees_of_freedom#/media/File:6DOF.svg]). A picture showing a graphical representation of the pitch, roll and yaw axes can be seen in Figure 16 in the section Design Choices, further on in the wiki. The movement of the spoon will be measured by an MPU6500 accelerometer. The servos and sensor will be attached to a Digispark Attiny85 microcontroller. 4 AAA batteries will be used to power the circuit. The prototype works with a PID controller by inducing a force opposite of the measured acceleration, which then aims to bring the spoon to the reference position. The connection of these components can be seen in the following Figure: | |||
[[File:Circuitstabilizingspoon.PNG|thumb|center|600px|''Figure 15: Circuit for Prototype'']] | |||
== | === Arduino code === | ||
'''Active force method''' | |||
The Arduino code for the very first prototype without PID controller is shown below. | |||
[[Arduino code 1]] | |||
'''Prototype with PID controller''' | |||
The Arduino code for the prototype with the PID controller can be seen below. Some comments have been added to explain the code. | |||
[[Arduino code 2]] | |||
=== Design Choices === | |||
'''Stabilizing two or three axes?''' | |||
How many axes the spoon should stabilize is a question that quickly came up. We use the pitch, roll and yaw axes that are usually used in planes. These axes are also frequently mentioned in literature and they are perfect for the stabilization of the spoon. Figure 16 below shows these axes for clarity. It is obvious that the pitch and roll axes are necessary to stabilize, to make sure that food doesn’t fall off the spoon. However, the question arose whether the yaw axis is necessary, helpful, or completely useless. Below some of the arguments for and against using 3 axes instead of 2 are outlined. | |||
[[File:Aircraft axes.jpg|thumb|center|300px|x350px|Figure 16: The roll, pitch and yaw axes, displayed from the viewpoint of an aircraft<ref>Roll, Pitch and Yaw, How things Fly. https://howthingsfly.si.edu/flight-dynamics/roll-pitch-and-yaw</ref>]] | |||
The main argument for only stabilizing two axes is that the yaw axis simply doesn’t have to be stabilized. The movement in the same plane as the spoon (the yaw axis) would not contribute to many difficulties with eating. If this axis were to be stabilized, you even run the risk of stabilizing voluntary motions. Another argument for not using 3 motors is that it would make our design bulkier. It is critical that the stabilizing mechanism is as small and light as possible for ease of use, shown and discussed in our requirements of the product. | |||
'''Type of controller''' | |||
The type of controller that the self-stabilizing spoon will use has also been a big decision point. A few of the popular control mechanisms have been described in the State of the Art, for example using the Active Force Method or a PID controller. Ultimately we settled on using a PID controller with the stabilizing mechanism consisting of two motors that supply a force against the tremor direction, thus keeping the spoon level. | |||
We already had a preference for a PID controller after we saw that many studies in the literature were also using them for prototypes and initial designs for self-stabilizing devices. A few of us already have experience with PID controller so it would take less time to set up. We do realize that PID controllers are outdated in the sense that the technology is pretty old, but for the sake of building an initial prototype in the limited timeframe that we had in this course (8 weeks) we think this is a good stepping stone for the prototype, which could be improved further with state of the art technology if this product is further worked out. | |||
'''Choice of components''' | |||
The individual physical components for the first prototype have been chosen with the following things in mind. First is the compatibility. The component must do what it is expected to do (shown in the circuit and description above) and have enough strength to fulfill the tasks (e.g. the servos). Second is the size of the component. As mentioned in the requirements, the total device should be as small and light as possible, in order to make it as comfortable and easy to use. The last important property of the component that was looked at is the price. Again the requirements mention the price should be as low as possible because many comparable but way more expensive products are already on the market. | |||
===The First Prototype: Proof of Concept=== | |||
The initial prototype has been made in week 3. The goal of this test is to see whether our ideas about stabilizing the spoons actually work. Figure 17 below shows this initial prototype. The initial prototype consists of the Inertial Measurement unit, one servo motor and a spoon, all connected to the Arduino. The code that is used is the first one shown in the section Arduino code. Even though this code is written for two motors, it still works for any set-up with one motor as well. So now we have only one sensor present, but we see that when the sensor and motor with spoon attached are rotated in the pitch direction, the spoon keeps stays level. From this we conclude that the proof of concept is a success and from here we integrated the other components into the final prototype. | |||
[[File:Prototype.png|280px|thumb|center|''Figure 17: First Prototype: only pitch axis stabilized'']] | |||
===The Process=== | |||
After typing a few keywords in Google it seemed like making the prototype wouldn’t be a particularly hard task. There are lots of examples of people who made something like we are attempting<ref> https://create.arduino.cc/projecthub/RupinC/assistive-spoon-for-patients-with-parkinson-s-3628b6 </ref><ref>https://www.instructables.com/id/Gyro-Stabilizer-W-Arduino-and-Servo/</ref><ref>https://howtomechatronics.com/projects/diy-arduino-gimbal-self-stabilizing-platform/</ref>. The first approach was to write our own PID controller based on the codes used in these projects and the help from the examples in the Arduino PID library <ref>https://playground.arduino.cc/Code/PIDLibrary/</ref>. After that the idea was to improve the controller in order to get the desired stabilization. | |||
Although, in the end, this first approach is more or less what we did to achieve the final controller, there have been a few bumps in the road. The coronavirus had a big impact on the process, this impact was direct as well as indirect. | |||
'''Lack of testing equipment''' | |||
For the first prototype we borrowed the needed materials from the department Electrical Engineering, some friends and we used some of our own. While researching the components, we focused on everything that would actually be in the final product. This included the Digispark Attiny85 microcontroller, which does not have serial communication. In the Arduino code, this means that every Serial.print() statement does not do anything and therefore it is hard to detect bugs in the code. We knew this beforehand and planned on borrowing the Arduino Uno again, but this was not possible due to the coronavirus. Therefore, we had to revise what we needed and ordered an Arduino Uno, a breadboard and extra wires. | |||
'''Ordering late''' | |||
Before ordering the components, we had to contact Lambèr Royakkers, who sent us to the Mechanical Engineering workshop to ask if they already had the things that we needed in their possession. The workshop was closed due to the coronavirus and we had to order them ourselves. Together with having to reorder, this process costed us a week of our valuable time. | |||
'''MPU6500''' | |||
[[File:WhatsApp Image 2020-04-02 at 22.35.06.jpeg|thumb|300px|''Figure 18: Arduino circuit realisation'']] | |||
The sensor that we wanted to use, the MPU6050, was sold out when we ordered our components. However, a seemingly similar one was available, the MPU6500. Time pressure and inexperience made us decide to go for this sensor. Not knowing that it meant that it was not possible to use the example projects mentioned above. These Arduino codes use so called ‘libraries’, which are sets of functions written by experienced programmers. The MPU6050 is widely used and there are lot of different libraries available. The Arduino examples above don’t even use the same ones. | |||
The MPU6500 is less popular and there were no examples within the scope of our project available. There was a library available that made it possible to read the values of the sensor<ref>https://github.com/rpicopter/ArduinoMotionSensorExample</ref>. Having values and getting the right values out of a PID controller turned out to be two completely different things and after spending a day working on this without result, we tried another approach. Until this moment a combination of three existing projects was used instead of recreating one of the three. The new plan was to use the MPU6500 with the Gyro stabilizer from instructables. This ended up in deep research into Arduino communication, I2C protocols and sensor addresses, where it felt like every answer raised two new questions. | |||
Although this research was very interesting and it gave useful insights in how Arduino’s work, this level of programming was not going to bring us closer to a self-stabilizing spoon. It would need an advanced Arduino user or a lot more time adjust libraries in a way that would work for us. In the meantime the MPU6050 sensor was available again so we decided to order it so we could test the existing Arduino codes and finalize our own PID controller. | |||
'''The final week''' | |||
The MPU6050 surely made everything a lot easier. The ‘instructables’ code worked somewhat, but a lot less stable than in the corresponding video. The spoon tended to start vibrating instead of stabilizing after fast movements and after about 30 seconds it stopped working until the reset button was pressed. After this it was time to test and tune our own PID controller. | |||
'''Indirect impact''' | |||
Due to the coronavirus only one of us was working on the electronics part alone. Indirect this is also a reason that everything took a lot longer than expected. If we could meet it would have been a lot easier to work together on programming and assembling everything, even if it is with group members that have no experience at all. Another advantage of working at the university would be the possibility to ask help from other students and helpdesks/workshops. Having someone taking a fresh look at a project can sometimes save a lot of time debugging, especially when there is just a wire connected wrongly. | |||
=== The Final Prototype === | |||
The prototype consists of two parts, the internal electronics and the 3D-printed design. Due to the coronacrisis it was not possible to meet in order to put everything together. In an ideal situation the electronics would have been soldered on a protoboard that fits into the grip of the 3D-printed case. Unfortunately this was not possible because the needed soldering equipment for soldering such precision is only available on the university. | |||
Since there is no fitting case, the electronics are taped together, which makes the system much less stable. The sensor is taped to the ‘roll’ sensor; therefore this movement is much more accurate than the ‘pitch’ sensor. With the 3D-printed case this won’t be this way. | |||
<div style="display: inline; width:1200px; float: right;"> | |||
<div style="display: inline; width:550px; float: left;"> | |||
[[File:3DPrintFull.jpeg|400px|thumb|''Figure 19: 3D case prototype '']] | |||
</div> | |||
<div style="display: inline; width:600px; float: right;">[[File:WhatsApp Image 2020-04-02 at 22.35.06 (1).jpeg|420px|thumb|left|''Figure 20: Final prototype (without 3D case)'']] | |||
</div> | |||
</div> | |||
{{break}} | |||
{{break}} | |||
<br> | |||
===Bill of Materials=== | |||
{| border=1 style="border-collapse: collapse;" | |||
! style = "width: 12em;" |Product | |||
! style = "width: 4em;" |Costs | |||
! style = "width: 58em;" |Link | |||
|- style="text-align: center; height: 2em;" | |||
| Attiny85 Microcontroller || €5.00 || https://www.tinytronics.nl/shop/nl/arduino/main-boards/digispark-attiny85-met-micro-usb | |||
|- style="text-align: center" | |||
| 2x Sg90 Servo || €8.00 || https://www.tinytronics.nl/shop/nl/robotica/motoren/motor/sg90-mini-servo | |||
|- style="text-align: center; height: 2em;" | |||
| MPU6050 accelerometer || €5.00 || https://www.tinytronics.nl/shop/nl/sensoren/accelerometer-gyro/mpu-6050-accelerometer-en-gyroscope-3-axis-module-3.3v-5v | |||
|- style="text-align: center" | |||
| Printplaat || €0.80 || https://www.tinytronics.nl/shop/nl/prototyping/printplaten/experimenteer-printplaat-5cm*7cm-dubbelzijdig | |||
|- style="text-align: center; height: 2em;" | |||
| Behuizing (3D print) || ~€2 || - | |||
|- style="text-align: center; height: 2em;" | |||
| 2x AAA battery holders || €1.60 || https://www.tinytronics.nl/shop/nl/batterij-en-accu/batterijhouders/2x-cr2032-lir2032-batterij-houder-met-losse-draden | |||
|- style="text-align: center; height: 2em;" | |||
| 4x AAA chargeable batteries || €7.00 || https://www.tinytronics.nl/shop/nl/batterij-en-accu/aaa/eneloop-oplaadbare-batterij-4x-aaa-750mah | |||
|- style="text-align: center; height: 2em;" | |||
| Wires || €4.00 || https://www.tinytronics.nl/shop/nl/kabels/prototype-draden/breadboard-draden-140-stuks-verschillende-maten-in-doosje | |||
|- style = "height: 1px"; | |||
| || || | |||
|- style = "background: #CEE0F2; text-align: center; height: 2em;" | |||
| Total Cost || €33.40 ||- | |||
|- style = "height: 1px"; | |||
| || || | |||
|- style = "text-align: center; height: 2em;" | |||
| UNO R3|| €11.50 || https://www.tinytronics.nl/shop/nl/arduino/main-boards/uno-r3-met-usb-kabel | |||
|- style = "text-align: center; height: 2em;" | |||
| Desoldering braids || €1.50 || https://www.tinytronics.nl/shop/nl/prototyping/solderen/desoldeerlint-1mm-1.5m | |||
|- style = "text-align: center; height: 2em;" | |||
| Breadboard || €4.00 || https://www.tinytronics.nl/shop/nl/prototyping/breadboards/breadboard-830-points | |||
|- style = "text-align: center; height: 2em;" | |||
| MPU6500 accelerometer || €5.00 || https://www.tinytronics.nl/shop/nl/sensoren/accelerometer-gyro/mpu-6500-accelerometer-gyroscope-6dof-module-3.3v-5v | |||
|- style = "text-align: center; height: 2em;" | |||
| Shipping cost || €7.50 || - | |||
|} | |||
All materials used in our product are listed above the double line, while under the double lines we listed all the materials we had to use in order to create our product | |||
== Efficiency of Performance / Testing the Prototype == | |||
Test methods must be developed to test whether the prototype meets the requirements and to see whether it works well enough. Two methods have been devised to measure the efficiency of the performance of the prototype. The first test is practical and therefore technical and the second method is based on theory. | |||
'''Technical''' | |||
Method 1. | |||
In the requirements, it has been explained that a typical tremor has a frequency of 4–6 Hz. We have also made the requirement that 60 to 70 percent of the tremor must be compensated. This resulted in that 2.6 - 3.9 Hz would have to be cancelled. And so that when the spoon is working, there is only a frequency of 1.4 - 2.1 Hz. If this is indeed the case, then it can be concluded that the spoon works well enough in this respect. | |||
Method 2. In another study, they also tested a Parkinson's spoon. There they took advantage of the decrease in amplitude. If the amplitude of the movements decreased significantly when the spoon was on as compared to off, the test was successful and it was concluded that the function of the spoon was meaningful<ref name="Pathak" />. This is also a method on which we will test the efficiency of the spoon. | |||
Method 3. The purpose of the spoon is that as much food as possible remains on the spoon and is therefore not fallen off during a tremor. So what matters in the end, is what percentage of the food remains on the spoon when the stabilizing system is on as compared to when it is turned off. If this percentage is significantly more, it can be concluded that the purpose of the spoon has been achieved and so a conclusion can be drawn about the efficiency of the spoon. | |||
''' | |||
'''Theoretical''' | |||
Then there is also a method to test the Parkinson Spoon theoretically. This is done through a follow-up survey to the first survey. In this survey, it is first explained what our product exactly is and then questions are asked whether the caregivers think that this product can work. It can be a survey for many caregivers or an interview is conducted with one of the caregivers. The questions we want to ask in the survey/interview can be read in this link: [https://docs.google.com/forms/d/e/1FAIpQLSdJ-8iwV9Se4oQi3CIAKBsOPk1voeyoFTL4zOGBAmYWDUKtuA/viewform?usp=sf_link Survey 2]. | |||
'''Conclusion Efficiency of Performance''' | |||
Due to the lack of time, explained in The Process, it was not possible to actually test the performance of the device. | |||
So unfortunately, we were no longer able to test our prototype. To still evaluate if the prototype is usable we looked at how many requirements the prototype meets. Here you can see the set requirements again. The following requirements have been achieved: | |||
{| class="wikitable" | border="1" style="border-collapse:collapse" | |||
! style="font-weight:bold"; | Requirement ID | |||
! style="font-weight:bold"; | Technical requirement description | |||
|- | |||
|- | |||
| R1 | |||
| The device must cancel out at least 60% -70% of a sudden movement caused by a tremor | |||
|- | |||
|- style = "background: #90EE90" | |||
| R2 | |||
| The device must be able to withstand heat flux | |||
|- | |||
|- style = "background: #90EE90" | |||
| R3 | |||
| The device must be able to withstand water or other liquid | |||
|- | |||
| R4 | |||
| Energy consumption should be as low as possible | |||
|- | |||
|- style = "background: #90EE90" | |||
| R5 | |||
| It must be a device that can be mounted on a spoon. So a separate device. | |||
|- | |||
| | |||
! style="font-weight:bold"; | Functional requirement description | |||
|- | |||
|- style = "background: #90EE90" | |||
| R6 | |||
| The device must ensure that a person with a disability in the nervous system can eat independently | |||
|- | |||
| R7 | |||
| The size of the cutlery must not be larger than a normal spoon | |||
|- | |||
|- style = "background: #90EE90" | |||
| R8 | |||
| The weight of the spoon must not be more than that from a normal spoon | |||
|- | |||
|- style = "background: #90EE90" | |||
| R9 | |||
| The cost of the device must not be higher than 100 euro | |||
|- | |||
|- style = "background: #90EE90" | |||
| R10 | |||
| The device should have constructive elegance | |||
|- | |||
| R11 | |||
| The device must work for 3 hours without the need for replenishing batteries. | |||
|- | |||
|- style = "background: #90EE90" | |||
| R12 | |||
|The device must be natural and simple to use | |||
|- | |||
| R13 | |||
|The device must be durable and able to withstand longer use | |||
|- | |||
|- style = "background: #90EE90" | |||
| R14 | |||
| The device must be able to fit on any spoon and hold it securely | |||
|- | |||
|- style = "background: #90EE90" | |||
| R15 | |||
| The device must be compact and streamlined | |||
|} | |||
The requirements which are met, are colored green above. As can be seen in the table above, 10 out of the 15 requirements are met. Some of the requirements that were not met, were not met because we were unable to do the tests and therefore cannot conclude whether they have been met. These could therefore be checked off later, if the tests on the prototype are done in the future. So a very large part of the requirements have been met and we can therefore say that the prototype is successful. | |||
== Future Improvements/Research/Developments == | |||
This section deals with the improvements that could be made after this project is done. The reasons for not including these in the main project are the limited timeframe of this project and the coronavirus, limiting our USE implementation. Below the areas in which either the USE aspects can be implemented and the technical design can be improved are highlighted. | |||
'''USE survey''' | |||
It has already been described that the survey that has been made for this project has not been able to be used, due to the coronavirus. Understandably caregivers and institutions did not have time to answer our questions in order to improve the USE aspects of our design and product. Carrying out another survey now that a prototype has been made could even be more beneficial, as you can give the caregivers a better idea of our product, giving us better answers to implement these design changes and improving the design for the end-user. A themed analysis would be carried out to analyse the data that is received from the survey, which in turn we can use to improve the design. | |||
'''User testing''' | |||
In this project, we have regrettably not done a user testing session with an actual Parkinson's patient. However, this is certainly something that we would consider if we had more time. A type of session where we simply tell a patient to use our device and observe what some of the difficulties (and good parts!) of our design can make us aware of issues that we didn't even think about before, simply because we don't deal with the problems ourselves. There are different ways to go about this. You could just observe like just described and use your knowledge about the subject together with the user's experience. Including a survey or some type of review session with the user can give more insight into specific problems that are not visible to an observer. | |||
'''Hardware improvements''' | |||
One of the areas in which the prototype can be improved a lot is the hardware that is used. Currently, it uses cheap commonplace components that are not ideal for example considering the size of the components, as we want the product to be the least bulky it can be. The servo motors take up quite a lot of space. The current servo that is used twice is the SG90 mini servo (link in the Bill of Materials) which has dimensions of 23x12.2x29 mm. The smallest component that is sold normally is the Power HD Sub-Micro Servo HD-1440A servo, with dimensions 20.2x20.2x8.5 mm, which is less than half of the volume than the ones we used<ref> Power HD Sub-Micro Servo HD-1440A servo. retrieved from: https://www.pololu.com/product/1040/specs</ref>. This means that two of these servos would still be smaller (in volume) then 1 SG90 servo. This servo does cost a little more but this is not very significant (5.43 vs 4.00 euros) Similar to this arguably better components can be found for the other parts as well. Another example of this is the microcontroller. A microcontroller developed by InvenSense has dimensions 3x3x0.9 mm which is extremely small compared to the one that we used<ref> Invensense MPU-6500. Retrieved from: https://invensense.tdk.com/products/motion-tracking/6-axis/mpu-6500/ </ref>. | |||
Of course, the parts that we used for the prototype, as well as the parts that are researched parts, are freely available for purchase for any non-specific use. This means that if parts were to be constructed by ourselves if we had the knowledge to do so, they would be specifically made with the product specifications and preferences in mind. This means that the size, power, weight, etc. can be optimized, which would make a big difference if this product would be produced and put for sale for consumers worldwide. | |||
'''Software Improvements''' | |||
Currently, the prototype uses a PID controller. It is evident that the PID controller is not state of the art anymore as it is quite old. One literature source talks about how PID controllers are simple compared to other solutions and can be integrated into almost any system together with the robustness properties that ensure stability and high performance under changes of the parameters.<ref> Kozak, Š.Kozák. (2014). State-of-the-art in Control Engineering. Journal of Electrical Systems and Information Technology. 1. 1–9. https://doi.org/10.1016/j.jesit.2014.03.002</ref>. There are other alternatives such as the Field Programmable Gate Array (FPGA) and more predictive instead of reactive control systems. Because the PID controller is purely reactive it could be interesting to look into more predictive methods of stabilization in possible future research. | |||
== Conclusion == | |||
The problem addressed during this project is the fact that people with a nervous disorder, specifically Parkinson's disease and essential tremors, have much more trouble with daily tasks than healthy people. We have focussed on the need for help of this target group during meals, because they have trouble with something as simple as bringing a spoon to their mouth. This means that their meals take a lot longer and they often have to be assisted while eating. | |||
To give these people more freedom, self-esteem and independence, we have developed a device that can stabilize a spoon or other cutlery while eating with a tremor. Research has shown that there are already similar products on the market, but these prove to be large, expensive and inconvenient to transport when eating out. That is why we were convinced that we could improve the current products on the market by making an affordable and small device that can be mounted on a regular spoon. | |||
In the past seven weeks we have been busy realizing the prototype described above. In the wiki page, the process and the choices made, can be read. Unfortunately, the final prototype has not been tested, as can be read in the results section, due to the COVID-19 conditions which caused that only one of the group members could work on the prototype hardware and software. It is therefore impossible to draw a real conclusion on whether our product is the solution for the problem mentioned. | |||
To be able to say something about the quality of the solution to the problem, we looked at how many requirements were met in the final prototype. This turned out to be at least 10/15, of which some of the unfulfilled requirements were not met because they simply have not been tested. So, in conclusion, at least 10 and maybe after tests have been done in the future more than 10, of the 15 requirements have been met. With the future improvements in mind, it can be concluded that the prototype is a great starting point for a product that later can be used to solve this problem. | |||
== Literature Study week 1 == | |||
At least 25 pieces of literature have been found in the field of the problem statement in week 1. They have been collected, sorted into categories and a short summary per article has been written. | |||
=== Similar products === | === Similar products === | ||
Line 507: | Line 920: | ||
''A proposal for a wearable auto stabilizing cup holder that helps in routine performance tasks such as drinking water. The system uses IMU sensors and actuators for stabilizing the cup when under severe hand vibration.'' | ''A proposal for a wearable auto stabilizing cup holder that helps in routine performance tasks such as drinking water. The system uses IMU sensors and actuators for stabilizing the cup when under severe hand vibration.'' | ||
[6] Turgeon, P., Laliberte, T., Routhier, F., Campeau-Lecours, A. Preliminary design of an active stabilization assistive eating device for people living with movement disorders(2019) IEEE International Conference on Rehabilitation Robotics, 2019-June, art. no. 8779388, pp. 217-223. | [6] Turgeon, P., Laliberte, T., Routhier, F., Campeau-Lecours, A. Preliminary design of an active stabilization assistive eating device for people living with movement disorders(2019) IEEE International Conference on Rehabilitation Robotics, 2019-June, art. no. 8779388, pp. 217-223. https://doi.org/10.1109/ICORR.2019.8779388 | ||
''A preliminary design for a stabilizing eating device. It includes mechanical design, damping arrangement, electronic design and control algorithms.'' | ''A preliminary design for a stabilizing eating device. It includes mechanical design, damping arrangement, electronic design and control algorithms.'' | ||
Line 515: | Line 928: | ||
[7] McGruder, J., Cors, D., Tiernan, A. M., & Tomlin, G. (2003). Weighted Wrist Cuffs for Tremor Reduction During Eating in Adults With Static Brain Lesions. American Journal of Occupational Therapy, 57(5), 507–516. https://doi.org/10.5014/ajot.57.5.507 | [7] McGruder, J., Cors, D., Tiernan, A. M., & Tomlin, G. (2003). Weighted Wrist Cuffs for Tremor Reduction During Eating in Adults With Static Brain Lesions. American Journal of Occupational Therapy, 57(5), 507–516. https://doi.org/10.5014/ajot.57.5.507 | ||
''Research on the usage of weights on the forearm. Research shows that making the wrist heavier resulted in | ''Research on the usage of weights on the forearm. Research shows that making the wrist heavier resulted in fewer tremors while self-feeding for some individuals.'' | ||
[8] Meshack, R. P., & Norman, K. E. (2002). A randomized controlled trial of the effects of weights on amplitude and frequency of postural hand | [8] Meshack, R. P., & Norman, K. E. (2002). A randomized controlled trial of the effects of weights on amplitude and frequency of postural hand tremors in people with Parkinson’s disease. Clinical Rehabilitation, 16(5), 481–492. https://doi.org/10.1191/0269215502cr521oa | ||
''Again research on weighted utensils for patient suffering from Parkinson’s Disease. This time no support for significant effect on reduction of the tremor.'' | ''Again research on weighted utensils for patient suffering from Parkinson’s Disease. This time no support for a significant effect on reduction of the tremor.'' | ||
[9] Matsumoto, Y., Seki, M., Ando, T., Kobayashi, Y., Nakashima, Y., Iijima, H., … Fujie, M. G. (2013). Development of an Exoskeleton to Support Eating Movements in Patients with Essential Tremor. Journal of Robotics and Mechatronics, 25(6), 949–958. https://doi.org/10.20965/jrm.2013.p0949 | [9] Matsumoto, Y., Seki, M., Ando, T., Kobayashi, Y., Nakashima, Y., Iijima, H., … Fujie, M. G. (2013). Development of an Exoskeleton to Support Eating Movements in Patients with Essential Tremor. Journal of Robotics and Mechatronics, 25(6), 949–958. https://doi.org/10.20965/jrm.2013.p0949 | ||
Line 525: | Line 938: | ||
''Usage of exoskeleton to suppress tremors and support voluntary movement. The research shows that the exoskeleton works to a certain extent.'' | ''Usage of exoskeleton to suppress tremors and support voluntary movement. The research shows that the exoskeleton works to a certain extent.'' | ||
[10] Song, C., Gehlbach, P. L., & Kang, J. U. (2012). Active tremor cancellation by a “Smart” handheld vitreoretinal microsurgical tool using swept source optical coherence tomography. Optics Express, 20(21), 23414. https://doi.org/10.1364/oe.20.023414 | [10] Song, C., Gehlbach, P. L., & Kang, J. U. (2012). Active tremor cancellation by a “Smart” handheld vitreoretinal microsurgical tool using swept-source optical coherence tomography. Optics Express, 20(21), 23414. https://doi.org/10.1364/oe.20.023414 | ||
''In the medical world are tremors also an obstacle, especially for microsurgeons. The device helps steady the surgeon tool by | ''In the medical world are tremors also an obstacle, especially for microsurgeons. The device helps steady the surgeon tool by canceling the tremors. This could also be applied to our subject.'' | ||
[11] Ma, H.-I., Hwang, W.-J., Chen-Sea, M.-J., & Sheu, C.-F. (2008). Handle size as a task constraint in spoon-use movement in patients | [11] Ma, H.-I., Hwang, W.-J., Chen-Sea, M.-J., & Sheu, C.-F. (2008). Handle size as a task constraint in spoon-use movement in patients with Parkinson’s disease. Clinical Rehabilitation, 22(6), 520–528. https://doi.org/10.1177/0269215507086181 | ||
''Research on the effect of the size of a spoon handle on the amount of tremors that a Parkinson’s Disease patient is experiencing. The results show that a smaller to medium sized spoon handle caused a faster and smoother movement compared to a big handle.'' | ''Research on the effect of the size of a spoon handle on the amount of tremors that a Parkinson’s Disease patient is experiencing. The results show that a smaller to medium sized spoon handle caused a faster and smoother movement compared to a big handle.'' | ||
Line 535: | Line 948: | ||
[12] Hamdy, A. (1999). Active damping of vibrations in elevator cars. Journal of Structural Control, 6(1), 53–100. https://doi.org/10.1002/stc.4300060105 | [12] Hamdy, A. (1999). Active damping of vibrations in elevator cars. Journal of Structural Control, 6(1), 53–100. https://doi.org/10.1002/stc.4300060105 | ||
''Usage of active damping system for cars. | ''Usage of active damping system for cars. It doesn’t apply perfectly to the spoon but shows how a system can actively reduce the extremes.'' | ||
[13] Chuanasa, J., & Songschon, S. (2014). Essential tremor suppression by a novel self-balancing device. Prosthetics and Orthotics International, 39(3), 219–225. https://doi.org/10.1177/0309364614525185 | [13] Chuanasa, J., & Songschon, S. (2014). Essential tremor suppression by a novel self-balancing device. Prosthetics and Orthotics International, 39(3), 219–225. https://doi.org/10.1177/0309364614525185 | ||
Line 549: | Line 962: | ||
''The paper proposes a new AFC (active force control) method for tremor attentuation, using a three-degree-of-freedom musculoskeletal model. Matlab is used to analyze the model. Conclusion: AFC-based system with a piezoelectric actuator and a PD controller is very effective is suppressing the human hand tremor.'' | ''The paper proposes a new AFC (active force control) method for tremor attentuation, using a three-degree-of-freedom musculoskeletal model. Matlab is used to analyze the model. Conclusion: AFC-based system with a piezoelectric actuator and a PD controller is very effective is suppressing the human hand tremor.'' | ||
[16] Vidya, V., Poornachandran, P., Sujadevi, V.G., Dharmana, M.M.Suppressing Parkinson's diseases induced involuntary movements using wearables(2018) Proceedings of 2017 IEEE International Conference on Technological Advancements in Power and Energy: Exploring Energy Solutions for an Intelligent Power Grid, TAP Energy 2017, pp. 1-4. | [16] Vidya, V., Poornachandran, P., Sujadevi, V.G., Dharmana, M.M.Suppressing Parkinson's diseases induced involuntary movements using wearables(2018) Proceedings of 2017 IEEE International Conference on Technological Advancements in Power and Energy: Exploring Energy Solutions for an Intelligent Power Grid, TAP Energy 2017, pp. 1-4. https://doi.org/10.1109/TAPENERGY.2017.8397267 | ||
''This paper proposes and implements a low-cost wearable assistive device for Parkinson’s disease patients. A coin vibrator motor a micro controller are used. The induced vibration on the wrist distracts the patient’s brain from the bio-mechanical feedback loop with the hand and reduces the tremor and improving the ability to grip or hold an object.'' | ''This paper proposes and implements a low-cost wearable assistive device for Parkinson’s disease patients. A coin vibrator motor a micro controller are used. The induced vibration on the wrist distracts the patient’s brain from the bio-mechanical feedback loop with the hand and reduces the tremor and improving the ability to grip or hold an object.'' | ||
[17] Gallego, J.A., Rocon, E., Belda-Lois, J.M., Pons, J.L. A neuroprosthesis for tremor management through the control of muscle co-contraction (2013) Journal of NeuroEngineering and Rehabilitation, 10 (1), art. no. 36. | [17] Gallego, J.A., Rocon, E., Belda-Lois, J.M., Pons, J.L. A neuroprosthesis for tremor management through the control of muscle co-contraction (2013) Journal of NeuroEngineering and Rehabilitation, 10 (1), art. no. 36. https://doi.org/10.1186/1743-0003-10-36 | ||
''This study uses a neuroprosthesis in order to reduce effects of tremors. The treatment relies on muscle co-contraction for tremor management. Results: The neuroprosthesis attained significant attenuation of tremor (p<0.001), and reduced its amplitude up to a 52.33±25.48%.'' | |||
=== Reading tremors === | === Reading tremors === | ||
Line 591: | Line 1,002: | ||
[24] Deuschl, G., Petersen, I., Lorenz, D., & Christensen, K. (2015). Tremor in the elderly: Essential and aging-related tremor. Movement Disorders : Official Journal of the Movement Disorder Society, 30(10), 1327-34. | [24] Deuschl, G., Petersen, I., Lorenz, D., & Christensen, K. (2015). Tremor in the elderly: Essential and aging-related tremor. Movement Disorders : Official Journal of the Movement Disorder Society, 30(10), 1327-34. | ||
doi | https://doi.org/10.1002/mds.26265 | ||
''Tremor research on elderly, seen is that people get tremors as they get older.'' | ''Tremor research on elderly, seen is that people get tremors as they get older.'' | ||
[25] Balestrino, R., & Schapira, A. (2020). Parkinson disease. European Journal of Neurology, 27(1), 27-42. | [25] Balestrino, R., & Schapira, A. (2020). Parkinson disease. European Journal of Neurology, 27(1), 27-42. | ||
doi | https://doi.org/10.1111/ene.14108 | ||
'' General research on Parkinson's disease. '' | '' General research on Parkinson's disease. '' | ||
== References == | == References == | ||
Line 644: | Line 1,018: | ||
This section contains tables with the amounts of time spent on each subject by each member, per week. | This section contains tables with the amounts of time spent on each subject by each member, per week. | ||
[[Logbook Group 13]] | |||
Latest revision as of 13:58, 4 May 2020
Group members
Student name | Student ID | Study | |
---|---|---|---|
Yara Daamen | 1337157 | Pyschology & Technology | y.f.daamen@student.tue.nl |
Heather Hanegraaf | 1330454 | Biomedische Technologie | h.e.h.hanegraaf@student.tue.nl |
Mayke Scheffer | 1234784 | Electrical Engineering | m.scheffer1@student.tue.nl |
Wouter Haneveer | 1300334 | Computer Science | w.haneveer@student.tue.nl |
Gijs van Bakel | 1239471 | Applied Physics | g.v.bakel@student.tue.nl |
Peer review
Presentation
You can download the presentation here: https://we.tl/t-bdd7DOqQko .
Problem Statement
Simple tasks like eating are not as easy for everyone. For instance: people with a tremor, or who are suffering from Parkinson’s disease, have trouble with something as simple as bringing a spoon to their mouth. Their meals take a lot longer and they often have to be assisted while eating. There are several products available on the market, like self-stabilizing spoons and forks, but the disadvantage of these products is that they are quite expensive and big. With these existing solutions people are able to eat independently again, but they always have to take their own cutlery with them.
Objectives
Independent use - The user should be able to utilize this product independently to assist them while eating. This means that the device should be easy to turn on and be natural to use. This way, the user can do daily life tasks without needing help from caregivers, and thus making them more independent.
Cost efficient - As people with Parkinson's disease often already have enough costs to care for their disability, it is important that the device is affordable (less than €100,-). This way, it can be available for way more users in need. Another point to keep in mind is safety. If this device is too expensive the user will be at risk of being robbed, which has to be considered as people with Parkinson's disease can be more vulnerable and an easy target to rob.
Comfortable in use - The device should be comfortable in use for the target group. It should have a shape that is comfortable to hold for the duration of a three-course meal. Using the device should not cause any pain or harm and users should have no negative feelings when using it. These criteria will be verified through user tests. The user should be fully comfortable using the device within two weeks of getting used to it.
Recognize nature of movement - The device should recognize unwanted vibrations that are, for instance, caused by a tremor or Parkinson’s disease. The unwanted vibrations should be distinguished from deliberate movement of the cutlery within one period of movement. The error in recognizing the nature of the movement should be less than 10%.
Act on unwanted movement - When an unwanted movement is recognized, this should be compensated by keeping the piece of cutlery stable. The stabilizing should not take more than two periods of unwanted vibrations. The piece of cutlery should only be allowed to move in the direction of the deliberate movements.
Modular - The device should be compatible with at least 90% of the cutlery that is used in restaurants. Therefore the part of the device that is connected to the cutlery must be adjustable in size and it should be able to attach and use the device within one minute. This means that the user can feel more comfortable when using the device, as the device can be attached to the cutlery other people are using for example. The device should be able to work for at least three hours without intermediate charging. This is for the comfort of the user, as they might want to use the spoon during the whole day without having to charge it.
Approach, Milestones, Deliverables and Planning
Approach
The aim of this project is to help people with nerve diseases that cause tremors to become more independent. We are going to do this by making a device that can be attached to any cutlery, which makes it possible to eat independently for the target group. We want to achieve this goal by doing extensive research and eventually delivering a simplified prototype including information about this prototype on the wiki page. The approach to reach these goals contains multiple steps.
1. Research
Firstly, we will be going through research papers and other sources which describe the state of the art of such cutlery and its respective components. This allows our team to get a grasp of the current technology of such a system and introduce us to the new developments in this field. This helps to create a foundation for the project, which we can develop into. The state of art also gives valuable insight into possible solutions to solve our problem statement. The research has to be done with the use of literature, survey(s), personal interview(s), recent reports from research institutes and the media and analysing patents that are strongly connected to our project.
2. USE aspects
Furthermore, we will continue to analyze the problem from a USE – user, society, enterprise – perspective. An important source of this analysis is the state of the art research, where the impact of these cutlery systems in different stakeholders is discussed. The USE aspects will be of utmost importance for our project as every engineer should strive to develop new technologies for helping not only the users but also the society as a whole and to consider the possible consequences of the system they develop. This analysis will lead to a list of requirements for our design. We also set up a survey to find out any unknown requirements. This makes that the requirements are based on the USE analysis and the survey.
3. Product shaping
When we finish these two steps, we will develop a prototype in which the product will be conceptualized and programmed. In this process, the RPC's are used to design the software, hardware and the appearance of the prototype.
4. Documentation
To finish, the wiki has to be updated and should contain the whole process of designing our prototype, as well as all of the research that is done to get there. To accomplish this, someone will be assigned to check and edit the page every week. Besides the wiki, a presentation has to be made in anticipation of the last few weeks.
Listed below is a summary of the main steps in our approach of the project.
- Doing research on our chosen project using SotA literature analysis
- Analysing the USE aspects and set up the survey to determine the requirements of our device
- Choose the Hardware and Software for the prototype
- Work on the prototype
- Create a demo of the tracking functionality
- Evaluate the prototype
Milestones
Here the major milestones can be found for every week. :
- Week 1: The subject is chosen and also the Plan for the project has been made.
- Week 2: It is clear who the users are, the research (SotA) is finished and also the requirements are determined.
- Week 3: Research into design prototype and costs + set up survey.
- Week 4: Research into software prototype and a list of parts and estimation of costs is made.
- Week 5: Building prototype + information from survey to improve the prototype.
- Week 6: The prototype has been made.
- Week 7: The demo will be finished and ready to be presented.
- Week 8: The wiki page is finished and updated with the results that were found from testing the prototype. Also, future developments are looked into and added to the wiki page.
Deliverables
Within this project there are four final deliverables.
- This wiki page, which contains all of our research and findings
- A presentation, which is a summary of what was done and what our most important results are
- A prototype, due to the situation caused by COVID-19 this consists of two parts: the electronics and the 3D printed case which could not be put together.
- A demo, due to the situation caused by COVID-19 this is included in the presentation
Planning
Name | Week #1 | Week #2 | Week #3 | Week #4 | Week #5 | Week #6 | Week #7 | Week #8 |
---|---|---|---|---|---|---|---|---|
Research | RPC's and USE Analysis + start prototype research | Hardware Design + Survey | Software Design + Survey | Prototype | Proof Reading | Demo | Conclusions + Future Developments | |
Heather Hanegraaf | Write approach, milestones and deliverables | Requirements | Wiki Page check | USE Analysis | USE Analysis | Presentation script | Start making presentation | Wiki Page check |
Brainstorm subject ideas | Requirements justification | Survey | Survey | Send Survey | Survey ideas | Finish presentation | Finish presentation + audio | |
Make the planning | Adjust Planning | Finish Requirements | Efficiency of performance method | Clean the wiki page | Clean the wiki page | |||
Yara Daamen | Research 13 papers | USE Analysis | Survey | Wiki Page check | Foam grapper system | Foam grapper system | Finish Presentation | Wiki Page check |
Add the research papers to the wiki page | Adjust objectives | Finish chapter "holding spoon" | Finish presentation + audio | |||||
Survey | ||||||||
Mayke Scheffer | Write problem statement and objectives | Research Prototype | Explain start prototype | Improve Prototype | Wiki Page check | Make final prototype | Finish prototype | Wiki Page check |
Improve Prototype | Order Components | Prototype Justification | Finish prototype | |||||
Meeting Prototype Building | Edit BoM | Start testing prototype | ||||||
Wouter Haneveer | Research 5 papers | 3D printing | 3D printing report on wiki page | make 3D printing | Wiki Page check | Finish 3D printing | Wiki Page check | |
Add the research papers to the wiki page | Summary State of the art sources 7-25 | 3D printing improve | Final 3D model printing | Edit BoM | ||||
Edit Wiki page | Clean wiki page | |||||||
Gijs van Bakel | Write User part | Research Prototype | Mechanical solutions research | Literature Study check | Meeting Prototype Building | Prototype Justification | Wiki Page check | Wiki Page check |
Research 7 papers | Summary state of the art sources 1-6 | Arduino code on wiki page | Write future improvements | Finish future improvements | ||||
Group Work | Brainstorm about the subject during meeting | Meeting Planning + prepare feedback session | Group meeting | Group meeting | Group meeting | Skype Meeting online | Skype Meeting 1 | Skype Meeting 1 |
Online meeting (WhatsApp) about subject | Skype Meeting 2 | Skype Meeting 2 | ||||||
Skype meeting 3 |
State of the Art
Several papers have been collected on the topic of self-stabilizing technologies, which are shown at the 'Literature study week 1' section near the end of the report, together with a short summary in one or two sentences. They are sorted into distinctive categories for clarity. The following section summarizes the most important findings of the collected literature for our project, together with additional research on other topics that have been done at a later time such as the section on mechanical stabilization.
Similar products
Active cancellation hardware is currently used in noise-canceling headphones and a similar method can be used for self-stabilizing spoons[1]. This method uses two DC motors connected with mechanical yokes that couple vertical and horizontal motion of the spoon. The sensor/controller system uses a tri-axial accelerometer embedded in the spoon base to sense the direction of tremor in the x and y directions and directs the spoon to move in the opposite direction. A bandpass filter is used to filter out noise, and acceleration data as a function of time is resolved into the frequency domain using Fourier transformation[2].
Vibration isolation and a dynamic vibration absorber can be used to reduce the hand tremor with a semi-active device, which can not only reduce hand tremors but can also generate its needed electrical energy[3]. In this system, two clamped guided piezoelectric beams are used to hold the spoon and a clamped piezoelectric beam is used as a dynamic vibration absorber.
A PID controller can be used to actively control the system. This type of controller continuously calculates an error value e(t) as the difference between the desired setpoint (SP) and a measured process variable (PV) and applies a correction based on proportional, integral, and derivative terms (denoted P, I and D respectively), hence the name. In the study “Design of a noninvasive and smart hand tremor attenuation system with active control: a simulation study” two motors are used that can rotate in perpendicular directions, which allow the mechanism tip to move horizontally and vertically[4].
Another method uses Inertial Measurement Unit (IMU) sensors and actuators for stabilizing a cup while under severe hand vibration. It is like the Active force method in the sense that a microcontroller processes the feedback from the IMU, upon which it rotates the two motors in the opposite direction of hand movement in order to achieve proper stabilization. PI and PID controllers are also used for this self-stabilizing cup[5].
Note on the frequency of tremors: Based on previous studies, it is concluded that the frequency of the hand tremor is different from the frequency of the voluntary movement. Accordingly, the frequency of the hand tremor in Parkinson’s disease is in the range of 3–6 Hz and it is between 5 and 12 Hz in essential tremor disease. Therefore, a low-pass filter, with a cut-off frequency of 3 Hz, can be used to distinguish the voluntary motion from tremor movement[6].
Solutions to reduce tremors
Next to self-stabilizing wearables we also did research on ways to reduce tremors, the most important findings to reduce tremors are listed below.
One could think about adding weight to the patient's wrist or use a heavier spoon, since then an equal amount of force would mean less movement since the mass is bigger[7]. Although some research[8] does support this, there are also studies[9] that state that no significant changes can be seen by adding weight.
Another solution that could be applied to the spoon is to make the handle smaller. As research[10] shows that a smaller handle makes people with Parkinson's disease move faster and smoother, possibly since they have more control over the spoon due to the shorter distance to it.
An exoskeleton can also be used to suppress tremors[11]. Here, an exoskeleton uses an electromyogram (EMG) signal, which is a biosignal which affects the activation of muscles, to measure whether the movement is voluntary or not. If the movement is voluntary the exoskeleton moves with the body, else it will not move and suppress the movement. However, exoskeletons can be used in other parts of the arm as well, like seen in research[12] much more complicated exoskeletons can be made. This one uses Active Force Control (AFC) based on piezoelectric actuators to reduce tremors in the wrist.
Tremors could also be reduced by measuring the distance to an object and keeping this distance the same with the help of motors[13]. However, for our project this is not relevant since we want our tool to be usable in a dynamic environment and to pick up food, we need to go towards the food and this way would work against what we want to accomplish.
With the use of accelerometers, actuators and position sensors, tremors could be seen and reduced by countering the force of the tremor with an equally big force in the opposite direction, according to research[14]. However, this system is designed for cars and is therefore too big and expensive to use for a spoon. If a way smaller and cheaper version could be made, it might be a good way to reduce tremors in a spoon but the problem is that it might be difficult to see whether a movement is from a tremor or a voluntary movement from the user itself.
By rotating an unbalanced mass, one could counter and thus reduce a tremor[15] . However, added on a spoon this would make the spoon too heavy since we should add multiple masses to be able to create a counterforce in every direction, thus making it not usable for cutlery.
Using a coin type vibration motor and a microcontroller, it is possible to create random vibration patterns to distract the user from the bio-mechanical feedback loop with the hand and reduces the hand tremor and improving the ability to grip or hold an object[16].
Lastly, we found that muscle co-contraction could be used to stabilize joints[17]. When a tremor is measured, the muscles are electronically contracted to stabilize the joint, this reduces the tremors since your muscles are contracted and thus unable to create a tremor.
Measuring tremors
We also did research on ways to measure tremors, here are our findings of how to measure tremors.
One could measure tremors by using advanced mathematical methods of time series analysis as seen in this research[18]. Here an easy to use Microsoft windows application is built to investigate forms of tremors using advanced mathematical methods of time series analysis.
We also found a device using four accelerometers and is capable to measure tremors, movement and accidental falls[19]. This device also has the possibility to connect via Bluetooth, Wi-Fi and GSM to a remote supervisor.
Another way to measure tremors is by combining accelerometers with gyroscopic transducers. A device is made using three-axis accelerometer and three axis gyroscopic transducers embedded in one device called shimmer[20]. This device can measure the acceleration, velocity and displacement of a tremor.
Stabilization in other fields
So far all the sources that are found are directly related to our product, either with the active force method, a PID controller or some other electronic device. However we know that other methods of stabilizing, for instance mechanically, are also used in other fields. Since no sources have been found that directly use mechanical stabilization for stabilizing cutlery, some literature on self-stabilizing cameras has been found to see if we can draw any parallels. Mainly because we also wanted to see whether this could be applied to our problem statement. So to reach this goal, more literature research into stabilization in general has been done, with the results of this presented below.
Some literature[21] mentions how image stabilization is actually not done actively, but “edited in”. A template matching method is used that consists of selecting small high-contrast regions of an image and these are matched with a reference image to compute their displacement, which is then corrected[22].
Another source of literature mentions a similar approach to the ones that have been found for stabilizing cutlery, using a PID controller with an inertial measurement unit (IMU)[23]. The same method is used for cameras on UAVs (unmanned aerial vehicles)[24].
MEMS (micro-electromechanical system)-based gyroscopes and accelerometers are also used in order to stabilize cameras. These units are however specifically made for this purpose and would be too big to use in the area of self-stabilizing cutlery[25].
USE Analysis
It is good to first know who the users of the product are. Society and enterprise must also be taken into account before we start making the prototype. That is why a USE analysis is being carried out. The requirements will then be formed from this USE analysis after which we will us to develop the prototype.
User
First, we take a look at the user aspect of our product. At the start of this project it was only clear that there would be a product for people with a tremor or a disorder in the nerves. First of all, research was done into which disorders where tremors occur, since people with those disorders are potential users of our product. It was interesting to conduct further research into the disorders MS, Parkinson's and essential tremors. Now, a short analysis will follow about these diseases and then a choice will be made for which patients our device will be developed.
MS
More than 2.3 million people are affected by MS worldwide. Most people living with MS are diagnosed between the ages of 20 and 50, with more than twice as many women as men being diagnosed with the disease. MS is an abbreviation for multiple sclerosis. It is an unpredictable, often disabling disease of the central nervous system, caused by the immune system which attacks the protective sheath (myelin) that covers nerve fibers and causes communication problems between your brain and the rest of your body. Eventually, the disease can cause permanent damage or deterioration of the nerves[26]. Symptoms range from numbness and tingling to blindness and paralysis. The disease varies greatly from person to person, and from time to time, for the same person. For instance, one person might experience abnormal fatigue, another might have severe vision problems, and another could develop attention and memory issues. Besides these symptoms, tremor, lack of coordination or unsteady gait can also be experienced. Even severe symptoms could disappear completely and the person could regain lost functions. However, in the worst cases, people can have partial or complete paralysis[27].
Parkinson's disease
Parkinson's disease is the second most common progressive brain disease with 7 million patients worldwide. Parkinson's disease is a brain disorder that leads to shaking, stiffness, and difficulty with walking, balance, and coordination. Parkinson's symptoms usually begin gradually and get worse over time. As the disease progresses, people may have difficulty walking and talking. They may also have mental and behavioral changes, sleep problems, depression, memory difficulties, and fatigue. One clear risk factor for Parkinson's is age, most people with Parkinson’s develop the disease at about age 60. Parkinson's disease signs and symptoms can be different for everyone. Early signs may be mild and go unnoticed. Symptoms often begin on one side of your body and usually remain worse on that side, even after symptoms begin to affect both sides. Parkinson's disease has four main symptoms: tremor (trembling) in hands, arms, legs, jaw, or head, stiffness of the limbs and trunk, slowness of movement and impaired balance and coordination, sometimes leading to falls[28]. Another symptom is chewing and swallowing difficulties can occur, especially during the later stages of the disease. These can be due to changes in function either in the autonomic nervous system or the muscles in the throat, known as the pharyngeal muscles[29].
Essential tremors
Essential tremor is a nervous system (neurological) disorder that causes involuntary and rhythmic shaking. It can affect almost any part of your body, but the trembling occurs most often in hands — especially when doing simple tasks, such as drinking from a glass or tying shoelaces. Essential tremor is usually not a dangerous condition, but it typically gets worse over time and can be severe for some people. Other conditions don't cause essential tremor, although essential tremor is sometimes confused with Parkinson's disease. Essential tremor can occur at any age but is most common in people aged 40 and older. The tremor signs and symptoms begin gradually, usually more prominently on one side of the body, worsen with movement, usually occur in the hands first, affecting one hand or both hands, it can include a "yes-yes" or "no-no" motion of the head and it may be aggravated by emotional stress, fatigue, caffeine or temperature extremes[30].
Target group
Our targeted users are people suffering from hand and arm tremors which are caused by the Parkinson’s disease but also people suffering from essential tremors. We have chosen both conditions as users, as this increases the number of people who are potential users. Furthermore, essential tremors and the tremors in Parkinson's disease are very similar, therefore the spoon can be used by both patients.
To really focus on perfecting a product fitted to our targeted users, it is necessary to choose a specific topic. Therefore, we mainly focus on Parkinson's patients, as this is a much better known problem that needs to be addressed. These users, people with Parkinson’s disease, are in almost all cases elderly around or above 60. These people are often in need of a lot of care and can’t perform a variety of independent tasks on their own. Especially eating is a very frequent activity that has to be assisted minimally 3 times a day. For patients who are still mentally healthy it can be a very degrading feeling to have to be fed. A device that could help these patients could greatly improve their independence and feeling of self-worth. Although we focus on Parkinson, the spoon can thus still be used by both parties.
Society
For the society, this device can make a small, but needed, change to the healthcare. As the population of elderly grows bigger and bigger so will the amount of patients with Parkinson’s disease. This will have a big impact on the society as they are in high need of caring. By using this device, the working load for the caretakers could be decreased, allowing them to have more time for other activities. Furthermore, it can greatly improve patients' independence and feeling of self-worth. This is also a benefit to society, as people may feel happier overall.
Enterprise
The Enterprise stakeholder is about companies that have the same kind of idea to tackle this problem. It is clear that there is already a market for these products. We will now discuss some of those similar products.
Flexible TPE and Lepel Torso Grip
Our solution is aimed at robots and works through the use of electricity, but there are also companies that have come up with a much simpler solution. For example, a flexible silicone edge around the edge of the spoon. In this way, the food stays on the spoon better. This can indeed be a good solution for the problem, but the success rate of an electric spoon is higher than with this solution.
Another simple solution is to make a better grip on the spoon. This way the spoon is easier to hold for people with Parkinson's disease. The handle of the spoon itself then becomes larger, which research shows that this has no positive effect on the use of the spoon. This research was conducted by Clinical Rehabilitation and their findings were as follows: "The movement of the participants with Parkinson's disease was faster (shorter movement time) and smoother (fewer movement units) when they used spoons with a small or medium-sized handle than when using a spoon With a large-sized handle. In contrast, the healthy controls showed no significant differences in movement kinematics between handle sizes. Moreover, the participants with Parkinson's disease had a significantly smaller hand aperture and used more fingers to hold the spoons than the controls did"[31]. This shows that the handle should not be too large, but it should be big enough since patients with Parkinson's hold the spoon with more fingers. So, in our design we want a combination of good grip, big enough size for holding the spoon, but not too big because this would have a negative effect on the time to move and the smoothness to do so.
Foodrobot
A robotic arm is another solution to the problem. ZorgvanNu explains how it works: "Obi has two control buttons: one to choose which bowl to scoop from, and one to control the scooping movement. An arm with a spoon on it scoops up the food and brings it to the mouth. If you are going to use Obi, first set the correct position of the arm in relation to your mouth. You can always set it (or have it adjusted) in a different way, so that you do not always have to sit in the same way"[32]. This can be an effective solution if the tremors become so bad that the patient can no longer hold the spoon. However, we have opted for a different solution, which is to be more mobile and not to have to carry a large device if the patient goes out for diner, for example. Another disadvantage of this solution is that the contact between human and robot must be very consciously taken into account. Because if the patient suffocates, the robot simply continues, which would not be user-friendly. It is a good solution, if people come in the next stage of Parkinson's and they have no other option left. However, our solution is for people who can still use a spoon themselves.
Liftware, Gyenno and "Smart"-spoon
There are also products that are very similar to what we want to produce. This is namely a spoon that measures the tremors and then tries to counteract it by making the opposite movement. Liftware, Gyenno and "Smart" spoon are examples of this. Although there are already working products on the market, we are convinced that we can improve the product. Those products are namely still expensive and the spoon is attached to the device. Our goal is to produce a simple and cheap working device that can be attached to any spoon to create a natural eating experience.
Survey
A survey has been set up to find out how the prototype can be better shaped and which requirements have to be met. This survey was sent to several Parkinson associations. The first association we chose to message was called Parkinson Vereniging. We chose to send it here, as it is the largest institution of Parkinson's disease in the Netherlands. It was decided to conduct a survey in the Netherlands, as those associations are best accessible and the quickest response to our survey. The e-mail address we sent it to is: info@parkinson-vereniging.nl[33]. The survey is addressed to the caregivers of patients with Parkinson's. Here's what the survey looks like. Link Survey. They responded by telling us the Parkinson Vereniging wasn't really meant for that. They did however link two other options to continue our research. The first link they sent was of parkinsonzorgzoeker.nl[34]. However, this site is mostly meant for approaching individuals, whereas we needed to contact as many people as possible. We thus decided that this site was not useful for us. The next link they sent was also from Parkinson Vereniging, but this time meant especially for research requests[35]. We also sent them a mail. However, they reacted saying that they were for research centred around the people who have Parkinson's disease, not the caretakers. We then chose to go for different associations. We found Brabantzorg[36], but they told us they were too busy because of corona. This is also the case for an association called Careyn[37]. They also informed us that they were too busy with corona. The last association we messaged was 24uurszorgsevice[38]. They haven't responded yet.
In view of circumstances (the COVID-19 virus) we still send the survey to the caregivers, but bearing in mind that there was probably no response to this, because the caregivers have their hands full. Hoping that there would be a reaction, it was the intention that a thematic analysis[39] was carried out on the results. This allowed us to make our product even better for the users, but given that we unfortunately did not have any responses to the survey, the requirements that follow in the next section are only based on the USE analysis and thus on literature study.
Requirements
The requirements follow from the user analysis. This is because the users are going to use the product and therefore the device must meet their requirements.
Requirement ID | Technical requirement description |
---|---|
R1 | The device must cancel out at least 60% -70% of a sudden movement caused by a tremor |
R2 | The device must be able to withstand heat flux |
R3 | The device must be able to withstand water or other liquid |
R4 | Energy consumption should be as low as possible |
R5 | It must be a device that can be mounted on a spoon. So a separate device. |
Functional requirement description | |
R6 | The device must ensure that a person with a disability in the nervous system can eat independently |
R7 | The size of the cutlery must not be larger than a normal spoon |
R8 | The weight of the spoon must not be more than that of a normal spoon |
R9 | The cost of the device must not be higher than 100 euros |
R10 | The device should have constructive elegance |
R11 | The device must work for 3 hours without the need for replenishing batteries. |
R12 | The device must be natural and simple to use |
R13 | The device must be durable and able to withstand sustained use |
R14 | The device must be able to fit on any spoon and hold it securely |
R15 | The device must be compact and streamlined |
Technical Requirement Justification
It must be measurable whether the device works or not, which is why it has been stated in the requirements that the spoon must be able to resolve 60% to 70% of all tremor movements. In this way, it is testable whether the spoon is indeed functioning properly. The percentages come from literature studies, from similar products. This study demonstrated a 71% to 76% reduction in tremor with the ACT device on[2]. Moreover, the classical Parkinson's tremor that occurs at rest is often asymmetrical and has a distal maximum and a typical frequency of 4–6 Hz[40]. So to meet the requirement of 60 to 70%, 2.6 - 3.9 Hz would have to be cancelled. The product must also be able to withstand heat flux and liquid. This is because it is used when eating hot meals. For example, think of soup, which is both liquid and hot. Another standard but important requirement is that the product should consume the lowest energy possible, which is self-explanatory. The last technical requirement is very important. As you can read in the USE Analysis section, there are similar products that also help people with tremors to eat independently. However, their product is a spoon, fork or knife that eliminates tremors. We want to make a product that is modular, so it can be attached separately to a spoon, fork or knife. In this way, you only have to take the small device with you and not all the adjusted cutlery.
Functional Requirement Justification
Of course, The most important requirement is that the spoon must help the user to eat independently. Furthermore, there are also requirements for the weight and size of the device. This is because people with Parkinson's disease already have trouble eating, and therefore the size and weight must be kept as small and as light as possible, so as not to add any more obstacles. The price of the spoon is also important since comparable but very expensive products are already on the market. We want to develop a product that is affordable for everyone, so a requirement has been set for the price of the product. Furthermore, the device must have a constructive elegance, this requirement speaks for itself. It must look presentable, or nobody would want to use it. Another functional requirement is that the service life of the spoon should last approximately 3 hours. This is because the device must at least accompany a meal since people do not want to replace the batteries in the middle of the meal.
The device should be natural to use because a lot of elderly (especially those who are not mentally healthy anymore) struggle to use new technologies. If the device is not natural and simple to use, the eating experience might only be more stressful than before. The device should be durable because it will be used multiple times per day and will be cleaned and moved all the time. Furthermore, people with tremors can accidentally drop this device on the ground and bump it around, so it should be sturdy enough to withstand all of these incidents. As already stated before, the device must be separately attached to cutlery, but it is important that it is able to grab onto (almost) all cutlery and keep it secure. This makes our product stand out as it can be applied to the already provided cutlery. The last requirement, that the device must be compact and streamlines is also important. If there are loose parts or parts sticking out, they can get stuck to the environment which stops the user from eating. Especially due to the tremors the device will move around a lot and we do not want it to get stuck to anything.
Systems for holding spoon
From the USE analysis, the requirement emerged that our product must be a device that can be attached to the spoon (or other cutlery) and that it should be a separate device. This is because it then becomes much more portable. In this way, you only have to take the small device with you and not all the adjusted cutlery. However, this requires a system that ensures that the device can be attached to any spoon (or other cutlery), regardless of its size. Research has been done into which type of system would work best for this. In this section, you can read the results of the research.
There are several ways to hold the spoon in place within the tool. It should be able to tightly hold on to almost any type of spoon and should thus be able to get a grip on different kinds of handles. Some of these systems offer a part of the solution or more.
Gripper
One of these systems is a gripper for small parts. These grippers are made to accommodate to different kinds of weights and shapes of small objects[41]. However, these grippers are mostly designed for small and delicate parts notes Costas Charalambous :“Grippers and vacuum cups always need a light tough to properly grab small parts because they’re delicate,”. Nonetheless, these grippers could be applied to our product even if they're originally made for more delicate parts. You can see such a gripper in Figure 2.
Vacuum Gripper with Fingers
Another one of these systems is a vacuum gripper which you can see in Figure 3. These grippers are very useful for gripping any kind of workpieces regardless of size, material and surface. It is also very lightweight and would be ideal for our device. However, this product seems to be very expensive. As we want to develop a cheap solution we will not be able to use this system, as one of our requirements mentions that the costs should be as low as possible.
Vacuum Gripper wrapped around
The third system is similar to the vacuum system, but replaces the "fingers" with a material that wrappes around the object and holds it. It is demonstrated in Figure 4. This material can meld to any shape upon contact with the object[42]. This system reduces the amount of parts that have to be controlled and can thus be more reliable and cheap.
This research was important to realise what systems exist right now. However, we also found out that these systems are not applicable for our product. These systems are indeed very accurate and useful, but as we stated before, we want a affordable product. This means that we cannot use these systems. The attachment system we ended up using is very simple and described in the 3D printing section.
3D printing
To make the case for all the electronics, we decided to use 3D printing to our advantage. However, before we can print something, we first need to draw the case. For this we decided to use Solidwork. With this program we are able to accurately draw a case since Solidwork makes it very easy to draw shapes with precise lengths. Solidwork also allows for easy fixes since if you change the length of one part Solidwork changes the other parts to fit this change.
Holding the spoon
The first step in designing the case is finding a way to hold most spoons without damaging it. Since we want our design to work for many different spoons, and every spoon has a different handle design, we needed to find a cheap way in which we could attach all spoons to our design. We decided to make a tube to put the spoon into, and then secure the spoon with a screw. To prevent damage to the spoon a piece of rubber can be added to the screw, however even without the rubber we did not damage the spoon by jamming it. To make it easier to turn the screw we could also add an attachment to the screw which you can easily turn, which would look like the one in Figure 5. Another problem was that it could be difficult to get the spoon in the center of the holder. To make this easy we made a V shape in the back of the holder which moves the back of the spoon to the center of the holder, shown in Figure 7.
Place servo's
The second step in our design was to find a place for the servos. We could not just attach both servos to the handle and the holder, since then the holder would have two attachment points with the handle and would not be able to turn. We thus needed to either first correct the pitch or the roll axis relative to the handle. If we tried to correct the pitch axis before the roll axis, we would need to attach the pitch servo to the handle, then attach the roll servo to the pitch servo, and lastly attach the holder to the roll servo. This would however not be possible since rotating the handle around the roll axis would change the axis the pitch servo would correct in. Thus we first needed to correct the roll axis and then correct the pitch axis. We had to attach a handle to the roll servo, attach the roll servo to the pitch servo and finally connect the pitch servo to the holder. The roll servo needs to be behind the spoon in order to turn around the spoons roll axis, the pitch servo needs to be to the side of the spoon. Thus to be able to attach the roll servo to the pitch servo we need to make a connection piece. This connection piece needs to move from the side of the holder to the back of the holder while giving the holder enough space to turn along the pitch axis. The pitch servo needs to be attached to the connection on the body itself, while the roll servo needs to be connected to the connection with the feet of the servo.
The handle
Finally, we need to design a handle to hold the device with. This handle needs to be attached to the body of the roll servo, and have enough room inside it for the rest of the electronics. Because all the electronics need to be in the handle we also needed a way to open and close the handle. We decided to make the handle in two pieces, which we can attach together with screws. This also allows us to easily open the handle to replace batteries or remove broken electronics. Since one of the servos is outside the handle we needed a way for the cable to get inside the handle. In order to do this, we made a little cut in the side of one of the parts of the handle. With all the electronics that need to fit in the handle, the handle is bigger than we would have liked. This could be solved by using electronics particularly developed for this product, such that the shapes of the electronics allow for a more compact design.
The results
Below the printed results can be seen. The idea was to use the 3D printed case in the prototype, but because of the COVID-19 outbreak, we were unable to put the electronics together with the 3D printed component. This means that all these pictures are without most of the electronics. Since the servos used in the pictures are borrowed, we were unable to connect them to the parts thus in Figure 12 a notebook was put under the spoon in order to get the spoon on the correct height such that it looked like the product is fully attached.
Prototype
Circuit
To get an idea of how such a spoon would work, we started with a very simple prototype in week 3. This prototype works with the active force method. The prototype will first be focused on spoons, since not all cutlery (spoons, forks and knives) have to be stabilized in the same way. Two servos will be used to compensate movements on the pitch and roll axis of rotation ([1]). A picture showing a graphical representation of the pitch, roll and yaw axes can be seen in Figure 16 in the section Design Choices, further on in the wiki. The movement of the spoon will be measured by an MPU6500 accelerometer. The servos and sensor will be attached to a Digispark Attiny85 microcontroller. 4 AAA batteries will be used to power the circuit. The prototype works with a PID controller by inducing a force opposite of the measured acceleration, which then aims to bring the spoon to the reference position. The connection of these components can be seen in the following Figure:
Arduino code
Active force method
The Arduino code for the very first prototype without PID controller is shown below.
Prototype with PID controller
The Arduino code for the prototype with the PID controller can be seen below. Some comments have been added to explain the code.
Design Choices
Stabilizing two or three axes?
How many axes the spoon should stabilize is a question that quickly came up. We use the pitch, roll and yaw axes that are usually used in planes. These axes are also frequently mentioned in literature and they are perfect for the stabilization of the spoon. Figure 16 below shows these axes for clarity. It is obvious that the pitch and roll axes are necessary to stabilize, to make sure that food doesn’t fall off the spoon. However, the question arose whether the yaw axis is necessary, helpful, or completely useless. Below some of the arguments for and against using 3 axes instead of 2 are outlined.
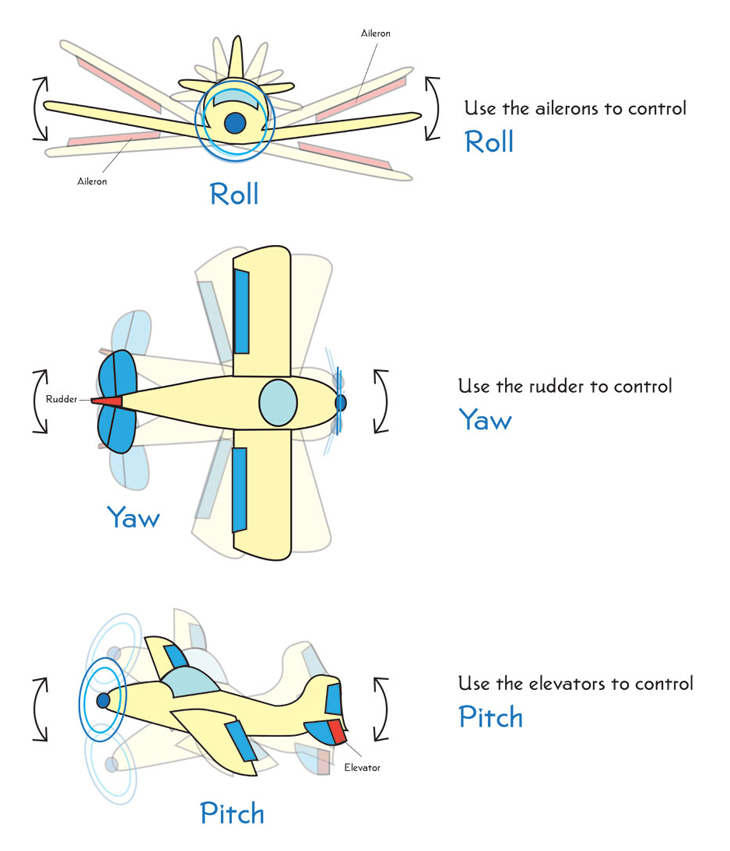
The main argument for only stabilizing two axes is that the yaw axis simply doesn’t have to be stabilized. The movement in the same plane as the spoon (the yaw axis) would not contribute to many difficulties with eating. If this axis were to be stabilized, you even run the risk of stabilizing voluntary motions. Another argument for not using 3 motors is that it would make our design bulkier. It is critical that the stabilizing mechanism is as small and light as possible for ease of use, shown and discussed in our requirements of the product.
Type of controller
The type of controller that the self-stabilizing spoon will use has also been a big decision point. A few of the popular control mechanisms have been described in the State of the Art, for example using the Active Force Method or a PID controller. Ultimately we settled on using a PID controller with the stabilizing mechanism consisting of two motors that supply a force against the tremor direction, thus keeping the spoon level.
We already had a preference for a PID controller after we saw that many studies in the literature were also using them for prototypes and initial designs for self-stabilizing devices. A few of us already have experience with PID controller so it would take less time to set up. We do realize that PID controllers are outdated in the sense that the technology is pretty old, but for the sake of building an initial prototype in the limited timeframe that we had in this course (8 weeks) we think this is a good stepping stone for the prototype, which could be improved further with state of the art technology if this product is further worked out.
Choice of components
The individual physical components for the first prototype have been chosen with the following things in mind. First is the compatibility. The component must do what it is expected to do (shown in the circuit and description above) and have enough strength to fulfill the tasks (e.g. the servos). Second is the size of the component. As mentioned in the requirements, the total device should be as small and light as possible, in order to make it as comfortable and easy to use. The last important property of the component that was looked at is the price. Again the requirements mention the price should be as low as possible because many comparable but way more expensive products are already on the market.
The First Prototype: Proof of Concept
The initial prototype has been made in week 3. The goal of this test is to see whether our ideas about stabilizing the spoons actually work. Figure 17 below shows this initial prototype. The initial prototype consists of the Inertial Measurement unit, one servo motor and a spoon, all connected to the Arduino. The code that is used is the first one shown in the section Arduino code. Even though this code is written for two motors, it still works for any set-up with one motor as well. So now we have only one sensor present, but we see that when the sensor and motor with spoon attached are rotated in the pitch direction, the spoon keeps stays level. From this we conclude that the proof of concept is a success and from here we integrated the other components into the final prototype.
The Process
After typing a few keywords in Google it seemed like making the prototype wouldn’t be a particularly hard task. There are lots of examples of people who made something like we are attempting[44][45][46]. The first approach was to write our own PID controller based on the codes used in these projects and the help from the examples in the Arduino PID library [47]. After that the idea was to improve the controller in order to get the desired stabilization. Although, in the end, this first approach is more or less what we did to achieve the final controller, there have been a few bumps in the road. The coronavirus had a big impact on the process, this impact was direct as well as indirect.
Lack of testing equipment
For the first prototype we borrowed the needed materials from the department Electrical Engineering, some friends and we used some of our own. While researching the components, we focused on everything that would actually be in the final product. This included the Digispark Attiny85 microcontroller, which does not have serial communication. In the Arduino code, this means that every Serial.print() statement does not do anything and therefore it is hard to detect bugs in the code. We knew this beforehand and planned on borrowing the Arduino Uno again, but this was not possible due to the coronavirus. Therefore, we had to revise what we needed and ordered an Arduino Uno, a breadboard and extra wires.
Ordering late
Before ordering the components, we had to contact Lambèr Royakkers, who sent us to the Mechanical Engineering workshop to ask if they already had the things that we needed in their possession. The workshop was closed due to the coronavirus and we had to order them ourselves. Together with having to reorder, this process costed us a week of our valuable time.
MPU6500
The sensor that we wanted to use, the MPU6050, was sold out when we ordered our components. However, a seemingly similar one was available, the MPU6500. Time pressure and inexperience made us decide to go for this sensor. Not knowing that it meant that it was not possible to use the example projects mentioned above. These Arduino codes use so called ‘libraries’, which are sets of functions written by experienced programmers. The MPU6050 is widely used and there are lot of different libraries available. The Arduino examples above don’t even use the same ones. The MPU6500 is less popular and there were no examples within the scope of our project available. There was a library available that made it possible to read the values of the sensor[48]. Having values and getting the right values out of a PID controller turned out to be two completely different things and after spending a day working on this without result, we tried another approach. Until this moment a combination of three existing projects was used instead of recreating one of the three. The new plan was to use the MPU6500 with the Gyro stabilizer from instructables. This ended up in deep research into Arduino communication, I2C protocols and sensor addresses, where it felt like every answer raised two new questions. Although this research was very interesting and it gave useful insights in how Arduino’s work, this level of programming was not going to bring us closer to a self-stabilizing spoon. It would need an advanced Arduino user or a lot more time adjust libraries in a way that would work for us. In the meantime the MPU6050 sensor was available again so we decided to order it so we could test the existing Arduino codes and finalize our own PID controller.
The final week
The MPU6050 surely made everything a lot easier. The ‘instructables’ code worked somewhat, but a lot less stable than in the corresponding video. The spoon tended to start vibrating instead of stabilizing after fast movements and after about 30 seconds it stopped working until the reset button was pressed. After this it was time to test and tune our own PID controller.
Indirect impact
Due to the coronavirus only one of us was working on the electronics part alone. Indirect this is also a reason that everything took a lot longer than expected. If we could meet it would have been a lot easier to work together on programming and assembling everything, even if it is with group members that have no experience at all. Another advantage of working at the university would be the possibility to ask help from other students and helpdesks/workshops. Having someone taking a fresh look at a project can sometimes save a lot of time debugging, especially when there is just a wire connected wrongly.
The Final Prototype
The prototype consists of two parts, the internal electronics and the 3D-printed design. Due to the coronacrisis it was not possible to meet in order to put everything together. In an ideal situation the electronics would have been soldered on a protoboard that fits into the grip of the 3D-printed case. Unfortunately this was not possible because the needed soldering equipment for soldering such precision is only available on the university. Since there is no fitting case, the electronics are taped together, which makes the system much less stable. The sensor is taped to the ‘roll’ sensor; therefore this movement is much more accurate than the ‘pitch’ sensor. With the 3D-printed case this won’t be this way.
Bill of Materials
All materials used in our product are listed above the double line, while under the double lines we listed all the materials we had to use in order to create our product
Efficiency of Performance / Testing the Prototype
Test methods must be developed to test whether the prototype meets the requirements and to see whether it works well enough. Two methods have been devised to measure the efficiency of the performance of the prototype. The first test is practical and therefore technical and the second method is based on theory.
Technical
Method 1. In the requirements, it has been explained that a typical tremor has a frequency of 4–6 Hz. We have also made the requirement that 60 to 70 percent of the tremor must be compensated. This resulted in that 2.6 - 3.9 Hz would have to be cancelled. And so that when the spoon is working, there is only a frequency of 1.4 - 2.1 Hz. If this is indeed the case, then it can be concluded that the spoon works well enough in this respect.
Method 2. In another study, they also tested a Parkinson's spoon. There they took advantage of the decrease in amplitude. If the amplitude of the movements decreased significantly when the spoon was on as compared to off, the test was successful and it was concluded that the function of the spoon was meaningful[2]. This is also a method on which we will test the efficiency of the spoon.
Method 3. The purpose of the spoon is that as much food as possible remains on the spoon and is therefore not fallen off during a tremor. So what matters in the end, is what percentage of the food remains on the spoon when the stabilizing system is on as compared to when it is turned off. If this percentage is significantly more, it can be concluded that the purpose of the spoon has been achieved and so a conclusion can be drawn about the efficiency of the spoon.
Theoretical
Then there is also a method to test the Parkinson Spoon theoretically. This is done through a follow-up survey to the first survey. In this survey, it is first explained what our product exactly is and then questions are asked whether the caregivers think that this product can work. It can be a survey for many caregivers or an interview is conducted with one of the caregivers. The questions we want to ask in the survey/interview can be read in this link: Survey 2.
Conclusion Efficiency of Performance
Due to the lack of time, explained in The Process, it was not possible to actually test the performance of the device.
So unfortunately, we were no longer able to test our prototype. To still evaluate if the prototype is usable we looked at how many requirements the prototype meets. Here you can see the set requirements again. The following requirements have been achieved:
Requirement ID | Technical requirement description |
---|---|
R1 | The device must cancel out at least 60% -70% of a sudden movement caused by a tremor |
R2 | The device must be able to withstand heat flux |
R3 | The device must be able to withstand water or other liquid |
R4 | Energy consumption should be as low as possible |
R5 | It must be a device that can be mounted on a spoon. So a separate device. |
Functional requirement description | |
R6 | The device must ensure that a person with a disability in the nervous system can eat independently |
R7 | The size of the cutlery must not be larger than a normal spoon |
R8 | The weight of the spoon must not be more than that from a normal spoon |
R9 | The cost of the device must not be higher than 100 euro |
R10 | The device should have constructive elegance |
R11 | The device must work for 3 hours without the need for replenishing batteries. |
R12 | The device must be natural and simple to use |
R13 | The device must be durable and able to withstand longer use |
R14 | The device must be able to fit on any spoon and hold it securely |
R15 | The device must be compact and streamlined |
The requirements which are met, are colored green above. As can be seen in the table above, 10 out of the 15 requirements are met. Some of the requirements that were not met, were not met because we were unable to do the tests and therefore cannot conclude whether they have been met. These could therefore be checked off later, if the tests on the prototype are done in the future. So a very large part of the requirements have been met and we can therefore say that the prototype is successful.
Future Improvements/Research/Developments
This section deals with the improvements that could be made after this project is done. The reasons for not including these in the main project are the limited timeframe of this project and the coronavirus, limiting our USE implementation. Below the areas in which either the USE aspects can be implemented and the technical design can be improved are highlighted.
USE survey
It has already been described that the survey that has been made for this project has not been able to be used, due to the coronavirus. Understandably caregivers and institutions did not have time to answer our questions in order to improve the USE aspects of our design and product. Carrying out another survey now that a prototype has been made could even be more beneficial, as you can give the caregivers a better idea of our product, giving us better answers to implement these design changes and improving the design for the end-user. A themed analysis would be carried out to analyse the data that is received from the survey, which in turn we can use to improve the design.
User testing
In this project, we have regrettably not done a user testing session with an actual Parkinson's patient. However, this is certainly something that we would consider if we had more time. A type of session where we simply tell a patient to use our device and observe what some of the difficulties (and good parts!) of our design can make us aware of issues that we didn't even think about before, simply because we don't deal with the problems ourselves. There are different ways to go about this. You could just observe like just described and use your knowledge about the subject together with the user's experience. Including a survey or some type of review session with the user can give more insight into specific problems that are not visible to an observer.
Hardware improvements
One of the areas in which the prototype can be improved a lot is the hardware that is used. Currently, it uses cheap commonplace components that are not ideal for example considering the size of the components, as we want the product to be the least bulky it can be. The servo motors take up quite a lot of space. The current servo that is used twice is the SG90 mini servo (link in the Bill of Materials) which has dimensions of 23x12.2x29 mm. The smallest component that is sold normally is the Power HD Sub-Micro Servo HD-1440A servo, with dimensions 20.2x20.2x8.5 mm, which is less than half of the volume than the ones we used[49]. This means that two of these servos would still be smaller (in volume) then 1 SG90 servo. This servo does cost a little more but this is not very significant (5.43 vs 4.00 euros) Similar to this arguably better components can be found for the other parts as well. Another example of this is the microcontroller. A microcontroller developed by InvenSense has dimensions 3x3x0.9 mm which is extremely small compared to the one that we used[50].
Of course, the parts that we used for the prototype, as well as the parts that are researched parts, are freely available for purchase for any non-specific use. This means that if parts were to be constructed by ourselves if we had the knowledge to do so, they would be specifically made with the product specifications and preferences in mind. This means that the size, power, weight, etc. can be optimized, which would make a big difference if this product would be produced and put for sale for consumers worldwide.
Software Improvements
Currently, the prototype uses a PID controller. It is evident that the PID controller is not state of the art anymore as it is quite old. One literature source talks about how PID controllers are simple compared to other solutions and can be integrated into almost any system together with the robustness properties that ensure stability and high performance under changes of the parameters.[51]. There are other alternatives such as the Field Programmable Gate Array (FPGA) and more predictive instead of reactive control systems. Because the PID controller is purely reactive it could be interesting to look into more predictive methods of stabilization in possible future research.
Conclusion
The problem addressed during this project is the fact that people with a nervous disorder, specifically Parkinson's disease and essential tremors, have much more trouble with daily tasks than healthy people. We have focussed on the need for help of this target group during meals, because they have trouble with something as simple as bringing a spoon to their mouth. This means that their meals take a lot longer and they often have to be assisted while eating.
To give these people more freedom, self-esteem and independence, we have developed a device that can stabilize a spoon or other cutlery while eating with a tremor. Research has shown that there are already similar products on the market, but these prove to be large, expensive and inconvenient to transport when eating out. That is why we were convinced that we could improve the current products on the market by making an affordable and small device that can be mounted on a regular spoon.
In the past seven weeks we have been busy realizing the prototype described above. In the wiki page, the process and the choices made, can be read. Unfortunately, the final prototype has not been tested, as can be read in the results section, due to the COVID-19 conditions which caused that only one of the group members could work on the prototype hardware and software. It is therefore impossible to draw a real conclusion on whether our product is the solution for the problem mentioned.
To be able to say something about the quality of the solution to the problem, we looked at how many requirements were met in the final prototype. This turned out to be at least 10/15, of which some of the unfulfilled requirements were not met because they simply have not been tested. So, in conclusion, at least 10 and maybe after tests have been done in the future more than 10, of the 15 requirements have been met. With the future improvements in mind, it can be concluded that the prototype is a great starting point for a product that later can be used to solve this problem.
Literature Study week 1
At least 25 pieces of literature have been found in the field of the problem statement in week 1. They have been collected, sorted into categories and a short summary per article has been written.
Similar products
[1] Thilmany, J. (2013). Stable spoon. Mechanical Engineering; New York, 135(5).
Spoon that cancels human tremors. Same technique as in noise cancelling headphones: active cancelation software. Digital cameras also cancels motion. LiftWare tremor-cancelling spoon from company Lift Labs.
[2] Pathak, A., Redmond, J. A., Allen, M., & Chou, K. L. (2013). A noninvasive handheld assistive device to accommodate essential tremor: A pilot study. Movement Disorders, 29(6), 838–842. https://doi.org/10.1002/mds.25796
Research on how active cancellation of tremor (ACT) can stabilize motion of spoon. Results show that the device helps reduce tremor amplitude and severity. Same company Lift Labs.
[3] Abbasi, M., & Afsharfard, A. (2018). Modeling and experimental study of a hand tremor suppression system. Mechanism and Machine Theory, 126, 189–200. https://doi.org/10.1016/j.mechmachtheory.2018.04.009
Very useful for our project. Research on application of the system. By experiments they obtain and validate electromechanical equations.
[4] Abbasi, M., Afsharfard, A., Arasteh, R., & Safaie, J. (2018). Design of a noninvasive and smart hand tremor attenuation system with active control: a simulation study. Medical & Biological Engineering & Computing, 56(7), 1315–1324. https://doi.org/10.1007/s11517-017-1769-9
Same researchers. Simulated study on how the device will work.
[5] Vishnu, V., Prabaharan, P., Sujadevi, V.G., Meher, M.D.IMU sensor based self-stabilizing cup for elderly and parkinsonism (2017) 2017 International Conference on Advances in Computing, Communications and Informatics, ICACCI 2017, 2017-January, pp. 2264-2269.
A proposal for a wearable auto stabilizing cup holder that helps in routine performance tasks such as drinking water. The system uses IMU sensors and actuators for stabilizing the cup when under severe hand vibration.
[6] Turgeon, P., Laliberte, T., Routhier, F., Campeau-Lecours, A. Preliminary design of an active stabilization assistive eating device for people living with movement disorders(2019) IEEE International Conference on Rehabilitation Robotics, 2019-June, art. no. 8779388, pp. 217-223. https://doi.org/10.1109/ICORR.2019.8779388
A preliminary design for a stabilizing eating device. It includes mechanical design, damping arrangement, electronic design and control algorithms.
Solutions to reduce tremors
[7] McGruder, J., Cors, D., Tiernan, A. M., & Tomlin, G. (2003). Weighted Wrist Cuffs for Tremor Reduction During Eating in Adults With Static Brain Lesions. American Journal of Occupational Therapy, 57(5), 507–516. https://doi.org/10.5014/ajot.57.5.507
Research on the usage of weights on the forearm. Research shows that making the wrist heavier resulted in fewer tremors while self-feeding for some individuals.
[8] Meshack, R. P., & Norman, K. E. (2002). A randomized controlled trial of the effects of weights on amplitude and frequency of postural hand tremors in people with Parkinson’s disease. Clinical Rehabilitation, 16(5), 481–492. https://doi.org/10.1191/0269215502cr521oa
Again research on weighted utensils for patient suffering from Parkinson’s Disease. This time no support for a significant effect on reduction of the tremor.
[9] Matsumoto, Y., Seki, M., Ando, T., Kobayashi, Y., Nakashima, Y., Iijima, H., … Fujie, M. G. (2013). Development of an Exoskeleton to Support Eating Movements in Patients with Essential Tremor. Journal of Robotics and Mechatronics, 25(6), 949–958. https://doi.org/10.20965/jrm.2013.p0949
Usage of exoskeleton to suppress tremors and support voluntary movement. The research shows that the exoskeleton works to a certain extent.
[10] Song, C., Gehlbach, P. L., & Kang, J. U. (2012). Active tremor cancellation by a “Smart” handheld vitreoretinal microsurgical tool using swept-source optical coherence tomography. Optics Express, 20(21), 23414. https://doi.org/10.1364/oe.20.023414
In the medical world are tremors also an obstacle, especially for microsurgeons. The device helps steady the surgeon tool by canceling the tremors. This could also be applied to our subject.
[11] Ma, H.-I., Hwang, W.-J., Chen-Sea, M.-J., & Sheu, C.-F. (2008). Handle size as a task constraint in spoon-use movement in patients with Parkinson’s disease. Clinical Rehabilitation, 22(6), 520–528. https://doi.org/10.1177/0269215507086181
Research on the effect of the size of a spoon handle on the amount of tremors that a Parkinson’s Disease patient is experiencing. The results show that a smaller to medium sized spoon handle caused a faster and smoother movement compared to a big handle.
[12] Hamdy, A. (1999). Active damping of vibrations in elevator cars. Journal of Structural Control, 6(1), 53–100. https://doi.org/10.1002/stc.4300060105
Usage of active damping system for cars. It doesn’t apply perfectly to the spoon but shows how a system can actively reduce the extremes.
[13] Chuanasa, J., & Songschon, S. (2014). Essential tremor suppression by a novel self-balancing device. Prosthetics and Orthotics International, 39(3), 219–225. https://doi.org/10.1177/0309364614525185
Self-balancing device that can be used for tremor suppression. Algorithm controls mass actuator.
[14] Rovini, E., & Merammani, C., & Cavallo, F. (2017) How wearable sensors can support parkinson’s disease diagnosis and treatment: A systematic view. Frontiers in Neuroscience, 11 (OCT), art. no. 555. DOI: 10.3389/fnins.2017.00555.
Review of 136 papers that shows a wide overview of wearable devices for the management of Parkinson’s disease. Objectives: This review focuses on wearable devices for PD applications and identifies five main fields: early diagnosis, tremor, body motion analysis, motor fluctuations (ON-OFF phases), and home and long-term monitoring.
[15] Hosseini, S.M., Al-Jumaily, A., Kalhori, H.Tremor suppression in wrist joint using active force control method(2017) 9th Australasian Congress on Applied Mechanics, ACAM 2017, 2017-November.
The paper proposes a new AFC (active force control) method for tremor attentuation, using a three-degree-of-freedom musculoskeletal model. Matlab is used to analyze the model. Conclusion: AFC-based system with a piezoelectric actuator and a PD controller is very effective is suppressing the human hand tremor.
[16] Vidya, V., Poornachandran, P., Sujadevi, V.G., Dharmana, M.M.Suppressing Parkinson's diseases induced involuntary movements using wearables(2018) Proceedings of 2017 IEEE International Conference on Technological Advancements in Power and Energy: Exploring Energy Solutions for an Intelligent Power Grid, TAP Energy 2017, pp. 1-4. https://doi.org/10.1109/TAPENERGY.2017.8397267
This paper proposes and implements a low-cost wearable assistive device for Parkinson’s disease patients. A coin vibrator motor a micro controller are used. The induced vibration on the wrist distracts the patient’s brain from the bio-mechanical feedback loop with the hand and reduces the tremor and improving the ability to grip or hold an object.
[17] Gallego, J.A., Rocon, E., Belda-Lois, J.M., Pons, J.L. A neuroprosthesis for tremor management through the control of muscle co-contraction (2013) Journal of NeuroEngineering and Rehabilitation, 10 (1), art. no. 36. https://doi.org/10.1186/1743-0003-10-36
This study uses a neuroprosthesis in order to reduce effects of tremors. The treatment relies on muscle co-contraction for tremor management. Results: The neuroprosthesis attained significant attenuation of tremor (p<0.001), and reduced its amplitude up to a 52.33±25.48%.
Reading tremors
[18] Lauk, M., Timmer, J., Lücking, C. H., Honerkamp, J., & Deuschl, G. (1999). A software for recording and analysis of human tremor. Computer Methods and Programs in Biomedicine, 60(1), 65–77. https://doi.org/10.1016/s0169-2607(99)00012-7
Research on monitoring the different types of tremors by analyzing the recording and applying mathematical methods.
[19] Marino, S., Cartella, E., Donato, N., Muscarà, N., Sorbera, C., Cimino, V., … Di Lorenzo, G. (2019). Quantitative assessment of Parkinsonian tremor by using biosensor device. Medicine, 98(51), e17897. https://doi.org/10.1097/md.0000000000017897
Home-made and low-cost device that can read tremors.
[20] Serrano, J.I., Lambrecht, S., del Castillo, M.D., Romero, J.P., Benito-León, J., Rocon, E.Identification of activities of daily living in tremorous patients using inertial sensors(2017) Expert Systems with Applications, 83, pp. 40-48. https://doi.org/10.1016/j.eswa.2017.04.032
Instead of measuring tremors, the paper instead focuses on contextualizing the symptoms of diseases like Parkinson’s. The study describes the development of a comprehensive methodology based on machine learning techniques to segment and detect activities of daily living in people with tremor using inertial sensors, which aims at facilitating detailed interpretation of tremor movements by neurologists.
[21] Mehmet Engin (2006). A recording and analysis system for human tremor. Measurement, 40(3), 288-293. https://doi.org/10.1016/j.measurement.2006.05.015
Tremor analysis based on frequency and amplitude to diagnose people’s condition.
[22] Gugliandolo G, Capra PP, Bramanti A, Di Lorenzo G, Campobello G, Donato N, Marino S (2019). A Movement-Tremors Recorder for Patients of Neurodegenerative Diseases. IEEE Transactions on Instrumentation and Measurement, 68(5), 1451-1457. https://doi.org/10.1109/TIM.2019.2900141
Tremor recorder for people affected by neurodegenerative diseases.
[23] Reem Musab, Azizan As’arry, Khairil Anas Md Rezali, Nawal Aswan Abdul Jalil, Raja Mohd Kamil Raja Ahmad, Mohd Zarhamdy Md Zain (2019). Tremor Quantification and its Measurements Using Shimmer. Journal of Physics: Conference Series, 1262. https://dx.doi.org/10.1088/1742-6596/1262/1/012024
Different sensors to measure tremors and comparison between them.Different sensors to measure tremors and comparison between them.
Possible users
[24] Deuschl, G., Petersen, I., Lorenz, D., & Christensen, K. (2015). Tremor in the elderly: Essential and aging-related tremor. Movement Disorders : Official Journal of the Movement Disorder Society, 30(10), 1327-34. https://doi.org/10.1002/mds.26265
Tremor research on elderly, seen is that people get tremors as they get older.
[25] Balestrino, R., & Schapira, A. (2020). Parkinson disease. European Journal of Neurology, 27(1), 27-42. https://doi.org/10.1111/ene.14108
General research on Parkinson's disease.
References
- ↑ Thilmany, J. (2013). Stable spoon. Mechanical Engineering; New York, 135(5)
- ↑ 2.0 2.1 2.2 Pathak, A., Redmond, J. A., Allen, M., & Chou, K. L. (2013). A noninvasive handheld assistive device to accommodate essential tremor: A pilot study. Movement Disorders, 29(6), 838–842. https://doi.org/10.1002/mds.25796
- ↑ Abbasi, M., & Afsharfard, A. (2018). Modeling and experimental study of a hand tremor suppression system. Mechanism and Machine Theory, 126, 189–200. https://doi.org/10.1016/j.mechmachtheory.2018.04.009
- ↑ Abbasi, M., Afsharfard, A., Arasteh, R., & Safaie, J. (2018). Design of a noninvasive and smart hand tremor attenuation system with active control: a simulation study. Medical & Biological Engineering & Computing, 56(7), 1315–1324 https://doi.org/10.1007/s11517-017-1769-9
- ↑ Vishnu, V., Prabaharan, P., Sujadevi, V.G., Meher, M.D.IMU sensor-based self-stabilizing cup for elderly and Parkinsonism (2017) 2017 International Conference on Advances in Computing, Communications and Informatics, ICACCI 2017, 2017-January, pp. 2264-2269.
- ↑ Bhidayasiri R (2005) Differential diagnosis of common tremor syndromes. Postgrad Med J 81(962):756–762. https://doi.org/10.1136/
- ↑ McGruder, J., Cors, D., Tiernan, A. M., & Tomlin, G. (2003). Weighted Wrist Cuffs for Tremor Reduction During Eating in Adults With Static Brain Lesions. American Journal of Occupational Therapy, 57(5), 507–516. https://doi.org/10.5014/ajot.57.5.507
- ↑ McGruder, J., Cors, D., Tiernan, A. M., & Tomlin, G. (2003). Weighted Wrist Cuffs for Tremor Reduction During Eating in Adults With Static Brain Lesions. American Journal of Occupational Therapy, 57(5), 507–516. https://doi.org/10.5014/ajot.57.5.507
- ↑ Meshack, R. P., & Norman, K. E. (2002). A randomized controlled trial of the effects of weights on amplitude and frequency of postural hand tremors in people with Parkinson’s disease. Clinical Rehabilitation, 16(5), 481–492. https://doi.org/10.1191/0269215502cr521oa
- ↑ Ma, H.-I., Hwang, W.-J., Chen-Sea, M.-J., & Sheu, C.-F. (2008). Handle size as a task constraint in spoon-use movement in patients with Parkinson’s disease. Clinical Rehabilitation, 22(6), 520–528. https://doi.org/10.1177/0269215507086181
- ↑ Meshack, R. P., & Norman, K. E. (2002). A randomized controlled trial of the effects of weights on amplitude and frequency of postural hand tremors in people with Parkinson’s disease. Clinical Rehabilitation, 16(5), 481–492. https://doi.org/10.1191/0269215502cr521oa
- ↑ Hosseini, S.M., Al-Jumaily, A., Kalhori, H.Tremor suppression in wrist joint using active force control method(2017) 9th Australasian Congress on Applied Mechanics, ACAM 2017, 2017-November.
- ↑ Song, C., Gehlbach, P. L., & Kang, J. U. (2012). Active tremor cancellation by a “Smart” handheld vitreoretinal microsurgical tool using swept-source optical coherence tomography. Optics Express, 20(21), 23414. https://doi.org/10.1364/oe.20.023414
- ↑ Hamdy, A. (1999). Active damping of vibrations in elevator cars. Journal of Structural Control, 6(1), 53–100. https://doi.org/10.1002/stc.4300060105
- ↑ Chuanasa, J., & Songschon, S. (2014). Essential tremor suppression by a novel self-balancing device. Prosthetics and Orthotics International, 39(3), 219–225. https://doi.org/10.1177/0309364614525185
- ↑ Vidya, V., Poornachandran, P., Sujadevi, V.G., Dharmana, M.M.Suppressing Parkinson's diseases induced involuntary movements using wearables(2018) Proceedings of 2017 IEEE International Conference on Technological Advancements in Power and Energy: Exploring Energy Solutions for an Intelligent Power Grid, TAP Energy 2017, pp. 1-4. https://doi.org/10.1109/TAPENERGY.2017.8397267
- ↑ Gallego, J.A., Rocon, E., Belda-Lois, J.M., Pons, J.L. A neuroprosthesis for tremor management through the control of muscle co-contraction (2013) Journal of NeuroEngineering and Rehabilitation, 10 (1), art. no. 36. DOI: 10.1186/1743-0003-10-36
- ↑ Lauk, M., Timmer, J., Lücking, C. H., Honerkamp, J., & Deuschl, G. (1999). A software for recording and analysis of human tremor. Computer Methods and Programs in Biomedicine, 60(1), 65–77. https://doi.org/10.1016/s0169-2607(99)00012-7
- ↑ Gugliandolo G, Capra PP, Bramanti A, Di Lorenzo G, Campobello G, Donato N, Marino S (2019). A Movement-Tremors Recorder for Patients of Neurodegenerative Diseases. IEEE Transactions on Instrumentation and Measurement, 68(5), 1451-1457. https://doi.org/10.1109/TIM.2019.2900141
- ↑ Reem Musab, Azizan As’arry, Khairil Anas Md Rezali, Nawal Aswan Abdul Jalil, Raja Mohd Kamil Raja Ahmad, Mohd Zarhamdy Md Zain (2019). Tremor Quantification and its Measurements Using Shimmer. Journal of Physics: Conference Series, 1262. https://dx.doi.org/10.1088/1742-6596/1262/1/012024
- ↑ Rodriguez-Padilla, I., Castelle, B., Marieu, V., Morichon, D. A simple and efficient image stabilization method for coastal monitoring video systems (2020) Remote Sensing, 12 (1), art. no. 70. https://doi.org/10.3390/RS12010070
- ↑ Rodriguez-Padilla, I., Castelle, B., Marieu, V., Morichon, D. A simple and efficient image stabilization method for coastal monitoring video systems (2020) Remote Sensing, 12 (1), art. no. 70. https://doi.org/10.3390/RS12010070
- ↑ Auysakul, J., Xu, H., Pooneeth, V. Video stabilization with a dual system based on an IMU sensor for the mobile robot (2019) Advances in Intelligent Systems and Computing, 856, pp. 618-626. https://doi.org/10.1007/978-3-030-00214-5_78
- ↑ Franco, F.P.L., Loubach, D.S., Fioravanti, A.R. An embedded system design for a two-axis camera platform control used in unmanned aerial vehicles (2017) Proceedings - 2017 LARS 14th Latin American Robotics Symposium and 2017 5th SBR Brazilian Symposium on Robotics, LARS-SBR 2017 - Part of the Robotics Conference 2017, 2017-December, pp. 1-6. https://doi.org/10.1109/SBR-LARS-R.2017.8215289
- ↑ Sofla, M.S., Parsa, M., Golshanian, H. Stabilizing a camera mount using MEMS gyroscope and accelerometer (2016) Transactions of the Institute of Measurement and Control, 38 (11), pp. 1345-1352. https://doi.org/10.1177/0142331215587339
- ↑ Mayo Clinic Staff. (2019, 19 April). Multiple sclerosis - Symptoms and causes. Retrieved from https://www.mayoclinic.org/diseases-conditions/multiple-sclerosis/symptoms-causes/syc-20350269
- ↑ National MS Society. (z.d.). MS the Disease. Retrieved from https://www.nationalmssociety.org/About-the-Society/Press-Room/MS-the-Disease
- ↑ National Institute of Aging. (2017, 16 May). Parkinson’s Disease. Retrieved from https://www.nia.nih.gov/health/parkinsons-disease
- ↑ The MNT Editorial Team. (2018, 26 October). Parkinson’s disease complications. Retrieved from https://www.medicalnewstoday.com/articles/323399#chewing-and-swallowing
- ↑ Mayo Clinic Staff. (2019, 23 January). Essential tremor - Symptoms and causes. Retrieved from https://www.mayoclinic.org/diseases-conditions/essential-tremor/symptoms-causes/syc-20350534
- ↑ Ma, H.-I., Hwang, W.-J., Chen-Sea, M.-J., & Sheu, C.-F. (2008). Handle size as a task constraint in spoon-use movement in patients with Parkinson’s disease. Clinical Rehabilitation, 22(6), 520–528. https://doi.org/10.1177/0269215507086181
- ↑ Zorg van nu. (2020, 11 February). Hulp bij eten met een eetrobot. Retrieved from https://www.zorgvannu.nl/oplossingen/hulp-bij-eten-met-een-eetrobot
- ↑ Parkinson Vereniging. (z.d.). Contact - Parkinson Vereniging. Retrieved from https://www.parkinson-vereniging.nl/vereniging/over-ons/contact
- ↑ parkinsonzorgzoeker. (z.d.). Contact - parkinsonzorgzoeker. Retrieved from https://(www.parkinsonzorgzoeker.nl
- ↑ Parkinson Vereniging. (z.d.). Contact - Parkinson Vereniging. Retrieved from https://www.parkinson-vereniging.nl/onderzoek/oproepen-onderzoek/oproepen
- ↑ Brabantzorg. (z.d.). Contact - Brabantzorg. Retrieved from https://www.brabantzorg.eu/contact/Paginas/default.aspx
- ↑ Careyn. (z.d.). Contact - Careyn. Retrieved from https://www.careyn.nl/contact-met-careyn/
- ↑ Brabantzorg. (z.d.). Contact - Brabantzorg. Retrieved from https://www.24uurszorgservice.nl/contact/
- ↑ VPPK. (2017 maart). Thematic Analysis. Retrieved from https://www.vppk.be/wp-content/uploads/2017/03/THEMATIC_ANALYSIS.pdf
- ↑ Zach, H., Dirkx, M., Bloem, B. R., & Helmich, R. C. (2015). The Clinical Evaluation of Parkinson's Tremor. Journal of Parkinson's disease, 5(3), 471–474. retrieved from: https://www.ncbi.nlm.nih.gov/pmc/articles/PMC4923747/ https://doi.org/10.3233/JPD-150650
- ↑ Camillo, J. (z.d.). Grippers for Small Parts. Geraadpleegd op 23 Maart 2020, van https://www.assemblymag.com/articles/94073-grippers-for-small-parts?iframe=1
- ↑ Wevolver | Knowledge shared by technology developers and scientists. (z.d.). Retrieved from https://www.wevolver.com/wevolver.staff/universal.robotic.gripper/
- ↑ Roll, Pitch and Yaw, How things Fly. https://howthingsfly.si.edu/flight-dynamics/roll-pitch-and-yaw
- ↑ https://create.arduino.cc/projecthub/RupinC/assistive-spoon-for-patients-with-parkinson-s-3628b6
- ↑ https://www.instructables.com/id/Gyro-Stabilizer-W-Arduino-and-Servo/
- ↑ https://howtomechatronics.com/projects/diy-arduino-gimbal-self-stabilizing-platform/
- ↑ https://playground.arduino.cc/Code/PIDLibrary/
- ↑ https://github.com/rpicopter/ArduinoMotionSensorExample
- ↑ Power HD Sub-Micro Servo HD-1440A servo. retrieved from: https://www.pololu.com/product/1040/specs
- ↑ Invensense MPU-6500. Retrieved from: https://invensense.tdk.com/products/motion-tracking/6-axis/mpu-6500/
- ↑ Kozak, Š.Kozák. (2014). State-of-the-art in Control Engineering. Journal of Electrical Systems and Information Technology. 1. 1–9. https://doi.org/10.1016/j.jesit.2014.03.002
Logbook
This section contains tables with the amounts of time spent on each subject by each member, per week. Logbook Group 13