PRE2018 3 Group3: Difference between revisions
(453 intermediate revisions by 6 users not shown) | |||
Line 1: | Line 1: | ||
= | [[File:Causes.jpg|thumb|300px|Figure 1: Causes for train delay in the Netherlands <ref name=trainStatistics />]] | ||
The Dutch railway network is one of the most crowded railway networks on the planet <ref name=drukspoor>Ramaekers, P., De Wit, T., & Pouwels, M. (2009, February 27). Hoe druk is het nu werkelijk op het Nederlandse spoor? CBS.</ref>; an intercity leaves the station every 10 minutes. The Dutch trains are also very punctual; 90% of all trains are in time <ref name=jaarverslag>NS jaarverslag 2017 https://www.nsjaarverslag.nl/jaarverslag-2017/resultaten4/a1054_Punctualiteit</ref> with a 5 minute tolerance. This is a rare accomplishment among railway companies. However, there is a downside to all of this; since it is so busy, a single problem can have dramatic effects. One delay can create a congestion and this can cause huge delays. In 2016 the Dutch government estimated that delays cost at least 145 million euros annually<ref name=kostenvertraging>Cost of train delays https://www.rijksoverheid.nl/documenten/rapporten/2016/10/24/mobiliteitsbeeld-2016</ref>. Therefore it is important that delays are prevented as much as possible. | |||
From the graph in Figure 1 it can be seen that external influences (indicated by orange), railway cleaning activities (indicated by purple) and the weather (indicated by yellow) are causes for train delays in the Netherlands <ref name=trainStatistics />. They add up to almost 20% of all train delays. These types of train delays are partly caused by snow and leaves on the train tracks. As a result we estimated that snow and leaves cause approximately 10% of the train delays in the Netherlands. | |||
The problem with leaves on the tracks is that trains compress the leaves beneath them. These leaves form a sticky low-friction coating on the tracks and this increases the breaking distance tremendously. This can lead to dangerous situations. That is why railway companies (like the Dutch 'Nederlandse Spoorwegen' or NS) prefer to avoid risksy situations by cancelling their trains. Currently, no proper solution exists for this obstacle. | |||
Snow on the other hand is the cause of a very different problem. Snow on the tracks is only dangerous in large quantities, which is rare in the Netherlands. However, snow can be a problem, when it falls between the switches, since it prevents switches from moving. This problem is solved by using switch heaters, but these fail from time to time and there is no backup. | |||
We as a group believe we can improve this sticky situation by introducing a robot to the Dutch railway network that is able to clean the tracks from obstacles like leaves and snow. This wiki describes the whole process of this project. | |||
= Group Members = | |||
{| class="wikitable" style="border-style: solid; border-width: 1px;" cellpadding="3" | {| class="wikitable" style="border-style: solid; border-width: 1px;" cellpadding="3" | ||
!style="text-align:left;"| Name | !style="text-align:left;"| Name | ||
Line 21: | Line 28: | ||
|} | |} | ||
= | =Project Information= | ||
More information about this project (e.g. planning, milestones, SotA, etc.) can be found by following this link: [[Project information]] | |||
=Concept= | |||
Our concept is a robot, called the DagBlad, that is able to clean the railway tracks from leaves and snow. | |||
This robot is not autonomous, since this turned out to be very difficult on the overcrowded Dutch railway network. Our robot is attached to the front of trains and is also powered by these. The DagBlad is connected to the CAN bus of the train, which allows it to retrieve valuable data, like speed, directly from the train. | |||
The robot tackles the obstacles (leaves and snow) by using a combination of sweepers and a laser (see 'Design' for more information). These are arranged in the order: sweeper, laser, sweeper. This is done deliberately. The first sweeper removes the loose layer of leaves and/or snow. This exposes the slippery layer of compressed leaves underneath. A powerful laser, which is pointed directly on this layer, heats the leaves. The leaves expand and this decreases the adhesion to the rail. The second sweeper is now able to remove the loosened layer. The rail is now cleaned from both leaves and snow (see 'Obstacles' for more information). | |||
==Objectives== | ==Objectives== | ||
The objectives when designing a kind of cleaning device for the Dutch railway tracks are of great importance. It is for NS and ProRail's best interest that these objectives, which we will call RPC's, ensure a product that is actually helpful. The so called RPC's - Requirements, Preferences and Constraints - are set up to determine what is important and function as guidelines for the robot's design. Using these guidelines will make sure essential matters to NS and ProRail are really thought through, so DagBlad functions as desired. The RPC's are stated below: | |||
Requirements | |||
* DagBlad is able to clean the tracks | |||
* DagBlad is able to remove leaves and snow using its sweepers and lasers | |||
* DagBlad is operational at any time | |||
* DagBlad is able to drive up to 160 km/h | |||
* The rotational speed of DagBlad's broom can go up to 1377,9 RPM | |||
Preferences | |||
* DagBlad should be easy to maintain | |||
* DagBlad's parts should be interchangeable | |||
* DagBlad should be as light as possible | |||
* DagBlad should be compact | |||
* DagBlad should be cleaning as fast and efficient as possible | |||
Constraints | |||
* DagBlad can only move in the direction the train is going | |||
* DagBlad has to be coupled and uncoupled at the start and end of its journey | |||
* DagBlad cannot drive and clean solely by itself | |||
* DagBlad cannot remove large objects like trees, debris or dead animals | |||
* DagBlad cannot be wider than 3.4 meters <ref name=loading_gauge>Loading gauge for trains in Europe and also the Netherlands https://en.wikipedia.org/wiki/Loading_gauge#The_Netherlands.</ref> | |||
* DagBlad cannot be taller than 2 meters | |||
==Robot Functions== | |||
The Dutch train tracks are very crowded during both day and night<ref name=jaarverslagschedule> NS jaarverslag 2017 https://www.nsjaarverslag.nl/jaarverslag-2017/resultaten4/a1054_Punctualiteit </ref>. This makes it very difficult to add an independent cleaning robot to the schedule. That is why the DagBlad robot is attached to the front of a train. This enables it to clean the tracks, while avoiding scheduling difficulties. | |||
The robot will only be used when it is necessary. This will mostly be in the autumn and winter seasons, because of the falling leaves and snow. The left sweeper rotates counterclockwise, while the right sweeper rotates clockwise. Consequently, leaves and snow are brushed from the rails. The sweepers start rotating and the laser turns on when the train moves faster than 30 km/h (see 'Software' for more information). This is done to ensure that the equipment is turned off when the train approaches/leaves a station. Otherwise, dangerous situations could occur. | |||
==Daytime and Nighttime== | |||
On average there are 4500 trains riding per day to transport around 1,1 million passengers <ref name=TrainsDaily>Alles over het spoor, Info over het spoor, (2019). Retrieved from https://www.allesoverhetspoor.nl/feitjes/leuke-feitjes/?gdpr=accept</ref>. Although a small percentage of these trains are riding through the night, most of these 4500 trains are driving during the day, as the night trains only drive once per hour between 1:00 and 5:00 in the Randstad of the Netherlands <ref name=Nighttrains>Nachttreinen, Waar en wanneer rijden nachttreinen?, NS. Retrieved from https://www.ns.nl/reisinformatie/bijzondere-trajecten/nachttreinen.html</ref>. Due to these busy train schedules during the day, it is not possible to let the cleaning robot drive autonomously on the railroads during daytime. This would only cause more delay for the NS. However, it is still extremely essential to let the machine clean the railroads during the day, because otherwise the design will not have any big positive impact on the delay problems. Hence, the only way for the DagBlad robot to clean the railroads during daytime is to attach the machine onto the front of the NS passenger trains. Next to cleaning the railroads during the day, the robot can also clean during the nighttime. Because it is less crowded on the railway during the night, the robot will be able to thoroughly clean the railroads without slowing down any other trains. However, it was decided to also not let the robot drive autonomously during the nighttime, as the switch from not autonomous to autonomous overnight would be unnecessary and difficult. Letting the robot clean while attached to a passenger train is efficient enough to clean the railroads. To make the DagBlad robot work during daytime and nighttime in this way, there are a few requirements which need to be met: | |||
[[File:Goederentreinen 17.jpg|thumb|270px|Figure 2: Total amount of freight trains in the year 2017 <ref name=FreightTrains />]] | |||
* It needs to be attachable to the front of the NS trains. | |||
* It should not block the sight of the machinist. | |||
* It cannot slow down the speed of the train. | |||
* It needs to be suitable and appropriate to pass by the platforms of the stations. | |||
* It needs to be detachable from the front of the NS trains. | |||
To meet the requirements of being able to both attach and detach from the NS trains, it needs to adapt to the front coupler of all the different NS train models. Luckily at the moment all the different Intercity and Sprinter model trains of the NS use the same type of Scharfeneberg coupler <ref name=Couplers>Langs de rails, Koppelingen. Retrieved from http://www.nicospilt.com/index_koppeling.htm</ref>. This Scharfenberg coupler is an automatic coupler which can be activated or deactivated from the machinist cabin <ref name=Scharfenberg>Treinen in beeld Nederland, Scharfenbergkoppeling. Retrieved from https://treinen-in-beeld-1.jouwweb.nl/scharfenbergkoppeling</ref>. A more detailed analysis on the coupling system can be found under the 'Design' section. | |||
The design of the cleaning machine also needs to fit with the requirements of not blocking the sight of the machinist and being suitable for platforms. This will be elaborated when developing the final design for the machine. However, from these two requirements it can already be made clear that the machine itself should not be higher than around 1.5 meter for the machinist’s sight, and not be wider than around 3 meter to fit in between platforms at stations <ref name=Trainsizes>Nederlands materieel technische gegevens, Treinen. Retrieved from http://www.angelfire.com/ego/ist3/trein.html</ref>. Furthermore, the robot will also need it’s own wheels. Thus, these wheels need to be set suitable for the rails which have a gauge of 1435 mm <ref name=Gauges>Langs de rails, Spoorwijdte. Retrieved from http://www.nicospilt.com/index_spoorwijdte.htm</ref>. | |||
Furthermore, the adaptation to attach to the passenger night trains that drive through the Randstad is possible. Next to these passenger trains, there are also many freight trains that ride on the tracks daily. According to a report of Prorail, in 2017 there have been riding more than 20.000 freight trains over the same railroads in that year, see Figure 2 <ref name=FreightTrains>Ontwikkeling spoorgoederenverkeer in Nederland, 2017 vergeleken met 2016, ProRail. (February, 2018) Retrieved from https://zoek.officielebekendmakingen.nl/blg-847011.pdf</ref>. Moreover, it can be seen that the rail tracks with the most delays are in the Randstad area in between Amsterdam, Rotterdam, Den Haag en Utrecht <ref name=trainStatistics>Rijden de treinen, Statistieken. (February, 2019) Retrieved from https://www.rijdendetreinen.nl/statistieken</ref>. This is the same area as where the most night trains are riding. Therefore, the robot needs to clean this area extra thoroughly. Hence, it will be more effective to attach the cleaning machine onto the night trains which are traveling in the Randstad. This will prevent extra delays, as the cleaning machine will not drive autonomously within this busy train schedules in the night of the Randstad. However, outside of the Randstad the cleaning machine will still have the possibility to drive autonomously to clean the railways, as there are no passenger trains active in the night. Although it is still possible to let the robot drive autonomously outside of the Randstad during the night, it was decided to not do this. After considering the requirements and needs of the users, it was concluded that making the robot drive autonomously, on top of attaching it to passenger trains, will be unnecessary and difficult on a daily basis. | |||
=USE Aspects= | |||
==Users== | ==Users== | ||
The NS and ProRail. | For this project the focus has been put on the railroads in the Netherlands. This decision was made, because it is only possible to design the product for one certain type of railroad system. At this stage designing a product which can be used globally by adapting to different types of railway systems is too advanced. Furthermore, the project would have too many potential users to focus on, as they will differ per country. Therefore, it was decided to stick to the Netherlands, as this is the country which we had the most experience with. Although it was decided to keep the focus in this specific area, there is still a wide variety of users. For this design there are people who can use and influence the design directly, as well as people who get influenced indirectly by the design. Hence, a distinction can be made between primary and secondary users. The term primary users will be used to refer to the group of users who are directly interacting with the design. The term secondary users will be used to refer to the group of users who are not directly in contact with the design but still affected by it. The distinction between these two different users will be made more clear by defining both groups. | ||
===Primary Users=== | |||
For this design, the group who buys, uses and introduces the design into its target scenario are considered as the primary users. Hence, the organisations who are responsible for the railway system in the Netherlands belong to this groups. Thus, only Prorail is the primary user, as they are the ones responsible and can make direct changes to the railway system. The NS can not be fully considered as a primary user, as they only make use of the railway system, but are not responsible for the railroad itself. Prorail are the ones responsible for the construction, maintenance, management and security of the railway system in the Netherlands. When a product with the aim to clean the railroads is used, Prorail is the main company to introduce, use, and interact with the product. | |||
===Secondary Users=== | |||
For this design, the people who get influenced positively or negatively by this design in an indirect way are considered as the secondary users. As mentioned above the NS is not considered as primary user, instead NS can be considered as a secondary user. They make use of the railway system in the Netherlands by transporting people from location to location with trains that drive on the railroads. Therefore, they will not be in direct contact with this design, as they will only get positively influenced but cannot influence the design itself directly. The use of the design on the railroads will be a great advantage to the NS, as it will make the railroads free and safe which reduces the delay for trains of NS. | |||
In addition to NS, this reduction in delay also has a positive effect on the users of NS. These users are people who make use of the trains of NS as transportation to get to their destination as fast as possible. Although NS and Prorail are in charge of the trains and railways in the Netherlands, this group of travelers is important and can also be considered as secondary users. | |||
Occasionally, trains of foreign companies such as Thalys or NMBS also make use of the railway system in the Netherlands. As a result, these foreign train companies can also be considered as secondary users. However, this group of users will not be further addressed, as the main focus is put on the companies NS and Prorail. | |||
==Society== | |||
Obstacles on the railroads, which cause a delay for many travelers, can be considered as a problem to society. In some occasions the delay can come up to major amounts of time or even cancellations of trains, which leads to missing important meetings or appointments. | |||
Moreover, this can form a challenge to the government, as the NS is a Dutch state-owned company. This means that the government has significant control over the NS through majority ownership. For this reason, one of the main aims of the government is to make transportation more accessible to its users. To be able to make transportation on railway more accessible, the delays of trains need to be taken care of. This design can help with solving this challenge to society. The design of this project can not fully solve the challenge of it, as there are many factors which have an influence on causing delays in transportation. However, this design will still have a positive impact on this relevant problem. It has the potential to play a big role in the future of railroad maintenance which is beneficial to society. | |||
==Enterprise== | |||
In the USE aspects, enterprise is considered to be the relevant companies that are connected to the project. The main aim for these enterprises is to make as much profit as possible. The previously discussed primary user Prorail can be seen as a relevant enterprise to this design. Although currently Prorail is still a government task organisation company that is part of NS, the Ministry of Infrastructure and Water is planning to make Prorail a public law independent administrative in 2021 <ref name=ProrailIndependent>Kamerbrief 19 oktober 2018, Omvorming ProRail, (October 2018). Retrieved from https://www.internetconsultatie.nl/wet_publiekrechtelijke_omvorming_prorail/document/3990</ref>. As a result Prorail will become an organisation which conducts governmental tasks, while they are not under authority of the Dutch government. Hence, in the future Prorail will look at this design from a business perspective. They will only decide to make use of this design if it is profitable for the company. Unless they are forced by the government as they will be an independent administrative. Therefore, the design is required to be efficient in general, as well as cost-efficient so that Prorail will have good consequences from using the product. | |||
=Design= | |||
==Prototype== | |||
[[File:Prototyperobot.jpg|thumb|270px|Figure 3: First idea for the prototype]] | |||
[[File:Viewengineer.jpg|thumb|270px|Figure 4: The robot is designed so the engineer has a clear view over the railroad]] | |||
The first idea for a prototype was made with SketchUp, as can be seen in Figure 3. Eventough the robot will be put in front of Sprinter trains, the model uses a standard NS Intercity (Bombardier TRAXX) locomotive for scale and context. Since the robot will block the locomotive's headlights, it is equipped by a pair. The robot is equipped with two pairs of opposite-rotating sweepers which are placed up front. The robot will also be equipped with a pair of lasers in between the sweepers. The prototype can be as wide, if not wider than the locomotive itself, if it only stays within a 3.4 meter margin as mentioned in the RPC's <ref name=loading_gauge>Loading gauge for trains in Europe and also the Netherlands https://en.wikipedia.org/wiki/Loading_gauge#The_Netherlands.</ref>. This margin is there to make sure vehicles on railway tracks can safely go through tunnels for instance without any hindrance. | |||
Notice the robot is much smaller in height than the locomotive, this is make sure the tracks are still visible for the engineer. The maximum height for the robot has been set to 2 meters. As can be seen in Figure 4, the front of the robot has a sloping edge, in order further enhance the engineer's view on the tracks. The corners of the design have been more rounded in order to minimize drag and improve driver's visibilty. | |||
The brushes and lasers are featured on the front of the robot to make sure the robot is able to clean the tracks prior to passing that piece of track. This way the wheels of the robot and train take out the bits that are left. That is also how rust is prevented from forming on the metal tracks. The brushes are pointed inward, barely touching each other, so leaves and snow get tossed outwards. | |||
==Coupling System== | |||
[[File:Coupler NS.jpg|thumb|270px|Figure 5: Coupler system of the NS Scharfenebrg coupler]] | |||
As discussed in the 'Daytime and Nighttime' section, the robot needs to adapt to the front coupler of all the different NS train models to both attach and detach from them. At the moment NS trains use a Scharfenberg coupler which is an automatic coupler that can be activated or deactivated from the machinist cabin. After getting in contact with the NS through customer service online, it was confirmed that the Scharfenberg coupler are mostly used. Additionally, the NS online customer service gave us the information that another type of coupler called BSI is also used for DDZ and DD-AR train models. Next to this BSI coupler, the NS also use the screw coupling for some trains. Although they use multiple types of couplers, it is the most efficient if the cleaning machine is adapted to one type of coupler. Hence it was decided to use the Scharfenberg coupler, as this is the most used coupler by the NS. Furthermore, the NS have given us a product sketch of the Scharfenberg coupler which they use, which can be seen in Figure 5. | |||
At the moment there are 6 types of main Scharfenberg couplers on the market: the type 10, type 35, type 330, type 430, type 55 and the type 140 <ref name=ScharfenbergCouplers>Scharfenberg couplers, Voith. Retrieved from http://www.voith.com/ca-en/products-services/power-transmission/scharfenberg-couplers-10318.html</ref>. The cleaning machine does not necessarily have to have the same type of Scharfenberg couplers as the train to which it needs to connect. There are transitional couplers, such as the modular transitional coupler, that can connect two different type of Scharfenberg couplers <ref name=ScharfenbergCouplers />. This modular transitional coupler separates the two couplers into two separate head and an adapter that forms the step. The two heads can be connected to each other directly, which makes it possible to connect coupler heads of any kind and at different heights into the transitional coupler. | |||
As a result, a suitable type of Scharfenberg coupler can be chosen for the design of the robot. | |||
* The type 10 Scharfenberg coupler is often used by railway companies, and is reliable due to its high strength and large gathering range laterally and vertically. <ref name=Type10>Scharfenberg couplers for high-speed trains, Voith. Retrieved from http://www.voith.com/ca-en/products-services/power-transmission/scharfenberg-couplers/scharfenberg-couplers-high-speed-trains-14406.html</ref> | |||
* The type 35 is suited for vehicles without a compressed-air system, so for fully electrified vehicles. <ref name=Type35>Scharfenberg couplers for railcars, Voith. Retrieved from http://voith.com/corp-en/scharfenberg-couplers/scharfenberg-couplers-railcars.html</ref> | |||
* The type 330 is often used in light rail applications due to its small size. However, it is still a strong and reliable coupler. <ref name=type330>Scharfenberg couplers for metro, Voith. Retrieved from http://voith.com/corp-en/scharfenberg-couplers/scharfenberg-couplers-metros.html</ref> | |||
* The type 430 is ideal for low floor trams and monorails, because of its compact and lightweight construction. Furthermore, it can fit behind the front covers. <ref name=type430>Scharfenberg couplers for monorails, Voith. Retrieved from http://voith.com/corp-en/scharfenberg-couplers/scharfenberg-couplers-monorails.html</ref> | |||
* The type 55 and type 140 are specifically made for high loads in rough environments. <ref name=ScharfenbergCouplers /> | |||
For the robot, the best option will be the type 330 or the type 430, as these two types are ideal for lighter sized vehicles and can still deliver a strong support. Furthermore, these types are not as big as the other types and can fit behind the front covers. The type 330 can transmit a buff load of 800 kN and a draft load of up to 600 kN, and the the 430 can transmit compressive and tensile forces of up to 300 kN. However, due to the robot being pushed by the train and not pulled by the train because of it's position in front of the train, the forces that the couplers can hold are not relevant, as it will be certain that the couplers can hold the pushing forces. | |||
=Usability= | |||
==How many robots needed?== | |||
[[File:Spoorkaart 2019.jpg|thumb|200px|Figure 6: Map of the Dutch railway network <ref name=Spoorkaart>Spoorkaart 2019, NS, (2019). Retrieved from https://nieuws.ns.nl/download/611967/spoorkaart2019-231351.pdf?_ga=2.11350260.1376181486.1552737761-29200527.1538036593</ref>]] | |||
To keep the railway clean throughout the day, the users will need to implement and use a minimum amount of these cleaning machine. The amount of cleaning robots that is needed per day is dependent on the weather situation. During the summer season the expected maintenance problems with leafs are lower than during the Autumn season. Therefore, to estimate the amount of robots that the users will need, the situation with the most extreme weather conditions will be considered. In these conditions the estimation was made that it would be optimal to let one robot attach to a train for each different train path. This choice was made, as it will cover the whole Dutch railway network, as can be seen in Figure 6. It was found that there are 127 different train lines in the Netherlands <ref name=Trainlines>Dienstregeling 2019, OV in Nederland, (2019). Retrieved from http://wiki.ovinnederland.nl/wiki/Dienstregeling_2019#Treinseries</ref>. From these 127 different train lines, 2 are Thalys high speed trains which travel to France, 2 are ICE high speed trains which travel to Germany, and 9 stop trains are all the way connected to Germany or France. Hence, 114 trains are traveling only on the Dutch railway network. However, 39 of these trains are Intercitys, which drive on the same railroad network as the Sprinter trains. Therefore, it is more efficient to not attach the robot to these Intercity's, as it is not necessary to clean the same railway track twice as much. As a result, at least 75 cleaning machines need to be implemented, but there need to be extra reserve robots in case of emergency. Hence, one extra robot will be distributed to the five biggest train station in the Netherlands. These include the station in Amsterdam, Utrecht, Rotterdam, Den Haag, and Eindhoven <ref name=Stations>Grootste treinstations Nederland, treinStationInfo, (2019). Retrieved from https://www.treinstationinfo.nl/treinreizen/grootste-treinstations-nederland/</ref>. As a result at least 80 robots will be needed for the users. | |||
==How much time does it take?== | |||
Currently the coupling of trains takes approximately 1 minute. However, if a coupling system with transitional coupler will be used, this will take slightly longer, but it will not interfere or delay the usual traveling times. For an optimal cleaning of the railways in the Netherlands, the robot will be attached every 6 hours on a train on each different Sprinter train line. Attaching it to every driving train cannot be possible due to the costs. The first robot will be attached to the first trains that drive after the night schedule, which is around 5:30. Then the robots will be attached again every 6 hours, if necessary. Thus, the robots will be active around 5:30, 11:30, 17:30 and 23:30. This schedule makes sure that the first and last active trains of 5:30 and 23:30 of each day will be attached with a cleaning robot. Furthermore, the morning rush hours of 6:00-9:00 and afternoon rush hours of 16:00-18:00 will each contain one cleaning robot with this schedule <ref name=RushHours>Spits, OV in Nederland, (2019). Retrieved from http://wiki.ovinnederland.nl/wiki/Spits</ref>. As a result, attaching the robot every 6 hours to passenger trains will be the most effective time schedule with regards to the efficiency and cost. | |||
==How will they use it?== | |||
The users can use the robot by attaching it to the passenger trains before the passenger train starts riding at the first station. Afterwards the robot will be detached when the cleaning is done at the the end station. The robots can be stored efficiently due to the relatively small sizes compared to passenger trains. | |||
=Obstacles= | |||
==Track Maintenance== | |||
Before investigating what problems can occur on the rails, it is useful to take a look at who is responsible of tackling these issues. | |||
For small-scale track maintenance, ProRail hires approved rail contractors who can maintain the track for them <ref name = trackmaintenance> Track maintenance PBL https://www.prorail.nl/rereizen/aanbesteden-en-inkoop/spooronderhoud-pgo? </ref>. To be recognized by ProRail, parties must have specific technical, professional and organizational skills and requirements. These can be found on the ProRail site. A list of approved entrepreneurs can also be found on the ProRail site <ref name = accreditedentrepreneurs> List of accredited entrepreneurs https://www.prorail.nl/sites/default/files/lijst_erkende_ondernemers_01-02-19.pdf </ref>. After the rail contractor has been recognized by ProRail, a public contract is signed in which the required performance is prescribed, not the required effort (as before). The idea behind this is that this should lead to more proactive maintenance and this should lead to an increase in availability and quality of the tracks. These contracts have a duration of 10 years and are called ‘Prestatie Gericht Onderhoud’ contracts (Performance-oriented Maintenance contracts or PGO contracts). | |||
Pilots were started in 2014 to work with this new form of contracts. The number of disruptions decreased in the areas of these pilots. ProRail says that in the coming years all maintenance areas will use these PBL contracts. | |||
In addition, ProRail has developed a new standard framework that should make it clearer when maintenance is needed and when the track can be used (limitedly) and when not. In addition, it will also become clearer who is responsible and when; ProRail or the contractor. | |||
The aforementioned list of accredited entrepreneurs shows that ProRail recognizes 4 companies in the field of track maintenance. These are: Asset Rail, Bam Infra, Strukton Rail and VolkerRail. | |||
Contacting VolkerRail has proven very helpful in gaining a better understanding of what the problems on the tracks are and how these are tackled. This will be discussed below. | |||
==Snow== | |||
===Problem=== | |||
In very cold periods like in the winter, snow and ice can build up on the tracks. The ice can block movable parts of the track (switches) and coat over the power lines or the third rail, preventing trains from drawing the power they need to move. Also, icicles on bridges and tunnels can cause serious damage to passing trains. All these problems can cause the trains to have delays. <ref name=keepmoving> keeping trains moving during snow and ice by NetworkRail. (2017) https://www.networkrail.co.uk/feeds/keeping-trains-moving-snow-ice/ </ref> | |||
When a train has to slow down as it approaches a station, snow gets compressed and can turn into solid ice. This does not just clog that area, but the ice can also coat the rails, which disconnects the trains from getting the required power. Ice sheets are a risk for dislodging and damaging trains. The steel rails can freeze together when it gets to cold. This is what makes the signals stay red and prevents the trains from moving. When snow drifts are deeper than 30 cm , trains can no longer run safely unless they have snow ploughs <ref name=winterweater> Winter weather can present some real challenges, NetworkRail(2017). https://www.networkrail.co.uk/running-the-railway/looking-after-the-railway/delays-explained/snow-and-ice/ </ref>. Fortunately, this is rare in the Netherlands. | |||
===Solution=== | |||
====Bleach, Salt==== | |||
Using these products we can lower the rate of freezing cause during the freezing and melting process some water molecules freeze while others melt, replacing each other in a state of equilibrium, while when one of these products are added in the mixture it disrupts this equilibrium. | |||
<ref name=meltice> The best way to melt ice without heat. By Jason Gabriel (April 24, 2017) https://sciencing.com/way-melt-ice-heat-5505463.html </ref> | |||
====Laser==== | |||
CO2 Lasers can be used to melt ice and snow with a wavelength of 10.6 μm, which ice strongly absorbs, to drill (via melting) through ice. The resulting drilling speed is measured at several irradiation intensities, ice-snow densities, and beam angles relative to the horizontal axis. The speed increases nearly in proportion to the laser intensity. | |||
<ref name=lasermelt> Studies of melting ice using CO2 laser for ice drilling. By T.Sakurai,H.Chosrowjan,T.Somekawa,M.Fujita,H.Motoyama,O.Watanabe,Y.Izawa (October the 8th, 2015) https://www.sciencedirect.com/science/article/pii/S0165232X15002116 </ref> | |||
For the laser to be able to remove the snow, it must be able to handle the maximum snowfall <ref name=snowfall> weather station Westland - De Poel http://www.westland-depoel.nl/vantagevue/ws/wxclimate2.php </ref> in the last 7 years the maximum snowfall on a day is 8cm on the 14th of January 2013. We first want to know how much snow the laser should be able to melt in a second. | |||
We calculate it by looking at the speed of the train which is 160 km/h, or 44.44 m/s. The width of the head of the tracks is 72 mm (HSL, high-speed tracks). Considering a layer of 4 cm of compact snow on the tracks, the train would be going through 25.57 kg of snow per second. The laser needs to be able to melt all this snow in order for the concept to work. The energy required to melt 25.57 kg of snow is 534413 J/s, considering -10 degrees Celcius. To generate this energy, the wavelength of the photons has to be 3.717*10^-31 m, resulting in a frequency of 8.065*10^38 Hz. The wavelength we get are corresponding to the wavelength of Gamma-rays. Lasers having Gamma-rays are at the moment still not developed as it still is a challenge for scientists however in the futur it might be possible according to Cordis <ref name=Cordis> Gamma-ray laser moves a step closer to reality by university college London (April 18th 2018) https://cordis.europa.eu/project/rcn/195403/brief/en </ref>. | |||
====Snow Plough==== | |||
A snow plough can be used to clear the train rails when there is more than 30 cm of snow, we could use this one the robot to make it possible to clear the rails for other trains, at the moment this is already installed on normal trains when the snow is higher than 30 cm. | |||
<ref name=keepmoving> keeping trains moving during snow and ice by NetworkRail. (2017) https://www.networkrail.co.uk/feeds/keeping-trains-moving-snow-ice/ </ref> | |||
==Ice== | |||
===Problem=== | |||
In colder periods, rain with a temperature around 0 ℃ can form glaze (ijzel). There is an important distinction between glaze and frost, which forms from water vapor that comes in contact with a solid surface. Frost is usually not a big problem for trains. It may cause some sparks at most, but this is not problematic <ref name = ontijzelschakeler> Ontijzelschakelaar https://energievoorziening.funnymedia.nl/onderdeelvdmaand/ontijzelschakelaar/ontijzelschakelaar.htm </ref>. Glaze on the other hand is cause for some serious concern, because, in the right conditions, it can form a layer of ice on the catenary. This may prevent the trains from receiving electricity, which makes them useless. Unfortunately, combatting this problem is not the focus of this project. | |||
Ice can also freeze the switches together, which prevents trains from switching tracks. The effects of ice can be harmful for trains and can cause some serious delays. | |||
===Solutions=== | |||
In theory, ice can thus be harmful for the tracks. However, according to a source at VolkerRail, ice is not a big problem in the Netherlands. Very low temperatures a rare in this country, which means that the layer of ice on the tracks and catenary is thus often very thin. Since the trains on the Dutch railway are rather heavy, the ice is crushed or pushed away. This information has led us to conclude that it was not worth focussing on solving the ice issue. The solutions mentioned below are thus not integrated in the final concept. | |||
====Switch Heating==== | |||
Ice or snow on the switches can still be harmful though. The way ProRail currently tackles this by making use of switch heating. This heating melts the snow and ice and thus making it harmless. There are four different kinds of switch heating <ref name=wisselverwarmingtypes>Wikipedia (2019) Wisselverwarming https://nl.wikipedia.org/wiki/Wisselverwarming</ref>, these are explained in appendix E. Currently 6.500 of the in total 8.900 switches are equipped with switch heating <ref name = Wisselverwarming> Wisselverwarming https://web.archive.org/web/20090308032821/http://www.prorail.nl/WeerenSpoor/Pages/Wisselverwarming.aspx</ref>. This works rather well, if the snow does not pile up too high, but as mentioned before, this does not occur very often. | |||
The heaters are also prone to malfunctions. When this happens, staff is deployed to melt the snow and ice away with gas burners or to blow the snow away with leaf blowers. Our source stressed however that these are emergency measurements and that this should be prevented. The contractors have to make sure that the heaters function correctly during the ‘heating season’ (stookseizoen). This is from the 15th of October until the 15th of April. | |||
====Laser==== | |||
We wanted to check whether we could use a laser to melt ice, just like we did for snow. It would be more logical to use a laser to melt ice, since icing is generally more common than snowfall and a layer on the tracks shouldn't be thicker than a millimeter. So considering 1 mm of ice on the HSL tracks, a train would pass 2.93 kg of ice per second. To calculate the energy needed to melt this amount of ice, temperature needs to be estimated so it's assumed to be minus 10 degrees Celcius. The laser would need to output 61764.4 J every second. Using the speed of light and Planck's constant, the corresponding wavelength can be calculated. This wavelength is 3.216*10^-30 m, which is really small. The frequency is then 9.321*10^37 Hz, so only a factor 10 smaller than the frequency required to remove snow. This is therefore not a viable option, since these frequencies for photons are way too high. | |||
==Leaves== | |||
===Problem=== | |||
In the Autumn trees will drop their leaves which might land on the railway. At first the leaves will not cause any trouble, but during the day they will cause problems. If the leaves which landed on the railhead become moist and heavily compressed by the passing trains, they will result in a low-friction coating. Due to this low-friction coating the railway becomes slippery and the wheels of the train starts to block when it is starting to brake. Due to this blocking one side wheels will experience more wear than the other sides which results in “square-wheels” <ref name=metro_blaadjes>A.Pel (2016) Die rotblaadjes op het spoor; waarom doen ze niets? https://www.metronieuws.nl/nieuws/binnenland/2016/11/die-rot-blaadjes-op-het-spoor-waarom-doen-ze-niets</ref>. These “square-wheels” need to be repaired in workshop which costs time and money. Due to the malfunctioning and repairing of the train wheels less trains will be deployed on trajects which is not preferred by the travellers. Another problem due to the low-friction coating is that it can take up to 800 meters extra to come to a total stop <ref name=railway_laserleaves>Railway Technology (2007) Tackling a Leafy Issue https://www.railway-technology.com/features/feature1457/</ref>. | |||
===Solutions=== | |||
====Leaf Blower==== | |||
A leaf blowers is used to blow loose leaves away from their initial position. This could be useful for the trains because they can blow the leaves away from the railhead. But this is not an option anymore. Due to the high compressing the leafy moist is stuck to the railway, therefore the leaf blower is not able to blow the leafy moist away <ref name=metro_blaadjes />. | |||
====Pressure Washer==== | |||
A pressure washer is used to clean object from a dirty layer which is stuck to the surface. Therefore the pressure washer can be used to remove the compressed layer of leaves from the railway. An example of a product which is already tested is the Nilfisk-ALTO developed by Nilfisk-Advance for the Banedanmark, the railway organization in Denmark. The Nilfisk-ALTO has a 7000 liter water tank and operates at a pressure of 500 bar and sprays 40 L/min. The wagon achieved to clean the railway from the leaves when it runs at an operating speed of 45 km/h <ref name=nilfisk_pressure>Nilfisk (2010) High pressure washer on track https://www.nilfisk.com/en/news/Pages/HPW_on_wheels.aspx</ref>. Due to the large amount of water that needs to be stored the pressure washer is not an option for the DagBlad. The DagBlad is attached to the front of a train during the day and therefore a container filled with 7000 liters of water will impedes the view of the machinist. | |||
====Traction Gel Applicator==== | |||
Traction gel applicator (TGA) is a substance which consists out of sand, metal particles and starch <ref name=prorail_gel>Prorail (2013) Sandite: slim recept tegen blad op het spoor https://www.prorail.nl/nieuws/sandite-slim-recept-tegen-blad-op-het-spoor</ref> . The TGA system consists of a sensor and 50 meters further the cabinet. The cabinet contains the electronics, a pump, a delivery hose, the substance and is solar powered. The sensor, which gets triggered by the wheels of the train, sends a signal to the cabinet that a train is coming. The pump of the cabinet then places some TGA on the railhead via a delivery hose. When the train passes the cabinet the TGA gets stuck on the wheels and this gives the train more traction for a short distance, 60 to 200 meters <ref name=gel_pdf>DIPOSTEL, Datasheet: Traction gel http://dipostel.com/wp-content/uploads/2017/01/gel-de-traction_ang.pdf</ref>. Due to this short distance the TGA cabinets are typically placed at the entries and exits of a train station <ref name=TGA>jsdrail, Traction Gel Applicators http://www.jsdrail.com/engineering/traction-gel-applicators/9.htm</ref>. | |||
====Sweeper==== | |||
[[File:LSRPM132M_sizes.png|thumb|270px|Figure 7: The horizontal sizes of the LSRPM 132 M]] | |||
[[File:breedte_wijdte_en.png|thumb|300px|Figure 8: The width and space of a railway]] | |||
[[File:Pulley_allignment.png|thumb|300px|Figure 9: The pulley alignment of the LSRPM 132 M using a belt]] | |||
[[File:height_leaves.png|thumb|300px|Figure 10: The height of the leaves on the railhead]] | |||
[[File:meting_1.png|thumb|300px|Figure 11: The different lengths which are used in the calculations]] | |||
[[File:Td-Pa.png|thumb|300px|Figure 12: The relation between the pressure in megaPascal '''''MPa''''' and the developed torque in Nm '''''Td''''']] | |||
[[File:P-Td.png|thumb|300px|Figure 13: The relation between the developed torque in Nm '''''Td''''' and the power in megaWatt '''''MW''''']] | |||
A sweeper can be used to remove dirt from surfaces. The brushes can be made out of metal (steel), polypropylene or from pig’s hair. For brushes used to clean the railway the bristles are made out of steel or polypropylene and the sweeper operates at a high torque which makes it possible to remove snow, coal, stones, dust, sand, leaves, trash and dirt<ref name=rail_sweeper>Railroad Tools and Solutions (LLC), Rail Sweeper http://www.rrtoolsnsolutions.com/PowerTools/rail-sweeper.asp</ref>. | |||
When the high-speed train is left out of the scope the maximum speed a train can achieve in the Netherlands is 160 km/h <ref name=NS_snelheid>Nederlandse Spoorwegen (NS), Hogesnelheidslijn | |||
https://www.ns.nl/over-ns/dossier/hogesnelheidslijn</ref>. This means that the brushes have to rotate at a speed higher than 160 km/h. For this research a minimum speed of 200 km/h is a requirement for the brushes. If the brush is placed horizontally a common diameter of the broom is 915 mm, the broom diameter of the Dymax rail sweeper is equal to 915 mm<ref name=dymax>Dymaxinc, Dymax rail sweeper for skid steers | |||
https://dymaxinc.com/attachments/dymax-rail-sweepers/</ref> and the diameter of the KM90/120 is also equal to 915 mm<ref name=Overaasen>Overaasen Snowremoval Systems, Railroad Brushes (KM90, 2KM90H and KM120H) | |||
https://www.overaasen.no/railroad_equipment/brushes/railroad_brush/</ref>. Therefore the brush diameter of the DagBlad is fixed at 915 mm if the sweeper is placed horizontally over both railheads. Most motors have their speed specification in rotations per minute (RPM). The speed in km/h of the motor depends on, in this case, the diameter of the brushes. The diameter is fixed at 915 mm and the minimum speed is 200 km/h therefore the minimum RPM can be calculated using the following equation | |||
<center> | |||
'''''v = d x RPM x 0,001885''''' (1) | |||
</center> | |||
where '''''v''''' is the speed in km/h, '''''d''''' is the diameter in cm and '''''RPM''''' is the speed in rotations per minute. | |||
Using 200 km/h and 915 mm for the diameter a minimal RPM of 1160 is needed to operate at a sufficient speed. When searching for already used rail sweepers the RPM is too low to use in our robot. After some research the LSRPM 132 M permanent magnet synchronous motor (PMSM) was found which has the following important specifications in the operation range of 1500 RPM<ref name=LSRPM132M>LSRPM - Dyneo, Permanent magnet synchronous motor 3 to 350 kW - 1500 to 5500 RPM | |||
http://www.leroy-somer.com/documentation_pdf/4936_en.pdf</ref>: | |||
*Rated power P_n = 12 kW | |||
*Efficiency η = 92,0 % | |||
*Rated torque T = 69 Nm | |||
*Rated current I = 21 A | |||
*Weight = 49 kg | |||
The sizes are shown in Figure 7. | |||
The RPM of a motor can be obtained using the following equation | |||
<center> | |||
'''''RPM =P/T''''' (2) | |||
</center> | |||
where '''''P''''' is the power in Watts and '''''T''''' is the torque in Nm. Filling in the data of the LSRPM 132 M a RPM of 1660 is obtained. Converting this RPM into km/h using (1) gives 286,44 km/h. This is a high enough speed to operate which means that the motor is also able to operate at a lower RPM which consumes less power, this also results in a lower required current. | |||
Another possible placement of the sweeper is to place it vertical and use two sweepers instead of one. The new diameter of the brushes is determined using the knowledge about the railway. The railway has an inside width of 1435 mm and a heart-to-heart width of 1500 mm <ref name=Gauges/>. This means that the width between the outsides of the railway is equal to 1565 mm, this is also show in the Figure 8. To clean the rail-head from the compressed leaves and the snow, which also lays between the two rail-heads, the diameter of one sweeper has to be half the width of the outside to outside. The minimum diameter which cleans the whole surface is equal to 782,5 mm. To foresee a problem which is caused by the brushes touching each other a diameter of 770 mm is used. | |||
The advantages of placing the brushes vertical is that less torque is needed per sweeper because the two sweepers now clean one railhead each instead of one sweeper two railheads. Another advantage of using two sweepers is that it is not needed to place the sweeper a bit diagonal. When a horizontal sweeper is used it is needed to place it a bit diagonal to move the leaves, but mostly the snow, next to the railway. If the sweeper is not placed diagonal the leaves and snow are only moved forward which means that the sweeper is constantly removing the same leaves and snow. By using the vertical sweepers the leaves and snow are moved to the direction in which the brush is rotating. This means that, from the perspective of the machinist, the left brush has to rotate counterclockwise and the right brush clockwise to move the leaves and snow next to the railway. | |||
The power transfer from the motor to the brushes will be done using a belt which is also suggested in the data sheet of the LSRPM PMSM <ref name=LSRPM-data>Leroy-Somer, Installation and maintenance LSRPM - PLSRPM | |||
http://www.leroy-somer.com/documentation_pdf/4155_en.pdf</ref>. The exact placement of the belt is shown in Figure 9. On one side of the motor an extra gear is needed to make the brush rotate counter-clockwise. | |||
The next important part of the sweeper is the material of the brushes. Common materials for the bristles are steel and polypropylene. The leaves are highly compressed and therefore strong bristles are needed. Steel bristles are strong but also affect the railway itself, metal on metal friction. The goal is to remove the leaves from the railhead while the rail itself in not additionally damaged, therefore the steel bristles are no option. Polypropylene can be soft but also hard, for our problem the hard polypropylene is the solution. | |||
The required specifications of the motor are calculated in the following parts. | |||
=====Pressure===== | |||
The leaves are compressed to the railhead by the trains themselves. To calculate the maximum pressure in Pascal that the leaves are compressed the surface and the weight have to be calculated. | |||
The four-coach configuration of the Regiorunner weighs 226 ton<ref name=NS-gewicht>Kleinetrein, Electric coach-units of the Nederlandse Spoorwegen (Dutch railways) http://www.kleinetrein.nl/spoors_1704/nsm_html/dutch/nsm_eltr.html</ref>. Every waggon has 8 wheels which means a total of 32 wheels for the four-coach configuration. | |||
Dividing the total weight over the wheels gives a weight of 7062,5 kg per wheel. | |||
The diameter of one wheel is 1000 mm<ref name=NS-diameter>Tom, Topic: Wieldiameter goederen wagons NS https://forum.beneluxspoor.net/index.php?topic=46384.0</ref>, this gives a wheel radius of 500 mm. To calculate the area which is compressed by the train the height of the leaves on the railhead needs to be known. A research of L. R. Goodes, T. J. Harvey, N. Symonds and T.G. Leighton on the leaves on the railhead shows a diagram shown in Figure 10 which displays the height of the leaves<ref name=leaves-railhead>L. R. Goodes, T. J. Harvey, N. Symonds and T.G. Leighton, A comparison of ultrasonically activated water stream and ultrasonic bath immersion cleaning of railhead leaf-film contaminant https://www.researchgate.net/publication/304811807_A_comparison_of_ultrasonically_activated_water_stream_and_ultrasonic_bath_immersion_cleaning_of_railhead_leaf-film_contaminant</ref>. From Figure 10 can be concluded that the highest point is 20 µm which will be used in the following calculations. An illustration of the lengths for the following calculations are shown in Figure 11. First the height '''''a''''' between the middle of the wheel and the highest point of the leaves is calculated using | |||
<center> | |||
'''''a = r-h''''', (3) | |||
</center> | |||
where '''''r''''' is the radius of the wheel and '''''h''''' is the highest point of the leaves on the railhead. Then the length from the middle of the wheel to the point where the radius '''''r''''' achieves the height '''''a''''' can be determined using pythagoras | |||
<center> | |||
'''''b = sqrt[(r^2)-(a^2)]'''''. (4) | |||
</center> | |||
Using the length '''''b''''' the total length which compresses the leaves '''''L''''' can be calculated using the following equation | |||
<center> | |||
'''''L = 2b'''''. (5) | |||
</center> | |||
To calculate the area '''''A''''' which is compressed by the train the length ''''L''''' is multiplied by the width of the railhead '''''w''''' | |||
<center> | |||
'''''A = L x w'''''. (6) | |||
</center> | |||
To calculate the pressure which is expressed on the leaves the weight per wheel has to be converted from kg to Newton which is done with the following equation | |||
<center> | |||
'''''N = 9.81 x M_w''''', (7) | |||
</center> | |||
where '''''N''''' is the weight per wheel in Newtons and '''''M_w''''' is the weight per wheel in kg. The pressure '''''Pa''''' in Pascal is finally determined using | |||
<center> | |||
'''''Pa = N/A'''''. (8) | |||
</center> | |||
When the train has passed the pressure on the leaves will decrease but the leaves are more stuck to the railhead than before. When the leaves are wet some amount of water is pressed out of the leaves which makes it stuck even more to the railhead. | |||
=====Torque===== | |||
The torque depends on how heavy or stucked the leaves are to railhead. In this calculation the torque is determined using bristle material which does not bent, this means that for the real-world problem the required torque is higher than calculated. First the effective radius of the sweeper which cleans/moves the leaves is calculated. In the most extreme case this is equal to half the width of the railhead. This is then multiplied by the mass of the of the compressed leaves. This will lead to the following equation | |||
<center> | |||
'''''Td = N x w/2''''', (9) | |||
</center> | |||
where '''''Td''''' is the required developed Torque, '''''N''''' is the mass of the compressed leaves in Nm and '''''w''''' is the width of the railhead. Figure 12 shows the relation between the pressure in megaPascal '''''MPa''''' and the developed torque in Nm '''''Td'''''. The shaft torque '''''Ts''''' is determined using the efficiency of the motor which will be equal to the efficiency of the LSRPM 132 M, in this case 92.0%<ref name=LSRPM132M/>. The equation for the shaft torque is equal to | |||
<center> | |||
'''''Ts = Td/efficiency''''', (10) | |||
</center> | |||
== | =====Power===== | ||
The | The required power is determined using the fixed speed in RPM calculated with (2). The equation for the power will look like this | ||
<center> | |||
'''''P = Ts x RPM'''''. (11) | |||
</center> | |||
The relation between the developed torque in Nm '''''Td''''' and the power in megaWatt '''''MW''''' is shown in Figure 13. | |||
=====Conclusion===== | |||
When the equations are filled in with the data from the Regiorunner and the knowledge from the research of of L. R. Goodes, T. J. Harvey, N. Symonds and T.G. Leighton on the leaves on the railhead<ref name=leaves-railhead/> a pressure of 59,5859 MPa is found. This leads to a required developed torque of 4503,4 N/m. When the speed of the sweeper is fixed at 200 km/h a required power of 6,2054 MW is obtained. The full implemented calculation can be found in appendix B. The LSRPM 132 M permanent magnet synchronous motor does not have the required specifications; it has a to low power and torque. The required power which goes into the megaWatts in not possible together with a developed torque of 4503,4 N/m and therefore the sweeper will not be used in the final product. | |||
In short, the, not yet possible, requirements of the motor to use a sweeper as a removal system for the leaves are | |||
*Power = 6,2054 MegaWatts | |||
*Torque = 4503,4 Nm | |||
*RPM = 1377,9 RPM | |||
====Laser==== | |||
[[File:laserrustremoval.jpg|thumb|280px|Figure 14: A visual representation of the laser removal system]] | |||
Lasers are used for all kind of operations but when operating at a wavelength of 1064 nm it becomes useful for the railway. Due to a carefully designed optical set-up of mirrors and lenses the laser was able to produce a series of pulses, 25.000 per second. At this wavelength the laser clears the track from debris. The highly compressed leaves on the railway absorb the pulses, which leads to a temperature of 5000 Celsius degrees. Due to this high temperature the leaves heat up rapidly which causes it to expand and getting lifted from the railhead<ref name=railway_laserleaves />. Research from Mr. Higgins with TU Delft showed that the desired outcome is achieved even at a speed of 50 mph (80,47 km/h)<ref name=TU-Delft-laser>R. Gray, End of the line for autumn train delays? Dutch begin trails to zap leaf litter from the track with LASERS https://www.dailymail.co.uk/sciencetech/article-2860418/End-line-autumn-train-delays-Dutch-begin-trials-zap-leaf-litter-tracks-LASERS.html</ref>. The Sprinters from the NS have a maximum speed of 160 km/h<ref name=NS_snelheid/> which is double the experiment speed. This means that it needs to be checked if the leaves are heated up strong enough to get lifted from the track using the same laser. The equations are shown in the next section and the full work-out, which also displays the equations a lot clearer, can be found in Appendix C. | |||
=====Time===== | |||
To calculate the new temperature when the train travels at 160 km/h the discrete step pulses '''''I''''' needs to be determined using the knowledge from the experiment at 50 mph. The first thing which needs to be done is to convert the speed from mph to m/s which is done by using the following equation | |||
<center> | |||
'''''v = (mph/0,6213711922)/3,6''''', (12) | |||
</center> | |||
where '''''v''''' is the speed in m/s. Using this speed and the knowledge from the laser the pulses per meter can be determined using | |||
<center> | |||
'''''p_m = p/v''''', (13) | |||
</center> | |||
where '''''p_m''''' is the pulses per meter and '''''p''''' is the amount of pulses per second. The time which the surface receives a pulse '''''t''''' is then equal to | |||
<center> | |||
'''''t = p_m/p'''''. (14) | |||
</center> | |||
== | =====Discrete Step Pulses===== | ||
The discrete step pulses '''''I''''', which is time dependent, is determined using the knowledge and data from the experiment<ref name=TU-Delft-laser/> and the calculated time '''''t'''''. The discrete step pulses '''''I''''' is obtained using | |||
<center> | |||
'''''I = (T.*λ.*δ)./((2./sqrt(π)).*sqrt(t)+(e.^t).*erfc(sqrt(t)-1))''''', (15) | |||
</center> | |||
where '''''T''''' is the temperature in kelvin, '''''λ''''' is the thermal conductivity which is 0,54 for water infiltrated leaves<ref name=TC-leaves>Hays, R.L. Planta (1975) 125: 281. https://doi.org/10.1007/BF00385604 </ref> and '''''δ''''' which is the wavelength in meters and for this laser equal to 1064 nm. The discrete intensity function '''''id''''', which is also time dependent, is equal to | |||
<center> | |||
'''''id = Tdes/(2/sqrt(pi))*sqrt(t)+ (e.^t).*erfc(sqrt(t)-1)''''', (16) | |||
</center> | |||
where '''''Tdes''''' is the desired temperature in kelvin, in this case 5273 K. With this data the discrete constant '''''I_0''''' is obtained using | |||
<center> | |||
'''''I_0 = I/id'''''. (17) | |||
</center> | |||
With the constant now known ('''''I_0''''' = 5,7456 x 10^-7) the discrete step pulses '''''I''''' can be obtained for the new speed which is 160 km/h. | |||
== | =====Temperature===== | ||
{| class="wikitable" | border=" | The increase in temperature of the surface is obtained using | ||
<center> | |||
'''''T = ((I)./(λ.*δ)).*((2./sqrt(pi)).*sqrt(t)+(e.^t).*erfc(sqrt(t)-1))'''''. (18) | |||
</center> | |||
For the experiment '''''T''''' was already know, 5273 K, but for the new speed this temperature is used as the desired temperature '''''Tdes'''''. The temperature which is reached in the time that the laser is active is determined using the calculated time and discrete step pulses. | |||
=====Conclusion===== | |||
With a research from M. Kalyon and B.S. Yilbas on laser pulse heating<ref name=laser-heating>Kalyon, M & Yilbas, Bekir. (2003). Laser pulse heating: A formulation of desired temperature at the surface. Optics and Lasers in Engineering - OPT LASER ENG. 39. 109-119. 10.1016/S0143-8166(02)00088-X.</ref> the new temperature when driving 160 km/h could be obtained. When the calculations are performed and discrete constant '''''I_0''''' is determined the newly reached temperature '''''T''''' can be calculated. The newly reached temperature '''''T''''' is equal to almost 5000 Celsius degrees. The difference in a percentage is -1,7248 x 10^-14 % which is really small. This means that a laser can theoretically be used at a speed of 160 km/h. The reason that the difference in temperature is really small is due to the fact that a laser travels at the speed of light (3 x 10^8 m/s). The increase of speed from the train (22.1 m/s) almost fully disappears in ratio with the speed of light. A visualisation of how the laser will work is shown in Figure 14. | |||
=====In Practice===== | |||
The calculations above show that it is theoretically possible to lift the compressed leaves from the railhead but in practise some extra instruments are needed. In the calculations the assumption was made that there were no other obstacles covering the compressed leaves on the railhead. In practise other not yet compressed leaves and/or a thin layers of snow are covering the compressed leaves from the laser. To make sure the compressed leaves are not covered a brush is placed in front of the laser. This brush cleans the the railhead from the not yet compressed leaves and the thin layers of snow. The laser can now directly hit the compressed leaves which will make them expand and get lifted from the railhead. The next thing is that the leaves are now lifted from the railhead but not yet removed. To make sure the leaves are removed from the railhead another brush is placed behind the laser. In the previous section about the sweeper is was concluded that a sweeper is not able to remove the compressed leaves from the railhead. This is still true but in this case the compressed leaves are not compressed anymore because they are lifted from the railhead. The required torque to remove the leaves from the railhead is now way less than when the leaves are compressed. The DagBlad still uses one motor to operate all the four brushes (left and right railhead, in front and behind the laser) which means that the new requirements for the motor have to be calculated. The difference between the previous calculations for the motor requirements is that for this calculation the pressure is not taken into account, the leaves are already lifted from the railhead, and that the mass of just the leaves and snow is used. | |||
=====Mass===== | |||
To calculate the new requirements of the motor the mass of the leaves and snow has to be calculated. The weight of compacted or wet leaves is equal to 550 lb. per cubic yard and the weight of loose and dry leaves is equal to 150 lb. per cubic yard<ref name=weight-leaves>EFCO Company, Swaploader “Hooked on Quality”, Cubic Yardage calculation sheet https://www.swaploader.com/wp-content/uploads/2015/02/Cubic_Yardage_Chart.pdf</ref>. As a rule of thumb snow has a weight of 20 pounds per cubic foot<ref name=weight-snow>Evogov, How Much Does Snow Weigh? https://evogov.s3.amazonaws.com/141/media/109213.pdf</ref>. Cubic foot is converted to cubic yard using | |||
<center> | |||
'''''CY = CF x 0,037037037''''', (19) | |||
</center> | |||
where '''''CY''''' is the volume in cubic yard and '''''CF''''' is the volume in cubic foot. To convert the volume from cubic yard to cubic meter the following equation is used | |||
<center> | |||
'''''CM = CY/1,3080''''', (20) | |||
</center> | |||
where '''''CM''''' is the volume in cubic meter. The weight of the leaves and snow is also given in pounds but in this case it is easier to convert them into kilograms before continuing the calculations. This is done by using the following equation | |||
<center> | |||
'''''kg = lb x 0,45359237''''', (21) | |||
</center> | |||
where '''''kg''''' is the mass in kilograms and '''''lb''''' is the mass in pounds. The mass the brushes have to remove can then be calculated using the following equation | |||
<center> | |||
'''''M_x = w x h x d x CM x kg''''', (22) | |||
</center> | |||
where '''''M_x''''' is the mass which needs to be removed from one of the three obstacles, '''''w''''' is the width of the railhead, '''''h''''' is the height of the leaves or snow and '''''d''''' is the effective diameter of the brush. In this calculation the height is chosen to be the maximum value, so 20 um for compacted leaves, 8 cm for snow and for the loose leaves no data could be found so a value of 1 cm is used. The calculations for '''''M_x''''' has to done 3 times: for the compacted or wet leaves, loose and dry leaves and the snow. The total mass is then equal to | |||
<center> | |||
'''''M = 2 x (M_compacted_leaves + M_loose_leaves + M_snow)''''', (23) | |||
</center> | |||
where '''''M_compacted_leaves''''' is the mass of the compacted or wet leaves, '''''M_loose_leaves ''''' is the mass of the loose and dry leaves and '''''M_snow''''' is the mass of the snow that has to be removed. Finally the mass to be removed has to be multiplied by 2 because the motor will drive the brushes for the left railhead but also for the right railhead. The full calculation can be found in Appendix D. The new motor requirements are shown below when the brush rotates at a speed of 200 km/h and the efficiency is equal to 76%: | |||
[[File:brush.PNG|thumb|280px|Figure 15: The kind of brush the DagBlad uses]] | |||
*Power = 741,4328 Watt | |||
*Developed torque = 0,4089 Nm | |||
*RPM = 1377,9 RPM | |||
This is realistic and doable. It also shows that the LSRPM 132 M has specifications which are a lot higher which means a smaller and cheaper motor can be used. The new motor which is going to be used is the E2T IEC 80 M4D. This motor has the following specification<ref name=IEC80>Elsto Drives & Controls Stokvis Group, elektromotoren https://www.bruinaandrijftechniek.nl/wp-content/uploads/2015/03/Elektromotoren.pdf</ref> : | |||
*Power = 750 Watts | |||
*Torque = 0,5245 Nm | |||
*RPM = 1430 RPM | |||
*Efficiency = 79,6 - 76,0 % | |||
*Weight = 12,5 kg | |||
*Price = 140 euro<ref name=IEC80-prijs>Elsto Drives & Controls Stokvis Group, Prijslijst 4 https://docplayer.nl/24488165-Power-control-green-solutions-prijslijst-4-motoren-regelaars-servo-nederlands-t-31-0-f-31-0-e-elsto.html</ref> | |||
The laser that will be used is the Adapt Laser Systems Lasersystem CL 1000 with the following specifications<ref name=CL1000>Adapt laser systems, Lasersystem CL 1000 https://www.adapt-laser.com/lasersystem-cl-1000/</ref>: | |||
*Power = 1000 Watts | |||
*Electrical requirement = 3 x 480 Volts | |||
*25000 pulses/second | |||
*Weight = 1030 lbs | |||
The brush that is going to be used has a diameter of 770 mm. The bristles of the brush are made out of flexible polypropylene. Due to this flexible polypropylene bristles the railway itself is not damaged while the snow and leaves are removed from the railhead. The lifetime of polypropylene itself, without using it, is over 400 years<ref name=poly-life>Bio-tec, Lifespan of plastics http://www.goecopure.com/lifespan-of-plastic.aspx</ref>. The fact that the DagBlad is is using the brush to remove obstacles from the railhead the lifetime will be way less due to wear. The exact lifetime of the brushes is hard to calculate and not much information can be found about the wear on the internet. The company Johnston sweepers gives a 2 year 2000 hours warranty on their sweepers<ref name=johnstonsweeper>Johnston Sweepers, RS655 Sweeper http://johnstonsweepers.us/wp-content/themes/jna/documents/Johnston_specsheet_RS655.pdf</ref>. This means that an average sweeper from them needs to be able to operate 2000 hours. The DagBlad operates 10 hours per day which means in the worst case scenario the brushes operate for 9 hours, the 1 hour loss is for the stopping of the train and accelerating. This means that the brushes can survive for 222 days and then a replacement for the brushes is needed. The prices for the brushes from Johnston Sweepers cannot be found separately on the internet and therefore brush from another company is used as a reference. A brush from Ganesh Brush, which can be ordered in a customized size, has a price of 1800 Rs which is equal to €23,15<ref name=brushprice>Ganesh Brush, Sweeping Brushes https://www.brushmanufacturersindia.in/street-sweeping-brushes.html#sweeping-brushes</ref>, this means that the price for a brush from Johnston Sweepers will probably be €50,- due to the quality difference. When calculating the price for one year of sweeping the prices per brush will be €82,21. The DagBlad has 4 brushes and therefore the price for the brushes will be €328,83 per year. To determine the total weight of the sweeper structure the weight of the WSP24 - Walk Behind Sweeper is used which is equal to 133lbs<ref name=walksweeper>Sweepster by Paladin, Walk Behind Sweepers https://www.paladinattachments.com/sites/default/files/prod_lit/BR%20-%20SW%20-%20sweepers.pdf</ref>. The structure, including the motor and handlebars, has an approximate weight of 110 lbs which leaves 23 lbs for just the sweeper structure. This 23 lbs is equal to 10,5 kg which is reasonable. The DagBlad needs 4 brushes which means that the total weight of the sweeper structure is equal to 42 kg without the motor. | |||
==Rust== | |||
In the beginning of this project it was thought that rust also caused problems and that it should be removed with the use of the DagBlad. When we contacted Prorail it became clear that rust is not a critical problem, due to the continues driving of the trains, the rust has no time to be created. With this information it is decided not to focus on rust on the train tracks anymore. | |||
==Metal== | |||
Next to leaves, snow, ice and rust, loose metal objects can also form an obstacle on the railway. Currently, not much research or work is available on metal trash collecting on and around railway tracks. The main reason for this is that metal trash is not a common obstacle on the railway. Although, it does not form a significant problem yet, a solution to this problem was still analyzed to check whether implementing it would be beneficial or disadvantageous. So to clean the railway from these metal obstacles, a magnet can be used to collect all the trash. Magnets can attract other iron-containing materials, such as trash cans on the railway, which is useful when cleaning the railroads. An article published by ProRail in 2017 <ref name = metalcleaning> ProRail (2017) Magneettrein maakt spoor schoon https://www.prorail.nl/nieuws/magneettrein-maakt-spoor-schoon </ref> revealed that a machine is already being used to tackle this problem. Therefore, metal will not be focused on any further. | |||
=Component List= | |||
In this section of the wiki a list of necessary components for the DagBlad robot is shown. | |||
==Electrical== | |||
{| class="wikitable" | style:"vertical-align:top; | border="2" style="border-collapse:collapse"; dashed; | |||
! style="font-weight:bold;" | Product | |||
! style="font-weight:bold;" | Amount | |||
! style="font-weight:bold;" | Price per unit | |||
! style="font-weight:bold;" | Mass per unit | |||
! style="font-weight:bold;" | Picture | |||
|- | |- | ||
| E2T IEC 80 M4D<ref name=IEC80-prijs/> | |||
| style="text-align: center;" | 1 | |||
| style="text-align: center;" | €140,- | |||
| style="text-align: center;" | 12.5 kg | |||
| [[File:E2TIEC80.jpg|150px]] | |||
|- | |- | ||
| | | Coupler system type 430 | ||
| | | style="text-align: center;" | 2 | ||
| | | style="text-align: center;" | ~€16.500,- | ||
| | | style="text-align: center;" | Unk. | ||
| [[File:coupler430.jpg|150px]] | |||
|- | |- | ||
| | | Computer (Arduino UNO) | ||
| | | style="text-align: center;" | 1 | ||
| | | style="text-align: center;" | €12,99<ref name=arduino_uno_price> Conrad, Iduino Compatible board Iduino UNO R3 ATMega328 https://www.conrad.nl/p/iduino-compatible-board-iduino-uno-r3-atmega328-1465104?WT.mc_id=gshop&gclid=Cj0KCQjwnKHlBRDLARIsAMtMHDGfIcVg2R6ZtI5puNzpNAJn0stN2VyeKj4rQQ9TET6Xi9maPzRa3icaAvAVEALw_wcB&tid=958856870_59564775006_pla-633211923346_pla-1465104&WT.srch=1&vat=true&insert_kz=8J</ref> | ||
| | | style="text-align: center;" | 25 grams | ||
| [[File:arduino_uno_picture.jpg|150px]] | |||
|- | |- | ||
| | | UIC568 | ||
| | | style="text-align: center;" | 1 | ||
| | | style="text-align: center;" | ~€42,- | ||
| | | style="text-align: center;" | ~10 kg | ||
| [[File:uic568_picture.jpg|150px]] | |||
|- | |- | ||
| | | Adapt Laser Systems Lasersystem CL 1000 | ||
| | | style="text-align: center;" | 2 | ||
| | | style="text-align: center;" | €427.500,-<ref name=CL1000/> | ||
| | | style="text-align: center;" | 467,2 kg | ||
| [[File:CL1000laser.jpg|150px]] | |||
|} | |||
===Software=== | |||
For our robot to be functional, it must be able to perform several tasks, getting rid of the leaves and snow automatically by using it’s sweepers and lasers, for this we need to implement the computer system/brain of the robot such that it is able to do so. For this we program the robot using Arduino software, the software must be able to activate the sweepers and the lasers when the train is riding over 30 km/h. | |||
====Speed Sensors==== | |||
We get the information about the speed of the train <ref name=speedsensorsolutions> Sensor solutions for rail vehicles https://www.lenord.com/fileadmin/kundenbereich/dokumente/broschueren/BRO_railway-solutions_EN.pdf </ref> from the speed sensor that the train already has. <ref name=speedtrainsense> Rail and Transit speed sensors https://www.motionsensors.com/industry-expertise/rail-transit.shtml </ref> The train uses magnetic speed sensors <ref name=railwayspeedsensor> Railway speed sensors MTR series https://www.baumer.com/se/en/product-overview/rotary-encoders-angle-sensors/hall-and-speed-sensors/mtr-xxx/p/medias/__secure__/en_E_M_Hallsensoren_MTR_xxx_static.pdf?mediaPK=8799686524958 </ref> | |||
the technique is also known to be called the Hall Effect.<ref name=Halleffect> What is Hall Effect and How Hall Effect Sensors Work? https://www.youtube.com/watch?v=wpAA3qeOYiI </ref> | |||
The RPM is calculated by using a counter that counts the steps and the disk slots which is a constant that depends on of slots in the disk, we divide the counter by the disk slots and then do it times 360,00 as we want to know the rotation in hours instead of seconds. Once the number of rotations per hour is found and put into a float, the wheel diameter which is in millimeters times pi times the previous float will give us a new float giving us the number of millimeters the train rides in an hour therefore we divide this float by | |||
1 000 000 such that we get the speed of the train in km per hour.<ref name=carbotusingspeed> Build a Robot Car with Speed Sensors https://dronebotworkshop.com/robot-car-with-speed-sensors/#Step_4_8211_Install_the_Wheels_Rotary_Encoders_and_Sensors </ref> | |||
This information is already calculated by the computer system of the train also known as the Train Communication Network <ref name=TCN> Train communication network https://en.wikipedia.org/wiki/Train_communication_network </ref> where the data from all the wagons is stocked during a train ride. To be able to get this information to our computer system the robot will make use of the UIC568 cable, this is a cable used in the majority of the trains in Europe <ref name=UIC568> UIC 568 https://en.wikipedia.org/wiki/UIC_568#Train_communication_network </ref> these cables are also the cables used by the Train Communication Network to get data from it’s different wagons, like the wagon containing the speed sensor. Now that we are able to get the information from the Train Communication Network the program has a search speed method that will look for the speed of the train, this has to run in a loop such that it keeps the speed of the train up to date in the program however before rerunning the search speed method we use a while loop that checks if the speed of the train float is bigger or equal to 30,00 constant float. When the speed is bigger or equal to 30 km/h the robot should start the sweepers and lasers. | |||
====Sweepers & Laser==== | |||
The two sweepers have to rotate in continuous rotation movement we want the left sweeper to go counterclockwise and the right one clockwise this can be done by using to motors that have a different pulse, one at a puls of 1 ms and the other with a pulse of 2 ms however we thought that it would also be possible to use 1 motor for both of them, as we just have to add one extra gear for one of the sweepers. <ref name=servomotors> Using servo motors with arduino https://www.youtube.com/watch?v=kUHmYKWwuWs </ref> | |||
To activate the motor the program at first needs to be able to know on which pin it is connected, afterwards the connections to the motor driver are put in as integers for example int en = 10; in1 = 9; in2 = 8; then there is a function that has digitalWrite(in3 , High); and digitalWrite(in 4, Low); that are used to have the sweepers turning in the right direction instead of the opposite way, the digitalWrite( en, High); activates the motor which will then activate the sweepers, this function is beeing called when the while loop says that the speed of the train is above or equal to 30 km/h, while in the else part of the loop the digitalwrite( en , Low); which deactivates the sweepers. Also it is digitalwrite( en , Low) when the robot is just starting up. <ref name=carbotusingspeed> Build a Robot Car with Speed Sensors https://dronebotworkshop.com/robot-car-with-speed-sensors/#Step_4_8211_Install_the_Wheels_Rotary_Encoders_and_Sensors </ref> | |||
The Laser as shown in the referenrence <ref name=arduinolaser> Arduino Laser https://tkkrlab.nl/wiki/Arduino_KY-008_Laser_sensor_module </ref> has Pinmod(13 , output) in the setup class of the program which defines its position on the computer system. | |||
The Laser needs to be activated when the speed of the train gets higher or equal to 30 km/h so in that part of the program there is a digitalWrite(13, High); to activate the laser. In the else part of the loop we have digitalWrite(13, Low); to deactivate the laser, also it’s part of the start up of the robot as the lasers should be deactivated then. | |||
====Computer System==== | |||
The computer system that is going to be used for this project is an Arduino Uno however the motor and the laser are not going to be directly connected to the pins of the arduino as the arduino can not give an enough amount of Volt,<ref name=arduinovolt> Switch 3-phase power with Uno https://forum.arduino.cc/index.php?topic=338259.0 </ref> Ampere,<ref name=arduinoampere>Which is the maximum current Arduino Uno can endure? http://forum.arduino.cc/index.php?topic=301475.0 </ref> Watt to feed the laser and the motor therefore an intermediate switch or a mosfet can be used to solve this problem. <ref name=arduinovoltage¤t> Arduino Power, Current and Voltage limitations https://www.electricrcaircraftguy.com/2014/02/arduino-power-current-and-voltage.html </ref> | |||
==Non-Electrical== | |||
{| class="wikitable" | style:"vertical-align:top; | border="2" style="border-collapse:collapse"; dashed; | |||
! style="font-weight:bold;" | Product | |||
! style="font-weight:bold;" | Amount | |||
! style="font-weight:bold;" | Price per unit | |||
! style="font-weight:bold;" | Mass per unit | |||
! style="font-weight:bold;" | Picture | |||
|- | |- | ||
| | | Hard polypropylene brushes with diameter 770 mm including frame | ||
| | | style="text-align: center;" | 4 | ||
| | | style="text-align: center;" | ~€50,- | ||
| | | style="text-align: center;" | ~10,5 kg | ||
| [[File:brush.PNG|150px]] | |||
|- | |- | ||
| | | Bogie | ||
| | | style="text-align: center;" | 1 | ||
| | | style="text-align: center;" | ~€25.000,- | ||
| | | style="text-align: center;" | ~1.250 kg | ||
| [[File:jacobsbogie.jpg|150px]] | |||
|- | |- | ||
| | | Frame | ||
| | | style="text-align: center;" | 1 | ||
| | | style="text-align: center;" | ~€3.500,- | ||
| | | style="text-align: center;" | ~750 kg | ||
|- | | [[File:Prototyperobot.jpg|150px]] | ||
| | |||
| | |||
| | |||
| | |||
|} | |} | ||
== | ===Frame and Wheels=== | ||
* | A bogie is a chassis or framework that carries four wheels of a train. The bogie is attached underneath a train. Most of the trains of NS make use of the ‘Jacobs bogie’ (see picture), because it is safer, cheaper and quieter. The DagBlad will need a bogie as well. Since the NS uses the Jacobs bogie <ref name = jacobsbogie> An example of a Jacobs bogie https://commons.wikimedia.org/wiki/File:Jacobs_bogie_of_EER_300.jpg </ref>, it is convenient to use this type for the DagBlad as well. It is difficult to find a price range for bogies, but we estimate the cost for a new bogie at around €25.000,- <ref name = bogieprices> Bray, N., & Vincent, P. J. (2006). Bogie freight wagons of Victoria: A brief history. Sunbury, Vic.: Brief History Books. </ref>. However, NS stated that they revise old bogies and give them a second life <ref name = revisebogies> Revising old bogies https://www.ns.nl/over-ns/treinonderhoud/moderniseren.html </ref>. This means that the DagBlad could possibly make use of an used bogie, which saves a lot of money. | ||
If this is not possible each DagBlad will require a bogie. A bogie is estimated to last 40 years <ref name = 40yeartrain> Wikipedia (2019) Mat '64 https://nl.wikipedia.org/wiki/Mat_%2764 </ref>, so the costs for all DagBlads are: (80 x 25.000)/40 = €50.000 per year or €625 per DagBlad per year. This price is fairly high, but as mentioned before, we hope to make use of second-hand bogies for the DagBlad. | |||
=Cost Analysis= | |||
[[File:Financieel.jpg|thumb|400px|Figure 17: Finances of ProRail in 2017 <ref name=jaarverslag2017 />]] | |||
As discussed in the USE aspects, the main aim of the enterprise ProRail is to make as much profit as possible. Furthermore, ProRail is dependent on subsidies and fees for the financing of its activities from the Ministry of Infrastructure and Water Management and other governments. Hence, it is important to analyse the current subsidies, fees and expenses of Prorail and keep the robot price lower than these subsidies and current expenses. Mainly the current expenses of Prorail on management and maintenance of the railway are important to investigate, as this is the area where the robot will be active. | |||
To find these expenses a year report of 2017 was analysed <ref name=jaarverslag2017> Jaarverslag 2017, Prorail. (2018) https://www.prorail.nl/sites/default/files/prorail_jaarverslag_2017_def_0.pdf </ref>, as the year report for 2018 was not yet published. In 2017, ProRail received € 2.583 million to spend as can be seen in Figure 17. from this € 2.583 million 68,5% was received to invest in management and maintenance which equals to € 1.771 million. Eventually they spent € 1.689 million from the received money in management and maintenance. ProRail mainly spends this maintenance money on keeping the railway safe and active. They let the maintenance work carried out as effectively and efficiently as possible by qualified contractors. There are three main maintenance and management activities that are conducted. | |||
[[File:Kosten 2017.jpg|thumb|400px|Figure 18: Operating costs of ProRail in 2017 <ref name=jaarverslag2017 />]] | |||
The first activity is large-scale maintenance. This concerns the activities that are necessary to ensure the quality of the maintain infrastructure and achieve long and medium-term lifespan. The activities focus in particular on maintenance and replacement, adjustment and modification of constructions, preservation of objects, grinding of rails and seasoning | |||
of the tracks. <ref name=jaarverslag2017 /> In 2017, Prorail has spent €109 million on large-scale maintenance, as shown in Figure 18. | |||
The second activity is small-scale maintenance. This concerns the activities that are necessary to improve the availability, reliability and safety. These activities focus on inspections of the infrastructure, correction of track location, replacement of components and functional recovery <ref name=jaarverslag2017 />. In 2017, Prorail has spent €303 million on small-scale maintenance, as shown in Figure 18. | |||
The third activity is the maintenance of the transfer spaces in stations and the management. The maintenance involves cleaning, structural maintenance, troubleshooting, energy, property taxes and insurances. Management relates to the management of IT systems, energy consumption of the rail infrastructure and the deployment in the event of emergencies <ref name=jaarverslag2017 />. In 2017, Prorail has spent €79 million on maintenance of transfer spaces, and €180 million on management, as shown in Figure 18. | |||
From these explanations on the three different activities, it can be concluded that the robot fits within the second activity, small-scale maintenance. As a result, it can be estimated that a budget of €303 million can be used for the robots. However, the robot is not able to cover all the small-scale maintenance problems that arise every year. The small-scale maintenance is mainly focused on solving the problems that arise on the railway that cause delay to passengers. From the statistics on delay causes, it can be found that 2% is caused by weather influences, 7% on construction activities and 9% on external influences <ref name=trainStatistics />. From this total of 18%, it was estimated that 3,5% is related to delay by leafs and snow. Hence, it was estimated that 3,5% of the €303 million small-scale maintenance budget can be used for the robots, which is €10,605 million. This estimation will be used in the calculation, as a preciser number on the budget that is needed for cleaning leafs is not published. | |||
As mentioned in the usability section, at least 80 robots will be needed for a successful implementation of the leaf cleaning system in the Netherlands. Therefore, a maximum of €132.562,50 per robot can be used per year. We aim to keep the costs of the robot lower than this amount per year, as it will increase the possibility of NS and ProRail implementing this robot due to the lower cost. | |||
As can be seen in the component list, the price of one laser is $480.000 which equals €446.761. There are two lasers necessary for each robot, which means that the costs of the lasers will be €893.522,- for each robot. According to the estimations the whole laser system can run for at least 80.000 hours if we replace the diode every 10.000 hours. In the worst case scenario, a robot drives around 6 hours a day. Therefore the two cleaning laser systems must be replaced every 80000/6/365 = 36,5 years. Thus, 1/36,5 * 893522 = €24.480,- will be spend on the laser systems of one robot per year. Furthermore, as discussed in the sweeper section, the price for 4 the brushes will be €328,83 per year. And when only new bogies will be used for the base and wheels of the robot, that will cost around €625 per year. Finally, the computer within one robot is estimated to be €50, as it can be used in combination with the speed sensor that is already built in the train. The frame is estimated to be around €3500 per robot. For the coupler type 430, the original price is not published. However, based on the value of other Scharfenberg couplers, the cost of the type 430 is estimated to be around €16.500,- per unit <ref name=couplerprices> Detailed Import Data of scharfenberg, Zauba. (2018) https://www.zauba.com/import-scharfenberg-hs-code.html </ref>. The coupler is estimated to be replaced within 20 years of usage, which results in a cost of €16.500 / 20 = €825 per year. The robot will have two couplers which equals to a cost of €1650 per year per robot | |||
Therefore, it can be concluded the robot has an estimated cost of €30.633,83 per year per robot, which results in a total cost of €30.633,83 x 80 = €2.450.706,40. Compared to the estimated €10,605 million that Prorail is currently using for cleaning snow and leaves, the use of 80 Dagblad robots will save at least around €8.154.293,60 (77%) per year. | |||
=Conclusion= | |||
The DagBlad is a robot that is developed to remove leaves and snow from the railway. These obstacles are the cause of approximately 10% of all the delays on the Dutch railway network. The DagBlad is able to achieve its goal by using a combination of sweepers and a powerful laser. | |||
The sweepers on the front remove a large part of the loose snow and leaves. This clears the way for the laser to tackle the compressed (wet) leaves underneath. Compressed leaves form a low-friction coating, which is dangerous for trains. A sweeper by itself is unable to remove this though layer, so a laser is required. The laser has a specific wavelength of 1064 nm that heats up the leaves and loosens them. A second sweeper is then able to remove the slippery layer from the railhead. | |||
Snow is only dangerous in large quantities (more than 30 cm) or in between switches. When compressed, it can turn into solid ice and block the movement of switches. Switch heaters are designed to melt the snow in between switches, but they cannot handle too much snow. The sweepers are able to reduce these problems, since they prevent snow from accumulating and blocking the switches too much. Switch heaters can then melt the remaining snow away. A 3D-model of the DagBlad can be found in Figure 3 and 4. | |||
In short, the DagBlad is an independent cart that consists of a sweeper, a laser and another sweeper respectively. Due to the overcrowded schedule on the Dutch rail network, it is almost impossible to fit another machine in this schedule. That is why the robot does not move along the tracks independently. It is attached to the front of trains via a Scharfenberg coupler. | |||
Since the DagBlad is designed to tackle weather-related problems, it is mainly used during the autumn and winter seasons. However, the need for the robot is still very dependent on the daily weather. This makes it hard to predict how many of them are needed. A rough estimation has been made by looking at the number of different train lines (114), substracting the number of intercity's (these are redundant) and adding 5 extra robots to the biggest stations, which results in a total of 80 DagBlad robots. | |||
Finally, a cost estimate has been made to predict the feasibility of the DagBlad robots. It will only be implemented if the costs of the development and deployment is lower than the current costs of maintenance and delays. Our estimates indicate that at least 8,15 million euros will be saved by implementing the robot in its current state. This will make it very interesting for ProRail and NS to adopt it. | |||
In conclusion, we see that there is a lot of potential for this robot to be implemented in the Dutch rail network. It will reduce the maintenance costs for ProRail and the number of delays, which saves costs for NS. The DagBlad is robot is thus a cheaper and better solution. | |||
=Discussion= | |||
The DagBlad is currently an independent cart that can only be used if it is attached to trains. This is a rather inefficient method, since it has to attach and detach regularly. It would be interesting to investigate whether it might be better to attach the DagBlad to the front and back of trains permanently. This reduces the effort involved in attaching the robot. However, this requires all trains to be equipped with two DagBlad units on both sides, which will be a significant one-time investment. Also in terms of coupling the locomotive to the train it might form a problem since each end will be equipped with a unit. The brushes need to be retractable somehow. Further research into this option is required to make valuable claims. | |||
In order to improve DagBlad's current design and functionality, a few things need to be tweaked. The cart could still be a bit lower in height and shorter in length than it is now, so the engineer has a better view over the tracks directly in front of him. This will come in handy at train stations. Making DagBlad smaller also makes coupling, moving and maintenance easier for personnel. The costs will also be reduced since less material is required. | |||
For the current cost analysis the profit was estimated to be at least €8.154.293,60 per year. However, by adopting the DagBlad system, the costs that are caused by delays will also be reduced, as more delays will be prevented by the DagBlad robots. This was not taken into consideration for the cost analysis. To improve the current cost analysis, further research can be done on the estimated profit caused by the delays that will be prevented by the robot. | |||
=Sources= | |||
<references/> | |||
=Appendix A= | |||
[[File:dagblad_appendix_A.png]] | |||
=Appendix B= | |||
[[File:dagblad_appendix_B.png]] | |||
== | =Appendix C= | ||
[[File:dagblad_appendix_C.png]] | |||
== | =Appendix D= | ||
[[File:dagblad_appendix_D.png]] | |||
= | =Appendix E= | ||
Types of switch heating: | |||
*Central tube heating (Centrale Buis Gas or CBG): this principle is very similar to a boiler in homes. An antifreeze liquid is heated in a boiler and then transported to heat exchangers. Heat is transferred to the snow via conduction and convection. | |||
*Geothermal heat: this method is based on the same principle as the CBG-system. However, instead of a boiler, a heat pump is used. 75% of the necessary energy is generated through geothermal heat, while the remaining 25% through electricity. | |||
*Gas heating: this principle makes use of a controlled combustion of natural gas close to the switch. This melts the ice. The gas is transported to the destination via pipes. | |||
*Electricity: for this variant heat is generated by heating resistors. |
Latest revision as of 20:29, 8 April 2019

The Dutch railway network is one of the most crowded railway networks on the planet [2]; an intercity leaves the station every 10 minutes. The Dutch trains are also very punctual; 90% of all trains are in time [3] with a 5 minute tolerance. This is a rare accomplishment among railway companies. However, there is a downside to all of this; since it is so busy, a single problem can have dramatic effects. One delay can create a congestion and this can cause huge delays. In 2016 the Dutch government estimated that delays cost at least 145 million euros annually[4]. Therefore it is important that delays are prevented as much as possible.
From the graph in Figure 1 it can be seen that external influences (indicated by orange), railway cleaning activities (indicated by purple) and the weather (indicated by yellow) are causes for train delays in the Netherlands [1]. They add up to almost 20% of all train delays. These types of train delays are partly caused by snow and leaves on the train tracks. As a result we estimated that snow and leaves cause approximately 10% of the train delays in the Netherlands.
The problem with leaves on the tracks is that trains compress the leaves beneath them. These leaves form a sticky low-friction coating on the tracks and this increases the breaking distance tremendously. This can lead to dangerous situations. That is why railway companies (like the Dutch 'Nederlandse Spoorwegen' or NS) prefer to avoid risksy situations by cancelling their trains. Currently, no proper solution exists for this obstacle.
Snow on the other hand is the cause of a very different problem. Snow on the tracks is only dangerous in large quantities, which is rare in the Netherlands. However, snow can be a problem, when it falls between the switches, since it prevents switches from moving. This problem is solved by using switch heaters, but these fail from time to time and there is no backup.
We as a group believe we can improve this sticky situation by introducing a robot to the Dutch railway network that is able to clean the tracks from obstacles like leaves and snow. This wiki describes the whole process of this project.
Group Members
Name | Study | ID Number |
---|---|---|
Max Hanssen | Industrial Design | 1257269 |
Jorick van Hekke | Electrical Engineering | 1225185 |
Suryanto Horlez | Computer Science | 1286714 |
Joeri Schults | Mechanical Engineering | 1266330 |
Jules Vaes | Mechanical Engineering | 1263196 |
Project Information
More information about this project (e.g. planning, milestones, SotA, etc.) can be found by following this link: Project information
Concept
Our concept is a robot, called the DagBlad, that is able to clean the railway tracks from leaves and snow. This robot is not autonomous, since this turned out to be very difficult on the overcrowded Dutch railway network. Our robot is attached to the front of trains and is also powered by these. The DagBlad is connected to the CAN bus of the train, which allows it to retrieve valuable data, like speed, directly from the train.
The robot tackles the obstacles (leaves and snow) by using a combination of sweepers and a laser (see 'Design' for more information). These are arranged in the order: sweeper, laser, sweeper. This is done deliberately. The first sweeper removes the loose layer of leaves and/or snow. This exposes the slippery layer of compressed leaves underneath. A powerful laser, which is pointed directly on this layer, heats the leaves. The leaves expand and this decreases the adhesion to the rail. The second sweeper is now able to remove the loosened layer. The rail is now cleaned from both leaves and snow (see 'Obstacles' for more information).
Objectives
The objectives when designing a kind of cleaning device for the Dutch railway tracks are of great importance. It is for NS and ProRail's best interest that these objectives, which we will call RPC's, ensure a product that is actually helpful. The so called RPC's - Requirements, Preferences and Constraints - are set up to determine what is important and function as guidelines for the robot's design. Using these guidelines will make sure essential matters to NS and ProRail are really thought through, so DagBlad functions as desired. The RPC's are stated below:
Requirements
- DagBlad is able to clean the tracks
- DagBlad is able to remove leaves and snow using its sweepers and lasers
- DagBlad is operational at any time
- DagBlad is able to drive up to 160 km/h
- The rotational speed of DagBlad's broom can go up to 1377,9 RPM
Preferences
- DagBlad should be easy to maintain
- DagBlad's parts should be interchangeable
- DagBlad should be as light as possible
- DagBlad should be compact
- DagBlad should be cleaning as fast and efficient as possible
Constraints
- DagBlad can only move in the direction the train is going
- DagBlad has to be coupled and uncoupled at the start and end of its journey
- DagBlad cannot drive and clean solely by itself
- DagBlad cannot remove large objects like trees, debris or dead animals
- DagBlad cannot be wider than 3.4 meters [5]
- DagBlad cannot be taller than 2 meters
Robot Functions
The Dutch train tracks are very crowded during both day and night[6]. This makes it very difficult to add an independent cleaning robot to the schedule. That is why the DagBlad robot is attached to the front of a train. This enables it to clean the tracks, while avoiding scheduling difficulties.
The robot will only be used when it is necessary. This will mostly be in the autumn and winter seasons, because of the falling leaves and snow. The left sweeper rotates counterclockwise, while the right sweeper rotates clockwise. Consequently, leaves and snow are brushed from the rails. The sweepers start rotating and the laser turns on when the train moves faster than 30 km/h (see 'Software' for more information). This is done to ensure that the equipment is turned off when the train approaches/leaves a station. Otherwise, dangerous situations could occur.
Daytime and Nighttime
On average there are 4500 trains riding per day to transport around 1,1 million passengers [7]. Although a small percentage of these trains are riding through the night, most of these 4500 trains are driving during the day, as the night trains only drive once per hour between 1:00 and 5:00 in the Randstad of the Netherlands [8]. Due to these busy train schedules during the day, it is not possible to let the cleaning robot drive autonomously on the railroads during daytime. This would only cause more delay for the NS. However, it is still extremely essential to let the machine clean the railroads during the day, because otherwise the design will not have any big positive impact on the delay problems. Hence, the only way for the DagBlad robot to clean the railroads during daytime is to attach the machine onto the front of the NS passenger trains. Next to cleaning the railroads during the day, the robot can also clean during the nighttime. Because it is less crowded on the railway during the night, the robot will be able to thoroughly clean the railroads without slowing down any other trains. However, it was decided to also not let the robot drive autonomously during the nighttime, as the switch from not autonomous to autonomous overnight would be unnecessary and difficult. Letting the robot clean while attached to a passenger train is efficient enough to clean the railroads. To make the DagBlad robot work during daytime and nighttime in this way, there are a few requirements which need to be met:

- It needs to be attachable to the front of the NS trains.
- It should not block the sight of the machinist.
- It cannot slow down the speed of the train.
- It needs to be suitable and appropriate to pass by the platforms of the stations.
- It needs to be detachable from the front of the NS trains.
To meet the requirements of being able to both attach and detach from the NS trains, it needs to adapt to the front coupler of all the different NS train models. Luckily at the moment all the different Intercity and Sprinter model trains of the NS use the same type of Scharfeneberg coupler [10]. This Scharfenberg coupler is an automatic coupler which can be activated or deactivated from the machinist cabin [11]. A more detailed analysis on the coupling system can be found under the 'Design' section. The design of the cleaning machine also needs to fit with the requirements of not blocking the sight of the machinist and being suitable for platforms. This will be elaborated when developing the final design for the machine. However, from these two requirements it can already be made clear that the machine itself should not be higher than around 1.5 meter for the machinist’s sight, and not be wider than around 3 meter to fit in between platforms at stations [12]. Furthermore, the robot will also need it’s own wheels. Thus, these wheels need to be set suitable for the rails which have a gauge of 1435 mm [13]. Furthermore, the adaptation to attach to the passenger night trains that drive through the Randstad is possible. Next to these passenger trains, there are also many freight trains that ride on the tracks daily. According to a report of Prorail, in 2017 there have been riding more than 20.000 freight trains over the same railroads in that year, see Figure 2 [9]. Moreover, it can be seen that the rail tracks with the most delays are in the Randstad area in between Amsterdam, Rotterdam, Den Haag en Utrecht [1]. This is the same area as where the most night trains are riding. Therefore, the robot needs to clean this area extra thoroughly. Hence, it will be more effective to attach the cleaning machine onto the night trains which are traveling in the Randstad. This will prevent extra delays, as the cleaning machine will not drive autonomously within this busy train schedules in the night of the Randstad. However, outside of the Randstad the cleaning machine will still have the possibility to drive autonomously to clean the railways, as there are no passenger trains active in the night. Although it is still possible to let the robot drive autonomously outside of the Randstad during the night, it was decided to not do this. After considering the requirements and needs of the users, it was concluded that making the robot drive autonomously, on top of attaching it to passenger trains, will be unnecessary and difficult on a daily basis.
USE Aspects
Users
For this project the focus has been put on the railroads in the Netherlands. This decision was made, because it is only possible to design the product for one certain type of railroad system. At this stage designing a product which can be used globally by adapting to different types of railway systems is too advanced. Furthermore, the project would have too many potential users to focus on, as they will differ per country. Therefore, it was decided to stick to the Netherlands, as this is the country which we had the most experience with. Although it was decided to keep the focus in this specific area, there is still a wide variety of users. For this design there are people who can use and influence the design directly, as well as people who get influenced indirectly by the design. Hence, a distinction can be made between primary and secondary users. The term primary users will be used to refer to the group of users who are directly interacting with the design. The term secondary users will be used to refer to the group of users who are not directly in contact with the design but still affected by it. The distinction between these two different users will be made more clear by defining both groups.
Primary Users
For this design, the group who buys, uses and introduces the design into its target scenario are considered as the primary users. Hence, the organisations who are responsible for the railway system in the Netherlands belong to this groups. Thus, only Prorail is the primary user, as they are the ones responsible and can make direct changes to the railway system. The NS can not be fully considered as a primary user, as they only make use of the railway system, but are not responsible for the railroad itself. Prorail are the ones responsible for the construction, maintenance, management and security of the railway system in the Netherlands. When a product with the aim to clean the railroads is used, Prorail is the main company to introduce, use, and interact with the product.
Secondary Users
For this design, the people who get influenced positively or negatively by this design in an indirect way are considered as the secondary users. As mentioned above the NS is not considered as primary user, instead NS can be considered as a secondary user. They make use of the railway system in the Netherlands by transporting people from location to location with trains that drive on the railroads. Therefore, they will not be in direct contact with this design, as they will only get positively influenced but cannot influence the design itself directly. The use of the design on the railroads will be a great advantage to the NS, as it will make the railroads free and safe which reduces the delay for trains of NS.
In addition to NS, this reduction in delay also has a positive effect on the users of NS. These users are people who make use of the trains of NS as transportation to get to their destination as fast as possible. Although NS and Prorail are in charge of the trains and railways in the Netherlands, this group of travelers is important and can also be considered as secondary users.
Occasionally, trains of foreign companies such as Thalys or NMBS also make use of the railway system in the Netherlands. As a result, these foreign train companies can also be considered as secondary users. However, this group of users will not be further addressed, as the main focus is put on the companies NS and Prorail.
Society
Obstacles on the railroads, which cause a delay for many travelers, can be considered as a problem to society. In some occasions the delay can come up to major amounts of time or even cancellations of trains, which leads to missing important meetings or appointments. Moreover, this can form a challenge to the government, as the NS is a Dutch state-owned company. This means that the government has significant control over the NS through majority ownership. For this reason, one of the main aims of the government is to make transportation more accessible to its users. To be able to make transportation on railway more accessible, the delays of trains need to be taken care of. This design can help with solving this challenge to society. The design of this project can not fully solve the challenge of it, as there are many factors which have an influence on causing delays in transportation. However, this design will still have a positive impact on this relevant problem. It has the potential to play a big role in the future of railroad maintenance which is beneficial to society.
Enterprise
In the USE aspects, enterprise is considered to be the relevant companies that are connected to the project. The main aim for these enterprises is to make as much profit as possible. The previously discussed primary user Prorail can be seen as a relevant enterprise to this design. Although currently Prorail is still a government task organisation company that is part of NS, the Ministry of Infrastructure and Water is planning to make Prorail a public law independent administrative in 2021 [14]. As a result Prorail will become an organisation which conducts governmental tasks, while they are not under authority of the Dutch government. Hence, in the future Prorail will look at this design from a business perspective. They will only decide to make use of this design if it is profitable for the company. Unless they are forced by the government as they will be an independent administrative. Therefore, the design is required to be efficient in general, as well as cost-efficient so that Prorail will have good consequences from using the product.
Design
Prototype
The first idea for a prototype was made with SketchUp, as can be seen in Figure 3. Eventough the robot will be put in front of Sprinter trains, the model uses a standard NS Intercity (Bombardier TRAXX) locomotive for scale and context. Since the robot will block the locomotive's headlights, it is equipped by a pair. The robot is equipped with two pairs of opposite-rotating sweepers which are placed up front. The robot will also be equipped with a pair of lasers in between the sweepers. The prototype can be as wide, if not wider than the locomotive itself, if it only stays within a 3.4 meter margin as mentioned in the RPC's [5]. This margin is there to make sure vehicles on railway tracks can safely go through tunnels for instance without any hindrance.
Notice the robot is much smaller in height than the locomotive, this is make sure the tracks are still visible for the engineer. The maximum height for the robot has been set to 2 meters. As can be seen in Figure 4, the front of the robot has a sloping edge, in order further enhance the engineer's view on the tracks. The corners of the design have been more rounded in order to minimize drag and improve driver's visibilty.
The brushes and lasers are featured on the front of the robot to make sure the robot is able to clean the tracks prior to passing that piece of track. This way the wheels of the robot and train take out the bits that are left. That is also how rust is prevented from forming on the metal tracks. The brushes are pointed inward, barely touching each other, so leaves and snow get tossed outwards.
Coupling System
As discussed in the 'Daytime and Nighttime' section, the robot needs to adapt to the front coupler of all the different NS train models to both attach and detach from them. At the moment NS trains use a Scharfenberg coupler which is an automatic coupler that can be activated or deactivated from the machinist cabin. After getting in contact with the NS through customer service online, it was confirmed that the Scharfenberg coupler are mostly used. Additionally, the NS online customer service gave us the information that another type of coupler called BSI is also used for DDZ and DD-AR train models. Next to this BSI coupler, the NS also use the screw coupling for some trains. Although they use multiple types of couplers, it is the most efficient if the cleaning machine is adapted to one type of coupler. Hence it was decided to use the Scharfenberg coupler, as this is the most used coupler by the NS. Furthermore, the NS have given us a product sketch of the Scharfenberg coupler which they use, which can be seen in Figure 5.
At the moment there are 6 types of main Scharfenberg couplers on the market: the type 10, type 35, type 330, type 430, type 55 and the type 140 [15]. The cleaning machine does not necessarily have to have the same type of Scharfenberg couplers as the train to which it needs to connect. There are transitional couplers, such as the modular transitional coupler, that can connect two different type of Scharfenberg couplers [15]. This modular transitional coupler separates the two couplers into two separate head and an adapter that forms the step. The two heads can be connected to each other directly, which makes it possible to connect coupler heads of any kind and at different heights into the transitional coupler. As a result, a suitable type of Scharfenberg coupler can be chosen for the design of the robot.
- The type 10 Scharfenberg coupler is often used by railway companies, and is reliable due to its high strength and large gathering range laterally and vertically. [16]
- The type 35 is suited for vehicles without a compressed-air system, so for fully electrified vehicles. [17]
- The type 330 is often used in light rail applications due to its small size. However, it is still a strong and reliable coupler. [18]
- The type 430 is ideal for low floor trams and monorails, because of its compact and lightweight construction. Furthermore, it can fit behind the front covers. [19]
- The type 55 and type 140 are specifically made for high loads in rough environments. [15]
For the robot, the best option will be the type 330 or the type 430, as these two types are ideal for lighter sized vehicles and can still deliver a strong support. Furthermore, these types are not as big as the other types and can fit behind the front covers. The type 330 can transmit a buff load of 800 kN and a draft load of up to 600 kN, and the the 430 can transmit compressive and tensile forces of up to 300 kN. However, due to the robot being pushed by the train and not pulled by the train because of it's position in front of the train, the forces that the couplers can hold are not relevant, as it will be certain that the couplers can hold the pushing forces.
Usability
How many robots needed?

To keep the railway clean throughout the day, the users will need to implement and use a minimum amount of these cleaning machine. The amount of cleaning robots that is needed per day is dependent on the weather situation. During the summer season the expected maintenance problems with leafs are lower than during the Autumn season. Therefore, to estimate the amount of robots that the users will need, the situation with the most extreme weather conditions will be considered. In these conditions the estimation was made that it would be optimal to let one robot attach to a train for each different train path. This choice was made, as it will cover the whole Dutch railway network, as can be seen in Figure 6. It was found that there are 127 different train lines in the Netherlands [21]. From these 127 different train lines, 2 are Thalys high speed trains which travel to France, 2 are ICE high speed trains which travel to Germany, and 9 stop trains are all the way connected to Germany or France. Hence, 114 trains are traveling only on the Dutch railway network. However, 39 of these trains are Intercitys, which drive on the same railroad network as the Sprinter trains. Therefore, it is more efficient to not attach the robot to these Intercity's, as it is not necessary to clean the same railway track twice as much. As a result, at least 75 cleaning machines need to be implemented, but there need to be extra reserve robots in case of emergency. Hence, one extra robot will be distributed to the five biggest train station in the Netherlands. These include the station in Amsterdam, Utrecht, Rotterdam, Den Haag, and Eindhoven [22]. As a result at least 80 robots will be needed for the users.
How much time does it take?
Currently the coupling of trains takes approximately 1 minute. However, if a coupling system with transitional coupler will be used, this will take slightly longer, but it will not interfere or delay the usual traveling times. For an optimal cleaning of the railways in the Netherlands, the robot will be attached every 6 hours on a train on each different Sprinter train line. Attaching it to every driving train cannot be possible due to the costs. The first robot will be attached to the first trains that drive after the night schedule, which is around 5:30. Then the robots will be attached again every 6 hours, if necessary. Thus, the robots will be active around 5:30, 11:30, 17:30 and 23:30. This schedule makes sure that the first and last active trains of 5:30 and 23:30 of each day will be attached with a cleaning robot. Furthermore, the morning rush hours of 6:00-9:00 and afternoon rush hours of 16:00-18:00 will each contain one cleaning robot with this schedule [23]. As a result, attaching the robot every 6 hours to passenger trains will be the most effective time schedule with regards to the efficiency and cost.
How will they use it?
The users can use the robot by attaching it to the passenger trains before the passenger train starts riding at the first station. Afterwards the robot will be detached when the cleaning is done at the the end station. The robots can be stored efficiently due to the relatively small sizes compared to passenger trains.
Obstacles
Track Maintenance
Before investigating what problems can occur on the rails, it is useful to take a look at who is responsible of tackling these issues.
For small-scale track maintenance, ProRail hires approved rail contractors who can maintain the track for them [24]. To be recognized by ProRail, parties must have specific technical, professional and organizational skills and requirements. These can be found on the ProRail site. A list of approved entrepreneurs can also be found on the ProRail site [25]. After the rail contractor has been recognized by ProRail, a public contract is signed in which the required performance is prescribed, not the required effort (as before). The idea behind this is that this should lead to more proactive maintenance and this should lead to an increase in availability and quality of the tracks. These contracts have a duration of 10 years and are called ‘Prestatie Gericht Onderhoud’ contracts (Performance-oriented Maintenance contracts or PGO contracts). Pilots were started in 2014 to work with this new form of contracts. The number of disruptions decreased in the areas of these pilots. ProRail says that in the coming years all maintenance areas will use these PBL contracts. In addition, ProRail has developed a new standard framework that should make it clearer when maintenance is needed and when the track can be used (limitedly) and when not. In addition, it will also become clearer who is responsible and when; ProRail or the contractor. The aforementioned list of accredited entrepreneurs shows that ProRail recognizes 4 companies in the field of track maintenance. These are: Asset Rail, Bam Infra, Strukton Rail and VolkerRail.
Contacting VolkerRail has proven very helpful in gaining a better understanding of what the problems on the tracks are and how these are tackled. This will be discussed below.
Snow
Problem
In very cold periods like in the winter, snow and ice can build up on the tracks. The ice can block movable parts of the track (switches) and coat over the power lines or the third rail, preventing trains from drawing the power they need to move. Also, icicles on bridges and tunnels can cause serious damage to passing trains. All these problems can cause the trains to have delays. [26]
When a train has to slow down as it approaches a station, snow gets compressed and can turn into solid ice. This does not just clog that area, but the ice can also coat the rails, which disconnects the trains from getting the required power. Ice sheets are a risk for dislodging and damaging trains. The steel rails can freeze together when it gets to cold. This is what makes the signals stay red and prevents the trains from moving. When snow drifts are deeper than 30 cm , trains can no longer run safely unless they have snow ploughs [27]. Fortunately, this is rare in the Netherlands.
Solution
Bleach, Salt
Using these products we can lower the rate of freezing cause during the freezing and melting process some water molecules freeze while others melt, replacing each other in a state of equilibrium, while when one of these products are added in the mixture it disrupts this equilibrium. [28]
Laser
CO2 Lasers can be used to melt ice and snow with a wavelength of 10.6 μm, which ice strongly absorbs, to drill (via melting) through ice. The resulting drilling speed is measured at several irradiation intensities, ice-snow densities, and beam angles relative to the horizontal axis. The speed increases nearly in proportion to the laser intensity. [29] For the laser to be able to remove the snow, it must be able to handle the maximum snowfall [30] in the last 7 years the maximum snowfall on a day is 8cm on the 14th of January 2013. We first want to know how much snow the laser should be able to melt in a second. We calculate it by looking at the speed of the train which is 160 km/h, or 44.44 m/s. The width of the head of the tracks is 72 mm (HSL, high-speed tracks). Considering a layer of 4 cm of compact snow on the tracks, the train would be going through 25.57 kg of snow per second. The laser needs to be able to melt all this snow in order for the concept to work. The energy required to melt 25.57 kg of snow is 534413 J/s, considering -10 degrees Celcius. To generate this energy, the wavelength of the photons has to be 3.717*10^-31 m, resulting in a frequency of 8.065*10^38 Hz. The wavelength we get are corresponding to the wavelength of Gamma-rays. Lasers having Gamma-rays are at the moment still not developed as it still is a challenge for scientists however in the futur it might be possible according to Cordis [31].
Snow Plough
A snow plough can be used to clear the train rails when there is more than 30 cm of snow, we could use this one the robot to make it possible to clear the rails for other trains, at the moment this is already installed on normal trains when the snow is higher than 30 cm. [26]
Ice
Problem
In colder periods, rain with a temperature around 0 ℃ can form glaze (ijzel). There is an important distinction between glaze and frost, which forms from water vapor that comes in contact with a solid surface. Frost is usually not a big problem for trains. It may cause some sparks at most, but this is not problematic [32]. Glaze on the other hand is cause for some serious concern, because, in the right conditions, it can form a layer of ice on the catenary. This may prevent the trains from receiving electricity, which makes them useless. Unfortunately, combatting this problem is not the focus of this project. Ice can also freeze the switches together, which prevents trains from switching tracks. The effects of ice can be harmful for trains and can cause some serious delays.
Solutions
In theory, ice can thus be harmful for the tracks. However, according to a source at VolkerRail, ice is not a big problem in the Netherlands. Very low temperatures a rare in this country, which means that the layer of ice on the tracks and catenary is thus often very thin. Since the trains on the Dutch railway are rather heavy, the ice is crushed or pushed away. This information has led us to conclude that it was not worth focussing on solving the ice issue. The solutions mentioned below are thus not integrated in the final concept.
Switch Heating
Ice or snow on the switches can still be harmful though. The way ProRail currently tackles this by making use of switch heating. This heating melts the snow and ice and thus making it harmless. There are four different kinds of switch heating [33], these are explained in appendix E. Currently 6.500 of the in total 8.900 switches are equipped with switch heating [34]. This works rather well, if the snow does not pile up too high, but as mentioned before, this does not occur very often. The heaters are also prone to malfunctions. When this happens, staff is deployed to melt the snow and ice away with gas burners or to blow the snow away with leaf blowers. Our source stressed however that these are emergency measurements and that this should be prevented. The contractors have to make sure that the heaters function correctly during the ‘heating season’ (stookseizoen). This is from the 15th of October until the 15th of April.
Laser
We wanted to check whether we could use a laser to melt ice, just like we did for snow. It would be more logical to use a laser to melt ice, since icing is generally more common than snowfall and a layer on the tracks shouldn't be thicker than a millimeter. So considering 1 mm of ice on the HSL tracks, a train would pass 2.93 kg of ice per second. To calculate the energy needed to melt this amount of ice, temperature needs to be estimated so it's assumed to be minus 10 degrees Celcius. The laser would need to output 61764.4 J every second. Using the speed of light and Planck's constant, the corresponding wavelength can be calculated. This wavelength is 3.216*10^-30 m, which is really small. The frequency is then 9.321*10^37 Hz, so only a factor 10 smaller than the frequency required to remove snow. This is therefore not a viable option, since these frequencies for photons are way too high.
Leaves
Problem
In the Autumn trees will drop their leaves which might land on the railway. At first the leaves will not cause any trouble, but during the day they will cause problems. If the leaves which landed on the railhead become moist and heavily compressed by the passing trains, they will result in a low-friction coating. Due to this low-friction coating the railway becomes slippery and the wheels of the train starts to block when it is starting to brake. Due to this blocking one side wheels will experience more wear than the other sides which results in “square-wheels” [35]. These “square-wheels” need to be repaired in workshop which costs time and money. Due to the malfunctioning and repairing of the train wheels less trains will be deployed on trajects which is not preferred by the travellers. Another problem due to the low-friction coating is that it can take up to 800 meters extra to come to a total stop [36].
Solutions
Leaf Blower
A leaf blowers is used to blow loose leaves away from their initial position. This could be useful for the trains because they can blow the leaves away from the railhead. But this is not an option anymore. Due to the high compressing the leafy moist is stuck to the railway, therefore the leaf blower is not able to blow the leafy moist away [35].
Pressure Washer
A pressure washer is used to clean object from a dirty layer which is stuck to the surface. Therefore the pressure washer can be used to remove the compressed layer of leaves from the railway. An example of a product which is already tested is the Nilfisk-ALTO developed by Nilfisk-Advance for the Banedanmark, the railway organization in Denmark. The Nilfisk-ALTO has a 7000 liter water tank and operates at a pressure of 500 bar and sprays 40 L/min. The wagon achieved to clean the railway from the leaves when it runs at an operating speed of 45 km/h [37]. Due to the large amount of water that needs to be stored the pressure washer is not an option for the DagBlad. The DagBlad is attached to the front of a train during the day and therefore a container filled with 7000 liters of water will impedes the view of the machinist.
Traction Gel Applicator
Traction gel applicator (TGA) is a substance which consists out of sand, metal particles and starch [38] . The TGA system consists of a sensor and 50 meters further the cabinet. The cabinet contains the electronics, a pump, a delivery hose, the substance and is solar powered. The sensor, which gets triggered by the wheels of the train, sends a signal to the cabinet that a train is coming. The pump of the cabinet then places some TGA on the railhead via a delivery hose. When the train passes the cabinet the TGA gets stuck on the wheels and this gives the train more traction for a short distance, 60 to 200 meters [39]. Due to this short distance the TGA cabinets are typically placed at the entries and exits of a train station [40].
Sweeper
A sweeper can be used to remove dirt from surfaces. The brushes can be made out of metal (steel), polypropylene or from pig’s hair. For brushes used to clean the railway the bristles are made out of steel or polypropylene and the sweeper operates at a high torque which makes it possible to remove snow, coal, stones, dust, sand, leaves, trash and dirt[41]. When the high-speed train is left out of the scope the maximum speed a train can achieve in the Netherlands is 160 km/h [42]. This means that the brushes have to rotate at a speed higher than 160 km/h. For this research a minimum speed of 200 km/h is a requirement for the brushes. If the brush is placed horizontally a common diameter of the broom is 915 mm, the broom diameter of the Dymax rail sweeper is equal to 915 mm[43] and the diameter of the KM90/120 is also equal to 915 mm[44]. Therefore the brush diameter of the DagBlad is fixed at 915 mm if the sweeper is placed horizontally over both railheads. Most motors have their speed specification in rotations per minute (RPM). The speed in km/h of the motor depends on, in this case, the diameter of the brushes. The diameter is fixed at 915 mm and the minimum speed is 200 km/h therefore the minimum RPM can be calculated using the following equation
v = d x RPM x 0,001885 (1)
where v is the speed in km/h, d is the diameter in cm and RPM is the speed in rotations per minute. Using 200 km/h and 915 mm for the diameter a minimal RPM of 1160 is needed to operate at a sufficient speed. When searching for already used rail sweepers the RPM is too low to use in our robot. After some research the LSRPM 132 M permanent magnet synchronous motor (PMSM) was found which has the following important specifications in the operation range of 1500 RPM[45]:
- Rated power P_n = 12 kW
- Efficiency η = 92,0 %
- Rated torque T = 69 Nm
- Rated current I = 21 A
- Weight = 49 kg
The sizes are shown in Figure 7. The RPM of a motor can be obtained using the following equation
RPM =P/T (2)
where P is the power in Watts and T is the torque in Nm. Filling in the data of the LSRPM 132 M a RPM of 1660 is obtained. Converting this RPM into km/h using (1) gives 286,44 km/h. This is a high enough speed to operate which means that the motor is also able to operate at a lower RPM which consumes less power, this also results in a lower required current.
Another possible placement of the sweeper is to place it vertical and use two sweepers instead of one. The new diameter of the brushes is determined using the knowledge about the railway. The railway has an inside width of 1435 mm and a heart-to-heart width of 1500 mm [13]. This means that the width between the outsides of the railway is equal to 1565 mm, this is also show in the Figure 8. To clean the rail-head from the compressed leaves and the snow, which also lays between the two rail-heads, the diameter of one sweeper has to be half the width of the outside to outside. The minimum diameter which cleans the whole surface is equal to 782,5 mm. To foresee a problem which is caused by the brushes touching each other a diameter of 770 mm is used. The advantages of placing the brushes vertical is that less torque is needed per sweeper because the two sweepers now clean one railhead each instead of one sweeper two railheads. Another advantage of using two sweepers is that it is not needed to place the sweeper a bit diagonal. When a horizontal sweeper is used it is needed to place it a bit diagonal to move the leaves, but mostly the snow, next to the railway. If the sweeper is not placed diagonal the leaves and snow are only moved forward which means that the sweeper is constantly removing the same leaves and snow. By using the vertical sweepers the leaves and snow are moved to the direction in which the brush is rotating. This means that, from the perspective of the machinist, the left brush has to rotate counterclockwise and the right brush clockwise to move the leaves and snow next to the railway.
The power transfer from the motor to the brushes will be done using a belt which is also suggested in the data sheet of the LSRPM PMSM [46]. The exact placement of the belt is shown in Figure 9. On one side of the motor an extra gear is needed to make the brush rotate counter-clockwise.
The next important part of the sweeper is the material of the brushes. Common materials for the bristles are steel and polypropylene. The leaves are highly compressed and therefore strong bristles are needed. Steel bristles are strong but also affect the railway itself, metal on metal friction. The goal is to remove the leaves from the railhead while the rail itself in not additionally damaged, therefore the steel bristles are no option. Polypropylene can be soft but also hard, for our problem the hard polypropylene is the solution.
The required specifications of the motor are calculated in the following parts.
Pressure
The leaves are compressed to the railhead by the trains themselves. To calculate the maximum pressure in Pascal that the leaves are compressed the surface and the weight have to be calculated. The four-coach configuration of the Regiorunner weighs 226 ton[47]. Every waggon has 8 wheels which means a total of 32 wheels for the four-coach configuration. Dividing the total weight over the wheels gives a weight of 7062,5 kg per wheel. The diameter of one wheel is 1000 mm[48], this gives a wheel radius of 500 mm. To calculate the area which is compressed by the train the height of the leaves on the railhead needs to be known. A research of L. R. Goodes, T. J. Harvey, N. Symonds and T.G. Leighton on the leaves on the railhead shows a diagram shown in Figure 10 which displays the height of the leaves[49]. From Figure 10 can be concluded that the highest point is 20 µm which will be used in the following calculations. An illustration of the lengths for the following calculations are shown in Figure 11. First the height a between the middle of the wheel and the highest point of the leaves is calculated using
a = r-h, (3)
where r is the radius of the wheel and h is the highest point of the leaves on the railhead. Then the length from the middle of the wheel to the point where the radius r achieves the height a can be determined using pythagoras
b = sqrt[(r^2)-(a^2)]. (4)
Using the length b the total length which compresses the leaves L can be calculated using the following equation
L = 2b. (5)
To calculate the area A which is compressed by the train the length 'L is multiplied by the width of the railhead w
A = L x w. (6)
To calculate the pressure which is expressed on the leaves the weight per wheel has to be converted from kg to Newton which is done with the following equation
N = 9.81 x M_w, (7)
where N is the weight per wheel in Newtons and M_w is the weight per wheel in kg. The pressure Pa in Pascal is finally determined using
Pa = N/A. (8)
When the train has passed the pressure on the leaves will decrease but the leaves are more stuck to the railhead than before. When the leaves are wet some amount of water is pressed out of the leaves which makes it stuck even more to the railhead.
Torque
The torque depends on how heavy or stucked the leaves are to railhead. In this calculation the torque is determined using bristle material which does not bent, this means that for the real-world problem the required torque is higher than calculated. First the effective radius of the sweeper which cleans/moves the leaves is calculated. In the most extreme case this is equal to half the width of the railhead. This is then multiplied by the mass of the of the compressed leaves. This will lead to the following equation
Td = N x w/2, (9)
where Td is the required developed Torque, N is the mass of the compressed leaves in Nm and w is the width of the railhead. Figure 12 shows the relation between the pressure in megaPascal MPa and the developed torque in Nm Td. The shaft torque Ts is determined using the efficiency of the motor which will be equal to the efficiency of the LSRPM 132 M, in this case 92.0%[45]. The equation for the shaft torque is equal to
Ts = Td/efficiency, (10)
Power
The required power is determined using the fixed speed in RPM calculated with (2). The equation for the power will look like this
P = Ts x RPM. (11)
The relation between the developed torque in Nm Td and the power in megaWatt MW is shown in Figure 13.
Conclusion
When the equations are filled in with the data from the Regiorunner and the knowledge from the research of of L. R. Goodes, T. J. Harvey, N. Symonds and T.G. Leighton on the leaves on the railhead[49] a pressure of 59,5859 MPa is found. This leads to a required developed torque of 4503,4 N/m. When the speed of the sweeper is fixed at 200 km/h a required power of 6,2054 MW is obtained. The full implemented calculation can be found in appendix B. The LSRPM 132 M permanent magnet synchronous motor does not have the required specifications; it has a to low power and torque. The required power which goes into the megaWatts in not possible together with a developed torque of 4503,4 N/m and therefore the sweeper will not be used in the final product. In short, the, not yet possible, requirements of the motor to use a sweeper as a removal system for the leaves are
- Power = 6,2054 MegaWatts
- Torque = 4503,4 Nm
- RPM = 1377,9 RPM
Laser
Lasers are used for all kind of operations but when operating at a wavelength of 1064 nm it becomes useful for the railway. Due to a carefully designed optical set-up of mirrors and lenses the laser was able to produce a series of pulses, 25.000 per second. At this wavelength the laser clears the track from debris. The highly compressed leaves on the railway absorb the pulses, which leads to a temperature of 5000 Celsius degrees. Due to this high temperature the leaves heat up rapidly which causes it to expand and getting lifted from the railhead[36]. Research from Mr. Higgins with TU Delft showed that the desired outcome is achieved even at a speed of 50 mph (80,47 km/h)[50]. The Sprinters from the NS have a maximum speed of 160 km/h[42] which is double the experiment speed. This means that it needs to be checked if the leaves are heated up strong enough to get lifted from the track using the same laser. The equations are shown in the next section and the full work-out, which also displays the equations a lot clearer, can be found in Appendix C.
Time
To calculate the new temperature when the train travels at 160 km/h the discrete step pulses I needs to be determined using the knowledge from the experiment at 50 mph. The first thing which needs to be done is to convert the speed from mph to m/s which is done by using the following equation
v = (mph/0,6213711922)/3,6, (12)
where v is the speed in m/s. Using this speed and the knowledge from the laser the pulses per meter can be determined using
p_m = p/v, (13)
where p_m is the pulses per meter and p is the amount of pulses per second. The time which the surface receives a pulse t is then equal to
t = p_m/p. (14)
Discrete Step Pulses
The discrete step pulses I, which is time dependent, is determined using the knowledge and data from the experiment[50] and the calculated time t. The discrete step pulses I is obtained using
I = (T.*λ.*δ)./((2./sqrt(π)).*sqrt(t)+(e.^t).*erfc(sqrt(t)-1)), (15)
where T is the temperature in kelvin, λ is the thermal conductivity which is 0,54 for water infiltrated leaves[51] and δ which is the wavelength in meters and for this laser equal to 1064 nm. The discrete intensity function id, which is also time dependent, is equal to
id = Tdes/(2/sqrt(pi))*sqrt(t)+ (e.^t).*erfc(sqrt(t)-1), (16)
where Tdes is the desired temperature in kelvin, in this case 5273 K. With this data the discrete constant I_0 is obtained using
I_0 = I/id. (17)
With the constant now known (I_0 = 5,7456 x 10^-7) the discrete step pulses I can be obtained for the new speed which is 160 km/h.
Temperature
The increase in temperature of the surface is obtained using
T = ((I)./(λ.*δ)).*((2./sqrt(pi)).*sqrt(t)+(e.^t).*erfc(sqrt(t)-1)). (18)
For the experiment T was already know, 5273 K, but for the new speed this temperature is used as the desired temperature Tdes. The temperature which is reached in the time that the laser is active is determined using the calculated time and discrete step pulses.
Conclusion
With a research from M. Kalyon and B.S. Yilbas on laser pulse heating[52] the new temperature when driving 160 km/h could be obtained. When the calculations are performed and discrete constant I_0 is determined the newly reached temperature T can be calculated. The newly reached temperature T is equal to almost 5000 Celsius degrees. The difference in a percentage is -1,7248 x 10^-14 % which is really small. This means that a laser can theoretically be used at a speed of 160 km/h. The reason that the difference in temperature is really small is due to the fact that a laser travels at the speed of light (3 x 10^8 m/s). The increase of speed from the train (22.1 m/s) almost fully disappears in ratio with the speed of light. A visualisation of how the laser will work is shown in Figure 14.
In Practice
The calculations above show that it is theoretically possible to lift the compressed leaves from the railhead but in practise some extra instruments are needed. In the calculations the assumption was made that there were no other obstacles covering the compressed leaves on the railhead. In practise other not yet compressed leaves and/or a thin layers of snow are covering the compressed leaves from the laser. To make sure the compressed leaves are not covered a brush is placed in front of the laser. This brush cleans the the railhead from the not yet compressed leaves and the thin layers of snow. The laser can now directly hit the compressed leaves which will make them expand and get lifted from the railhead. The next thing is that the leaves are now lifted from the railhead but not yet removed. To make sure the leaves are removed from the railhead another brush is placed behind the laser. In the previous section about the sweeper is was concluded that a sweeper is not able to remove the compressed leaves from the railhead. This is still true but in this case the compressed leaves are not compressed anymore because they are lifted from the railhead. The required torque to remove the leaves from the railhead is now way less than when the leaves are compressed. The DagBlad still uses one motor to operate all the four brushes (left and right railhead, in front and behind the laser) which means that the new requirements for the motor have to be calculated. The difference between the previous calculations for the motor requirements is that for this calculation the pressure is not taken into account, the leaves are already lifted from the railhead, and that the mass of just the leaves and snow is used.
Mass
To calculate the new requirements of the motor the mass of the leaves and snow has to be calculated. The weight of compacted or wet leaves is equal to 550 lb. per cubic yard and the weight of loose and dry leaves is equal to 150 lb. per cubic yard[53]. As a rule of thumb snow has a weight of 20 pounds per cubic foot[54]. Cubic foot is converted to cubic yard using
CY = CF x 0,037037037, (19)
where CY is the volume in cubic yard and CF is the volume in cubic foot. To convert the volume from cubic yard to cubic meter the following equation is used
CM = CY/1,3080, (20)
where CM is the volume in cubic meter. The weight of the leaves and snow is also given in pounds but in this case it is easier to convert them into kilograms before continuing the calculations. This is done by using the following equation
kg = lb x 0,45359237, (21)
where kg is the mass in kilograms and lb is the mass in pounds. The mass the brushes have to remove can then be calculated using the following equation
M_x = w x h x d x CM x kg, (22)
where M_x is the mass which needs to be removed from one of the three obstacles, w is the width of the railhead, h is the height of the leaves or snow and d is the effective diameter of the brush. In this calculation the height is chosen to be the maximum value, so 20 um for compacted leaves, 8 cm for snow and for the loose leaves no data could be found so a value of 1 cm is used. The calculations for M_x has to done 3 times: for the compacted or wet leaves, loose and dry leaves and the snow. The total mass is then equal to
M = 2 x (M_compacted_leaves + M_loose_leaves + M_snow), (23)
where M_compacted_leaves is the mass of the compacted or wet leaves, M_loose_leaves is the mass of the loose and dry leaves and M_snow is the mass of the snow that has to be removed. Finally the mass to be removed has to be multiplied by 2 because the motor will drive the brushes for the left railhead but also for the right railhead. The full calculation can be found in Appendix D. The new motor requirements are shown below when the brush rotates at a speed of 200 km/h and the efficiency is equal to 76%:
- Power = 741,4328 Watt
- Developed torque = 0,4089 Nm
- RPM = 1377,9 RPM
This is realistic and doable. It also shows that the LSRPM 132 M has specifications which are a lot higher which means a smaller and cheaper motor can be used. The new motor which is going to be used is the E2T IEC 80 M4D. This motor has the following specification[55] :
- Power = 750 Watts
- Torque = 0,5245 Nm
- RPM = 1430 RPM
- Efficiency = 79,6 - 76,0 %
- Weight = 12,5 kg
- Price = 140 euro[56]
The laser that will be used is the Adapt Laser Systems Lasersystem CL 1000 with the following specifications[57]:
- Power = 1000 Watts
- Electrical requirement = 3 x 480 Volts
- 25000 pulses/second
- Weight = 1030 lbs
The brush that is going to be used has a diameter of 770 mm. The bristles of the brush are made out of flexible polypropylene. Due to this flexible polypropylene bristles the railway itself is not damaged while the snow and leaves are removed from the railhead. The lifetime of polypropylene itself, without using it, is over 400 years[58]. The fact that the DagBlad is is using the brush to remove obstacles from the railhead the lifetime will be way less due to wear. The exact lifetime of the brushes is hard to calculate and not much information can be found about the wear on the internet. The company Johnston sweepers gives a 2 year 2000 hours warranty on their sweepers[59]. This means that an average sweeper from them needs to be able to operate 2000 hours. The DagBlad operates 10 hours per day which means in the worst case scenario the brushes operate for 9 hours, the 1 hour loss is for the stopping of the train and accelerating. This means that the brushes can survive for 222 days and then a replacement for the brushes is needed. The prices for the brushes from Johnston Sweepers cannot be found separately on the internet and therefore brush from another company is used as a reference. A brush from Ganesh Brush, which can be ordered in a customized size, has a price of 1800 Rs which is equal to €23,15[60], this means that the price for a brush from Johnston Sweepers will probably be €50,- due to the quality difference. When calculating the price for one year of sweeping the prices per brush will be €82,21. The DagBlad has 4 brushes and therefore the price for the brushes will be €328,83 per year. To determine the total weight of the sweeper structure the weight of the WSP24 - Walk Behind Sweeper is used which is equal to 133lbs[61]. The structure, including the motor and handlebars, has an approximate weight of 110 lbs which leaves 23 lbs for just the sweeper structure. This 23 lbs is equal to 10,5 kg which is reasonable. The DagBlad needs 4 brushes which means that the total weight of the sweeper structure is equal to 42 kg without the motor.
Rust
In the beginning of this project it was thought that rust also caused problems and that it should be removed with the use of the DagBlad. When we contacted Prorail it became clear that rust is not a critical problem, due to the continues driving of the trains, the rust has no time to be created. With this information it is decided not to focus on rust on the train tracks anymore.
Metal
Next to leaves, snow, ice and rust, loose metal objects can also form an obstacle on the railway. Currently, not much research or work is available on metal trash collecting on and around railway tracks. The main reason for this is that metal trash is not a common obstacle on the railway. Although, it does not form a significant problem yet, a solution to this problem was still analyzed to check whether implementing it would be beneficial or disadvantageous. So to clean the railway from these metal obstacles, a magnet can be used to collect all the trash. Magnets can attract other iron-containing materials, such as trash cans on the railway, which is useful when cleaning the railroads. An article published by ProRail in 2017 [62] revealed that a machine is already being used to tackle this problem. Therefore, metal will not be focused on any further.
Component List
In this section of the wiki a list of necessary components for the DagBlad robot is shown.
Electrical
Product | Amount | Price per unit | Mass per unit | Picture |
---|---|---|---|---|
E2T IEC 80 M4D[56] | 1 | €140,- | 12.5 kg | ![]() |
Coupler system type 430 | 2 | ~€16.500,- | Unk. | ![]() |
Computer (Arduino UNO) | 1 | €12,99[63] | 25 grams | ![]() |
UIC568 | 1 | ~€42,- | ~10 kg | ![]() |
Adapt Laser Systems Lasersystem CL 1000 | 2 | €427.500,-[57] | 467,2 kg | ![]() |
Software
For our robot to be functional, it must be able to perform several tasks, getting rid of the leaves and snow automatically by using it’s sweepers and lasers, for this we need to implement the computer system/brain of the robot such that it is able to do so. For this we program the robot using Arduino software, the software must be able to activate the sweepers and the lasers when the train is riding over 30 km/h.
Speed Sensors
We get the information about the speed of the train [64] from the speed sensor that the train already has. [65] The train uses magnetic speed sensors [66] the technique is also known to be called the Hall Effect.[67]
The RPM is calculated by using a counter that counts the steps and the disk slots which is a constant that depends on of slots in the disk, we divide the counter by the disk slots and then do it times 360,00 as we want to know the rotation in hours instead of seconds. Once the number of rotations per hour is found and put into a float, the wheel diameter which is in millimeters times pi times the previous float will give us a new float giving us the number of millimeters the train rides in an hour therefore we divide this float by 1 000 000 such that we get the speed of the train in km per hour.[68]
This information is already calculated by the computer system of the train also known as the Train Communication Network [69] where the data from all the wagons is stocked during a train ride. To be able to get this information to our computer system the robot will make use of the UIC568 cable, this is a cable used in the majority of the trains in Europe [70] these cables are also the cables used by the Train Communication Network to get data from it’s different wagons, like the wagon containing the speed sensor. Now that we are able to get the information from the Train Communication Network the program has a search speed method that will look for the speed of the train, this has to run in a loop such that it keeps the speed of the train up to date in the program however before rerunning the search speed method we use a while loop that checks if the speed of the train float is bigger or equal to 30,00 constant float. When the speed is bigger or equal to 30 km/h the robot should start the sweepers and lasers.
Sweepers & Laser
The two sweepers have to rotate in continuous rotation movement we want the left sweeper to go counterclockwise and the right one clockwise this can be done by using to motors that have a different pulse, one at a puls of 1 ms and the other with a pulse of 2 ms however we thought that it would also be possible to use 1 motor for both of them, as we just have to add one extra gear for one of the sweepers. [71]
To activate the motor the program at first needs to be able to know on which pin it is connected, afterwards the connections to the motor driver are put in as integers for example int en = 10; in1 = 9; in2 = 8; then there is a function that has digitalWrite(in3 , High); and digitalWrite(in 4, Low); that are used to have the sweepers turning in the right direction instead of the opposite way, the digitalWrite( en, High); activates the motor which will then activate the sweepers, this function is beeing called when the while loop says that the speed of the train is above or equal to 30 km/h, while in the else part of the loop the digitalwrite( en , Low); which deactivates the sweepers. Also it is digitalwrite( en , Low) when the robot is just starting up. [68]
The Laser as shown in the referenrence [72] has Pinmod(13 , output) in the setup class of the program which defines its position on the computer system. The Laser needs to be activated when the speed of the train gets higher or equal to 30 km/h so in that part of the program there is a digitalWrite(13, High); to activate the laser. In the else part of the loop we have digitalWrite(13, Low); to deactivate the laser, also it’s part of the start up of the robot as the lasers should be deactivated then.
Computer System
The computer system that is going to be used for this project is an Arduino Uno however the motor and the laser are not going to be directly connected to the pins of the arduino as the arduino can not give an enough amount of Volt,[73] Ampere,[74] Watt to feed the laser and the motor therefore an intermediate switch or a mosfet can be used to solve this problem. [75]
Non-Electrical
Product | Amount | Price per unit | Mass per unit | Picture |
---|---|---|---|---|
Hard polypropylene brushes with diameter 770 mm including frame | 4 | ~€50,- | ~10,5 kg | |
Bogie | 1 | ~€25.000,- | ~1.250 kg | ![]() |
Frame | 1 | ~€3.500,- | ~750 kg | ![]() |
Frame and Wheels
A bogie is a chassis or framework that carries four wheels of a train. The bogie is attached underneath a train. Most of the trains of NS make use of the ‘Jacobs bogie’ (see picture), because it is safer, cheaper and quieter. The DagBlad will need a bogie as well. Since the NS uses the Jacobs bogie [76], it is convenient to use this type for the DagBlad as well. It is difficult to find a price range for bogies, but we estimate the cost for a new bogie at around €25.000,- [77]. However, NS stated that they revise old bogies and give them a second life [78]. This means that the DagBlad could possibly make use of an used bogie, which saves a lot of money.
If this is not possible each DagBlad will require a bogie. A bogie is estimated to last 40 years [79], so the costs for all DagBlads are: (80 x 25.000)/40 = €50.000 per year or €625 per DagBlad per year. This price is fairly high, but as mentioned before, we hope to make use of second-hand bogies for the DagBlad.
Cost Analysis

As discussed in the USE aspects, the main aim of the enterprise ProRail is to make as much profit as possible. Furthermore, ProRail is dependent on subsidies and fees for the financing of its activities from the Ministry of Infrastructure and Water Management and other governments. Hence, it is important to analyse the current subsidies, fees and expenses of Prorail and keep the robot price lower than these subsidies and current expenses. Mainly the current expenses of Prorail on management and maintenance of the railway are important to investigate, as this is the area where the robot will be active.
To find these expenses a year report of 2017 was analysed [80], as the year report for 2018 was not yet published. In 2017, ProRail received € 2.583 million to spend as can be seen in Figure 17. from this € 2.583 million 68,5% was received to invest in management and maintenance which equals to € 1.771 million. Eventually they spent € 1.689 million from the received money in management and maintenance. ProRail mainly spends this maintenance money on keeping the railway safe and active. They let the maintenance work carried out as effectively and efficiently as possible by qualified contractors. There are three main maintenance and management activities that are conducted.
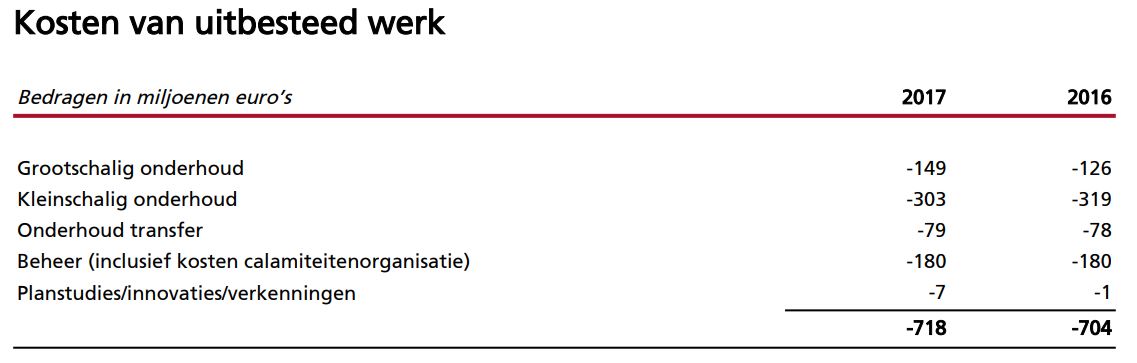
The first activity is large-scale maintenance. This concerns the activities that are necessary to ensure the quality of the maintain infrastructure and achieve long and medium-term lifespan. The activities focus in particular on maintenance and replacement, adjustment and modification of constructions, preservation of objects, grinding of rails and seasoning of the tracks. [80] In 2017, Prorail has spent €109 million on large-scale maintenance, as shown in Figure 18.
The second activity is small-scale maintenance. This concerns the activities that are necessary to improve the availability, reliability and safety. These activities focus on inspections of the infrastructure, correction of track location, replacement of components and functional recovery [80]. In 2017, Prorail has spent €303 million on small-scale maintenance, as shown in Figure 18.
The third activity is the maintenance of the transfer spaces in stations and the management. The maintenance involves cleaning, structural maintenance, troubleshooting, energy, property taxes and insurances. Management relates to the management of IT systems, energy consumption of the rail infrastructure and the deployment in the event of emergencies [80]. In 2017, Prorail has spent €79 million on maintenance of transfer spaces, and €180 million on management, as shown in Figure 18.
From these explanations on the three different activities, it can be concluded that the robot fits within the second activity, small-scale maintenance. As a result, it can be estimated that a budget of €303 million can be used for the robots. However, the robot is not able to cover all the small-scale maintenance problems that arise every year. The small-scale maintenance is mainly focused on solving the problems that arise on the railway that cause delay to passengers. From the statistics on delay causes, it can be found that 2% is caused by weather influences, 7% on construction activities and 9% on external influences [1]. From this total of 18%, it was estimated that 3,5% is related to delay by leafs and snow. Hence, it was estimated that 3,5% of the €303 million small-scale maintenance budget can be used for the robots, which is €10,605 million. This estimation will be used in the calculation, as a preciser number on the budget that is needed for cleaning leafs is not published.
As mentioned in the usability section, at least 80 robots will be needed for a successful implementation of the leaf cleaning system in the Netherlands. Therefore, a maximum of €132.562,50 per robot can be used per year. We aim to keep the costs of the robot lower than this amount per year, as it will increase the possibility of NS and ProRail implementing this robot due to the lower cost.
As can be seen in the component list, the price of one laser is $480.000 which equals €446.761. There are two lasers necessary for each robot, which means that the costs of the lasers will be €893.522,- for each robot. According to the estimations the whole laser system can run for at least 80.000 hours if we replace the diode every 10.000 hours. In the worst case scenario, a robot drives around 6 hours a day. Therefore the two cleaning laser systems must be replaced every 80000/6/365 = 36,5 years. Thus, 1/36,5 * 893522 = €24.480,- will be spend on the laser systems of one robot per year. Furthermore, as discussed in the sweeper section, the price for 4 the brushes will be €328,83 per year. And when only new bogies will be used for the base and wheels of the robot, that will cost around €625 per year. Finally, the computer within one robot is estimated to be €50, as it can be used in combination with the speed sensor that is already built in the train. The frame is estimated to be around €3500 per robot. For the coupler type 430, the original price is not published. However, based on the value of other Scharfenberg couplers, the cost of the type 430 is estimated to be around €16.500,- per unit [81]. The coupler is estimated to be replaced within 20 years of usage, which results in a cost of €16.500 / 20 = €825 per year. The robot will have two couplers which equals to a cost of €1650 per year per robot
Therefore, it can be concluded the robot has an estimated cost of €30.633,83 per year per robot, which results in a total cost of €30.633,83 x 80 = €2.450.706,40. Compared to the estimated €10,605 million that Prorail is currently using for cleaning snow and leaves, the use of 80 Dagblad robots will save at least around €8.154.293,60 (77%) per year.
Conclusion
The DagBlad is a robot that is developed to remove leaves and snow from the railway. These obstacles are the cause of approximately 10% of all the delays on the Dutch railway network. The DagBlad is able to achieve its goal by using a combination of sweepers and a powerful laser.
The sweepers on the front remove a large part of the loose snow and leaves. This clears the way for the laser to tackle the compressed (wet) leaves underneath. Compressed leaves form a low-friction coating, which is dangerous for trains. A sweeper by itself is unable to remove this though layer, so a laser is required. The laser has a specific wavelength of 1064 nm that heats up the leaves and loosens them. A second sweeper is then able to remove the slippery layer from the railhead.
Snow is only dangerous in large quantities (more than 30 cm) or in between switches. When compressed, it can turn into solid ice and block the movement of switches. Switch heaters are designed to melt the snow in between switches, but they cannot handle too much snow. The sweepers are able to reduce these problems, since they prevent snow from accumulating and blocking the switches too much. Switch heaters can then melt the remaining snow away. A 3D-model of the DagBlad can be found in Figure 3 and 4.
In short, the DagBlad is an independent cart that consists of a sweeper, a laser and another sweeper respectively. Due to the overcrowded schedule on the Dutch rail network, it is almost impossible to fit another machine in this schedule. That is why the robot does not move along the tracks independently. It is attached to the front of trains via a Scharfenberg coupler.
Since the DagBlad is designed to tackle weather-related problems, it is mainly used during the autumn and winter seasons. However, the need for the robot is still very dependent on the daily weather. This makes it hard to predict how many of them are needed. A rough estimation has been made by looking at the number of different train lines (114), substracting the number of intercity's (these are redundant) and adding 5 extra robots to the biggest stations, which results in a total of 80 DagBlad robots.
Finally, a cost estimate has been made to predict the feasibility of the DagBlad robots. It will only be implemented if the costs of the development and deployment is lower than the current costs of maintenance and delays. Our estimates indicate that at least 8,15 million euros will be saved by implementing the robot in its current state. This will make it very interesting for ProRail and NS to adopt it.
In conclusion, we see that there is a lot of potential for this robot to be implemented in the Dutch rail network. It will reduce the maintenance costs for ProRail and the number of delays, which saves costs for NS. The DagBlad is robot is thus a cheaper and better solution.
Discussion
The DagBlad is currently an independent cart that can only be used if it is attached to trains. This is a rather inefficient method, since it has to attach and detach regularly. It would be interesting to investigate whether it might be better to attach the DagBlad to the front and back of trains permanently. This reduces the effort involved in attaching the robot. However, this requires all trains to be equipped with two DagBlad units on both sides, which will be a significant one-time investment. Also in terms of coupling the locomotive to the train it might form a problem since each end will be equipped with a unit. The brushes need to be retractable somehow. Further research into this option is required to make valuable claims.
In order to improve DagBlad's current design and functionality, a few things need to be tweaked. The cart could still be a bit lower in height and shorter in length than it is now, so the engineer has a better view over the tracks directly in front of him. This will come in handy at train stations. Making DagBlad smaller also makes coupling, moving and maintenance easier for personnel. The costs will also be reduced since less material is required.
For the current cost analysis the profit was estimated to be at least €8.154.293,60 per year. However, by adopting the DagBlad system, the costs that are caused by delays will also be reduced, as more delays will be prevented by the DagBlad robots. This was not taken into consideration for the cost analysis. To improve the current cost analysis, further research can be done on the estimated profit caused by the delays that will be prevented by the robot.
Sources
- ↑ 1.0 1.1 1.2 1.3 Rijden de treinen, Statistieken. (February, 2019) Retrieved from https://www.rijdendetreinen.nl/statistieken
- ↑ Ramaekers, P., De Wit, T., & Pouwels, M. (2009, February 27). Hoe druk is het nu werkelijk op het Nederlandse spoor? CBS.
- ↑ NS jaarverslag 2017 https://www.nsjaarverslag.nl/jaarverslag-2017/resultaten4/a1054_Punctualiteit
- ↑ Cost of train delays https://www.rijksoverheid.nl/documenten/rapporten/2016/10/24/mobiliteitsbeeld-2016
- ↑ 5.0 5.1 Loading gauge for trains in Europe and also the Netherlands https://en.wikipedia.org/wiki/Loading_gauge#The_Netherlands.
- ↑ NS jaarverslag 2017 https://www.nsjaarverslag.nl/jaarverslag-2017/resultaten4/a1054_Punctualiteit
- ↑ Alles over het spoor, Info over het spoor, (2019). Retrieved from https://www.allesoverhetspoor.nl/feitjes/leuke-feitjes/?gdpr=accept
- ↑ Nachttreinen, Waar en wanneer rijden nachttreinen?, NS. Retrieved from https://www.ns.nl/reisinformatie/bijzondere-trajecten/nachttreinen.html
- ↑ 9.0 9.1 Ontwikkeling spoorgoederenverkeer in Nederland, 2017 vergeleken met 2016, ProRail. (February, 2018) Retrieved from https://zoek.officielebekendmakingen.nl/blg-847011.pdf
- ↑ Langs de rails, Koppelingen. Retrieved from http://www.nicospilt.com/index_koppeling.htm
- ↑ Treinen in beeld Nederland, Scharfenbergkoppeling. Retrieved from https://treinen-in-beeld-1.jouwweb.nl/scharfenbergkoppeling
- ↑ Nederlands materieel technische gegevens, Treinen. Retrieved from http://www.angelfire.com/ego/ist3/trein.html
- ↑ 13.0 13.1 Langs de rails, Spoorwijdte. Retrieved from http://www.nicospilt.com/index_spoorwijdte.htm
- ↑ Kamerbrief 19 oktober 2018, Omvorming ProRail, (October 2018). Retrieved from https://www.internetconsultatie.nl/wet_publiekrechtelijke_omvorming_prorail/document/3990
- ↑ 15.0 15.1 15.2 Scharfenberg couplers, Voith. Retrieved from http://www.voith.com/ca-en/products-services/power-transmission/scharfenberg-couplers-10318.html
- ↑ Scharfenberg couplers for high-speed trains, Voith. Retrieved from http://www.voith.com/ca-en/products-services/power-transmission/scharfenberg-couplers/scharfenberg-couplers-high-speed-trains-14406.html
- ↑ Scharfenberg couplers for railcars, Voith. Retrieved from http://voith.com/corp-en/scharfenberg-couplers/scharfenberg-couplers-railcars.html
- ↑ Scharfenberg couplers for metro, Voith. Retrieved from http://voith.com/corp-en/scharfenberg-couplers/scharfenberg-couplers-metros.html
- ↑ Scharfenberg couplers for monorails, Voith. Retrieved from http://voith.com/corp-en/scharfenberg-couplers/scharfenberg-couplers-monorails.html
- ↑ Spoorkaart 2019, NS, (2019). Retrieved from https://nieuws.ns.nl/download/611967/spoorkaart2019-231351.pdf?_ga=2.11350260.1376181486.1552737761-29200527.1538036593
- ↑ Dienstregeling 2019, OV in Nederland, (2019). Retrieved from http://wiki.ovinnederland.nl/wiki/Dienstregeling_2019#Treinseries
- ↑ Grootste treinstations Nederland, treinStationInfo, (2019). Retrieved from https://www.treinstationinfo.nl/treinreizen/grootste-treinstations-nederland/
- ↑ Spits, OV in Nederland, (2019). Retrieved from http://wiki.ovinnederland.nl/wiki/Spits
- ↑ Track maintenance PBL https://www.prorail.nl/rereizen/aanbesteden-en-inkoop/spooronderhoud-pgo?
- ↑ List of accredited entrepreneurs https://www.prorail.nl/sites/default/files/lijst_erkende_ondernemers_01-02-19.pdf
- ↑ 26.0 26.1 keeping trains moving during snow and ice by NetworkRail. (2017) https://www.networkrail.co.uk/feeds/keeping-trains-moving-snow-ice/
- ↑ Winter weather can present some real challenges, NetworkRail(2017). https://www.networkrail.co.uk/running-the-railway/looking-after-the-railway/delays-explained/snow-and-ice/
- ↑ The best way to melt ice without heat. By Jason Gabriel (April 24, 2017) https://sciencing.com/way-melt-ice-heat-5505463.html
- ↑ Studies of melting ice using CO2 laser for ice drilling. By T.Sakurai,H.Chosrowjan,T.Somekawa,M.Fujita,H.Motoyama,O.Watanabe,Y.Izawa (October the 8th, 2015) https://www.sciencedirect.com/science/article/pii/S0165232X15002116
- ↑ weather station Westland - De Poel http://www.westland-depoel.nl/vantagevue/ws/wxclimate2.php
- ↑ Gamma-ray laser moves a step closer to reality by university college London (April 18th 2018) https://cordis.europa.eu/project/rcn/195403/brief/en
- ↑ Ontijzelschakelaar https://energievoorziening.funnymedia.nl/onderdeelvdmaand/ontijzelschakelaar/ontijzelschakelaar.htm
- ↑ Wikipedia (2019) Wisselverwarming https://nl.wikipedia.org/wiki/Wisselverwarming
- ↑ Wisselverwarming https://web.archive.org/web/20090308032821/http://www.prorail.nl/WeerenSpoor/Pages/Wisselverwarming.aspx
- ↑ 35.0 35.1 A.Pel (2016) Die rotblaadjes op het spoor; waarom doen ze niets? https://www.metronieuws.nl/nieuws/binnenland/2016/11/die-rot-blaadjes-op-het-spoor-waarom-doen-ze-niets
- ↑ 36.0 36.1 Railway Technology (2007) Tackling a Leafy Issue https://www.railway-technology.com/features/feature1457/
- ↑ Nilfisk (2010) High pressure washer on track https://www.nilfisk.com/en/news/Pages/HPW_on_wheels.aspx
- ↑ Prorail (2013) Sandite: slim recept tegen blad op het spoor https://www.prorail.nl/nieuws/sandite-slim-recept-tegen-blad-op-het-spoor
- ↑ DIPOSTEL, Datasheet: Traction gel http://dipostel.com/wp-content/uploads/2017/01/gel-de-traction_ang.pdf
- ↑ jsdrail, Traction Gel Applicators http://www.jsdrail.com/engineering/traction-gel-applicators/9.htm
- ↑ Railroad Tools and Solutions (LLC), Rail Sweeper http://www.rrtoolsnsolutions.com/PowerTools/rail-sweeper.asp
- ↑ 42.0 42.1 Nederlandse Spoorwegen (NS), Hogesnelheidslijn https://www.ns.nl/over-ns/dossier/hogesnelheidslijn
- ↑ Dymaxinc, Dymax rail sweeper for skid steers https://dymaxinc.com/attachments/dymax-rail-sweepers/
- ↑ Overaasen Snowremoval Systems, Railroad Brushes (KM90, 2KM90H and KM120H) https://www.overaasen.no/railroad_equipment/brushes/railroad_brush/
- ↑ 45.0 45.1 LSRPM - Dyneo, Permanent magnet synchronous motor 3 to 350 kW - 1500 to 5500 RPM http://www.leroy-somer.com/documentation_pdf/4936_en.pdf
- ↑ Leroy-Somer, Installation and maintenance LSRPM - PLSRPM http://www.leroy-somer.com/documentation_pdf/4155_en.pdf
- ↑ Kleinetrein, Electric coach-units of the Nederlandse Spoorwegen (Dutch railways) http://www.kleinetrein.nl/spoors_1704/nsm_html/dutch/nsm_eltr.html
- ↑ Tom, Topic: Wieldiameter goederen wagons NS https://forum.beneluxspoor.net/index.php?topic=46384.0
- ↑ 49.0 49.1 L. R. Goodes, T. J. Harvey, N. Symonds and T.G. Leighton, A comparison of ultrasonically activated water stream and ultrasonic bath immersion cleaning of railhead leaf-film contaminant https://www.researchgate.net/publication/304811807_A_comparison_of_ultrasonically_activated_water_stream_and_ultrasonic_bath_immersion_cleaning_of_railhead_leaf-film_contaminant
- ↑ 50.0 50.1 R. Gray, End of the line for autumn train delays? Dutch begin trails to zap leaf litter from the track with LASERS https://www.dailymail.co.uk/sciencetech/article-2860418/End-line-autumn-train-delays-Dutch-begin-trials-zap-leaf-litter-tracks-LASERS.html
- ↑ Hays, R.L. Planta (1975) 125: 281. https://doi.org/10.1007/BF00385604
- ↑ Kalyon, M & Yilbas, Bekir. (2003). Laser pulse heating: A formulation of desired temperature at the surface. Optics and Lasers in Engineering - OPT LASER ENG. 39. 109-119. 10.1016/S0143-8166(02)00088-X.
- ↑ EFCO Company, Swaploader “Hooked on Quality”, Cubic Yardage calculation sheet https://www.swaploader.com/wp-content/uploads/2015/02/Cubic_Yardage_Chart.pdf
- ↑ Evogov, How Much Does Snow Weigh? https://evogov.s3.amazonaws.com/141/media/109213.pdf
- ↑ Elsto Drives & Controls Stokvis Group, elektromotoren https://www.bruinaandrijftechniek.nl/wp-content/uploads/2015/03/Elektromotoren.pdf
- ↑ 56.0 56.1 Elsto Drives & Controls Stokvis Group, Prijslijst 4 https://docplayer.nl/24488165-Power-control-green-solutions-prijslijst-4-motoren-regelaars-servo-nederlands-t-31-0-f-31-0-e-elsto.html
- ↑ 57.0 57.1 Adapt laser systems, Lasersystem CL 1000 https://www.adapt-laser.com/lasersystem-cl-1000/
- ↑ Bio-tec, Lifespan of plastics http://www.goecopure.com/lifespan-of-plastic.aspx
- ↑ Johnston Sweepers, RS655 Sweeper http://johnstonsweepers.us/wp-content/themes/jna/documents/Johnston_specsheet_RS655.pdf
- ↑ Ganesh Brush, Sweeping Brushes https://www.brushmanufacturersindia.in/street-sweeping-brushes.html#sweeping-brushes
- ↑ Sweepster by Paladin, Walk Behind Sweepers https://www.paladinattachments.com/sites/default/files/prod_lit/BR%20-%20SW%20-%20sweepers.pdf
- ↑ ProRail (2017) Magneettrein maakt spoor schoon https://www.prorail.nl/nieuws/magneettrein-maakt-spoor-schoon
- ↑ Conrad, Iduino Compatible board Iduino UNO R3 ATMega328 https://www.conrad.nl/p/iduino-compatible-board-iduino-uno-r3-atmega328-1465104?WT.mc_id=gshop&gclid=Cj0KCQjwnKHlBRDLARIsAMtMHDGfIcVg2R6ZtI5puNzpNAJn0stN2VyeKj4rQQ9TET6Xi9maPzRa3icaAvAVEALw_wcB&tid=958856870_59564775006_pla-633211923346_pla-1465104&WT.srch=1&vat=true&insert_kz=8J
- ↑ Sensor solutions for rail vehicles https://www.lenord.com/fileadmin/kundenbereich/dokumente/broschueren/BRO_railway-solutions_EN.pdf
- ↑ Rail and Transit speed sensors https://www.motionsensors.com/industry-expertise/rail-transit.shtml
- ↑ Railway speed sensors MTR series https://www.baumer.com/se/en/product-overview/rotary-encoders-angle-sensors/hall-and-speed-sensors/mtr-xxx/p/medias/__secure__/en_E_M_Hallsensoren_MTR_xxx_static.pdf?mediaPK=8799686524958
- ↑ What is Hall Effect and How Hall Effect Sensors Work? https://www.youtube.com/watch?v=wpAA3qeOYiI
- ↑ 68.0 68.1 Build a Robot Car with Speed Sensors https://dronebotworkshop.com/robot-car-with-speed-sensors/#Step_4_8211_Install_the_Wheels_Rotary_Encoders_and_Sensors
- ↑ Train communication network https://en.wikipedia.org/wiki/Train_communication_network
- ↑ UIC 568 https://en.wikipedia.org/wiki/UIC_568#Train_communication_network
- ↑ Using servo motors with arduino https://www.youtube.com/watch?v=kUHmYKWwuWs
- ↑ Arduino Laser https://tkkrlab.nl/wiki/Arduino_KY-008_Laser_sensor_module
- ↑ Switch 3-phase power with Uno https://forum.arduino.cc/index.php?topic=338259.0
- ↑ Which is the maximum current Arduino Uno can endure? http://forum.arduino.cc/index.php?topic=301475.0
- ↑ Arduino Power, Current and Voltage limitations https://www.electricrcaircraftguy.com/2014/02/arduino-power-current-and-voltage.html
- ↑ An example of a Jacobs bogie https://commons.wikimedia.org/wiki/File:Jacobs_bogie_of_EER_300.jpg
- ↑ Bray, N., & Vincent, P. J. (2006). Bogie freight wagons of Victoria: A brief history. Sunbury, Vic.: Brief History Books.
- ↑ Revising old bogies https://www.ns.nl/over-ns/treinonderhoud/moderniseren.html
- ↑ Wikipedia (2019) Mat '64 https://nl.wikipedia.org/wiki/Mat_%2764
- ↑ 80.0 80.1 80.2 80.3 80.4 80.5 Jaarverslag 2017, Prorail. (2018) https://www.prorail.nl/sites/default/files/prorail_jaarverslag_2017_def_0.pdf
- ↑ Detailed Import Data of scharfenberg, Zauba. (2018) https://www.zauba.com/import-scharfenberg-hs-code.html
Appendix A
Appendix B
Appendix C
Appendix D
Appendix E
Types of switch heating:
- Central tube heating (Centrale Buis Gas or CBG): this principle is very similar to a boiler in homes. An antifreeze liquid is heated in a boiler and then transported to heat exchangers. Heat is transferred to the snow via conduction and convection.
- Geothermal heat: this method is based on the same principle as the CBG-system. However, instead of a boiler, a heat pump is used. 75% of the necessary energy is generated through geothermal heat, while the remaining 25% through electricity.
- Gas heating: this principle makes use of a controlled combustion of natural gas close to the switch. This melts the ice. The gas is transported to the destination via pipes.
- Electricity: for this variant heat is generated by heating resistors.