BEP Shaft Rescue Robot (2022/2023, Q3): Difference between revisions
(Added more images for the existing solutions.) Tag: 2017 source edit |
m (Added link to Overleaf Project Documentation) |
||
(20 intermediate revisions by 4 users not shown) | |||
Line 1: | Line 1: | ||
==TEAM:== | |||
== TEAM: == | |||
*Luke Alkemade (l.n.alkemade@student.tue.nl) | *Luke Alkemade (l.n.alkemade@student.tue.nl) | ||
Line 10: | Line 8: | ||
*Thomas Leniere (t.leniere@student.tue.nl) | *Thomas Leniere (t.leniere@student.tue.nl) | ||
== Links == | |||
Project Documentation: [https://www.overleaf.com/read/pfpxfzcvkwhp Overleaf (Read-Only)] | |||
<br /> | |||
==<nowiki>'''</nowiki>Borehole/Well Analysis<nowiki>'''</nowiki> (source: https://wikiwater.fr/E28-Various-types-of-wells-and-boreholes-General-points<nowiki/>)'== | ==<nowiki>'''</nowiki>Borehole/Well Analysis<nowiki>'''</nowiki> (source: https://wikiwater.fr/E28-Various-types-of-wells-and-boreholes-General-points<nowiki/>)'== | ||
During the analysis of the different incidents, it was found that most of the cases involved either wells or boreholes. Thus further research into the specifications of these holes should be done. | During the analysis of the different incidents, it was found that most of the cases involved either wells or boreholes. Thus further research into the specifications of these holes should be done. | ||
Line 64: | Line 65: | ||
Undercutting driving involves constructing a large-diameter pipe and digging inside it to lower it gradually. The weight of the pipe pushes it downwards as the digging progresses, and the earth is dug out from inside either manually or with a mechanized bucket that empties the inside of the pipe. Due to the large diameter of the pipe, this method has a lower risk of collapse than percussion driving. However, it may not be suitable for hard ground or areas with rocks or large stones. | Undercutting driving involves constructing a large-diameter pipe and digging inside it to lower it gradually. The weight of the pipe pushes it downwards as the digging progresses, and the earth is dug out from inside either manually or with a mechanized bucket that empties the inside of the pipe. Due to the large diameter of the pipe, this method has a lower risk of collapse than percussion driving. However, it may not be suitable for hard ground or areas with rocks or large stones. | ||
===Drilled wells or boreholes=== | |||
Bored wells are an effective method of sinking wells, allowing for quicker and deeper digging than traditional hand-dug or driven wells. This method involves drilling a cylindrical hole vertically into the ground using a cutting tool such as an auger or drill bit, with the diameter of the well ranging from 5 cm to 1.5 m. Most bored wells are equipped with a water pump, which can be manual, motor-driven or submersible, chosen based on factors such as the well's depth, the desired flow rate, and available resources, both technical and financial. | Bored wells are an effective method of sinking wells, allowing for quicker and deeper digging than traditional hand-dug or driven wells. This method involves drilling a cylindrical hole vertically into the ground using a cutting tool such as an auger or drill bit, with the diameter of the well ranging from 5 cm to 1.5 m. Most bored wells are equipped with a water pump, which can be manual, motor-driven or submersible, chosen based on factors such as the well's depth, the desired flow rate, and available resources, both technical and financial. | ||
Line 82: | Line 83: | ||
===Construction Boreholes=== | ===Construction Boreholes=== | ||
Boreholes are made for a variety of purposes including the investigation and sampling of the geological succession for construction, water abstraction, or mineral extraction purposes, and monitoring of groundwater behavior and composition. Different drilling and extraction methods are used for each purpose. After analyzing the researched cases by the group, all boreholes mentioned in the articles are for water extraction purposes. The accidents happen in well boreholes that dried up and are therefore out of use or boreholes that were unsuccessfully at sampling for ground water. In conclusion, boreholes for other purposes than water sampling/extraction are not relevant in this project case. | Boreholes are made for a variety of purposes including the investigation and sampling of the geological succession for construction, water abstraction, or mineral extraction purposes, and monitoring of groundwater behavior and composition. Different drilling and extraction methods are used for each purpose. After analyzing the researched cases by the group, all boreholes mentioned in the articles are for water extraction purposes. The accidents happen in well boreholes that dried up and are therefore out of use or boreholes that were unsuccessfully at sampling for ground water. In conclusion, boreholes for other purposes than water sampling/extraction are not relevant in this project case. | ||
<br / | |||
===Location and Ground Structure=== | |||
The soil structure for each borehole differs. Every location has a different soil structure as well as the soil structure within a borehole changes depending on the depth. Below is a drilling log from Ratanger, Norway and a drilling log from the Middle East. In both figures show how the drilling speed of a borehole changes based on the soil composition at each depth. The dampness, texture, hardness, and composition changes at each depth. The types of layers differ based on the location as well as the depth at which each layer is found. There is not one uniform rule or characteristic to soil layers around the world. Even within a single country, the composition can differ drastically. | |||
[[File:DrillinglogRatangerNorway.png|left|thumb|Portion of a DTH drilling log from a borehole in Precambrian migmatite gneiss at Hasvåg, Flatanger, ]] | |||
[[File:Penetrationlogmiddleeast.png|center|thumb|Penetration log from a borehole drilled through alluvium and into underlying igneous rock, in the ]] | |||
<ref>Misstear, B. D. R., Banks, D., & Clark, L. (2017). Water wells and boreholes (Second). Wiley Blackwell. Retrieved February 15, 2023, from https://tue.on.worldcat.org/search/detail/1042323330?queryString=water%20wells%20and%20boreholes&clusterResults=true&groupVariantRecords=false</ref> | |||
After being drilled, the boreholes are lined with a metal casing to support the walls and a pumping system is installed. At this point, the borehole does not form a danger to children as it is is covered and fitted with pipes and a pumping system. | |||
Boreholes require maintenance every few years. | |||
Relining or other repairs may not be feasible or | |||
cost‐effective for some wells, which are then | |||
decommissioned or abandoned. If a well is not | |||
decommissioned properly it can lead to a number | |||
of problems. It may pose a physical danger to people and animals. This is especially so with the open well top of a hand‐dug well or a large diameter drilled well. | |||
For example, India has over 27 million borewells, of which several are dried up and no longer in use. In such a situation, usually, the pipe and the iron cast are removed, leaving behind an open hole as visible in the figure below. They are removed to show that the well is no longer useful. In other cases, the water is sampled after the borewell is first drilled. If the result is not satisfactory, the iron cast and the pipes are not installed in the first place and the hole is abandoned. In some minor cases, the casting is still present after the shaft has been abandoned. | |||
In the majority of the cases, the rescue mission is more complicated due to the missing shaft lining. Without the shaft, the borehole is more prone to erosion or collapsing danger. Erosion results in the hole opening being widened which makes it easier for a child to fall into it. During the rescue mission, the unprotected walls are fragile. It can result in debris and dust falling into the shaft as well as part of the shaft collapsing. | |||
[[File:Boreholespain.png|left|thumb|Abandoned borehole in Spain, Photograph: Malaga Fire brigades/HANDOUT/EPA]] | |||
Over the last 30 years, the proliferation of borewells with motorized pumps has allowed farmers ever greater access to precious groundwater. This resource has supported gains in agricultural productivity, particularly in South Asia, which accounts for nearly half of the global groundwater used for irrigation. This aligns with the majority of the borehole accidents happening in South Asia, as it has the highest concentration of boreholes. They are usually drilled in the fields or in small villages that do not have access to a developed water network. In combination with absent safety measures, the high concentration of abandoned boreholes in fields and small villages results in multiple accidents every year.<ref>source: <nowiki>https://www.worldbank.org/en/news/feature/2015/05/26/drilling-down-into-south-asias-groundwater-dilemma</nowiki></ref> | |||
<br clear="all"> | |||
==Analyzing Incidents.== | |||
Before beginning to think about solutions to the design questions, the problem must be clearly understood. To do this, a python database is created, which holds the interesting data found on past accidents. This data includes the following topics: | |||
*Date of the incident | |||
*Country in which the incident took place | |||
*City/Area where the incident took place | |||
*The victim's age | |||
*The victim's weight, if it is known | |||
*The victim's length, if it is known | |||
*The victim's gender | |||
*What type of hole the incident occured with | |||
*The depth of said hole | |||
*The width of said hole, if it is known | |||
*Whether the victim survived or not | |||
*The time required to retrieve the victim's body | |||
*Method used to reach the body | |||
*Whether oxygen had to be supplied to the victim. | |||
This database is still missing a lot of entries, so the data is not yet representative, but the following has been found so far. | |||
[[File:HoleAccidentAgeDistribution.png|none|thumb|350x350px|Distribution of Victim Ages]] | |||
[[File:HoleIncidentCountryDistribution.png|none|thumb|467x467px|Distribution of Countries where incident occurred]] | |||
==Existing Solutions== | ==Existing Solutions== | ||
Line 90: | Line 137: | ||
As of now, there is no scientific or reliable method is available, only a manual rescue method is used to save the child who fell into the bore well, where a big hole is dug beside the bore well to the depth the child is stuck (shown below). If the child is closer to the surface a rescuer gets in and pulls them out. However, if the child has fallen to greater depths, a camera is sent into the hole and then a parallel bore is dug. From there another horizontal bore is dug. Quiet often the rescue succeeds but not always. For more information on the rescue procedure [https://ndrf.gov.in/sites/default/files/SOP%20BOREWELL.pdf click here]. | As of now, there is no scientific or reliable method is available, only a manual rescue method is used to save the child who fell into the bore well, where a big hole is dug beside the bore well to the depth the child is stuck (shown below). If the child is closer to the surface a rescuer gets in and pulls them out. However, if the child has fallen to greater depths, a camera is sent into the hole and then a parallel bore is dug. From there another horizontal bore is dug. Quiet often the rescue succeeds but not always. For more information on the rescue procedure [https://ndrf.gov.in/sites/default/files/SOP%20BOREWELL.pdf click here]. | ||
[[File:tunnel_method.png|frame|left|300px|Parallel tunnel method.]] | [[File:tunnel_method.png|frame|left|300px|Parallel tunnel method [https://www.sciencedirect.com/science/article/pii/S2214785321027322].]] | ||
Advantages to this type of solution include: | Advantages to this type of solution include: | ||
* Old fashion method that doesn't require new technologies. | |||
*Old fashion method that doesn't require new technologies. | |||
Disadvantages to this type of solution include: | Disadvantages to this type of solution include: | ||
* Large amounts of human resources such as rescuers, and heavy machinery such as tractors, JCBs etc. are required | |||
* Huge rock at a certain depth in a borehole results in re-initiation of the whole process | *Large amounts of human resources such as rescuers, and heavy machinery such as tractors, JCBs etc. are required | ||
* Requires a lot of time [15-72 hours] | *Huge rock at a certain depth in a borehole results in re-initiation of the whole process | ||
* Complicated geology calculations for the precise tunnel positioning | *Requires a lot of time [15-72 hours] | ||
* A lot of Geology is involved and rescue plans must be fast and precise. Even with the best geophysical instruments, it is not easy to estimate the type and size of rock that blocks access to the point where the child is stuck | *Complicated geology calculations for the precise tunnel positioning | ||
* Drilling through rock can make the entire Bore well collapse | *A lot of Geology is involved and rescue plans must be fast and precise. Even with the best geophysical instruments, it is not easy to estimate the type and size of rock that blocks access to the point where the child is stuck | ||
*Drilling through rock can make the entire Bore well collapse | |||
====Challenges==== | ====Challenges==== | ||
In order to create a list of requirements for the rescue system, it is important to define all the challenges of the process. This list must be updated and later can be used for creating the RPCs. | In order to create a list of requirements for the rescue system, it is important to define all the challenges of the process. This list must be updated and later can be used for creating the RPCs. | ||
* Tender and small age of victims | |||
* Remoteness of bore well locations | *Tender and small age of victims | ||
* Lack of supportive infrastructure | *Remoteness of bore well locations | ||
* Confined space | *Lack of supportive infrastructure | ||
* Low visibility | *Confined space | ||
* Law and order issues | *Low visibility | ||
* Operation against time | *Law and order issues | ||
* Weather condition | *Operation against time | ||
* Fallen derbies on the child during the rescue. | *Weather condition | ||
* Lack of immediate oxygen supply | *Fallen derbies on the child during the rescue. | ||
*Lack of immediate oxygen supply | |||
===Robot arm=== | ===Robot arm=== | ||
One commonly researched solution was one that used some form of a robot/pneumatic arm to reach down into the bore well and pick the child up. In some cases, these arms have claws/grippers/animatronic hands which are meant to hold onto the head of a trapped child and pull them up that way. Other proposed solutions assume that there is enough free space between the child and hole walls to hold the child by or under their arms to pull them out. To lower the robot arms the system would either use a length of rope or have a cylindrical frame that would fit into the hole. | One commonly researched solution was one that used some form of a robot/pneumatic arm to reach down into the bore well and pick the child up. In some cases, these arms have claws/grippers/animatronic hands which are meant to hold onto the head of a trapped child and pull them up that way. Other proposed solutions assume that there is enough free space between the child and hole walls to hold the child by or under their arms to pull them out. To lower the robot arms the system would either use a length of rope or have a cylindrical frame that would fit into the hole. [https://www.researchgate.net/profile/Madhankumar-s/publication/325010343_Design_of_Bore_Well_Rescue_System_using_Morphological_Chart/links/5eb0d7ee45851592d6b96a80/Design-of-Bore-Well-Rescue-System-using-Morphological-Chart.pdf] | ||
<gallery | <gallery widths="300px" heights="300px"> | ||
File:claw.png|Solution with a claw. | File:claw.png|Solution with a claw [https://www.researchgate.net/publication/344870084_Investigation_and_analysis_on_child_rescue_system_from_open_bore_well]. | ||
File:underarms.png|Grippers that go under the arm. | File:underarms.png|Grippers that go under the arm [https://d1wqtxts1xzle7.cloudfront.net/53812044/IRJET-V4I6658-libre.pdf?1499673644=&response-content-disposition=inline%3B+filename%3DDesign_and_Development_of_Child_rescue_M.pdf&Expires=1676451985&Signature=Y0yxHL-8EdhrEIp562qZX8QXXsweSyuNVuvBlGsZtqE4soc~ckwHtv63tQ03f4rzzGpCYaHjgZ1hbsXRfwWGE3bHU3ihcUrO9dbomQtMzHYcgFLpddbvN-P6SEzL7riYWjyFuhjx80bNqjjubyD38UNTx3bW3bVpP6jODqGf7g3oFKspoYkU~wKOv1Tzt~it1hb25I6rOSgWJXvdo66jOI0os0Zm1dK0t5MYS6kJ1zcuv65WNwe-dAOcS8sDmrf4b-YuJnzxNXHH4zqGYm-xRuqPvhkBto77HRdDzYzXYvsn2ONBINO0eS6GpcuJKIe0i7DCt52nM9Fxjv0rivhuYg__&Key-Pair-Id=APKAJLOHF5GGSLRBV4ZA]. | ||
File:pangolin.png|Animatronic hands. | File:pangolin.png|Animatronic hands [https://ieeexplore.ieee.org/abstract/document/9297864]. | ||
</gallery> | </gallery> | ||
In addition to the claws, the proposed systems are often fitted with other components to help with the operation of the robots or provide life support to the child. Other components can include cameras for surveillance of the child or detecting/handling their body. Sensors such as infrared can be used to detect the depth of the hole and distance to the child. They can also be used to monitor the temperature of the hole environment, in addition to gas, ultrasonic, PIR and other sensors for monitoring the health of the child or detecting dangerous substances in the hole. Then, oxygen supply systems are lowered with the arm to keep the child alive for the duration of the rescue mission. | In addition to the claws, the proposed systems are often fitted with other components to help with the operation of the robots or provide life support to the child. Other components can include cameras for surveillance of the child or detecting/handling their body. Sensors such as infrared can be used to detect the depth of the hole and distance to the child. They can also be used to monitor the temperature of the hole environment, in addition to gas, ultrasonic, PIR and other sensors for monitoring the health of the child or detecting dangerous substances in the hole. Then, oxygen supply systems are lowered with the arm to keep the child alive for the duration of the rescue mission. [https://ieeexplore.ieee.org/stamp/stamp.jsp?tp=&arnumber=8524550][https://jespublication.com/upload/2022-V13I60182.pdf][https://ieeexplore.ieee.org/abstract/document/9297864] | ||
Advantages to this type of solution include: | Advantages to this type of solution include [https://www.researchgate.net/publication/344870084_Investigation_and_analysis_on_child_rescue_system_from_open_bore_well]: | ||
*It is meant to be cheaper than the traditional parallel tunnel method. | |||
*Lower costs for equipment required and how much manpower a rescue mission needs. | |||
*Higher reliability and efficiency, thus, the shorter amount of time needed to carry out a rescue mission. | |||
*It can be assembled together with life support devices such as oxygen supply systems or camera surveillance hardware, so everything needed for the rescue mission would all be in one assembly. | |||
*When the arm is fitted with rubber grips it can reduce the chances of the child slipping out of grasp. | |||
Disadvantages of the solution include: | Disadvantages of the solution include: | ||
* Sensors used for functions such as accurate positioning or location of the child might not always be reliable due to sensitivity issues. | |||
* Lifting a child up by their head or arms might not be very comfortable or safe, especially if they have already been injured as a result of falling into the hole. | *Sensors used for functions such as accurate positioning or location of the child might not always be reliable due to sensitivity issues. | ||
* A lot of the robot arm solutions assume it is possible to fit balloons or other components around or under the child, but in many instances, there is little to no space between their body and the hole wall. | *Lifting a child up by their head or arms might not be very comfortable or safe, especially if they have already been injured as a result of falling into the hole. | ||
*A lot of the robot arm solutions assume it is possible to fit balloons or other components around or under the child, but in many instances, there is little to no space between their body and the hole wall. | |||
===Balloon mechanism=== | ===Balloon mechanism=== | ||
Some proposed solutions in research papers that were found suggested the use of balloons to provide a seat for the child to rest on in order to pull them out. In one solution shown below, a rack and pinion mechanism lowers a cylindrical cage and then extends rods around the child under which a balloon is inflated, thus, creating a protective casing. On the right of the figures below is a similar solution that works on the principle of lowering a cylindrical tube that encases the child and inflates a balloon underneath to support them while being lifted out of the hole. | Some proposed solutions in research papers that were found suggested the use of balloons to provide a seat for the child to rest on in order to pull them out. In one solution shown below, a rack and pinion mechanism lowers a cylindrical cage and then extends rods around the child under which a balloon is inflated, thus, creating a protective casing. On the right of the figures below is a similar solution that works on the principle of lowering a cylindrical tube that encases the child and inflates a balloon underneath to support them while being lifted out of the hole. [https://citeseerx.ist.psu.edu/document?repid=rep1&type=pdf&doi=a273cd4100df6b0462cbe8fa8fb37cfa0347f400] | ||
< | <gallery widths="300px" heights="300px"> | ||
File:ballooncasing.png|Extended rods with balloon [https://d1wqtxts1xzle7.cloudfront.net/64757500/IRJET_V7I9475-libre.pdf?1603545646=&response-content-disposition=inline%3B+filename%3DIRJET_Borewell_Child_Rescue_System.pdf&Expires=1676451657&Signature=ffsE21X2P9EaJ82PXxJqY8M4PDAelSEP4T3cqzAoAFUIRISk8cR9TctFxjwJP21lbHhbv4aF5u8OzKlX9A31oRgtobtS7q072auhdF2-Nxe6WBH31BULSEj5e82TQIfXY0vlk5uzUen5CPNZLogBXWEjiuqMsKBIiduH9Sj-FqF1xWNx7GXFWz1yizbrqoKGiuZPo6iCHageybs0FZYRWXL9P7EsBFD4x2U3uFouWaS-Va7AplHsTkVwDB4ZBg2Kd0MXXUAmzXybmT2hngD38vOI2bN-a9p2DNvocSIGFuAw3j0a2fPkbmv8nsKdwwy8DmowM-ED9blsHJ9GzaYdkA__&Key-Pair-Id=APKAJLOHF5GGSLRBV4ZA]. | |||
File:balloonbaby.png|Glass cylindrical tube with balloon [https://citeseerx.ist.psu.edu/document?repid=rep1&type=pdf&doi=a273cd4100df6b0462cbe8fa8fb37cfa0347f400]. | |||
</ | </gallery> | ||
Similar to the robot arm solutions, these configurations are also usually fitted with sensors (temperature, smoke, oxygen, proximity, and so forth) to detect the environment of the hole and monitor the child's condition. Additionally, cameras are used to provide some visual surveillance of the situation and help guide the movement of the electronics. Then, oxygen pipes are of course used to keep the child breathing while they are still stuck. | Similar to the robot arm solutions, these configurations are also usually fitted with sensors (temperature, smoke, oxygen, proximity, and so forth) to detect the environment of the hole and monitor the child's condition. Additionally, cameras are used to provide some visual surveillance of the situation and help guide the movement of the electronics. Then, oxygen pipes are of course used to keep the child breathing while they are still stuck. [https://citeseerx.ist.psu.edu/document?repid=rep1&type=pdf&doi=a273cd4100df6b0462cbe8fa8fb37cfa0347f400] | ||
Advantages of this balloon mechanism include: | Advantages of this balloon mechanism include [https://d1wqtxts1xzle7.cloudfront.net/64757500/IRJET_V7I9475-libre.pdf?1603545646=&response-content-disposition=inline%3B+filename%3DIRJET_Borewell_Child_Rescue_System.pdf&Expires=1676451657&Signature=ffsE21X2P9EaJ82PXxJqY8M4PDAelSEP4T3cqzAoAFUIRISk8cR9TctFxjwJP21lbHhbv4aF5u8OzKlX9A31oRgtobtS7q072auhdF2-Nxe6WBH31BULSEj5e82TQIfXY0vlk5uzUen5CPNZLogBXWEjiuqMsKBIiduH9Sj-FqF1xWNx7GXFWz1yizbrqoKGiuZPo6iCHageybs0FZYRWXL9P7EsBFD4x2U3uFouWaS-Va7AplHsTkVwDB4ZBg2Kd0MXXUAmzXybmT2hngD38vOI2bN-a9p2DNvocSIGFuAw3j0a2fPkbmv8nsKdwwy8DmowM-ED9blsHJ9GzaYdkA__&Key-Pair-Id=APKAJLOHF5GGSLRBV4ZA]: | ||
* Time required to rescue the child is a lot shorter in contrast to the parallel tunnel method. | |||
* There is no need to do more digging in order to get to the child. | *Time required to rescue the child is a lot shorter in contrast to the parallel tunnel method. | ||
* When fitted in a cylindrical enclosure, this leaves room for additions such as cooling or other comfort options. | *There is no need to do more digging in order to get to the child. | ||
* Can be used in combination with a robot arm to support the child while the arm has a hold on them. | *When fitted in a cylindrical enclosure, this leaves room for additions such as cooling or other comfort options. | ||
* When deflated, the balloon can be moved around and under the child. | *Can be used in combination with a robot arm to support the child while the arm has a hold on them. | ||
*When deflated, the balloon can be moved around and under the child. | |||
Disadvantages of the proposed solution include: | Disadvantages of the proposed solution include: | ||
* As was the case for the robot arm solution, there also might not be any space to fit something past the child trapped in the hole. | |||
* Dimensions of borewells can often be too small to fit a cylindrical enclosure around a child. | *As was the case for the robot arm solution, there also might not be any space to fit something past the child trapped in the hole. | ||
* The balloon needs to be inflated to the right amount which corresponds to the size and weight of the child. This requires additional sensors just to monitor how much air is being pumped in. | *Dimensions of borewells can often be too small to fit a cylindrical enclosure around a child. | ||
*The balloon needs to be inflated to the right amount which corresponds to the size and weight of the child. This requires additional sensors just to monitor how much air is being pumped in. | |||
<references /> |
Latest revision as of 11:11, 1 March 2023
TEAM:
- Luke Alkemade (l.n.alkemade@student.tue.nl)
- Arif Ashworth (a.j.ashworth@student.tue.nl)
- Guillem Ribes Espurz (g.ribes.espurz@student.tue.nl)
- Stijn Michiels (s.f.h.michiels@student.tue.nl / +31 6 12871230)
- Vadims Kisels (v.kisels@student.tue.nl)
- Thomas Leniere (t.leniere@student.tue.nl)
Links
Project Documentation: Overleaf (Read-Only)
'''Borehole/Well Analysis''' (source: https://wikiwater.fr/E28-Various-types-of-wells-and-boreholes-General-points)'
During the analysis of the different incidents, it was found that most of the cases involved either wells or boreholes. Thus further research into the specifications of these holes should be done.
Wells can be classified into three types :
- hand-dug wells
- driven wells
- drilled wells or boreholes
In this section the different types of wells will be explained and there will be a analysis on the dept, diameter and the change of collapse.
Hand-dug Wells
With the exception of modern wells, these wells are manually dug holes in the ground using shovels, picks, and similar tools. Typically, they are not very deep and range from 8 to 20 meters. There are two main catogrories of Hand dug wells these are traditional wells and modern wells.
Traditinal wells
Traditional wells are constructed using local resources and traditional methods, often with the assistance of professional well-diggers. These wells are dug by hand without concrete spouts, and the walls are supported only by wood or branches. The diameter of these wells varies, but they tend to be smaller than modern wells. Traditional wells can be split up into two subsections, temporary wells and permantent wells.
Temporary wells
Temporary wells are quickly constructed with simple linings of branches or straw and are typically less than 10 meters deep. However, they require regular reinforcement to prevent collapse, and the amount of water they can supply is limited.
Permanent wells
Permanent wells are dug deeper, often reaching depths of 10-20 meters or more. Experienced well-diggers construct these wells, and the diameter typically ranges from 0.8 to 1 meter. Although they have a longer lifespan than temporary wells, the walls of permanent wells may deteriorate over time if not supported adequately.
Modern wells
Modern wells are often constructed with mechanical digging equipment, although hand digging may also be used. The diameter of these wells varies from 1 to 1.8 meters, and the walls are firmly supported by a metal or concrete casing. The wells are topped with a margelle (coping) and protected from animals.
Change of Collapsing
Temporary digging wells are typically shallow and used for short periods. These wells have a higher chance of collapsing due to their lack of structural stability, which can result in injuries and fatalities. The walls of these wells are not lined with any materials, which increases the risk of collapse. Additionally, temporary wells may be dug in areas with soft soils, which can quickly erode, further increasing the risk of collapse.
Permanent wells are designed for long-term use and are more structurally stable than temporary digging wells. These wells are typically lined with concrete, stone, or brick to prevent collapse, and often have a mechanical pumping system in place to draw water. Although permanent wells are less likely to collapse than temporary wells, they still require regular maintenance to ensure their structural integrity.
Modern hand-dug wells are a more recent development and use modern materials and techniques. These wells are typically lined with precast concrete rings or PVC casing, which makes them more structurally sound and less likely to collapse. Modern hand-dug wells are also designed to allow for easy installation of pumps and other accessories, making them more convenient to use and maintain.
Driven Wells
A driven well, also known as an instantaneous well or sand-point well, is a capture-engineered structure that is dug vertically by driving a perforated pipe with a pointed end directly into the ground using a variety of techniques until it reaches the water table. This technique is suitable for soft or medium-hard ground.
Driving Techniques
There are different driving techniques for driven wells:
- Percussion driving
- Water injection driving
- Undercutting driving
Depending on the driving technique used, driven wells can have varying diameters and depths, with the desired flow rate also playing a role.
Small-diameter wells with depths of less than 15-20 meters can be dug using percussion driving. Water injection driving can dig wells up to around 30-40 meters deep, while large-diameter wells with depths of 15-20 meters can be dug using undercutting driving. However, driven wells are generally limited to shallow or average depths of less than 40-45 meters and are more exposed to contamination and drying out during periods of drought.
Change of collapsing
The manufacturing method of a driven well can have different effects on the surrounding ground, depending on the driving technique used.
Percussion driving involves driving a pipe into the ground using a heavy tool and has the potential to cause the ground to collapse. This technique is not suitable for hard ground and requires the ground to be free of stones or rocks. If the ground is at risk of collapsing, a preliminary well casing must be inserted and removed when the final pipe is installed.
Water injection driving involves injecting water under pressure to create a hole in the ground. The water wells up at the bottom of the hole outside the pipe walls and rises to the surface of the ground as mud containing the ground cuttings. This mud can stabilize the walls of the well, reducing the risk of collapse.
Undercutting driving involves constructing a large-diameter pipe and digging inside it to lower it gradually. The weight of the pipe pushes it downwards as the digging progresses, and the earth is dug out from inside either manually or with a mechanized bucket that empties the inside of the pipe. Due to the large diameter of the pipe, this method has a lower risk of collapse than percussion driving. However, it may not be suitable for hard ground or areas with rocks or large stones.
Drilled wells or boreholes
Bored wells are an effective method of sinking wells, allowing for quicker and deeper digging than traditional hand-dug or driven wells. This method involves drilling a cylindrical hole vertically into the ground using a cutting tool such as an auger or drill bit, with the diameter of the well ranging from 5 cm to 1.5 m. Most bored wells are equipped with a water pump, which can be manual, motor-driven or submersible, chosen based on factors such as the well's depth, the desired flow rate, and available resources, both technical and financial.
Borehole drilling methods vary based on geological characteristics, depth, flow rate, and borehole diameter. Manual drilling is cost-effective, suitable for shallow depths and soft ground, and uses cheap manual tools such as augurs. Boreholes with diameters between 50-140mm are drilled manually, while mechanized drilling is used for diameters ranging from 100-160mm for light equipment and up to 1500mm for heavy machinery.
Manual drilling techniques include hand-auger drilling, percussion drilling, jetting or washbore drilling, and rotary manual or rota sludge drilling. Hand-auger drilling is used for depths up to 15-25 meters and soft ground. Percussion drilling can be used for depths up to 25 meters and is commonly used for drinking water. Jetting techniques, including rapid pressurized jetting and rotary manual or rota sludge drilling, can be used for depths up to 35 meters and 40 meters, respectively.
Mechanized drilling methods such as compressed air percussion drilling use compressed air to drive a drill bit into the ground. This technique is commonly used for deeper boreholes, up to hundreds of meters deep, and in hard ground. The diameter of these boreholes can range from 76-203 mm, depending on the specific needs of the project.
Change of collapsing
The likelihood of borehole collapse can vary depending on the drilling method used. Generally, manual drilling methods have a higher risk of borehole collapse than mechanized drilling methods. This is because manual drilling often relies on human power and does not provide as much control over the drilling process, which can result in irregular borehole shapes that are more prone to collapse.
Hand-auger drilling, for example, typically results in a borehole that is relatively narrow and straight, which may be more prone to collapse than other methods. Percussion drilling and jetting methods, on the other hand, tend to create a more irregularly shaped borehole that can be more resistant to collapse. Additionally, these methods often involve the use of drilling fluids, which can help to stabilize the borehole and prevent collapse.
Mechanized drilling methods, such as compressed air percussion drilling, typically have the lowest risk of borehole collapse. This is because these methods involve precise control over the drilling process, allowing for the creation of a smooth and consistent borehole shape that is less prone to collapse. The use of drilling fluids in mechanized drilling methods can also help to stabilize the borehole and prevent collapse.
Construction Boreholes
Boreholes are made for a variety of purposes including the investigation and sampling of the geological succession for construction, water abstraction, or mineral extraction purposes, and monitoring of groundwater behavior and composition. Different drilling and extraction methods are used for each purpose. After analyzing the researched cases by the group, all boreholes mentioned in the articles are for water extraction purposes. The accidents happen in well boreholes that dried up and are therefore out of use or boreholes that were unsuccessfully at sampling for ground water. In conclusion, boreholes for other purposes than water sampling/extraction are not relevant in this project case.
Location and Ground Structure
The soil structure for each borehole differs. Every location has a different soil structure as well as the soil structure within a borehole changes depending on the depth. Below is a drilling log from Ratanger, Norway and a drilling log from the Middle East. In both figures show how the drilling speed of a borehole changes based on the soil composition at each depth. The dampness, texture, hardness, and composition changes at each depth. The types of layers differ based on the location as well as the depth at which each layer is found. There is not one uniform rule or characteristic to soil layers around the world. Even within a single country, the composition can differ drastically.
After being drilled, the boreholes are lined with a metal casing to support the walls and a pumping system is installed. At this point, the borehole does not form a danger to children as it is is covered and fitted with pipes and a pumping system.
Boreholes require maintenance every few years. Relining or other repairs may not be feasible or cost‐effective for some wells, which are then decommissioned or abandoned. If a well is not decommissioned properly it can lead to a number of problems. It may pose a physical danger to people and animals. This is especially so with the open well top of a hand‐dug well or a large diameter drilled well.
For example, India has over 27 million borewells, of which several are dried up and no longer in use. In such a situation, usually, the pipe and the iron cast are removed, leaving behind an open hole as visible in the figure below. They are removed to show that the well is no longer useful. In other cases, the water is sampled after the borewell is first drilled. If the result is not satisfactory, the iron cast and the pipes are not installed in the first place and the hole is abandoned. In some minor cases, the casting is still present after the shaft has been abandoned. In the majority of the cases, the rescue mission is more complicated due to the missing shaft lining. Without the shaft, the borehole is more prone to erosion or collapsing danger. Erosion results in the hole opening being widened which makes it easier for a child to fall into it. During the rescue mission, the unprotected walls are fragile. It can result in debris and dust falling into the shaft as well as part of the shaft collapsing.
Over the last 30 years, the proliferation of borewells with motorized pumps has allowed farmers ever greater access to precious groundwater. This resource has supported gains in agricultural productivity, particularly in South Asia, which accounts for nearly half of the global groundwater used for irrigation. This aligns with the majority of the borehole accidents happening in South Asia, as it has the highest concentration of boreholes. They are usually drilled in the fields or in small villages that do not have access to a developed water network. In combination with absent safety measures, the high concentration of abandoned boreholes in fields and small villages results in multiple accidents every year.[2]
Analyzing Incidents.
Before beginning to think about solutions to the design questions, the problem must be clearly understood. To do this, a python database is created, which holds the interesting data found on past accidents. This data includes the following topics:
- Date of the incident
- Country in which the incident took place
- City/Area where the incident took place
- The victim's age
- The victim's weight, if it is known
- The victim's length, if it is known
- The victim's gender
- What type of hole the incident occured with
- The depth of said hole
- The width of said hole, if it is known
- Whether the victim survived or not
- The time required to retrieve the victim's body
- Method used to reach the body
- Whether oxygen had to be supplied to the victim.
This database is still missing a lot of entries, so the data is not yet representative, but the following has been found so far.
Existing Solutions
Parallel tunnel
As of now, there is no scientific or reliable method is available, only a manual rescue method is used to save the child who fell into the bore well, where a big hole is dug beside the bore well to the depth the child is stuck (shown below). If the child is closer to the surface a rescuer gets in and pulls them out. However, if the child has fallen to greater depths, a camera is sent into the hole and then a parallel bore is dug. From there another horizontal bore is dug. Quiet often the rescue succeeds but not always. For more information on the rescue procedure click here.
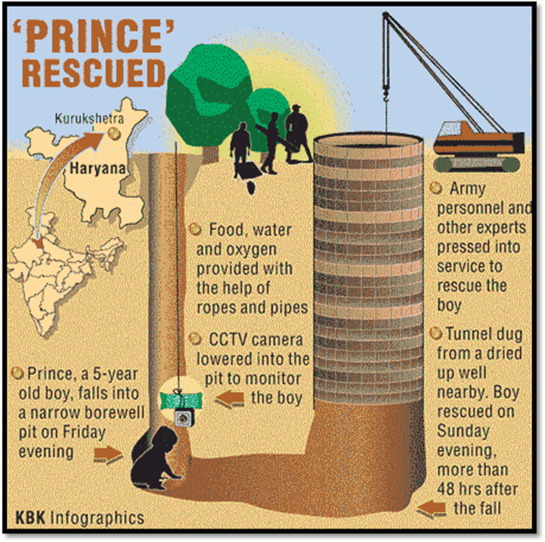
Advantages to this type of solution include:
- Old fashion method that doesn't require new technologies.
Disadvantages to this type of solution include:
- Large amounts of human resources such as rescuers, and heavy machinery such as tractors, JCBs etc. are required
- Huge rock at a certain depth in a borehole results in re-initiation of the whole process
- Requires a lot of time [15-72 hours]
- Complicated geology calculations for the precise tunnel positioning
- A lot of Geology is involved and rescue plans must be fast and precise. Even with the best geophysical instruments, it is not easy to estimate the type and size of rock that blocks access to the point where the child is stuck
- Drilling through rock can make the entire Bore well collapse
Challenges
In order to create a list of requirements for the rescue system, it is important to define all the challenges of the process. This list must be updated and later can be used for creating the RPCs.
- Tender and small age of victims
- Remoteness of bore well locations
- Lack of supportive infrastructure
- Confined space
- Low visibility
- Law and order issues
- Operation against time
- Weather condition
- Fallen derbies on the child during the rescue.
- Lack of immediate oxygen supply
Robot arm
One commonly researched solution was one that used some form of a robot/pneumatic arm to reach down into the bore well and pick the child up. In some cases, these arms have claws/grippers/animatronic hands which are meant to hold onto the head of a trapped child and pull them up that way. Other proposed solutions assume that there is enough free space between the child and hole walls to hold the child by or under their arms to pull them out. To lower the robot arms the system would either use a length of rope or have a cylindrical frame that would fit into the hole. [7]
In addition to the claws, the proposed systems are often fitted with other components to help with the operation of the robots or provide life support to the child. Other components can include cameras for surveillance of the child or detecting/handling their body. Sensors such as infrared can be used to detect the depth of the hole and distance to the child. They can also be used to monitor the temperature of the hole environment, in addition to gas, ultrasonic, PIR and other sensors for monitoring the health of the child or detecting dangerous substances in the hole. Then, oxygen supply systems are lowered with the arm to keep the child alive for the duration of the rescue mission. [8][9][10]
Advantages to this type of solution include [11]:
- It is meant to be cheaper than the traditional parallel tunnel method.
- Lower costs for equipment required and how much manpower a rescue mission needs.
- Higher reliability and efficiency, thus, the shorter amount of time needed to carry out a rescue mission.
- It can be assembled together with life support devices such as oxygen supply systems or camera surveillance hardware, so everything needed for the rescue mission would all be in one assembly.
- When the arm is fitted with rubber grips it can reduce the chances of the child slipping out of grasp.
Disadvantages of the solution include:
- Sensors used for functions such as accurate positioning or location of the child might not always be reliable due to sensitivity issues.
- Lifting a child up by their head or arms might not be very comfortable or safe, especially if they have already been injured as a result of falling into the hole.
- A lot of the robot arm solutions assume it is possible to fit balloons or other components around or under the child, but in many instances, there is little to no space between their body and the hole wall.
Balloon mechanism
Some proposed solutions in research papers that were found suggested the use of balloons to provide a seat for the child to rest on in order to pull them out. In one solution shown below, a rack and pinion mechanism lowers a cylindrical cage and then extends rods around the child under which a balloon is inflated, thus, creating a protective casing. On the right of the figures below is a similar solution that works on the principle of lowering a cylindrical tube that encases the child and inflates a balloon underneath to support them while being lifted out of the hole. [12]
Similar to the robot arm solutions, these configurations are also usually fitted with sensors (temperature, smoke, oxygen, proximity, and so forth) to detect the environment of the hole and monitor the child's condition. Additionally, cameras are used to provide some visual surveillance of the situation and help guide the movement of the electronics. Then, oxygen pipes are of course used to keep the child breathing while they are still stuck. [13]
Advantages of this balloon mechanism include [14]:
- Time required to rescue the child is a lot shorter in contrast to the parallel tunnel method.
- There is no need to do more digging in order to get to the child.
- When fitted in a cylindrical enclosure, this leaves room for additions such as cooling or other comfort options.
- Can be used in combination with a robot arm to support the child while the arm has a hold on them.
- When deflated, the balloon can be moved around and under the child.
Disadvantages of the proposed solution include:
- As was the case for the robot arm solution, there also might not be any space to fit something past the child trapped in the hole.
- Dimensions of borewells can often be too small to fit a cylindrical enclosure around a child.
- The balloon needs to be inflated to the right amount which corresponds to the size and weight of the child. This requires additional sensors just to monitor how much air is being pumped in.
- ↑ Misstear, B. D. R., Banks, D., & Clark, L. (2017). Water wells and boreholes (Second). Wiley Blackwell. Retrieved February 15, 2023, from https://tue.on.worldcat.org/search/detail/1042323330?queryString=water%20wells%20and%20boreholes&clusterResults=true&groupVariantRecords=false
- ↑ source: https://www.worldbank.org/en/news/feature/2015/05/26/drilling-down-into-south-asias-groundwater-dilemma