PRE2024 3 Group13
Ice extraction on the moon
Authors:
Name | Student ID | Email address |
---|---|---|
Bas Coppus | 1706160 | b.coppus@student.tue.nl |
Mikolaj Pujanek | 1732595 | m.p.pujanek@student.tue.nl |
Maksim Fisekovic | 1889524 | m.fisekovic@student.tue.nl |
Ingmar Verweij | 1629433 | i.verweij@student.tue.nl |
Thomas Passon | 1890190 | t.passon@student.tue.nl |
Ideas (REMOVE THIS SECTION LATER)
Maybe the classification structure could be:
Mayor type [Thermal, Mechanical]
Minor type [Crushing, Sieving, Discrete, Continuous]
Explanation of method (how does it work)
Data about the method (How efficient is it (g/kWh, kg/h), what are its limitations (cannot process hard regolith, etc.))
Abstract
A key challenge in establishing a permanent human presence on the Moon is securing a reliable, local source of drinking water, as transporting it from Earth is prohibitively expensive. This paper presents a comprehensive review of existing and proposed methods for extracting water ice from the lunar surface. It begins with a background on the availability and physical form of water on the Moon, then categorizes and evaluates extraction techniques. Each method is assessed based on mass, time, and power efficiency, with results organized in a comparative table for reference. In highlighting both established technologies and recent innovations, this review aims to guide future research and engineering efforts toward efficient lunar resource utilization.
Introduction
Background
In the last few years, the Moon has seen renewed interest from space agencies, notably with NASA’s Artemis mission aiming to reestablish human presence on the Moon for the first time since the 1970s. The mission's goal is to have a settlement on the Moon as a stepping stone for a settlement on Mars [1]. Space exploration and settlement come with many challenges, one of which is setting up the necessary infrastructure to support human life on alien worlds. Aside from a breathable atmosphere and a suitable temperature range, space explorers will need access to drinking water. This paper aims to give an overview of the current state of this engineering problem for the specific case of obtaining water on the Moon.
The chief aim of this paper is to provide a review of the currently available methods for lunar ice extraction. To our best knowledge, no such review has been written yet, except for the brief mention of water extraction in [2]. Hence, for the sake of developing a comprehensive review, we will not only include recently developed methods, but older ones as well. Our target audience is academics and engineers alike who wish to expand their knowledge about this research area. For this reason, the paper will also include a background section on the availability of water on the Moon - where it can be found and in what form. Afterwards, various methods developed for the extraction of lunar water will be presented, categorized, and compared.
Relevance of the topic
Here: include stuff from initial literature review
Settling on the moon has many major benefits, mainly, its abundance of resources. One of these resources is the existance of Helium-3 (He3 or He-3).[3]This resource can be used in various fusion reactions to produce power[4], which could aid in the green energy transition. This resource, when mined on the moon, can be used to power systems and infrastructure on site, but it can also be transported back to earth, to be used for power there. Another resource is various metals and other compounds used for manufacturing.[5]
A method to transport these resources back to earth, is the so called 'Mass Driver'. This machine uses coils with a current through them to accelerate payloads to massive speeds, to quickly reach the escape velocity of the moon in order to send them to earth. This is useful, due to the lack or scarceness of resources to make propellant on the moon.[6]
A plan to extract the Helium-3 out of the lunar regolith, which is abundant in shadowed regions on the moon, due to the effect of solar exposure on the Helium-3 contents[7], is the 'Mark' design, which uses solar energy and heat to extract He-3 from the regolith.
In order to transport these resources between the mining site and the mass driver, two different methods could be used, a lunar railroad[8] or wheeled lunar rovers[9]
From these efforts to research infrastructure related to the exploitation of Helium-3, it is clear that NASA establishing a presense on the moon is pretty likely. Of course, any advanced operations require infrastructure, and transporting the necessary materials from Earth is prohibitively costly. Therefore, inquiries are being made into using the resources available indigenously on the Moon. One specific problem, for a small settlement on the moon, is the amount of water it needs per crew member. Sending water from earth to the moon is very expensive, $2,000 to $20,000 per kg[10], so it is more economical to harvest ice on the moon's surface. According to Nasa's Human Integrated Design Manual estimates a 118 Liter of water is needed to support a crew of 18 people with regenerative live support. This means that the system needs 6.47 kg per crew member per day [11]. To meet this quota, ice has to be extracted from the surface of the moon by robots. This ice does not lay as snow or big chunks on top of the regolith, but as grains of ice between the grains of regolith. There are various ways of capturing these grains of ice, such as sieving, thermal extraction and grinding.
Comparison of extraction methods
The aim of this paper is to provide a "map" of all the different methods for extracting lunar ice. This will be done by listing the different methods and designing a classification system that can be used to identify methods by different constraints. Each method will be explained thoroughly and will be distinguished by different efficiency ratings: mass efficiency (how much water is it able to extract from the regolith based on the water contents), time efficiency (how many liters of water can it extract per hour) and power efficiency. The latter will be expressed in energy needed to extract the desired 118 liters of water per day. In order to provide a broad survey of the extraction methods, each method will additionally have possible limitation or constraints noted. Each of the findings will be summarized in a lookup table, which will have each type of efficiency noted. After this, eventual missing data will be summarized and future research in the field will be discussed.
Ice on the moon
In this section, we give a general background for the paper's topic. This is meant to familiarize the reader with the overview of the problems associated with extracting water on the Moon. We will explain where water can be found and in what form, and introduce relevant physical phenomena. We also lay out the characteristics of lunar regolith, i.e. the rocky soil that covers the Moon's surface, especially in the context of how it can harbor water.
Ice location on the moon
[1] https://science.nasa.gov/solar-system/moon/nasas-lro-lunar-ice-deposits-are-widespread/#:~:text=Prior%20studies%20found%20signs%20of,Haworth%2C%20Shoemaker%20and%20Faustini%20craters. (cited) [2] https://doi.org/10.3847/PSJ/ad5b55 [3] https://nssdc.gsfc.nasa.gov/planetary/ice/ice_moon.html (cited introduction)
[1,2] Found lunar ice in the PSRs (permanently shadowed regions) of the moon like lunar craters near the south pole (77 degrees south). Examples of such locations are some regions of the craters Cabeus, Haworth, Shoemaker and Faustini. [3] Describes how ice detection is done using a neutron spectrometer. Thermal and epithermal (slow and intermediate) neutrons result from collisions of normal (fast) neutrons with hydrogen atoms. A lot of hydrogen atoms would indicate water. Both the north and south pole contain ice.
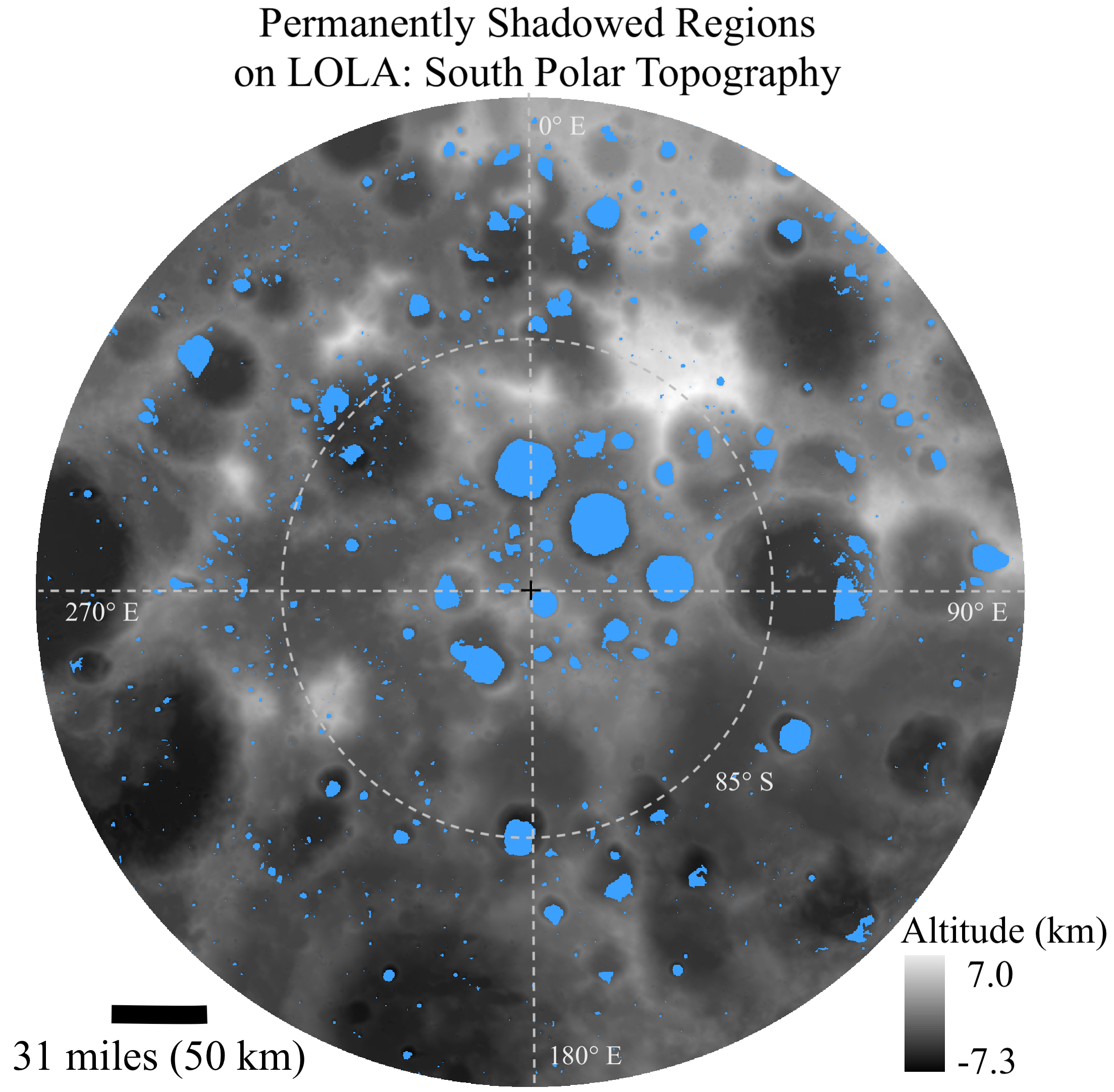
Ice is located in deposits in lunar dust and rock, which is known as regolith. Nasa's Lunar Reconnaissance Orbiter (LRO) mission showed where ice is likely or less likely to find on the moon. Previous studies found that ice is located in the larger permanently shadowed regions (PSRs) near the lunar south pole. Some known areas are the Cabeus, Haworth, Shoemaker and Faustini craters. According to Dr. Timothy P. McClanahan: "We find that there is widespread evidence of water ice within PSRs outside the South Pole, towards at least 77 degrees south latitude”, see figure 1 [12]. According to McClanahan's model and analysis, it is shown that the greatest ice concentrations are expected to near the PSRs' coldest locations, which are below 75 K or -198°C and near the base of the PSRs' poleward facing slopes. They can not determine if the PSRs' ice deposits are buried under a dry layer of regolith. It is expected that for each square meter, at a deposit, there should be five more liters of ice within the surface top one meter, compared to the surrounding areas[12].
Ice sources
On Earth, water exists in solid, liquid and gas form. On the moon however, there exist only the solid and gas form of water. This is due to the ultra cold environment and near vacuum pressure. If the temperature is below 150K water always exists in ice[13].
There are a few processes that contribute as an ice source on the moon. The first one is celestial bodies, containing ice, crashing into the moon. A second process is solar winds injecting H+-ions and a third process is via outgassing magmatic water during the early lunar eruptions[13]. However, the water content of the outgassing magmatic water and the injection of H+-ions is relatively low, so it can be neglected. The most important source is the impacts of meteors which contain ice. When a meteor with ice hits the moon, due to the impact, the ice will be vaporized and a cloud of dust and water vapor will be formed. Some of these water molecules will defuse into space due to the lack of an atmosphere, while others will go back down to the moon's surface. Only the water molecules in a cold trap will remain on the lunar surface, otherwise the water molecules will vaporize and diffuse to space.
Cold traps
A cold trap is a cold area where a hot gas can condense into a liquid. This is for example used in whiskey breweries where they want to have a higher alcohol percentage. They heat up the mixture of alcohol and water, not to the boiling point of water but to the boiling point of the alcohol, which is lower than that of water. This vapor will go to a condenser, which are tubes inside a cold bath. Here the alcohol vapor will condense into a liquid. The same thing happens in a cold trap on the moon. The water gases defuse downward and will collide with the cold areas of the moon. These areas are the permanently shadowed regions (PSRs) of the moon's surface[12]. At these areas, ice will freeze immediately on the moon's regolith. Since the water molecules are adhesive, the frozen water molecules attract other water molecules, which will create a thin ice film on the regolith. These areas can be buried due to impacts by other meteorites.
These cold trapes are unique for celestial bodies, with no or a thin atmosphere, in comparison to Earth. Earth has also a cold trap but not on the surface but in the atmosphere. This cold trap prevents water vapor leaving the Earth. If water is heated on Earth, it will vaporize and start to defuse away from earth till 10 to 17 km above sea level. Here, in the tropopause, the temperature is -80°C and all the water vaper will freeze and form clouds in which water or snow will fall down back to Earth[14]. There is also a protective layer of ozone above the tropopause layer which will protect the water from ionization radiation such that H2 and O2 will be formed in a lesser degree than without the ozone. But the reason why the Moon's cold traps are unique in comparison with other celestial bodies, such as Mercury and Ceres is that the moon does have ice exposed on the surface[15]. This ice can already be found in the top few millimeters of the PSRs' surfaces. (introduction)
Regolith
Regolith is the moons earth. It is important to know what the properties are of regolith, since ice or water vapor will accumulate on it in cold traps. One of the materials of regolith is glass, Nano-phase iron and titanium[16]. From the Apollo 15, 16 and 17 missions, the regolith has a thermal conductivity from 150 to 295 • 10-6 W/cm K[17].
Particle properties
The particle size distribution of the Moon's soil is consistent, even to depths of at least several meters[18]. Earth does not have such equal distribution of particles due to the different ecosystems. The mean particle size is approximately 0.070 mm, in which geologist describe regolith as very fine sand. The average coefficient of uniformity (CU) is 16 and the average coefficient of curvature (CC) is 1.2. CU is the ratio of the grain diameters between 60% and 10% finer relative to a certain set grain diameter. It tells something about the grain size distribution. the smaller the number, the more equal sized particles there are. CC is the value of how well the soil can be compressed under a certain load and how stable it is. Since the CU is 16, its soil is well-graded, which means there are a lot of particles with different sizes. It also gives an impression on how erodible the particles are. The higher the CU the more erodible and unstable the particles are in this case the particles are internally erodible. As a comparison, sand is well graded when CU >6. The CC differs between 1 to 3 for sands[19]. The higher the number of CC, the more the particles can be interlocked with each other and so it can be more compressed and stick together. These properties has to do with the irregular shape of the particles. The particles varies from spherical to angular. Due to these irregular particle shapes, they have a mechanical interlocking mechanism, which explains the cohesive behavior, see figure 2[18]. These irregular regolith particles have an eight times larger surface area than a sphere of the same size.
Bulk and relative densities
The bulk density at the surface is around 1.30 g/cm3 and increases rapidly to 1.52 g/cm3 a depth of 10 cm. Then, more slowly to 1.83g/cm3 at 100 cm and there after it behaves asymptoticly to a value of 1.92 g/cm3. These are the bulk densities of regolith without water[18]. A more interesting and important property is the relative density. This is refers to a given soil can be packed geometrically over a range of bulk densities. Both, the maximum and minimum bulk densities are measured. The minimum is measured such that the soil is lose as possible and the maximum is measured such that the soil is packed as possible without destroying the particles. If the particles break, you alter the particle size and so the soil density. The relative densities are expressed in percentages. A soil is: very loose if the relative density is between 0 to 15%; loose if the relative density is between 15 to 35%; medium if the relative density is between 35 to 65%;dense if the relative density is between 65 to 85% and very dense if the relative density is between 85 to 100%. To give a impression: sand loaded from a truck has a relative density of 30%. It is relay hard to obtain very high and very low relative densities on Earth. For example: heavy equipment used for making highways and dams achieve a relative density about 65 to 75%[18].
On the moon the relative density is set on the surface to be 0% and increases to 84% for the first 30 cm and 97% for the next 35 cm. This large change in relative density with the increasing depth has to do with the impacts of small meteorites. These meteorites stirrup the surface, which makes it loose, and at the same time compress the underlying soil. The relative density below 10 cm is much greater than it can be accounted for by compression under the soils own weight.
Astronauts have measured the relative densities of fresh craters. They concluded that the relative densities of the soil where low on the rim of the craters. But on the inside of the craters, the relative density was high. In the first 15 cm, the relative density is 65%; and from 30 to 60 cm, it was 92%[18].
Despite the high relative density of the regolith, it is very porous. Its porosity is about 40 to 50%[18]. Porosity is the void fraction in a material. The lower the number the less voids or holes it has. This is an anomaly and it is caused by the irregular particle shape and the higher CU value (the particle size distribution). The smaller particles do not fit correctly in the gaps between the larger particles. This means that even if the soil can be compacted very tightly, its structure, or soil skeleton, is relatively open.
Ice bonding with regolith
It is still unknown how ice freezes between the regolith particles. However, there is a hypothetical way of addressing this problem. In figure 3[20], some hypothetical relationships, or bonding, between ice and regolith is shown[20]. The "Raisins in pudding", and filling relationship are non-excavatable. These types of soil with the low temperatures are as hard as granite. The bridging and "nodules, fracture fills and lenses, might be excavatable but it depends on the degree of cementation. The non-bridging, non-filing supporting and non-supporting are excavatable.
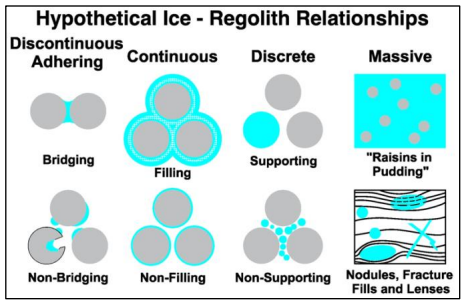
There is no known process or mechanism on the Moon that can create frozen solid mixtures if ice and soil. This has to do with the geothermal gradient pointing upward. This makes the sub surface of a PSR warmer than the surface of the PSR. Because vapor migrates diffusive upward in a thermal gradient, the vapor will deposit only at upper layer of the surface. However, if the sun shines on the surface of the Moon, it will create a thermal wave that pushes the gradient downward. This wave is only dominant in the first 30 to 80 cm. Nevertheless, this thermal wave is not active in a PSR, because sunlight can not reach these areas of the Moon and the refection from other surfaces into a PSR is negligible[20]. When an icy-meteorite hits the Moon's surface and creates vapor that enters a PSR, it will deposit on its top surface in the pore space of the regolith. Since there are no mechanisms or processes that migrate this ice or vapor downward, it will create a vapor barrier on its surface This means that pure ice will build up on the surface and not a mixture of regolith and ice. When this ice breaks in to small pieces, it will create a mixture of pure regolith and pure ice pieces[21].
A second process is that Ice can be re-vaporized due to micrometeorites impacts in PSRs. These impacts will also heat the PSR locally, in which the vapor can migrate to a deeper depth. If it freezes there, then bridging or filling forms can be made. However, this is not the case. The Moon is constantly bombarded with micrometeorites and these bombardments vaporizes the Moon's ice and lithic molecules. But, this vapor deposition does not bond the soil into a solid mass. It is even the opposite, due to the bombardment of the soil, bonds are breaking instead of forming between ice and regolith. There might be a chance that a there was a lot vapor in a short time, in which soil bounds together due to ice formation. These crusts have been found on the Moon, but they where rare and fragile due to the weak bonds. So if bonding with the soil occurs, it will easily break due to the impacts. Due to the heat gradient, vapor deposition only occurs on the top layer of the surface. This concludes that the vapor does not bond the soil.
To create tick coatings, bridging or pore-filling forms, water has to be liquid; seep through the soil and then freeze. This happens on Earth due to gravity pulling on the water molecules, which creates forms of permafrost. On the Moon, however, these processes can not occur with liquid water. It can happen to molten lithic material, but this amount is very small because the only prosses that can make molten lithic is with micrometeorites. Water will freeze immediate due to the low pressure and low temperature. So, thick coatings, bridging or pore-filling forms will not occur on the moon, simply because liquid water can not exists there[20].
Water content of regolith
In this paragraph, the water content of the regolith will be described by the LCROSS experiment and direct measurements via spectral modeling. To simulate the hardness of the regolith with certain water contends, some regolith simulant has been used.
Spectral modeling and the LCROSS experiment
In the past, Epithermal neutrons have been used to measure hydrogen in the upper tens of centimeters of the Lunar soil. However, such measurements can not isolate the uppermost optical surface and can not distinguish H2O, OH and H. Another method is used by the Lyman Alpha Mapping Project (LAMP), which uses reflected ratios of UV light to indicate the presence of water. This instrument was onboard on the Lunar Reconnaissance Orbiter (LRO). Unfortunately, this method can not distinguish water ice and OH. Moreover, if the spacing between the regolith is low or there are very fine particles, it will give a faulty measurement since these UV reflection ratios are nonunique in comparison with that of ice water[15]. Because these methods fail to discriminate OH and H2O ice, near-infrared (NIR) reflectance spectroscopy is used. This method measures the direct vibrations of molecules. It is also possible to discriminate water that is bond in minerals. The NIR reflectance data is required by the Moon Mineralogy Mapper (M(3) ) instrument which was onboard the Chandrayaan-1 spacecraft. This method can detect water contents as little as 5 wt%, which is intimate mixing, or 2 vol%, which is linear areal mixing. But the actual limitations are determined by the instrumental response and signal-to-noise rations. 5 wt% Is the weight ratio in a mixture. In this case, it means that if you have 100 grams of regolith 5 grams is made of ice. The same goes for 2 vol%, but now is it about the volume ratio of a mixture. in this case, if you have 100 liter of regolith, 2 liter is made of ice. The NIR reflectance measurements suggest that there areas in PSRs that contain 30 wt% ice or higher, if it is intimately mixed, or over 20 vol% if ice occurs as patches[15].
The Lunar Crater Observation and Sensing Satellite (LCROSS) was a device to detect direct evidence of ice in PSRs. It had also NIR and eight other measurement instruments on board. It was carried by the Atlas V rocket, the Centaur, along with LRO. To achieve the LCROSS's goal, the upper stage of the Centaur was used to crash it on a PSR named: Cabeus. An hour before the impact, all nine instruments were turned on to make sure that all the ejecta came from the rocket and not from micrometeorites. The reason why they choose this area, was because of the sun light that would illuminate the ejecta from the impact and the shade of the PSR gave a black background. This was needed for certain measurements instruments to operate properly and with the least amount of uncertainty. The result of this experiment is that with the average ejected dust mass of 2175 ± 544 kg, an average water content of 5.6 ± 2.9 wt% has been measured%[22].
Regolith simulants
Regolith simulants are materials that is mend to simulate certain properties of regolith. These materials are made because there is not a lot of regolith on earth and it is expensive to get a lot of it from the Moon to the Earth. The simulant used to simulate icy regolith of the polar regions is named NU-LHT-2M. This simulant is also used for simulating lunar highland regolith. There were 6 samples, in which water was added by 0.2 wt%, 4.6wt%, 9.0 wt%, 12.8 wt%, 17.3 wt% and 20.3 wt% respectively[23]. These samples were frozen overnight with a temperature of -20°C. A 5mm diameter pencil with a conical tip is used to measure the penetration resistance. The 0.2 wt% sample was very soft and very easy to penetrate. The samples ranging from 4.6 wt% to 12.8 wt% had small clumps but were easy to fairly unable to penetrate as the water concentration went up. The samples from 17.3 wt% and higher were a solid block and not penetrable at all. The saturation of this simulant lays between 13 wt% to 17 wt% and a rapid change occurs in a mass range between 5 to 9 wt%, where the simulant gets from soft to very hard. However, this method of freezing water on or in to the simulants is not realistic compared to how water freezes on the Moon. On the Moon, liquid water freezes in Pico seconds[20], so it cannot creep in to the pores of the soil and become a solid block. In the experiment, it took a whole night to let it freeze. So water could creep between the particles and in to the pores. However, there is a lot of unknown information about the water content of the Moon’s regolith. So it might be possible that there exist such icy regolith patches with high water content and this has to be accounted for.
Methods
There are a lot of extraction methods for lunar ice, so, in order to structure them, a classification system was created.
(Image of classifications with branches for each mayor type and those have branches for each minor type)
Example: Example method
- explain briefly what the method is and what classification it falls under (and maybe a brief explanation of this classification)* This method uses magic to create water out of thin air. It is a mechanical, continuous process, because magic is mechanical.
Function
- explain in detail how the method works* This method works by creating ice out of thin air. It does this by using magic.
Scope of Application
- explain what the method can do and where it is applicable* This method can extract 200 gigatonnes of ice per second, however, it is not very feasible with current technology, since there is no 'thin air' on the moon.
etc.
Thermal extraction
https://www.sciencedirect.com/science/article/abs/pii/S0032063320302956 (Thomas)
https://www.sciencedirect.com/science/article/pii/S0032063324001375 (Thomas, can do 1 more but mainly worked on this so far)
https://ntrs.nasa.gov/api/citations/20120009955/downloads/20120009955.pdf ( I have trouble to find this)
https://arxiv.org/pdf/2306.03776
https://ui.adsabs.harvard.edu/abs/2020P%26SS..19305082B/abstract (This one has been done already )
https://www.1-act.com/wp-content/uploads/2022/07/ICES-2022-130-Lunar-Ice-Miner-FINAL-Manuscript.pdf?srsltid=AfmBOoq05-rlx4JxEvtzN-i9Ts2u-BNGwA1eV9QzArr8OX6VnNgTI-qd (Bas finished)
https://ttu-ir.tdl.org/items/df90dcde-dd5b-4f6e-82ba-6674f84af21c (This one is the same as above)
https://www.1-act.com/wp-content/uploads/2021/08/ICES_Paper-235-Lunar-Ice-Miner_revB.pdf?srsltid=AfmBOoow-ps4wXyGZxVFry9RHJaJsRRUd_C0r4LRX-d3zuBvUaWHIZaY (Bas finished)
https://ascelibrary.org/doi/10.1061/%28ASCE%29AS.1943-5525.0001165( finished Bas)
Extraction of ice through the use of thermal extraction is done by applying heat to the surface regolith of the moon. By heating the surface, the ice that is contained in the regolith warms up and escapes by turning into vapor. This vapor is then collected and can be transported in different ways.
There are multiple alternatives of thermal extraction can be used to extract the ice. The first strategy is to homogeneously heat the surface regolith, as can be seen in the figure to the right . The other strategy is to insert heated metal rods into the surface, with different amounts of rods being taken into account. The surface would then be capped to collect the vapor that is escaping from the top. This method can be seen in the figure to the left.
The article "Thermal extraction of water ice from the lunar surface - A 3D numerical model"[24], a numerical model is used to compare these two different methods of thermal extraction. By running different simulations, the two methods are compared for different power levels and different contents of ice in the regolith. The results that are looked at are the time at which the maximum extracted vapor mass was achieved, the maximum extracted vaport mass, the percentage of the available mass that was extracted and the maximum temperature reached in the regolith.
The regolith volume that was considered has a surface of 1.2 x 1.2 m² and a depth of 1 meter. The dimensions were chosen to easily acomodate for different amount of drills. The different regolith ice contents that were considered are the volume percentages of 1%, 5% and 10%. The heating power used for the homogeneous heating was between 1 W and 10 kW. The heating power used for the drills was also between 1 W and 10 kW per drill, with the different amounts of drills being 1, 4, 9, 16 and 25.
When considering the best methods of these two alternatives, the most efficient method is the surface heating method. This method has an extraction effienciency of 59% in the best case. The best case scenario is when the power used to heat the surface is 1 kW, with a volume perecentage of 5. The method then extracts 59% or 42.65 kilos of water. This extraction method takes a long time, taking about 45 hours. The fastest extraction for surface heating takes 7.5 hours to extract 41.3 kilos of water, but this method is less efficient with an efficiency of only 29%, while also using 10 kW on a volume percentage of 10. The heated rods extraction method is a lot less efficient, with the most efficient setup having an efficiency of only 35%. This setup only extracts about 5 kg of water in 5.4 hours, while using 25 rods of 1kW on a volume percentage of 1%. The fastest setup of this method extracts 2.25 kg in 1.07 hours, but only has an efficiency of 1.6%. The power needed for this setup is 25 rods of 10 kW, applied on a volume percentage of 10kW.
The simplifications that are used in this simulation are addressed in a more detailed model.[25]The particular simplification that are adressed are simplifications on regolith emissivity and porosity, water sublimation rate, as well as regolith and water ice thermal conductivity and permeability. The simplifications on regolith emissivity, ice sublimation and thermal conductivity resulted in the simulation showing a slower extraction process and less water being collected. The simplifications on regolith porosity and permeability resulted in the simulation showing a faster process and more water being collected then it should have. Overall, the crude model that was used in the simulations was improved by considering less simplistic models for regolith emissivity and porosity, water sublimation rate, and regolith and water ice thermal conductivity and permeability
Another method for extracting lunar ice using heating is the 'crucible method'. In this method regolith is extracted (mined) from the surface in batches and is heated in a crucible, so called 'discrete' excavators.[26]
These three methods can be compared to each other based on their extraction rate (per hour) and energy efficiency. This gives 0.9 kg/h for the crucible method, 0.32 kg/h for the heated rods method and 0.09 for the surface heating method and the crucible method extracted ~765 g/kWh, the heated rods method ~130 g/kWh and the surface heating method ~25 g/kWh[27] This means that, in order to extract 118 liters of water a day (~5 kg/h), NASA would need 6.5 kW, 38.5 kW and 200 kW for the crucible method, heated rods method and surface heating method, respectively.
Thermal Corer
category
Function
Waste heat-based thermal corer for Lunar extraction is a method similarly to ………. However, waste heat is used to heat the regolith and there are tubes that go into the soil. This waste heat is produced by the on board Multi-Mission Radioisotope Thermoelectric Generators (MMRTGs) and a mechanically pumped fluid loop (MPFL) is used to distribute the waste heat to the components that require this energy[28][29]. A MMRTG is a nuclear power source. One of these components are the heat-based coring drills, or thermal cores, which have little flow channels through the wall of the thermal cores. These drills are hollow inside, which encapsulate the regolith in a cylindrical geometry. When a drill is inserted into the cold soil, the heat will flow through the channels and heat up the soil inside the drill. This will sublimate the ice into vapor. Inside the drill, the inflow channels of the hot fluid are more on the inside if the tube and the channels become larger, such that it increase the residence time. At the bottom of the drill the hot and cold fluid channels merge. At this point, the fluid will flow trough the cold fluid channels, upwards, at the outside of the drill. The thermal cores have a length of 17.3 cm and an inner diameter of 5 cm. There is also a cold trap onboard, which has integrated variable conductance heat pipes (VCHPs). The cold trap has 2 modes without using electricity and moving part, one mode is ice collecting and the other one is ice removing[28][29]. The cold trap consists of a tank with condenser pipes which are connected to a radiator outside the tank. In this tank, there are also heat pipes. During the drilling, there will be no hot fluid trough this tank, and the condenser will be turned on. The water vapor will be turned into ice until the drilling is finished. After that, the hot fluid will flow trough these pipes in the tank and the condenser will be turned off. At this stage, the ice becomes water such that it can be collected[29]. Water will be laying on the bottom of the tank and the condenser pipes will be ice free. This makes the next ice drilling and collecting more efficient and the ice packing more denser[29].
Scope of application
To warm up ice from 40 K and sublimate at 200 K at a rate of 2.78 kg/h, 2.2 kW of thermal energy is needed[28][29]. This energy will be waste energy, so there will be no net energy used. Only the heat pump, drilling and the pressure in the cold trap will cost energy. This energy will be provided by the MMRTG.
Different flow rates and back pressures are used. These back pressures are pressures in the cold trap. In this simulation, the water mass of the regolith is 5 wt%; the temperature of the fluid is 50°C and the regolith’s temperature is -50°C. 3 Different back pressures are used and 3 different flow rates at a back pressure of 0 Pa are used[28], see tables……
Back pressure (Pa) | Extraction rate (kg/min) | Pumping power fluid (W) | Eextraction rate (kg/min) | Pumping power fluid (W) |
---|---|---|---|---|
0 | 1.0 | 0.4 | 1.15 | 1.9 |
5 | 0.9 | 0.4 | 1.09 | 1.9 |
2000 | 0.6 | 0.4 | 0.59 | 1.9 |
Flow rate (cc/s) | Mass fraction (t=0s) | Mass fraction (t=50s) | Mass fraction (t=300s) | Mass fraction (t=600s) | Pumping power (W) | Extraction time (min) |
---|---|---|---|---|---|---|
3.38 | 0.05 | 0.044 | 0.034 | 0.027 | 0.05 | 15.3 |
10.14 | 0.05 | 0.042 | 0.032 | 0.026 | 0.49 | 14.4 |
17.00 | 0.05 | 0.041 | 0.031 | 0.024 | 1.9 | 13.7 |
From these tables, a conclusion can be drawn: the higher the flow rate the more ice can be extracted but the more the pumping power costs and the higher the back pressure, the less ice can be extracted[28]. The extraction efficiency is the amount of water is extracted. With this method, the efficiency is 30% after 17 minutes[28].
A slightly different results are obtained by an other paper. They used an ambient temperature of -20°C, a fluid flow of 3.15 cm3/s, a fluid temperature of 50°C, a back pressure of 700 Pa and a water content of 10wt%. This was not a computer simulation but an actual test whit a heat core. The extraction efficiency is 44%[29]. An other simulation has been made, this time with a computer. Here, the fluid temperature is 400 K; the water mass fraction 5 wt%; a drill length of 50 cm; a drill inner with of 5 cm and an ambient temperature of 40K. From these set variables, an extraction rate of 1.82 kg/min can be obtained.
Further analysis conclude that extracting 1 kg of ice, will cost 2.6 kW/h of waste heat and 0.25 kW/h of electricity. This is based on a water content of 5 wt%; an ambient temperature of 40 K; a sublimation temperature of 250 K; a total extraction rate with the 6 drills of 0.36 kg/h and with a duration of 1 hour of each cycle[29].
Both papers included thermal properties of the soil, such as heat capacity and thermal conductivity. This analysis comes from the Crank–Nicolson model[30]. In this model, the thermal conductivity of dry regolith, just Lunar Ice and gas inside the pores of the regolith have been calculated. The same analysis is made for the specific heat with an addition to the phase change of ice when it melts. This model is also validated with different simulants with different pore porosity and pore vapor pressures. It is a good first model to simulate the thermal behavior of regolith and simulants.
remark ( this name has to be changed)
The water content and temperatures used in the computer simulations are realistic of both papers. The actual set up and test of the second paper is less realistic due to high temperature of the regolith. A second test should be conducted with the simulant temperature much lower than -20°C. According to the simulations of this method, the water extraction efficiency is lies between 30% and 44% depending on the temperature of the fluid and fluid flow. The same dependencies goes for the extraction rates. The extraction rate of 1.82 kg/min seems too optimistic, especially with the dimensions of the core ( a diameter of 5 cm and a length of 17 cm, so the total volume is 0.33L) . It is also not clear how many corers are used. The extraction rate of 0.36kg/h seems more realistic.
A down side is that this method only works with waste heat and a MMRTG. If the robot is driven via other power sources, then this method would not work as efficient as described. The waste heat of 2.6 kW/h has to be generated via another method.
Microwave heating
Function
Another way of collecting water is via microwave heating. This method can be more efficient and faster than thermal heating described above. There are no drills and precise machinery needed, so there are less moving parts that can break down. Moreover, drilling become useless when the water content is above approximately 10 wt%. This based on the simulant in section 1. The Nano-phase iron in side the regolith allows coupling of the micro waves by a 3 orders of magnitude, which enhances the heating efficiency[17].
Scope of application
To test this, a flask is used, which is put in a box with JSC-1 regolith simulant, the simulant bed. The flask itself had also the same simulant and was put under pressure of Torr which is Pa. The simulant in and out-side the flask had a thermocouple to measure the temperature. This set up was put inside a household microwave of 2.45 GHz with a power of 1100 W. To catch the water vapor, a tube went outside the microwave and was coupled to a cold trap. The mass of the simulant inside the flask was 200 g and a water content form 0.5 to 2 wt% was added. The flask and simulant bed was cooled down slowly to -195°C with liquid nitrogen. The JSC-1 simulant, is the only simulant that came close to that of actual regolith. It has a thermal conductivity of 80 10-6 W/cm K. The microwave was turned on and off with interval steps of 30 seconds and max power. After a total 5 minutes of heating, at least 85% of the ice has been evaporated from the simulant and 99% was captured[17].
remarks
This method looks promising, due to the low energy consumption; short time period and high efficiency. However, a second experiment should be conducted but with more mass and a water content of at least 5.6 wt%.
Beneficiation (Aqua Factorem)
While thermal methods are very well researched and often proposed for lunar water extraction, they are highly energy intensive, which poses additional infrastructural challenges. In this section, we will cover “Aqua Factorem”[31] - a NASA-developed paper which proposes an alternative, low-energy approach focusing on regolith beneficiation.
Beneficiation is a standard mining term for separating higher-value material from unwanted material. The Aqua Factorem concept aims to extract lunar ice by taking advantage of the fact that micrometeoroids have already fractured both rock and ice into fine grains over geologic time. Observational evidence (e.g. LCROSS impact[22]) shows that weakly bound or granular ice probably exists near the surface. Even if some bonding of ice to rock fragments exists, only mild mechanical grinding is expected to free the ice grains. Here, they are sorted out at low temperature, then taken to a sunlit area for melting and purification. Because only ice is hauled out of the permanently shadowed region (PSR), and ice makes up only about five mass percent of the original regolith mass[22], the energy and infrastructure requirements - especially for delivering power into the crater - are dramatically reduced.
Extraction method
The system includes small, mobile RASSOR-type[32][33] excavators that dig regolith in a PSR, then pass the soil through a series of mechanical separators, where large rocks and gravel are rejected. Minimal grinding further liberates ice grains if they are bound to lithic grains. Two or more of these excavators can scoop and deliver about 1 ton of regolith per day to a beneficiation unit, where the ice is further separated from the rest of the regolith.
Beneficiation happens in a series of three major steps: pneumatic, magnetic, and electrostatic separation.
Pneumatic separation: Extremely fine dust tends to be the most magnetic fraction and can complicate the next steps, so it needs to be winnowed out. For this purpose, the regolith is entrained into a low‑pressure gas stream (e.g., nitrogen, CO2, or recycled vapors), since it is known that lower-density particles and finer grains will travel farther in a gas flow.. Cyclone separators then drop out heavier grains while carrying lighter or smaller particles onward. This can also group particles by size for more efficient downstream sorting.
Magnetic separation: This step removes the remaining highly magnetic fraction that is not ice (for instance, nanophase iron, basaltic grains, or metal specks), thereby increasing the proportion of non-magnetic ice in the stream. A drum or set of permanent magnets pulls paramagnetic or ferromagnetic particles to one side of a flow path. By repeating multiple times in the same pass, most of the magnetic fraction is diverted out. The PSR’s cold environment actually increases magnetic susceptibility for some minerals, aiding separation.
Electrostatic separation: This is the final cleanup, raising the ice concentration to very high levels. Ice has triboelectric properties distinct from rock, so when particles are rubbed or passed through an ionized environment, they acquire charge in different ways. Subsequently, in an electric field, differently charged particles deflect into separate collection bins. As a result, most remaining silicates, glasses, or metals wind up in one bin; the lighter-charged ice grains in another.
After beneficiation, the ice is hauled out of the PSR into a sunlit area to be melted. Mined ice contains volatile impurities (e.g. CO2, NH3, hydrocarbons), so the water must be purified to prevent contamination. The proposed multi-step approach includes filtration, degassing, reverse osmosis, ion exchange, and catalytic carbon filtering, which are all well-known terrestrial processes. The resulting water is ready to be used for supporting human operations on the Moon.
Scaling and economic viability
Since the energy-hungry steps (water cleanup and purification) happen in sunlight, minimal on-site power is used in the PSR. The expected energy requirement of this method is 100W for an operation producing 100kg of ice per hour, which includes powering the rovers, mechanical separation, and beneficiation. This greatly limits the amount of infrastructure needed in the PSR itself. The number of rovers deployed is also flexible, as the system is able to operate with as few as two rovers, and is scalable to incorporate more of them. This modular design allows gradual scale-up. Initially, a small minimum viable product (MVP) system can begin operations with low capital risk, then be expanded when proven. According to the paper, about 50 kW of power is enough to run the baseline pilot MVP mining system, and solar arrays positioned on nearby ridges (with short lunar nights) can feed cables or charge fuel cells carried into the PSR by the rovers.
Beyond using the water to sustain human operations on the Moon, the Aqua Factorem paper also notes that collected water can be used to make rocket propellant. This can be done in the same facilities used for melting and purification, where clean water would then be electrolyzed and cryogenically stored as LOX/LH2. The report discusses a development path: first, advance the approach to higher technology readiness level via lab and vacuum-chamber testing, then demonstrate small-scale hardware on a low-cost lunar mission (e.g. Commercial Lunar Payload Services, CLPS). Once validated in situ, a commercial-scale version can be funded by private capital, since the approach has relatively low upfront cost and can generate revenue selling propellant to geostationary satellite operators. Furthermore, once a beneficiation plant is operational, it could be repurposed to separate other valuable lunar minerals such as ilmenite (for metals) or anorthite (potential aluminum source), and to recover free metallic iron.
Critique
This approach seems very promising for water extraction on the Moon. Its main advantage is its low power requirement, which is especially crucial since lunar ice is most easily accessible in the PSRs, where energy is hard to come by due to the lack of sunlight. It is also very well-supported scientifically, with Section 2 of the paper detailing how each stage of the beneficiation process has been validated via lab experiments, theory, or analysis. The paper also includes an appendix on the size distributions of ice particles in the lunar soil, inferred i.a. from LCROSS[22] data. Finally, the paper also makes good arguments about the economic viability and scalability of the project, including proposed financing sources and focusing on expanding the operation to manufacture and sell propellant.
A considerable downside of this method is that the various separation methods introduce complexity, which could make the system more prone to failure. Just the mechanical separation stage itself includes several types of sieves and screens, which could require constant human maintenance as lunar rock is very coarse and could jam the mechanisms. The three-stage beneficiation requires specialized equipment and could need frequent maintenance.
The authors of the paper also account for flexibility in how exactly the operation would be implemented based on mission needs. In particular, it is mentioned in the paper that the regolith beneficiation could be performed in a single specialized facility, or onboard the rovers. The latter option has the rover itself carry all the separation systems, so it can dig regolith, pass it through magnetic/electrostatic steps on board, and haul out only the high-ice fraction. This makes the transport more efficient, the operation more flexible (each rover produces ice independently), and it eliminates the single failure point in the form of one central beneficiator. However, if the centralized approach is taken, this reduces the rover cost, increases rover robustness, and facilitates maintainability by concentrating the complex, failure-prone mechanisms in one place. Hybrid approaches are also proposed, for example with part of the beneficiation happening on a rover and the remainder in a central facility. This flexibility is a big advantage of the Aqua Factorem approach, making it a good candidate for water extraction on the Moon.
Crushing and sieving
As mentioned prior, regolith is an amalgamation of sands, grains and particles. Countless different minerals, including water (ice) can be found by analyzing the regolith structures. In order to effectively isolate the different coarse grains, it is necessary to crush and separate the large rocks of regolith found on the surface of the moon. This crushing and sieving of the regolith poses significant challenges due to the distinct characteristics on the moon. Pieces of regolith boast a variety of hardness based on the mining depth and ice percentage present within the rock, therefore, different types of crushers need to be employed for the mining of regolith with specific hardness. Furthermore, the gravity of the moon poses a challenge for the sieving process: separating the desired minerals from the remaining grains is difficult without enough force driving the sieve. This section will explore and summarize the current solutions that boast the highest efficiency in the field of crushing and sieving.
Ice mining without phase change
A paper by Husarova et al.[34] raises concerns that the fine-grain regolith available on the lunar surface does not contain water ice, as the surface temperatures allow ice to sublimate away. In order to increase the efficiency, this paper proposes several improvements with regards to the ideas introduced by NASA: Using a central crushing facility would require excavating and hauling large regolith blocks with only between 2 and 8 mass percentage water ice, which is very inefficient. It is therefore better to crush the regolith on site and extract water there. Furthermore, in order to avoid the sublimation of the ice on the surface, ice should be found at a depth of 11cm and below. Finally, this paper argues that extracting regolith through methods that induce a phase change is inefficient, as in order to change the phase of the ice, it is necessary to use high power, low efficiency devices that produce a lot of heat. Such subsurface ice regolith has the hardness of rock, so in order to avoid phase changes of the ice it needs to be crushed. This requires appropriate machinery, so called crushers. In order to investigate the efficiency and capacity of these crushers, it is first necessary to classify the hardness of the rocks. This is done according to the ice percentage present within a specific piece of rock. For example, rocks with less than 2% ice are classified as soft rocks, with a hardness around 2.0. An ice percentage of 8% yields rocks with a hardness of around 4.0, classifying them as rocks of moderate strength. Finally, any rock that contains 10% ice or more is deemed a hard rock, with a hardness exceeding 8.0. The type of crusher used depends on the hardness of the rock, jaw and cone crushers are to be used for strong rocks, while moderately hard rocks can be handled by roll crushers. Finally, highly efficient, small crushers called impact crushers can be used for softer rocks. The impact crushers are preferred, as they boast the highest efficiency among all the machines. An experiment conducted on earth regarding this method consists of a two-stage method. An impact crusher is used, followed by separation of ice crystals using centrifugal force as mentioned in the previous section on sieving. A conical sieve is used in the centrifugal sieving mechanism, as it simplifies and improves the separation compared to a cylindrical sieve. As mentioned previously, the energy consumption of thermal extraction is in the range of tens of kilowatts (kW). Comparing this crushing method that ensure no phase change of the ice with thermal extraction, it becomes clear that crushing and sieving is far more efficient in terms of energy consumption. The proposed crushing solution is capable of extracting 100 kg of ice with an energy consumption of 118W. This is comparable to the Aqua Factorem system and far more efficient than the thermal extraction methods mentioned previously, as these have a power consumption of at minimum 6500W for a little over 100 kg of ice.
The drawback of this approach is that the crushers operate on extremely hard materials frequently and in quick succession, leading to a lot of wear and tear in the material that constitutes the crushers, as well as the sieve. It is unclear how long one crusher could last while continuously mining rocks and extracting ice, as the paper only briefly mentions this problem, yet fails to propose a sustainable solution. The losses in terms of time, extracted ice and costs need to be determined through further experimentation before a solid conclusion can be drawn regarding the sustainability of this method.
Results
Given the previously mentioned methods, the 'example method' appears, at first sight, to be the most promising, due to its incredible extraction rate of 200 gigatonnes of ice per second. The problem is however, that the lack of thin air makes this method unusable, since there is no way to terraform the moon to form a thin atmosphere, due to its lack of magnetic field. The method 'etc.' appears more promising, because such and such.
The following lookup table lays out the different extraction rates for ease of comparison:
Wiki documentation
Initial literature review
Mass drivers
The paper: "Lunar based massdriver applications" [35] describes that there are two types of mass drivers a Gauss or a coilgun and a Lorentz Rail Accelerator (LRA). Due to the simplistic design of the components and the developed railgun technology, the work in this paper will be considered with the LRA.
The LRA needs to be powered and the best way to do do this is by making PV-panels out of the minerals of the moon, which has an efficiency of 16%. These solar-panels do not track the sun, because they are robust and low in maintenance. This means that only 40% of the lunar revolution (27.3 Earth days) the massdriver can not operate.
A small vehicle is used to load the massdriver. This reduces the retention time within the first acceleration modules. A vehicle with a load is sliding down a ramp in which the barrel of the LRA is at equal height of the payload such that the vehicle and load can detach with each other. In this case a velocity of 1 m/s is used. This way of loading or injecting is needed, otherwise the heat load and friction would damage the modules of the payload. To monitor the launch, a control center is needed with a sufficient height to oversee the launching and if needed breakoff the launch. This breakoff can be done by extending the barrel and do the reverse of the injection process.
The best way to build the massdriver is to use the minerals of the moon. The rails will be made by aluminum due to the higher conductivity per kilogram ratio as copper for example. Oxygen is a by product from a lot of refining metals.
The velocity of the payload increases the barrel quadratically but the acceleration decreases the barrel linearly. So the launch velocity has to be minimized to keep the total acceleration short. A maximum acceleration of 20g is permitted for comparable payload launches at Earth. The payload can directly shoot to Earth via elliptic trajectories. These shots are called Earthshots. The most efficient launch opportunity is at the lunar apogee, but only once shot per lunar orbit can be achieved. So, for frequent launches, an optimized sit is chosen between the perigee and mean lunar distance for balancing energy efficiency and launch frequency. This is feasible when the launch velocity is between 2.1-2.5 km/s and the barrel is between 15-16km long. The best position is at Oceanus Procellarum; Encke and kapler craters and Reiner-Gamma lunar swirl.For large scale projects, a mass of 10 metric tons of payload is needed. This can not be launched in one shot due to technical limitations(the rails would melt due to the high currents). So a stacking concept of multiple LRA's are used. The simplest way is stacking in the width. The gap width between the rails is 200mm, with this geometry, the highest force density can be achieved. To shot the a payload of 10 ton with 20g a current of 560kA is needed and a launch time of 12.5 s can be achieved. The acceleration modules have a length of 1 m, so only the first module has a heating load of 1 s, which will be designed to cope with this. If the massdriver operates continuously, a power of 8.63 GW is needed.
It is also possible to shot these payloads into the lunar orbit for constructing space stations or space crafts. With precise calculation, ships can gather these payloads. These payloads can also be gathered by guiding systems inside the payload.
In the paper "Mission and System Analysis for Lunar Massdriver Applications" [36], only the relevant chapters will be summarized, since it is a thesis of 200 pages. The chapter 5.7.5 Energy production and 5.7.6 Energy Storage will be summarized because as seen from the paper "Lunar based massdriver applications", it takes a lot of energy to operate the massdriver.
According to this paper, if a tracking solar-panel is used, a power of 1210 W per m2 can be harvest from the sun. However, the goal is to use materials from the moon to create low efficiency solar panels, since it is assumed that there are no nuclear or chemical sources are on the moon. These low efficient solar-panels can be made in huge amounts.
Another way of producing power is by using concentrated solar radiation. The complex mirror shapes can easily be produced by rapid prototyping techniques for base structure and coated by highly reflective materials such as aluminum. However, this is not very effective since you need motors which are hard to make with the materials on the moon and the moon has a 2 week cold or dark period so the slat inside the tower will cool down. So the best way of generating power is by stationary solar panels.
Energy storage is also important since that the moon will have no light for 2 weeks. One way is with gravity potential; a second idea is via kinetic energy; a third way is via thermic energy; a forth way via chemical potential and the last idea is via a direct electric storage.
The gravity potential energy storage is based on increasing the height of a certain mass when there is a lot of energy available and lowering the mass when there is no energy available on the moon's grid. The increase and decrease of the height can be done by pumped hydroelectricity plants. But due to the low gravitational force ( 1/6 of the Earth's gravity). Fluid based systems have an efficiency of 80%. This fluid will be liquid oxygen. An more efficient way is via electromotors. They have an efficiency of 94%. Here you only need an electromotor and a lifting mechanism. the masses can be made of regolith blocks.
Kinetic energy storage is based on a big fly wheel that rotes with a large mass. If there is plenty of energy the kinetic energy can be increased and decreased when there is a shortage. Due to near perfect vacuum environment, losses are suspended. Large quantities of energy can be stored in here.
Thermal energy can also be stored in containers of molten regolith. These containers can stay warm during a Lunar night. These high temperatures heat up a gas for example oxygen which goes to a turbine. The efficiency is 62.8%. Another approach is using a phase change of oxygen but it has an efficiency of 7%.
A chemical potential can also be used by reversing the refining process. A lot of oxygen is produced and a chemical reaction like combustion of metals will produce a lot of energy. However, the efficiency is very low and not suitable.
The last way of storing energy is via a direct electrical storage. However, a capacitor is not suitable due to the electrons leakage between the plates. Another way is via a superconducting material. When a current is applied, the current will indefinite time without loss. The conductor has to be thermally insulated and monitored to maintain its temperature below the critical temperature. If superconductors have to be supplied from Earth it is not feasible.
Helium-3 mining
Mikolaj:
For different modes of transportation on the Moon, two main approaches are proposed in literature: a lunar railroad[37], or traditional wheeled rovers[38]. Aerial transport is not possible due to the lack of an atmosphere, and of course for large numbers of autonomous robots, wheeled transport is preferred for its versatility and autonomy. However, if our solution has for example one central hub location with the mass driver, human base etc. and multiple refineries/mining stations, then setting up a railroad may be more efficient in the long run. This depends heavily on the specifics of the resources being mined and the characteristics of their deposits.
There have been studies of the economic and technological feasibility of extracting Helium-3 from regolith on the Moon. They suggest that extracting 100kg of Helium-3 (enough to produce 1GW of fusion power for a year, and approximately the entire supply currently available on Earth) would require processing about 100 million tons of regolith[39], or an area of 2 square kilometers to a depth of 3 meters. The authors cite this as feasible, compared to a typical terrestrial oil mine processing 150 million tons of oil sand in a year. The study is from 2014, and at that time they estimated that the cost of setting up a mine that produces one ton of Helium-3 per year would cost about 17 billion USD, while the estimated value of the produced fuel is 3.7 billion USD, making the project economically viable in the medium term (assuming fusion is solved). With recent breakthroughs in spaceflight cost-efficiency on the back of reusable rockets, such as SpaceX's Starship[40] (already contracted by NASA to help with the Artemis project), the cost of setting up such a mine might be even lower than that.
One proposed method of processing lunar regolith to extract Helium-3 was proposed by Gajda in 2006[41]. It features a large standalone rover that takes care of the entire extraction and refinement process: it uses a bucket wheel to scoop up regolith, isolates the smallest grains containing the Helium-3 using sieves and electrostatic separation, and then heats up the grains to release the Helium-3 along with other volatiles. This approach still needs a dedicated facility for separating the gases present in the obtained mixture. One downside of this approach is that the rover weighs 18 tons and has lots of moving parts, making it difficult and costly to deliver to the Moon, and possibly requiring a lot of maintenance. Our approach using many smaller, specialized robots could improve on this area.
Swarm control
Maksim:
Quick summary of each article: the article: "Time-Efficient Mars Exploration of Simultaneous Coverage and Charging with Multiple Drones "[42] describes a build idea for a robot swarm that would be operational on Mars. This robot swarm would consist of robots of constant speed, operated through an autonomous control principle. By making use of the CACER-II algorithm for pathfinding, as well as layered information maps for gathering data. The article "The Design Challenges of Drone Swarm Control" [43] describes the difference between direct and indirect control, and looks at several possible control scheme implementations. Chapter 4 of the book: "Robot Swarms: Dynamics and Control "[44] goes into depth about the behavior of swarms and how that can be translated into control schemes for swarm robotics. The book offers information about swarm robotics as a whole, instead of focusing only on space applications. The blog: "Robotic swarm swarm intelligence for Lunar exploration"[45] is an extremely well-written summary on existing swarm robotics and goes into depth on exactly swarm robotics in space. A myriad of examples on swarm robotics in space are given, as well as shown in several YouTube videos. While not describing swarm control in great detail, this blog gives many practical examples and implementations of swarms in space, which could form the basis for our control system. The article: "Collective control of spacecraft swarms for space exploration"[46] explains the rules necessary for controlling spacecraft swarms. This is slightly different than our desired project, as this article mainly mentions satellites and swarms travelling through space. However, the rules about swarm control should be applicable to most control systems.
What is the best way to design the swarm control? It is hard to tell, however, using autonomous or semi-autonomous control seems necessary. It is borderline impossible for humans to remotely control the swarm from earth. An information map could be implemented to avoid obstacles and perceive the environment. The robot design meant for Mars uses the CACER - II algorithm for pathfinding. Something perhaps more achievable is a semi-autonomous system for multiple robots as presented in "The Design Challenges of Drone Swarm Control"[43]. In this system, the robots are hardcoded to act based on a set of rules, depending on the position of the so called leader robot. This leader robot is remotely controlled by humans. This implementation seems feasible, as article: "Robotic swarm swarm intelligence for Lunar exploration"[45] claims that a study has been conducted on swarm navigation on planets, where researchers propose communication between units through time-division multiple access (TDMA), which would enable all units to constantly be aware of the position of the other units.
Locations of Helium-3 on the moon
Ingmar: From the paper "The estimation of helium-3 probable reserves in Lunar regolith"[3] it was found that He-3 is implanted into the lunar surface by the solar wind. The problem is not the implantation, however, but the retention of the He-3 within the lunar surface. The retention of He-3 depends on the grain size of the lunar regolith[3] (<50 micron seems to hold the most helium-3), the electroconductivity of the lunar regolith (TiO2 was mentioned)[47] and it also seems to depend on the solar exposure[48], meaning less sunlight is better able to retain the He-3. This would mean that craters at the lunar poles seem to be the best option. The Chang-E-1 mission was able to measure the thickness of the regolith layer by measuring the thermal radiation of the lunar regolith[49][50][51] (I don't fully understand this yet). Another method was found in the paper " Regolith Layer Thickness Mapping of the Moon by Radar and Optical Data "[52] by using radar waves (at 70cm) and measuring the thickness by using scattering from the underlying substrate. There have also been other materials on the surface of the moon, mainly uranium, thorium and platinum-group elements that could be exploited as well[53]. It was estimated that a mine that produces one ton of he3 would cost around 17 billion USD, while this one ton would give profits of around 3.7 billion USD, making it viable in the medium term[54]. “Mare Tranquillitatis” and “South Pole Aitken” seem to provide the most helium-3[55]. Also, energetically, the mining operation seems feasible, since the energy produced is roughly three times as much as the energy consumed in the entire chain of sending equipment to the moon; mining; refining; returning he3 to earth and using it in a reactor[55] .
Mining robots
Thomas:
[1] https://ntrs.nasa.gov/api/citations/20210022801/downloads/AIAA%20ASCEND%202021%20Paper_211018.pdf [2] https://ijcrt.org/papers/IJCRT2108016.pdf [3] https://www.mdpi.com/2075-1702/12/12/845 [4] https://www.mdpi.com/2076-3417/14/19/8876 [5] https://www.mdpi.com/2313-7673/9/11/680
Summary: Mining using robotics is advantageous, because [2] the of health and safety hazards and improved productivity[56]. The mining environment is always evolving, in the sense that the goal of mining is changing a lot, and the equipment are becoming more hydraulically operated and diesel driven. These challenges have meant that robotics has not been rapidly adopted by the mining industry to date, but it is clear that the mining industry will have to adopt more automation, and with robotics[57]. [3] Some possible evolutions of intelligent mining machines are the use of Artificial intelligence to improve the use of data and and deep reinforcement learning for controlling equipment . The use of swarm robotics in mining[58], [4] this article suggests different animal based models for different objectives, namely: the honey-bee model for high selectivity and precision, like extracting high-grade ores, the ant model, with its high reliability and task specialization, may be the most effective one for ore transportation. And finally the firefly model could be used in ore detection.
So far, there are multiple methods theorized for mining Helium-3 on the moon[59] [1]. Among these designs, there is the Mark series, which uses solar energy and heat to extract He-3. Another one of these methods is the spiral method, but this concept is not as far developed, even tough this design could improve flexibility and reduce to complexity and mass of each mining robot.
Mining on the moon using swarm robotics has also been theorized for mining water and ice[60] [5]. One of the limitations that is discussed is disrupted communications due to the lack of atmosphere on the moon. Extreme temperatures and fine, loose rock on the surface pose additional risks, such as traction loss and path deviations. These limitations underscore the need for an adaptable and robust framework when considering mining operations on the moon.
Planning
Here out weekly planning has been written down. This is a rough estimate about what should be done in what week. Since it is a rough estimation, we are more flexible to help each other within the project.
Week 2
Person 1 will start looking at the physical properties of the robots. What sensors do they need, how large the buckets and loading platforms are; operating time of the batteries; charge time; drive speed; what type of usurers are involved and energy usage. Go as detailed as possible.
Person 2 look at where the mines will be placed on the moon. This person also needs to find out how much can be mined and how many mines we need. First, find the top 5 important places then 5 additional or more places if possible. This needs to be done with urgency since we need these places and mines for simulations. try to find an actual map. Also find the quota needed to make this successful
Person 3 starts with simulating the mining robots in an arbitrary environment. The robot needs to dig, drive and recharge. Make some arbitrary points on the map where the robot can dig and recharge. This simulation can be done in NetLogo. Take into account the excavation time and unloading time. Also simulate the battery time and the driving from the digging site to the recharge station. This is called the simple excavating model. Also take the driving into account from the excavation site to the unloading side at the station or refinery
Person 4 looks at the program of the swarm robots. What type of behavior is needed and how to implement it in netlogo.
Person 5 looks at how to map the findings of person 2 into NetLogo including the mines, refineries, charging stations and the massdriver. Based on the findings of person 2, it will be determined if we make one big refinery or smaller ones. Here it is also important to know how much refining kg per material cost in terms of energy. If Person 1 is finished with his findings about the batteries, it can also be implemented in the map.
Week 3
Bas: research and find literature about ice locations and formation on the moon and start writing down a detailed user case.
Thomas: research and find literature about thermal excavation of water
Maksim: research and find literature about sieving the ice from the regolith
Mikolaj: research and find literature about crushing the ice and regolith
Ingmar: Research and find literature about a new method of excavating water and also research crushing
Week 4
Mikolaj: Continue research on the Aqua Factorem method and will expand the part about it on the wiki
Maksim: Continue research on the regolith crushing method and will expand the part about it on the wiki
Thomas: Continue research on the thermal extraction methods and will expand the part about it on the wiki
Bas: Continue research on regolith composition and will expand the part about it on the wiki
Ingmar: Aid Thomas in researching thermal extraction methods and look into chemical lunar ice excavation methods
Week 5
Person 1 finish the research about the ice formation.
Person 2
Person 3
Mikolaj: Restructuring the wiki to resemble a review paper. Extending the introduction to make sense in the context of a review paper.
Ingmar: Add the relevance of the topic to the introduction using the literature review. Write the introductory part of the 'methods' section and include an image with a tree for all the methods. Continue research into thermal methods.
Week 6
In this week the presentation will be made and finished at least at Friday. Everybody is responsible for their one work in the wiki and presentation.
Week 7
In this week on Monday or Thursday, the presentation will be held in the morning.
Week 8
Finishing the Wiki and documentation.
Individual effort
Name | Total time | Progress and time |
---|---|---|
Bas Coppus | 18h | Making small basic sections in the wiki page and trying to understand how to edit the page works (1h). Finding a subject to research and how to implement this research into a program, prototype or a literature research and finding some papers (2h) . Lecture and meetings (4h), Summarizing papers (5h), finding papers (4h), Make a planning (3h) |
Mikolaj Pujanek | 18h | Lecture and meetings (4h), researching what topic to use for the project (5h), finding and reading papers (6h), writing introduction for wiki page (1h), summarizing and extracting relevant insights from papers (2h) |
Maksim Fisekovic | 15h | Lecture and meetings (4h), researching and deciding on a topic (3h), finding and reading papers about the topic (5h), summarizing papers (3h) |
Ingmar Verweij | 17hr | Find a research subject (2h), Lecture and meetings (4hr), Finding literature paper (2hr), Reading literature (6hr), Summarizing literature (3hr) |
Thomas Passon | 13 hr | Lecture and meetings (4h), Finding papers (2h), reading the papers (5h), summarizing papers (2h) |
Name | Total time | Progress and time |
---|---|---|
Bas Coppus | 13h | Meetings (2h), reading papers(9h), structure the wiki and planning (2h) |
Mikolaj Pujanek | 15h | Meetings (2h), studying Lunarminer paper (5h), researching improvements and other papers (8h) |
Maksim Fisekovic | 15h | Meetings (2h), Reading papers (3h), Creating NetLogo simulation (10h) |
Ingmar Verweij | 12h | Meetings (2h), reading paper (4h), researching ice locations on the moon (6h) |
Thomas Passon | 14h | Meetings (2h), Finding papers (2h), researching different extraction methods (10h) |
Name | Total time | Progress and time |
---|---|---|
Bas Coppus | 20h | Meetings (2h), organize the docu wiki (1h), writing the introduction and ice location (7h), reading papers (10h) |
Mikolaj Pujanek | 17h | Meetings (2h), studying crushing/sieving methods (8h), writing for wiki (4h), researching other methods (3h) |
Maksim Fisekovic | 17h | Meetings (2h), studying sieving and crushing and sieving methods (8h), writing for the wiki (5h), researching thermal extraction (2h) |
Ingmar Verweij | 18h | Meetings (2h), Finding papers on alternate ice extraction methods (4h), Reading extraction method papers (6h), Finding papers on regolith crushing (2h), Reading regolith crushing papers (4h) |
Thomas Passon | 15h | Meetings (2h), Finding and reading articles of thermal extraction (8h), starting the writing for thermal extraction (5h) |
Name | Total time | Progress and time |
---|---|---|
Bas Coppus | 16h | Meetings (1h), docu-wiki(12h), additional reading(3h) |
Mikolaj Pujanek | 18h | Meetings (1h), reading Aqua Factorem and supporting papers (11h), writing for wiki (6h) |
Maksim Fisekovic | 16h | Meetings (1h), researching ice hardness and crusher sustainability (8h), additional reading on crushing and sieving (3h), writing for the wiki (4h) |
Ingmar Verweij | 18h | Meetings (1h), Researching chemical extraction methods (6h), Researching and reading thermal extraction method papers (6h), Writing the wiki (5h) |
Thomas Passon | 18h | Meetings (1h), docu-wiki(11h), reading (5h) |
Name | Total time | Progress and time |
---|---|---|
Bas Coppus | 17 h | meeting (2h), docu-wiki(12h), reading (3h) |
Mikolaj Pujanek | meetings (2h), restructuring docuwiki (4h), extending introduction (3h) | |
Maksim Fisekovic | ||
Ingmar Verweij | 18h | Meetings (2h), Writing introduction (6h), Working on the 'methods' introduction and creating a node-tree for all the methods (10h) |
Thomas Passon | 17h | Meetings (2h), docu-wiki(13h), reading(2h) |
Name | Total time | Progress and time |
---|---|---|
Bas Coppus | meeting (1h), reading (2h), presentation(1h), docu-wiki(5h) | |
Mikolaj Pujanek | ||
Maksim Fisekovic | ||
Ingmar Verweij | Meetings (2h), Finishing the 'methods' introduction and node-tree (4h), Researching and writing the crucible extraction method (8h) | |
Thomas Passon |
Name | Total time | Progress and time |
---|---|---|
Bas Coppus | ||
Mikolaj Pujanek | ||
Maksim Fisekovic | ||
Ingmar Verweij | ||
Thomas Passon |
Sources
- ↑ NASA. (2025, 11 februari). Artemis - NASA. https://www.nasa.gov/humans-in-space/artemis/
- ↑ Peng Zhang, Wei Dai, Ran Niu, Guang Zhang, Guanghui Liu, Xin Liu, Zheng Bo, Zhi Wang, Haibo Zheng, Chengbao Liu, et al. Overview of the Lunar In Situ Resource Utilization Techniques for Future Lunar Missions. Space Sci Technol. 2023;3:0037.DOI:10.34133/space.0037
- ↑ Jump up to: 3.0 3.1 3.2 Slyuta, E. N., Abdrakhimov, A. M., Galimov, E. M., & V.I. Vernadsky Institute of Geochemistry and Analytical Chemistry. (2007). THE ESTIMATION OF HELIUM-3 PROBABLE RESERVES IN LUNAR REGOLITH. Lunar And Planetary Science XXXVII. https://www.lpi.usra.edu/meetings/lpsc2007/pdf/2175.pdf
- ↑ Olson, A. D. S., NASA Kennedy Space Center, Wisconsin Center for Space Automation and Robotics, University of Wisconsin’s Fusion Technology Institute, Wisconsin Center for Space Automation and Robotics, NASA Kennedy Space Center Swamp Works Electrostatics & Surface Physics Lab, & AIAA Member. (z.d.). Lunar Helium-3: Mining Concepts, Extraction Research, and Potential ISRU Synergies. NASA Kennedy Space Center, FL, 32899, U.S.A. https://ntrs.nasa.gov/api/citations/20210022801/downloads/AIAA%20ASCEND%202021%20Paper_211018.pdf
- ↑ David, L. (2015, 7 januari). Is moon mining economically feasible? Space.com. https://www.space.com/28189-moon-mining-economic-feasibility.html
- ↑ Ehresmann, M., Gabrielli, R. A., Herdrich, G., & Laufer, R. (2017). Lunar based massdriver applications. Acta Astronautica, 134, 189–196. https://doi.org/10.1016/j.actaastro.2017.02.007
- ↑ Cocks, F. H. (2010). 3He in permanently shadowed lunar polar surfaces. Icarus, 206(2), 778–779. https://doi.org/10.1016/j.icarus.2009.12.032
- ↑ Schrunk, D., Thangavelu, M., Cooper, B., & Sharpe, B. (1998). Physical Transportation on the Moon: The Lunar Railroad. Space 98. doi:10.1061/40339(206)41
- ↑ Baratta, M., Genta, G., Laurenzano, D., & Misul, D. (2018). Exploring the surface of the Moon and Mars: What kind of ground vehicles are required? Acta Astronautica. doi:10.1016/j.actaastro.2018.04.030
- ↑ Ice on the Moon. (z.d.).https://nssdc.gsfc.nasa.gov/planetary/ice/ice_moon.html
- ↑ Tan, J., Melkoumian, N., Harvey, D., & Akmeliawati, R. (2024c). Lunarminer Framework for Nature-Inspired Swarm Robotics in Lunar Water Ice Extraction. Biomimetics, 9(11), 680. https://doi.org/10.3390/biomimetics9110680
- ↑ Jump up to: 12.0 12.1 12.2 12.3 Wasteigerwald, & Wasteigerwald. (2024, 3 oktober). NASA’s LRO: Lunar Ice Deposits are Widespread - NASA Science. NASA Science. https://science.nasa.gov/solar-system/moon/nasas-lro-lunar-ice-deposits-are-widespread/#:~:text=Prior%20studies%20found%20signs%20of,Haworth%2C%20Shoemaker%20and%20Faustini%20craters
- ↑ Jump up to: 13.0 13.1 Tian, Y., Tang, J., Jiang, S., Zhang, W., Pang, Y., Jiang, J., Liu, Z., Li, Y., Zou, M., & Wang, D. (2024). Lunar regolith water ice simulation method and characterization. Icarus, 417, 116119. https://doi.org/10.1016/j.icarus.2024.116119
- ↑ Denton, M., & Denton, M. (2024, 27 december). The Cold Trap: How it works. Evolution News. https://evolutionnews.org/2014/05/the_cold_trap_h/
- ↑ Jump up to: 15.0 15.1 15.2 Li, S., Lucey, P. G., Milliken, R. E., Hayne, P. O., Fisher, E., Williams, J., Hurley, D. M., & Elphic, R. C. (2018). Direct evidence of surface exposed water ice in the lunar polar regions. Proceedings Of The National Academy Of Sciences, 115(36), 8907–8912. https://doi.org/10.1073/pnas.1802345115
- ↑ Noble, S. (n.d.). The Lunar regolith. https://www.nasa.gov/wp-content/uploads/2019/04/05_1_snoble_thelunarregolith.pdf?emrc=0bd585
- ↑ Jump up to: 17.0 17.1 17.2 Ethridge, E., & Kaukler, W. (2007). Microwave Extraction of Water from Lunar Regolith Simulant. AIP Conference Proceedings, 880, 830–837. https://doi.org/10.1063/1.2437523
- ↑ Jump up to: 18.0 18.1 18.2 18.3 18.4 18.5 Carrier, W. D., III & Lunar Geotechnical Institute. (2005). The four things you need to know about the Geotechnical Properties of Lunar Soil. https://www.lpi.usra.edu/lunar/surface/carrier_lunar_soils.pdf
- ↑ Sivakugan, N. (2000). Soil classification (pp. 1–11). https://www.geoengineer.org/storage/education/10/general_file_collection/7906/siva-classification.pdf#:~:text=Based%20on%20grain%20sizes%2C%20the%20Australian%20Standards%20AS1726-1993,mm%29%2C%20gravels%282.36-63%20mm%29%2C%20cobbles%2863-200%20mm%29%20and%20boulders%28%3E200%20mm%29
- ↑ Jump up to: 20.0 20.1 20.2 20.3 20.4 20.5 Metzger, P. T., Sapkota, D., Jack Fox, Nicholas Bennett, University of Central Florida, Florida Space Institute, Fox Technical Associates, & UNSW Australian Centre for Space Engineering Research (ACSER). (2021). AQUA FACTOREM: ULTRA LOW ENERGY LUNAR WATER EXTRACTION. https://fsi.ucf.edu/wp-content/uploads/sites/4/2022/11/FInal-Report_Aqua-Factorem_v1.pdf
- ↑ Hurley, Dana M., David J. Lawrence, D. Benjamin J. Bussey, Richard R. Vondrak, Richard C. Elphic, and G. Randall Gladstone. "Two‐dimensional distribution of volatiles in the lunar regolith from space weathering
- ↑ Jump up to: 22.0 22.1 22.2 22.3 Colaprete, A., Schultz, P., Heldmann, J., Wooden, D., Shirley, M., Ennico, K., Hermalyn, B., Marshall, W., Ricco, A., Elphic, R. C., Goldstein, D., Summy, D., Bart, G. D., Asphaug, E., Korycansky, D., Landis, D., & Sollitt, L. (2010). Detection of Water in the LCROSS Ejecta Plume. Science, 330(6003), 463–468. https://doi.org/10.1126/science.1186986
- ↑ Pitcher, C., Kömle, N., Leibniz, O., Morales-Calderon, O., Gao, Y., & Richter, L. (2015). Investigation of the properties of icy lunar polar regolith simulants. Advances in Space Research, 57(5), 1197–1208. https://doi.org/10.1016/j.asr.2015.12.030
- ↑ Brisset, J., Miletich, T., & Metzger, P. (2020). Thermal extraction of water ice from the lunar surface: A 3D numerical model. https://doi.org/10.1016/j.pss.2020.105082
- ↑ Westcott, C., & Brisset, J. (2024). Thermal extraction of water ice from the lunar surface II - Vapor yields for an improved regolith model. Planetary and Space Science, 232, 105973. https://doi.org/10.1016/j.pss.2024.105973
- ↑ Just, G. ., Smith, ., oy, . . et al. ( 0 0), ‘Parametric review of existing regolith excavation techniques for lunar In Situ Resource Utilisation (ISRU) and recommendations for future excavation experiments’, Planetary and Space Science, 180/4: 104746
- ↑ Hab, N. (2022). Modeling, Simulation and Comparison of Lunar Thermal Water Extraction Methods for Space Resource Utilization. Electronic Library. https://elib.dlr.de/191061/
- ↑ Jump up to: 28.0 28.1 28.2 28.3 28.4 28.5 28.6 28.7 Lee, K.-L., Truong, Q., Hota, S. K., Rokkam, S., Advanced Cooling Technologies, Inc., Zacny, K., & Honeybee Robotics. (2022). Waste Heat-Based Thermal Corer for Lunar Ice Extraction. In 51st International Conference On Environmental Systems. https://www.1-act.com/wp-content/uploads/2022/07/ICES-2022-130-Lunar-Ice-Miner-FINAL-Manuscript.pdf?srsltid=AfmBOoq05-rlx4JxEvtzN-i9Ts2u-BNGwA1eV9QzArr8OX6VnNgTI-qd
- ↑ Jump up to: 29.0 29.1 29.2 29.3 29.4 29.5 29.6 Lee, K.-L., Tarau, C., Truong, Q., Rokkam, S., Advanced Cooling Technologies, Inc, Zacny, K., Williams, H., Bergman, D., & Honeybee Robotics. (2021). Thermal Management System for Lunar Ice Miners. In 50th International Conference On Environmental Systems. https://www.1-act.com/wp-content/uploads/2021/08/ICES_Paper-235-Lunar-Ice-Miner_revB.pdf?srsltid=AfmBOoqAkHVqgdu12731hdNRCnF3ZH8jBBFdHoqj-F_EuBnwWE9vZ40g
- ↑ Metzger, P. T., Zacny, K., & Morrison, P. (2020). Thermal Extraction of Volatiles from Lunar and Asteroid Regolith in Axisymmetric Crank–Nicolson Modeling. Journal Of Aerospace Engineering, 33(6). https://doi.org/10.1061/(asce)as.1943-5525.0001165
- ↑ Metzger, P. T., Sapkota, D., Jack Fox, Nicholas Bennett, University of Central Florida, Florida Space Institute, Fox Technical Associates, & UNSW Australian Centre for Space Engineering Research (ACSER). (2021). AQUA FACTOREM: ULTRA LOW ENERGY LUNAR WATER EXTRACTION. https://fsi.ucf.edu/wp-content/uploads/sites/4/2022/11/FInal-Report_Aqua-Factorem_v1.pdf
- ↑ Mueller, R. P., Cox, R. E., Ebert, T., Smith, J. D., Schuler, J. M., & Nick, A. J. (2013, March). Regolith advanced surface systems operations robot (RASSOR). In 2013 IEEE Aerospace Conference (pp. 1-12). IEEE.
- ↑ Mueller, R. P., Smith, J. D., Schuler, J. M., Nick, A. J., Gelino, N. J., Leucht, K. W., ... & Dokos, A. G. (2016, April). Design of an excavation robot: regolith advanced surface systems operations robot (RASSOR) 2.0. In 15th Biennial ASCE Conference on Engineering, Science, Construction, and Operations in Challenging Environments (pp. 163-174). Reston, VA: American Society of Civil Engineers.
- ↑ HUSAROVA, I., OSINOVYY, G., & Potapovych, L. P. (2023). Technology for water mining on the Moon without ice phase change.
- ↑ Ehresmann, M., Gabrielli, R. A., Herdrich, G., & Laufer, R. (2017). Lunar based massdriver applications. Acta Astronautica, 134, 189–196. https://doi.org/10.1016/j.actaastro.2017.02.007
- ↑ Ehresmann, M., Institute of Space Systems, Herdrich, G., Laufer, R., & Gabrielli, R. (2016). Mission and system analysis for lunar massdriver applications (Door S. Fasoulas) [Master thesis IRS-16-035, University of Stuttgart]. https://doi.org/10.13140/RG.2.2.35323.52003
- ↑ Schrunk, D., Thangavelu, M., Cooper, B., & Sharpe, B. (1998). Physical Transportation on the Moon: The Lunar Railroad. Space 98. doi:10.1061/40339(206)41
- ↑ Baratta, M., Genta, G., Laurenzano, D., & Misul, D. (2018). Exploring the surface of the Moon and Mars: What kind of ground vehicles are required? Acta Astronautica. doi:10.1016/j.actaastro.2018.04.030
- ↑ Simko, T., & Gray, M. (2014). Lunar Helium-3 Fuel for Nuclear Fusion. World Futures Review, 6(2), 158–171. doi:10.1177/1946756714536142
- ↑ Chris Palmer. SpaceX Starship Lands on Earth, But Manned Missions to Mars Will Require More. Engineering, 2021, 7(10): 1345‒1347 https://doi.org/10.1016/j.eng.2021.08.005
- ↑ Gajda, M. E. (2006). A lunar volatiles miner (Doctoral dissertation, University of Wisconsin--Madison).
- ↑ Chang, Y., Yan, C., Liu, X., Wang, X., Zhou, H., Xiang, X., Tang, D., & National University of Defense Technology. (2020). Time-Efficient Mars Exploration of Simultaneous Coverage and Charging with Multiple Drones. In arXiv [Journal-article]. https://arxiv.org/abs/2011.07759v1
- ↑ Jump up to: 43.0 43.1 Saffre, F., Hildmann, H., Karvonen, H., VTT Technical Research Centre of Finland Ltd, & TNO - Netherlands Organisation for Applied Scientific Research. (2021). The Design Challenges of Drone Swarm Control. In Springer, Engineering Psychology and Cognitive Ergonomics, HCII 2021. https://doi.org/10.1007/978-3-030-77932-0_32
- ↑ Gazi, V., Fidan, B., Marques, L., & Ordonez, R. (2015). Robot Swarms: Dynamics and Control. In ASME Press eBooks (pp. 79–126). https://doi.org/10.1115/1.860526_ch4
- ↑ Jump up to: 45.0 45.1 Kaczmarek, S. (2021, 31 augustus). Robotic Swarm Intelligence for Lunar Exploration - Sylvester Kaczmarek. Sylvester Kaczmarek. https://sylvesterkaczmarek.com/blog/robotic-swarm-intelligence-for-lunar-exploration/
- ↑ Sabatini, M., & Palmerini, G. B. (2009). Collective control of spacecraft swarms for space exploration. Celestial Mechanics And Dynamical Astronomy, 105(1–3), 229–244. https://doi.org/10.1007/s10569-009-9183-8
- ↑ Fa, W., & Jin, Y. (2010). Global inventory of Helium-3 in lunar regoliths estimated by a multi-channel microwave radiometer on the Chang-E 1 lunar satellite. Chinese Science Bulletin, 55(35), 4005–4009. https://doi.org/10.1007/s11434-010-4198-9
- ↑ Cocks, F. H. (2010). 3He in permanently shadowed lunar polar surfaces. Icarus, 206(2), 778–779. https://doi.org/10.1016/j.icarus.2009.12.032
- ↑ Ping, J., Su, X., Huang, Q., & Yan, J. (2011). The Chang’E-1 orbiter plays a distinctive role in China’s first successful selenodetic lunar mission. Science China Physics Mechanics And Astronomy, 54(12), 2130–2144. https://doi.org/10.1007/s11433-011-4561-0
- ↑ Shkuratov, Y. G., & Bondarenko, N. V. (2001). Regolith Layer Thickness Mapping of the Moon by Radar and Optical Data. Icarus, 149(2), 329–338. https://doi.org/10.1006/icar.2000.6545
- ↑ Fa, W., & Jin, Y. (2009). A primary analysis of microwave brightness temperature of lunar surface from Chang-E 1 multi-channel radiometer observation and inversion of regolith layer thickness. Icarus, 207(2), 605–615. https://doi.org/10.1016/j.icarus.2009.11.034
- ↑ Shkuratov, Y. G., & Bondarenko, N. V. (2001b). Regolith Layer Thickness Mapping of the Moon by Radar and Optical Data. Icarus, 149(2), 329–338. https://doi.org/10.1006/icar.2000.6545
- ↑ David, L. (2015, 7 januari). Is moon mining economically feasible? Space.com. https://www.space.com/28189-moon-mining-economic-feasibility.html
- ↑ Simko, T., & Gray, M. (2014). Lunar Helium-3 Fuel for Nuclear Fusion. World Futures Review, 6(2), 158–171. https://doi.org/10.1177/1946756714536142
- ↑ Jump up to: 55.0 55.1 Matar, S. (2021). Energy analysis of extracting helium-3 from the Moon (Doctoral dissertation, Politecnico di Torino)
- ↑ John, A., Krishna, M. S., Ali, A., Suku, A., & Kumar, S. (2021). APPLICATION OF ROBOTICS IN MINING- a REVIEW [Journal-article]. International Journal Of Creative Research Thoughts (IJCRT), 9(8), 105–106. https://ijcrt.org/papers/IJCRT2108016.pdf
- ↑ Kokkinis, A., Frantzis, T., Skordis, K., Nikolakopoulos, G., & Koustoumpardis, P. (2024). Review of Automated Operations in Drilling and Mining. Machines, 12(12), 845. https://doi.org/10.3390/machines12120845
- ↑ Tan, J., Melkoumian, N., Harvey, D., & Akmeliawati, R. (2024). Evaluating Swarm Robotics for Mining Environments: Insights into Model Performance and Application. Applied Sciences, 14(19), 8876. https://doi.org/10.3390/app14198876
- ↑ Olson, A. D. S., NASA Kennedy Space Center, Wisconsin Center for Space Automation and Robotics, University of Wisconsin’s Fusion Technology Institute, Wisconsin Center for Space Automation and Robotics, NASA Kennedy Space Center Swamp Works Electrostatics & Surface Physics Lab, & AIAA Member. (z.d.). Lunar Helium-3: Mining Concepts, Extraction Research, and Potential ISRU Synergies. NASA Kennedy Space Center, FL, 32899, U.S.A. https://ntrs.nasa.gov/api/citations/20210022801/downloads/AIAA%20ASCEND%202021%20Paper_211018.pdf
- ↑ Tan, J., Melkoumian, N., Harvey, D., & Akmeliawati, R. (2024b). Lunarminer Framework for Nature-Inspired Swarm Robotics in Lunar Water Ice Extraction. Biomimetics, 9(11), 680. https://doi.org/10.3390/biomimetics9110680